Schnell, präzise, prozesssicher
Das neue Heckert-BAZ ›500 D‹
Wer wie der Leichtbau-Druckguss-Spezialist Brabant Alucast einbaufertige Teile an die Automobilindustrie liefert, benötigt unter anderem eine leistungsstarke zerspanende Fertigung. Am Hauptsitz in Oss ist diese mit acht horizontalen Bearbeitungszentren der zur Starrag Group gehörenden Heckert GmbH ausgestattet, die durch ihre Dynamik und den durchdachten Aufbau hohe Qualität und kurze Stückzeiten ermöglichen. Insbesondere die beiden neuen HEC 500 D konnten im Benchmark überzeugen.
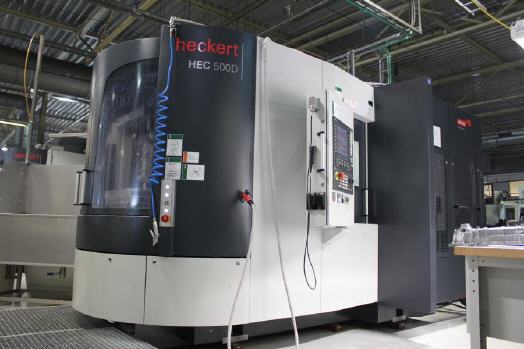
Brabant Alucast ist auf die Konstruktion, Entwicklung und Produktion von Hochdruck-Aluminium- und -Magnesium-Druckgussteilen für die Automobilindustrie spezialisiert und gehört in diesem Sektor nach Qualitäts-Ranking und Jahresumsatz zu den besten Firmen in Europa. Das Unternehmen mit Hauptsitz im niederländischen Oss und vier weiteren Niederlassungen in Holland, Deutschland, Italien und Tschechien verfügt über eine breite Vielfalt verschiedener Produktionsverfahren, um für seine Kunden hochwertige Teile herzustellen. Dazu zählen unter anderem die beiden selbst entwickelten Druckguss-Technologien Exactfit Casting™ und Vacural® Casting.
Doch Brabant Alucast verfügt nicht nur über Druckguss-Kapazitäten von 300 bis 4000 Tonnen. Das Unternehmen zeichnet sich besonders durch sein Komplettangebot aus, das die CNC-Bearbeitung und die Montage der Automobilkomponenten einschließt. Qualität und Kundenorientierung spielen dabei eine besondere Rolle. Für sein QM-System hat Brabant Alucast die ISO/TS 16949 (2009) Automotive Certification erhalten, und für seinen kundenorientierten Ansatz wurde das Unternehmen bereits sechs Mal mit dem European Aluminium Award (Automotive) ausgezeichnet.
Am Standort Oss konzentriert sich Brabant Alucast mit rund 300 Mitarbeitern auf den Druckguss und die zerspanende Bearbeitung der großen Teile aus verschiedenen Magnesium- und Aluminiumlegierungen. Meist sind es Motor- und Getriebekomponenten oder Strukturteile, die einbaufertig an BMW, GM/Opel, PSA, DAF, VW/Audi, Toyota, ZF und andere geliefert werden.
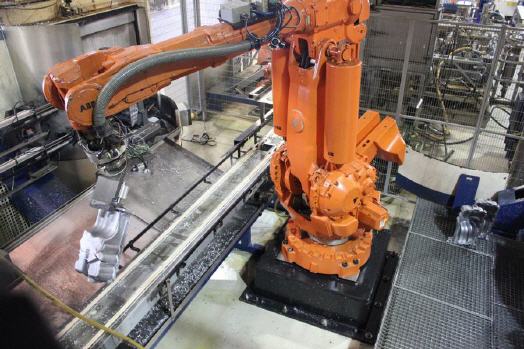
Christiano Sala ist in Oss als Entwicklungsingenieur Teile & Prozesse für die CNC-Bearbeitung zuständig. Ein Bereich, in dem sich unter anderem acht Heckert-Maschinen befinden – sechs CWK 500 D und seit kurzem zwei HEC 500 D. Er erinnert sich noch gut an den Beginn der erfolgreichen Zusammenarbeit mit der Heckert GmbH, Chemnitz, die zur Starrag Group gehört, einem technologisch weltweit führenden Hersteller von Präzisions-Werkzeugmaschinen: „Heckert war mir schon lange als ein weltweit führender Anbieter von Bearbeitungszentren bekannt, die sich zum Fräsen, Bohren und Drehen von komplexen Werkstücken eignen. Als 1999 Benny Van Haver vom Heckert-Vertrieb auf uns zukam, um für die Bearbeitung eines Schwungradgehäuses das Bearbeitungszentrum CWK 500 D zu empfehlen, war das ein Glücksfall. Denn mit dieser Maschine, ihren 82 m/min Eilgang sowie 1 g Beschleunigung erreichten wir mit Abstand die kürzeste Fertigungszeit.“ Auch der stabile Maschinenaufbau, die Größe des Störkreises und die hydraulischen Spannmöglichkeiten entsprachen den Vorstellungen von Christiano Sala und seinen Kollegen.
