Additive Fertigung von HM-Schneidwerkzeugen
Der Weg zu besseren Schneidwerkzeugen
Wolframkarbid-Kobalt ist ein hervorragender Werkstoff für Schneidwerkzeuge, da es extrem hitzebeständig und verschleißfest ist. Im neuen Forschungsprojekt »Additive Manufacturing von Wolframkarbid-Kobalt – AM von WC-Co« untersuchen Wissenschaftler des Instituts für Werkstoffanwendungen im Maschinenbau IWM und des Werkzeugmaschinenlabors WZL der RWTH Aachen University sowie des Fraunhofer-Instituts für Lasertechnik ILT nun, wie sich dieses Material mit dem Laser Powder Bed Fusion verarbeiten lässt. Das Ziel sind additiv gefertigte Schneidwerkzeuge, die dank komplexer Kühlgeometrien längere Standzeiten erreichen.
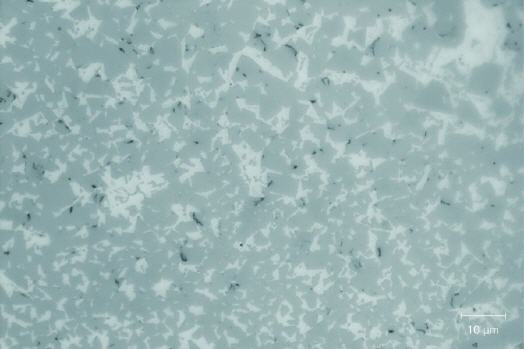
Schneidwerkzeuge aus Wolframkarbid-Kobalt (WC-Co) können bislang nur über komplexe Sinterprozesse hergestellt werden. Die hohe Festigkeit dieser Werkstoffe auf der einen Seite und die Sintertechnologie auf der anderen begrenzen jedoch die Formgebung von Schneidwerkzeugen. Das Einbringen komplexer Kühlstrukturen wird dadurch sehr aufwändig oder schlicht unmöglich.
Additive Fertigungsverfahren bieten dagegen eine hohe Gestaltungsfreiheit und eine endkonturnahe Fertigung. Dadurch werden Nachbearbeitungsprozesse minimiert und auch komplexe Kühlstrukturen innerhalb des Schneidwerkzeugs möglich. Insbesondere das Laser Powder Bed Fusion (LPBF) bietet hier viele Vorteile. Bei diesem additiven Fertigungsverfahren wird das Werkstück schichtweise mit dem Laser aus dem Pulverbett aufgebaut. Damit lassen sich Hinterschneidungen einbringen und komplexe Kühlgeometrien werden machbar. Im Turbinenbau wurden dank additiv gefertigter Teile schon deutlich höhere Betriebstemperaturen erreicht.
Die laserbasierten additiven Fertigungsverfahren erfordern eine sorgfältige Auswahl des Materials und der Prozessparameter, damit am Ende auch vergleichbare Festigkeiten wie bei konventionellen Verfahren erreicht werden. Im neuen Förderprojekt ›AM von WC-Co‹ wird eine Gruppe Aachener Forschungsinstitute dies genauer untersuchen. Zum Team gehören das Institut für Werkstoffanwendungen im Maschinenbau IWM und das Werkzeugmaschinenlabor WZL der RWTH Aachen University sowie das Fraunhofer ILT.
Ein großes Problem im LPBF-Prozess ist die Temperaturverteilung im aufgebauten Werkstück. Im Laserspot wird das Metallpulver geschmolzen, danach kühlt es schnell ab. Konventionelle Anlagen haben eine beheizte Bodenplatte, um die Abkühlung zu verlangsamen. Gerade bei hochschmelzenden Materialien und großen Bauteilen reicht das aber nicht, es kommt zu Spannungen und manchmal sogar zu Rissen im Bauteil.
Die Experten des Fraunhofer ILT beschäftigen sich schon seit einigen Jahren mit dem Problem und haben in Zusammenarbeit mit der Firma adphos Innovative Technologies GmbH unter anderem ein System entwickelt, bei dem ein Nahinfrarot (NIR)-Strahler das Bauteil von oben erwärmt. Mit bis zu 12 kW schafft der Strahler Temperaturen bis zu 800 °C im Bauteil. Im Projekt ›AM von WC-Co‹ soll diese Technologie zur Verarbeitung von Wolframkarbid-Kobalt genutzt werden.
Dazu wird die komplette Prozessroute von den Pulverwerkstoffen über den additiven Fertigungsprozess bis hin zur Nachbearbeitung und Erprobung untersucht. Die Wissenschaftler verfolgen das Ziel, diejenigen Materialien und Prozesse zu qualifizieren, mit denen sich konventionelle Sinterverfahren ersetzen lassen. Die additiv hergestellten Hartmetall-Schneidwerkzeuge sollen eine vergleichbare Härte wie konventionell hergestellte Werkzeuge besitzen, jedoch durch die eingebrachten Kühlstrukturen längere Standzeiten aufweisen.
Insbesondere bei der Bearbeitung anspruchsvoller Materialien wie zum Beispiel von Titanwerkstoffen sollte sich das auszahlen. Darüber hinaus kann das System mit den NIR-Strahlern zur Pulverbettheizung den Weg zur Verarbeitung weiterer hochschmelzender Legierungssysteme ebnen.
Mehr Informationen zum Fraunhofer ILT:
![]() |
Fraunhofer-Institut für Lasertechnik ILT |
![]() |
Steinbachstr. 15 |
![]() |
52074 Aachen |
![]() |
Telefon +49 241 8906-0 |
![]() |
www.ilt.fraunhofer.de |
War dieser Artikel für Sie hilfreich?
![]() |
![]() |
![]() |
![]() |
![]() |
Bitte bewerten Sie diese Seite durch Klick auf die Symbole.
Zugriffe heute: 1 - gesamt: 4665.