Poleposition bei der Zerspanung
BBS Motorsport setzt auf Fanuc-Steuerung
Beim Zerspanen von Guss- und Schmiederohlingen zu Rädern für Formel 1 Boliden und andere Rennwagen zählt die Zeit. Beste Ergebnisse erzielt der Premiumhersteller BBS Motorsport unter anderem mit Matsuura-Bearbeitungszentren. Die bevorzugte Steuerungs- und Antriebstechnik stammt vom Weltmarktführer Fanuc.
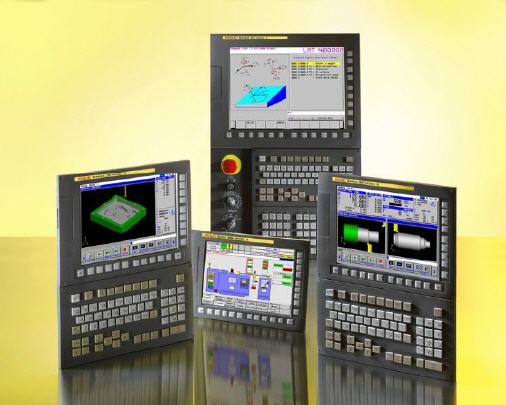
CNCs für Kenner und Könner: Fanuc-Steuerungen
Seine Leidenschaft für den Motorsport ist Roman Müller, Geschäftsführer der BBS Motorsport GmbH, unschwer anzumerken. Mit Begeisterung erzählt er von den Leichtmetallrädern, die sein Unternehmen entwickelt und produziert, und von den Erfolgen, die seit über 40 Jahren in jeglicher Rennsportklasse auf BBS-Räder erzielt werden. Ein Beispiel: Alle Weltmeisterschaftserfolge, die Michael Schumacher für Ferrari errang, fanden auf BBS-Rädern statt.
Roman Müllers Anspruch an sich selbst und sein erfahrenes Team ist dementsprechend hoch: „Wir wollen gemeinsam mit den führenden Rennteams die weltbesten Leichtmetallräder entwickeln, die für die entscheidenden Hundertstelsekunden Vorsprung sorgen.”
Seit 40 Jahren erfolgreicher Partner des automobilen Rennsports
Zahlreiche Entwicklungs-Highlights säumen die Unternehmensgeschichte. Bereits seit 1972 stellt BBS (1970 gegründet) dreiteilige Räder her, die aus einem Radstern sowie einer Außen- und einer Innenschüssel bestehen. Während letztere in verschieden Größen auf Lager liegen, wird der vorkonfektionierte Radstern kurzfristig auf die jeweiligen Fahrzeuge angepasst. Durch das Baukastensystem lassen sich viele Varianten hinsichtlich Breite, Einpresstiefe und Durchmesser kreieren. „In einer Woche ist ein solches individuelles Rad fertig”, sagt Roman Müller, „und der Kunde kann mit seinem Sportfahrzeug auf der Rennstrecke fahren.”
Dreiteilige Räder sind nach wie vor beliebt, doch heute dominieren einteilige Leichtmetallräder, die zumeist in einem Stück massiv gegossen oder geschmiedet werden. Sie vereinen die Leichtigkeit der speziellen Legierungen mit höchster Stabilität – ohne Schwachstellen, wie Roman Müller betont. Um dies zu garantieren, durchlaufen sie bei BBS Motorsport vielfältige Produktionskontrollen – das erste Mal bereits vor der Zerspanung, um sicher zu gehen, dass die Materialgüte den Ansprüchen genügt. Es folgen In-Prozess-Messungen auf den Werkzeugmaschinen und abschließend eine dreidimensionale 100%-Prüfung im Messraum.
Einen Meilenstein hinsichtlich Gewicht, Steifigkeit und Langlebigkeit setzte BBS mit der Entwicklung des Magnesium-Schmiederads. Für Roman Müller ein großer Erfolg: „Anfang der 90er Jahre war Ferrari der erste Rennstall, der unser Magnesium-Schmiederad für die Formel 1 genommen hat. Heute sind solche Räder zum Standard geworden, und werden leider nicht mehr nur von uns produziert.”
Doch nicht nur hinsichtlich der Materialien zeichnet sich BBS Motorsport durch Innovationen aus, auch auf Bearbeitungsseite hat das Unternehmen Maßstäbe gesetzt. Zum Beispiel lässt sich durch Hinterfräsen der Speichen das Verhältnis zwischen Gewicht und Stabilität optimieren. Hierbei werden Teile des Rades abgetragen, die für die Festigkeit nicht relevant und damit unnötiger Ballast sind. Eine ursprünglich von BBS entwickelte Technik, die heute vielfach kopiert wird.
