Fließlochschraubverbindungen prüfen
In fünf Schritten zum Ergebnis
Mit Fließlochschrauben können Multi-Material-Verbindungen hergestellt werden, auch wenn die Schraubstelle nur von einer Seite zugänglich ist. Anhand von fünf Parametern lässt sich die Qualität derartiger Verbindungen überprüfen und sicherstellen.
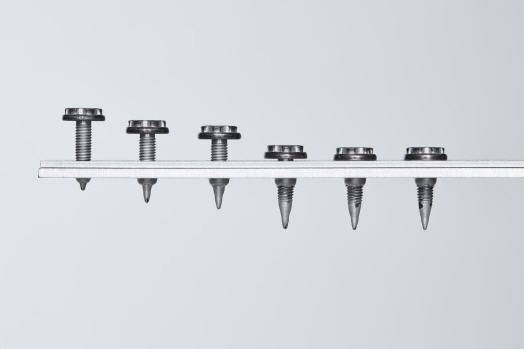
Fließlochverschraubungen werden in der Automobilindustrie eingesetzt, wenn die Verbindung mehrerer Materialien nur von einer Seite aus bewerkstelligt werden kann. Die Schraube ist dabei gleichzeitig Bohr- und Verbindungselement. Sie wird bei hoher Drehzahl und unter Druck durch alle Materiallagen gedrückt und formt dabei das Gewinde.
Experten der Atlas Copco IAS GmbH in Bretten haben in fünf Schritten wichtige Parameter zusammengefasst, anhand derer Sie die Qualität Ihrer Fließlochschraubverbindung einfach überprüfen können.
1. Beschichtung des Fügeelements kontrollieren
Zum Schutz vor Korrosion sind die Fügeelemente gleichmäßig mit Zink-Nickel oder Zinklamellen beschichtet. Ist diese Beschichtung beschädigt, besteht ein erhöhtes Korrosionsrisiko. Kontrollieren Sie daher die Fügeelemente vor der Montage stets auf eine gleichmäßige Beschichtung, um Ihre Bauteile vor Korrosion zu schützen.
2. Richtige Position des Schraubenkopfes
Die Position des Schraubenkopfes kann die Festigkeit und Korrosionsbeständigkeit der Verbindung stark beeinflussen. Wird der Schraubenkopf falsch angesetzt, können sich die zu montierenden Teile während des Fügens verschieben, die Verbindung kann geschwächt werden. Bei der Überprüfung der Schraubenkopfposition unterscheidet man aufgrund der unterschiedlichen Anforderungen zwischen Prozesspunkten und Festigkeitspunkten.
2.1 Prozesspunkte
Befestigungspunkte ohne strukturrelevante Eigenschaften, die nur zur Stabilisierung verwendet werden, können als Prozesspunkte bezeichnet werden. An diesen Punkten wird oft in Kombination mit Strukturklebstoffen gearbeitet und sichergestellt, dass sich die Bauteile nicht bewegen, bis der Klebstoff vollständig ausgehärtet ist.
Die Verbindungsqualität von Prozesspunkten ist in Ordnung, wenn:
- das Fügeelement eine vollständige Kopfauflage erreicht
- das Fügeelement eine einseitige Kopfauflage erreicht und die erzeugte Vorspannkraft die Bauteile ordnungsgemäß zusammenhält
Die Qualität ist nicht in Ordnung, wenn das Fügeelement keine Kopfauflage erreicht.
Wird keine Kopfauflage erreicht, kann eine falsche Drehzahl oder ein zu niedriges Drehmoment die Ursache sein. Überprüfen Sie zunächst die Drehzahl während des Gewindeformens. Ist diese zu niedrig, wird das gewünschte Drehmoment für das Gewindeformen überschritten. Dann bricht die Steuerung den Prozess ab und gibt eine Fehlermeldung. Das Ergebnis ist eine unvollständige Verbindung.