Benny Van Haver, schon damals als Vertriebsleiter Benelux in der Starrag Group für Brabant Alucast in den Niederlanden zuständig, bestätigt die gute Zusammenarbeit, die sich in den folgenden Jahren ausgeweitet hat: „Zum einen realisierten wir gemeinsam eine Roboterbeschickung für die CWK. Zum anderen folgten insgesamt noch fünf weitere CWK 500 D-Bestellungen zur Bearbeitung von Ölwannen, Ventilgehäuse, Leiterrahmen, Kurbel-und Getriebegehäuse. Alle Maschinen sind mit einer Schnittstelle zur Roboterautomation und zum Teil mit einer Brandschutzanlage für die Magnesiumbearbeitung ausgeführt.“ Die sechs Heckert CWK-Anlagen arbeiten noch immer im Drei-Schicht-Betrieb, ohne nennenswerte Einbußen an Präzision und Leistungsfähigkeit. „Die Langzeitqualität dieser Maschinen macht die Investition besonders lohnenswert“, urteilt Christiano Sala.
Eine kleine Pause musste die Partnerschaft dann doch überstehen. Nach einem Wechsel in Geschäftsführung und Strategie investierte das Brabant Alucast-Werk in Oss 2013 für ein neues Projekt in zwei preisgünstigere Maschinen eines japanischen Werkzeugmaschinenherstellers. „Unsere Erfahrungen damit waren allerdings nicht zufriedenstellend“, berichtet Christiano Sala. So fiel die Entscheidung beim jüngsten Auftrag – einer Anlage zur Bearbeitung von Ölwannenoberteilen – nach erneutem Wechsel der Geschäftsleitung wieder zugunsten von Heckert. Geordert wurden zwei Maschinen des CWK-Nachfolgemodells HEC 500 D.
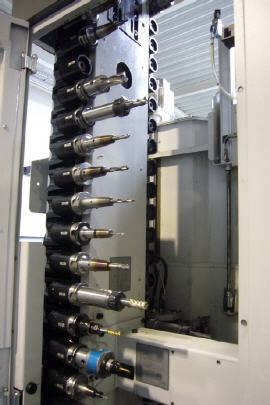
Christiano Sala betont: „Selbstverständlich haben wir vor dem Kauf intensive Studien betrieben, welche Maschinen sich für diesen Einsatz langfristig optimal eignen. Immerhin geht es um Stückzahlen von 100.000 Teilen pro Jahr, vermutlich über einen Zeitraum von mehreren Jahren.“ Unter anderem verglichen Sala und seine Kollegen die Fertigungszeit pro Teil mit dem exakt gleichen Programm auf einer Heckert CWK 500 D Baujahr 2005 (402,0 s), mit der des japanischen BAZ Baujahr 2013 (388,4 s) und der neuen Heckert HEC 500 D Baujahr 2015 (321,2 s). Das Ergebnis – siehe Werte in Klammern – war deutlich: Die HEC 500 D war 20% schneller als das Vorgängermodell CWK 500 D und 17,3% schneller als das nur zwei Jahre ältere japanische BAZ.