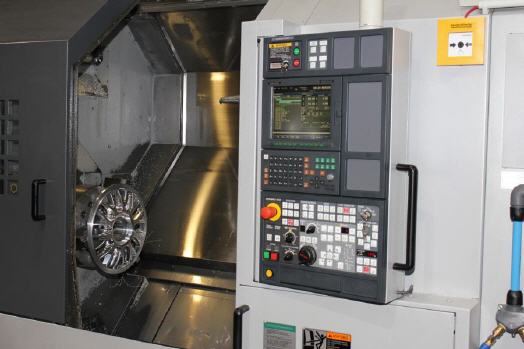
Mori Seiki SL403 mit Fanuc-Steuerung
Bei der Zerspanung die Nase vorn
Um solche diffizielen Bearbeitungen wirtschaftlich ausführen zu können, muss der Radhersteller in der Produktion topp ausgerüstet sein. Roman Müller hat sich in der Zerspanung auf zwei wesentliche Ausrüster festgelegt: Mori Seiki liefert die Dreh- und Matsuura die Fräsmaschinen.
An diesen Anbietern schätzt der Firmenchef in erster Linie die hohe Langzeitqualität. Die Matsuura-Bearbeitungszentren lobt der Rennsport-Lieferant zudem für ihre Schnelligkeit: „Als wir 1999 in die Hochgeschwindigkeitsbearbeitung einstiegen, haben wir Zentren verschiedener Anbieter getestet. Für unsere Anforderungen in der Leichtmetallbearbeitung schnitt die FX70 von Matsuura mit Abstand am besten ab.”
Bis zu dem Zeitpunkt bekam BBS üblicherweise den Rohling endkonturnah vorgeschmiedet, so dass nur noch eine geringe Fräs- und Bohrbearbeitung durchzuführen war. Um den sogenannten Near Netshape-Rohling herzustellen, musste allerdings in sehr teure Schmiedewerkzeuge investiert werden – was sich eigentlich nur bei höheren Stückzahlen lohnte, die wiederum im Rennsport selten sind.
So suchte das Team um Roman Müller nach einer Alternative und fand sie in der Hochgeschwindigketsbearbeitung von als Scheibe geschmiedeten Rohteilen. Aus ihnen ließ sich mittels Dreh- und Fräsbearbeitung jede gewünschte Kontur herausarbeiten – kundenspezifische sowie eigene Stylings. Roman Müller erklärt: “Wenn man in eine teure Schmiedeform investiert hat, ist man auf Jahre gebunden. Mit unseren Fünf-Achs-Fräsmaschinen haben wir an Flexibilität gewonnen und können Ideen innerhalb von zwei Wochen umsetzen und dem Kunden präsentieren.”
CNC- und Antriebstechnik vom Weltmarktführer
In den Folgejahren ist BBS Motorsport dem Hersteller Matsuura treu geblieben. Fertigungsleiter Francisco Serrano erinnert sich: “Schon seit Jahren setzen wir Werkzeugmaschinen mit Steuerungs- und Antriebstechnik von Fanuc ein und haben damit beste Erfahrungen gemacht. Die Produkte sind von herausragender Qualität, so dass wir damit in all den Jahren keinerlei Probleme hatten.
Zudem ist die Menüführung der CNC sehr einfach. Wir haben uns 2007 entschieden, Matsuura-Maschinen mit der Fanuc CNC der Serie 30i-A zu bestellen.” Er weist außerdem auf einen Vorteil hin, der aus der Durchgängigkeit des CNC-Fabrikats in seiner Fertigung resultiert: Facharbeiter, die sich mit einer Fanuc CNC auskennen, sind problemlos ohne zusätzliche Ausbildung maschinenübergreifend einsetzbar. Außerdem vermeidet die eingeschränkte Steuerungsvielfalt Schulungskosten und Fehler.
Für die NC-Programme sind in erster Linie die Maschinenbediener verantwortlich. Sie werden von Arbeitsvorbereitern unterstützt, die ein externes CAD/CAM-System nutzen, insbesondere für Designelemente mit komplexen Formen. Der Werker erhält hierfür fertige Unterprogramme, die er mit selbst erstellten Bohr- und Drehzyklen zu Hauptprogrammen zusammenfügt. Außerdem integriert er die zur In-Prozess-Kontrolle notwendigen Messprogramme.