Ist wiederum das Drehmoment beim Endanzug zu niedrig, dann wird zu wenig oder gar keine Klemmkraft aufgebaut. Die Verbindung ist nicht sicher. In diesem Fall passen Sie die Einstellungen an und stellen sicher, dass das Fügeelement mit dem richtigen Endmoment angezogen wird.
2.2 Festigkeitspunkte
Sogenannte Festigkeitspunkte sind für die spätere Stabilität des Fahrzeuges relevant. Im Karosseriebau finden sich zahlreiche Festigkeitspunkte insbesondere am Unterboden, im Vorderwagen, in der Aufprallzone sowie am Karosseriegerippe. Die Verbindung ist an einem Festigkeitspunkt ordnungsgemäß gesetzt, wenn das Fügeelement die vollständige Kopfauflage erreicht. Die Qualität ist nicht in Ordnung, wenn der Schraubenkopf nicht oder nur einseitig aufliegt.
Ist die Kopfauflage nicht vollständig erreicht, kommen mehrere Fehlerquellen infrage. Überprüfen Sie die folgenden vier Punkte:
- Positionierung des Roboters
- Klemmen der Bauteile
- Passung der Komponenten
- Schraubparameter beim Durchzug, Gewindeformen und Endanzug
Wenn der Roboter das Werkzeug nicht exakt senkrecht an die zu verbindenden Flächen führt, dringt das Fügeelement schräg – und damit nicht ordnungsgemäß – in die Baugruppe ein. Dies schwächt die Verbindung und macht sie anfälliger für Korrosion. Passen Sie den Annäherungswinkel des Roboters entsprechend an.
Wenn Karosserieteile nicht fest genug eingespannt oder gegen Bewegung abgestützt werden, kann es während des Fließlochschraubens durch hohe Druckbelastungen zu einer einseitigen Kopfauflage und somit zu einer fehlerhaften Verbindung kommen.
Passen die zu fügenden Komponenten nicht spaltenlos aufeinander, verändert sich der Fügewinkel, so dass die Kopfauflage der Schraube nur einseitig oder gar nicht erreicht wird.
Auch eine falsche Drehzahl während des Prozessschrittes Gewindeformen kann verhindern, dass die Schraube die Kopfauflage erreicht. Ist nämlich die Drehzahl für die zu verbindenden Materialien zu niedrig, kann ein höheres Gewindedrehmoment die Folge sein. Die Systemsteuerung stoppt dann den Vorgang, um das Bauteil vor weiteren Schäden zu schützen. Ein weiteres Problem, das zu einer unzureichenden Verbindung führen kann, ist das Nichterreichen des Endanzugmoments. Dann kann das Fügeelement im letzten Verfahrensschritt nicht ausreichend angezogen werden.
3. Abdeckung der Durchgangsbohrung
Das Verfahren des Fließlochschraubens erfordert in der Regel keine Vorbohrung im Obermaterial. Ausnahmen sind sehr dicke zu verbindende Teile, Gussteile oder komplexe Materialkombinationen sowie spezielle Fügeanforderungen, beispielsweise an die Wärmeleitfähigkeit. In solchen Fällen werden auch vorgebohrte Materialien verwendet. Hierbei erhält das Fügeelement die zusätzliche Funktion, die Durchgangsbohrung abzudecken und so zu schützen.
Verbindungen ohne Vorbohrung widerstehen Korrosionsgefahren in der Regel besser als solche mit Vorbohrung. Denn bei diesen kann leichter Feuchtigkeit unter den Kopf des Fügeelements und somit in und zwischen die Schichten der zu verbindenden Materialien gelangen. Bei solchen Verbindungen spielen Strukturklebstoffe und Dichtstoffe für Stabilität und Korrosionsschutz eine wichtige Rolle.
Ist die Vorbohrung nicht vollständig durch das Fügeelement abgedeckt, sollten die Roboterprogrammierung und der Durchmesser der Vorbohrung überprüft werden.