Für Benny Van Haver ist das eine Bestätigung für die erfolgreiche Entwicklungsarbeit bei Heckert: „Unsere F+E-Abteilung hat bewährte Eigenschaften wie den robusten, langlebigen Maschinenaufbau beibehalten, wesentliche Details aber auf modernsten Stand der Technik gebracht, zum Beispiel mit hochdynamischen Vorschubantrieben und äußerst genauen Profilschienenwälzführungen in allen Linearachsen.“ Und auch Christiano Sala ist mit dem Ergebnis hoch zufrieden: „Es ist schön zu sehen, dass Heckert die Anregungen von uns und anderen Anwendern ernst nimmt und entsprechende Verbesserungen einfließen lässt.“ Der Erfolg rechnet sich für ihn in barer Münze: Denn durch die kürzeren Stückzeiten reicht die Kapazität der beiden HEC-Maschinen fürs Volumen des jüngsten Auftrag aus. Bei den bisherigen Maschinen wäre die Investition in ein drittes BAZ notwendig geworden.
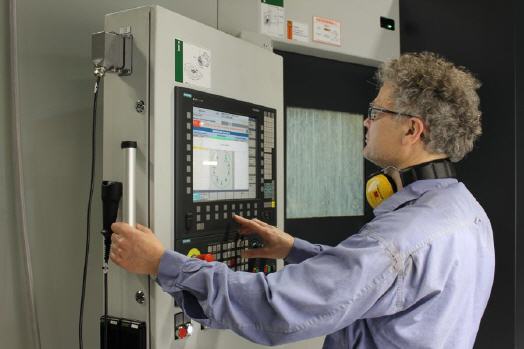
Einen wesentlichen Anteil an der kürzeren Fertigungszeit haben die schnellen Eilgänge von 100 m/min und Beschleunigungen von 1 g in den Linearachsen. Und die Motorspindel kann mit besonderen Leistungsdaten punkten: Der Drehzahlbereich liegt zwischen 50 und 20.000 U/min, die Leistung (40/100% ED) bei 50/48 kW und das Drehmoment (40/100% ED) bei 85/60 Nm. In nur einer Sekunde beschleunigt sie (nach VDI 2852) von Null auf 20.000 U/min. Dadurch reduzierten sich bei gleichem NC-Programm, gleicher Aufspannung und gleichen Werkzeugen die Nebenzeiten enorm. „Wenn dann erst das Programm hinsichtlich der Bearbeitungsdaten optimiert ist, sind vermutlich nochmals zehn Prozent Stückzeitverkürzung möglich“, schätzt Starrag Group-Vertreter Benelux Benny Van Haver.
Auch Entwicklungsingenieur Sala weiß, welches Potenzial in der Spindel steckt: „Die Ölwanne enthält zum Beispiel zahlreiche Gewinde M6. Um diese zu erzeugen, haben wir auf der CWK 109 Sekunden gebraucht. Auf der HEC benötigen wir nur noch 77,5 Sekunden. Auch bei diesen Zahlen haben wir eine Optimierung hinsichtlich der Spindeldrehzahl noch nicht berücksichtigt. Vermutlich können wir mit PKD-Werkzeugen noch höhere Schnittgeschwindigkeiten fahren und auch die Hauptzeit verkürzen.“
Doch noch befinden sich die neuen Bauteile in der Anlaufphase. Das heißt, neben den Ölwannenoberteilen sollen in Zukunft auch Zylinderkopfhauben und eventuell ein weiteres Produkt auf den HEC-Maschinen laufen, um die Auslastung rund um die Uhr sicher zu stellen. Dementsprechend wechselt die Produktion noch zwischen HEC- und CWK-Maschinen, wobei sich die NC-Programme an der „schwächeren“ Maschine orientieren müssen. Erst wenn sich die Zerspanungs-Verantwortlichen auf eine fixe Zuordnung festgelegt haben, geht es ans Optimieren der Bearbeitung.
Die hochdynamischen Horizontal-Bearbeitungszentren der Modellreihe HEC haben 2011 ihre Vorgänger der CWK-Baureihe abgelöst. Sie lassen sich in ihrer Ausstattung so flexibel gestalten, dass unterschiedlichste Materialien für alle Branchen der metallverarbeitenden Industrie bearbeitet werden können. Speziell zur Leichtmetallbearbeitung bietet Heckert HEC-Zentren mit Dynamikpaket an, die sich durch die erwähnt hohen Drehzahl-, Eilgang- und Beschleunigungswerte auszeichnen.