4. Spalte zwischen Materialien
Die Qualität einer Verbindung hängt auch von der Passform der Materialien ab. Spalte zwischen den Schichten können Korrosion oder Luftblasen verursachen, den Klebstoff brechen und die Festigkeitseigenschaften beeinträchtigen. Überprüfen Sie in diesem Fall die Materialstärke sowie das Drehmoment und die Drehzahl beim Durchbohren des Materials: Wenn der Toleranzbereich der Materialstärke überschritten wird, ist der Reibwiderstand höher und mehr „Kraft“ (eigentlich: ein Zusammenspiel aus Drehzahl und Kraft) nötig, um das Material zu erwärmen.
Manchmal verbessert eine kleine Anpassung der Montageparameter die Verbindungsqualität. Bei der Programmierung der Schraubparameter für Multimaterialverbindungen, insbesondere des Drehmoments für den letzten Verfahrensschritt, sind die individuellen Anforderungen der einzelnen Materialschichten zu berücksichtigen.
Ist die Drehzahl beim ersten Verfahrensschritt zu hoch, wird das Material zu heiß. Beim Durchzugformen schiebt das Fügeelement das Material zwischen die Schichten, so dass zwischen diesen ein Spalt entsteht. Auch eine zu geringe Drehzahl kann ein korrektes Fließen der Materialschichten verhindern.
5. Beweglichkeit des Fügeelements prüfen
Vor der Freigabe der Verbindung sollten Sie die Festigkeit des Fügeelements noch von Hand überprüfen: Bei dieser manuellen Kontrolle steht das „Losbrechmoment“ auf dem Prüfstand. Wenn Sie die Schraube gegen den Uhrzeigersinn drehen können, ist im Prozess etwas schiefgelaufen. Die Verbindung muss als defekt eingestuft werden.
Die fehlende Festigkeit kann mehrere Ursachen haben. Möglich ist, dass das Drehmoment für den Endanzug zu hoch eingestellt wurde. Das Gewinde wird abgeschält und beschädigt die Nabe. Dies kann auch auftreten, wenn versehentlich Klebstoff in die Verbindung eindringt und das Verfahren „schmiert“, was zu Drehmomentüberschreitungen führen kann.
Wenn der Klebstoff direkt unter dem Fügeelement platziert wird, senkt das die Reibung. Die Schraube überdreht und lockert sich. Bei Verbindungen ohne Vorbohrung kommt dies allerdings selten vor.
Auch können Dicke und Materialhärte von Gussteilen, die in der Montage verwendet werden, variieren. Dies kann dazu führen, dass das voreingestellte Drehmoment zu niedrig und die Verbindung somit unzureichend ist.
Fazit:
Anhand von fünf Schritten kann die Qualität von Fließlochschraubverbindungen während und nach der Produktion visuell überprüft werden. Für strukturelle Verbindungen sollten die Prozessparameter natürlich schon im Vorfeld entwickelt werden. In zwölf Innovationszentren weltweit entwickeln die Experten für industrielles Fügen von Atlas Copco gemeinsam mit ihren Kunden zukunftsfähige und zuverlässige Verbindungsverfahren, um deren Fertigungsziele zu unterstützen.
Mehr Informationen zu Atlas Copco:
![]() |
Atlas Copco Deutschland |
![]() |
Langemarckstr. 35 |
![]() |
D-45141 Essen |
![]() |
Tel.: +49 (0)201 21 77 0 |
![]() |
Fax: +49 (0)201-2177-100 |
![]() |
E-Mail: atlascopco.deutschland@de.atlascopco.com |
![]() |
www.atlascopco.de |
![]() |
------------------------------------------------------ |
![]() |
Handwerkzeuge: |
![]() |
Atlas Copco Tools Central Europe GmbH |
![]() |
Langemarckstr. 35 |
![]() |
D-45141 Essen |
![]() |
Tel.: +49 (0)201 21 77 0 |
![]() |
E-Mail: tools.de@atlascopco.com |
![]() |
www.atlascopco.com/de-de/itba |
War dieser Artikel für Sie hilfreich?
![]() |
![]() |
![]() |
![]() |
![]() |
Bitte bewerten Sie diese Seite durch Klick auf die Symbole.
Zugriffe heute: 2 - gesamt: 4566.