Durch ihren (thermo-)stabilen Aufbau, umfangreiche Kontroll- und Überwachungseinrichtungen sowie ein modernes Service- und Diagnosesystem sichert Heckert den Anwendern eine langfristige Bearbeitungsgenauigkeit der Toleranzklasse IT 5 zu. Das ist für Christiano Sala ein wichtiges Argument, denn seine Bauteile laufen in der Regel über viele Jahre im automatisierten Drei-Schicht-Betrieb – die Roboterbeschickung ist auch für die HEC 500 D fest geplant. Da ist eine hohe Prozesssicherheit unerlässlich. „Reguläre Maße müssen wir mit einem Prozessfähigkeitsindex CpK von 1 erreichen, kritische Merkmale mit CpK 1,67“, so der Entwicklungsingenieur. Die Ölwannenoberteile enthalten zahlreiche H7-Passungen, zum Beispiel sogenannte OCV-Bohrungen, die hochgenaue Ventile zur Nockenwellenverstellung aufnehmen müssen. Dementsprechend wichtig sind die Genauigkeiten in Durchmesser und Rundlauf sowie eine Oberflächengüte, die bei Ra = 0,8 µm liegt.
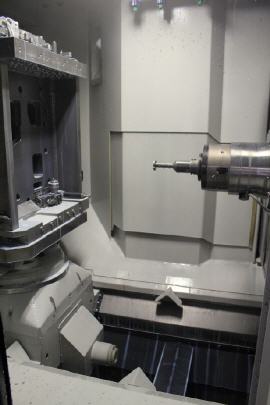
Starrag Group-Vertreter Benny Van Haver weist auf wesentliche Detailverbesserungen hin, die die HEC 500 D im Vergleich zum Vorgängermodell erfahren hat: „Es wurden die früheren Teleskopabdeckungen in der Maschine durchgängig durch Festbleche ersetzt. Das ermöglicht höhere Beschleunigungen und Eilgänge, da die Bleche nicht mit den Linearachsen mitgeführt werden müssen. Außerdem weist der Arbeitsraum nun im Querschnitt eine Trichterform auf, so dass die Späne in der Mitte auf einen Späneförderer fallen. So können sich keine Spänenester mehr bilden, die die Prozesssicherheit gefährden.“ Zudem überzeugen die neuen Werkzeugmagazine durch ihre Sauberkeit. Dazu wurden alle Hydraulik-Baugruppen aus ihrer Umgebung verbannt, und auch Späne oder Kühlwasser werden vom Wechsler ferngehalten.
Christiano Sala ist überzeugt, dass sich die Heckert HEC 500 D genauso langfristig bewähren werden wie die CWK-Zentren, die bei Brabant Alucast schon seit zehn bis 15 Jahren im Drei-Schicht-Betrieb ihre hohe Qualität halten. Daran haben auch die gut ausgebildeten Techniker ihren Anteil, die vor Ort für optimale Wartung sorgen. Sie sind derzeit dabei, die passende Wartung für die HEC-Maschinen zu sichern. Christiano Sala erklärt: „Wir hatten erst kürzlich Heckert-Mitarbeiter im Haus, die neue Wartungsprogramme vorgestellt haben. Vielleicht nutzen wir auch diese Angebote, die die Performance der Maschine permanent auf hohem Level halten und ein zeitgenaues, präventives Eingreifen ermöglichen.“
Fazit:
Durch die neuen HEC 500 D kann die Firma Brabant nachhaltig seine Profitabilität steigern. Für das erweiterte Produktspektrum erreichen die Maschinen 17,3 Prozent schnellere Bearbeitungszeiten. Dadurch genügen bereits zwei Maschinen, um die Fertigungsaufgabe zu meistern, eine weitere dritte Maschine wird nicht benötigt. Schon durch die Vorgängermaschinen wurde eine höchste Prozesssicherheit bestätigt, die auch bei einer fordernden Drei-Schicht-Fertigung keine Qualitätseinbußen zulässt.
Mehr Informationen:
![]() |
Heckert GmbH |
![]() |
Otto-Schmerbach-Str. 15/17 |
![]() |
09117 Chemnitz |
![]() |
Tel: +49 371 836 23 68 |
![]() |
Fax: +49 371 836 23 53 |
![]() |
E-Mail: service.heckert@starrag.com |
![]() |
www.starrag.com |
War dieser Artikel für Sie hilfreich?
![]() |
![]() |
![]() |
![]() |
![]() |
Bitte bewerten Sie diese Seite durch Klick auf die Symbole.
Zugriffe heute: 1 - gesamt: 2211.