Das klingt kompliziert, ist aber mit der Fanuc-Werkstattprogrammiersoftware ›Manual Guide i‹ einfach zu bewältigen. Sie vereint quasi zwei Programmierwelten, indem sie zum einen eine komfortable Dialogprogrammierung ermöglicht und zum anderen die Programmierung in DIN ISO oder mit Makros unterstützt. So kann jeder Anwender – je nach Anforderung und individuellen Kenntnissen – die optimale Programmierart wählen. Zudem lassen sich die verschiedenen Verfahren beliebig untereinander kombinieren. Bereits vorhandene DIN ISO-Programme können problemlos eingefügt und weiterbearbeitet werden.
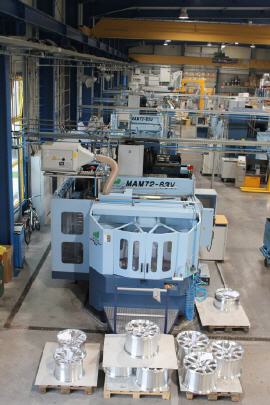
Fünfsachsige Räderbearbeitung mit Matsuura-BAZs
Hilfreiche CNC-Funktionen
Beim Zerspanen ist BBS Motorsport darauf aus, den optimalen Kompromiss zwischen kurzer Bearbeitungszeit und hoher Oberflächengüte zu finden. Unterstützung liefert die Fanuc-CNC der Serie 30i-A, mit der die Matsuura Bearbeitungszentren MAM72-63V ausgestattet sind und die als Highend-Steuerung optimal für Hochgeschwindigkeits (HSC)- und Fünf-Achsen-Bearbeitung ausgelegt ist.
Das heißt, sie ist nicht nur sehr schnell, sondern stellt auch eine Vielzahl von Softwarefunktionen für die Fünf-Achs-Bearbeitung zur Verfügung, um das vorhandene Potential der Maschine optimal auszunutzen. Für den HSC-Einsatz bietet sie das automatische Vorschubkontrollsystem AICC. Unter dieser Bezeichnung – AICC steht für Artifical Intelligence Contour Control – hat Fanuc Funktionen zusammengefasst, die Beschleunigungs- und Bremsvorgänge optimieren sowie Geschwindigkeiten automatisch für Eckenbearbeitung oder Kreissegmente anpassen können.
Somit übernimmt die AICC-Funktionalität gewissermaßen eine Voraussteuerung, die dafür sorgt, dass das Werkzeug der vorgegebenen Bahn mit hoher Konturtreue folgen kann.
Das ist beispielsweise bei schwer umsetzbaren Designstudien von Vorteil, wie Fertigungsleiter Francisco Serrano erklärt: “Kürzlich mussten wir einen Verlauf von Bohrungen einbringen, deren Durchmesser bei 0,4 mm begannen und die dann zunehmend größer wurden. Auch bei den sehr kleinen Radien mussten die Kanten messerscharf sein, was beim Fräsen ein entsprechend feines Arbeiten erforderte. Das haben wir mit der Fanuc-gesteuerten Matsuura perfekt hinbekommen.”
Im Allgemeinen versucht das BBS-Fertigungsteam bei der Leichtmetallbearbeitung Drehzahlen von bis zu 27.000 min-1 zu nutzen. Bei Aluminium werden Vorschübe von 8 bis 10 m/s, bei Magnesium 12 bis 14 m/s gefahren – bei einer Zustellung von 5 mm. Für die einfache Parametereinstellung nutzt BBS die in der Fanuc-CNC 30i-A angebotene Machining Level Condition Function, mit der der Anwender die Faktoren Präzision, Geschwindigkeit und Oberflächengüte gewichten kann.
Die Steuerung stellt dann selbst das optimale Parameter-Set zusammen. Hierbei wird auch die Fähigkeit der Steuerung ausgenutzt, Splines zu verarbeiten und die Oberflächenqualität mithilfe der Funktion Nano-Smoothing 2 zu optimieren. Francisco Serrano: “Zusammen mit den Anwendungstechnikern von Matsuura haben wir die gewünschten Schnittwerte und Oberflächengüten definiert und mit Hilfe dieser Funktion auf allen Maschinen eingestellt. So sind unsere Bearbeitungsergebnisse gleichbleibend gut.”
Er lobt weiterhin die extrem hohe Verfügbarkeit aller Fanuc-Komponenten: “In den letzten zwölf Jahren haben wir insgesamt nur vier Fanuc-Kundendienst-Einsätze gehabt. Davon war einer selbst verschuldet, zwei waren durch Verschleiß und nur einer durch eine defekte Achskarte verursacht.” Schließlich fasst der Fertigungsleiter zusammen: “Letztendlich sind zwar die Maschinen und ihre Leistungsfähigkeit entscheidend, aber wir haben mit Fanuc-Steuerungen und Antrieben so gute Erfahrungen gemacht, dass diese Komponenten bei unserer Entscheidung über den Kauf einer Werkzeugmaschine mit entscheiden.”
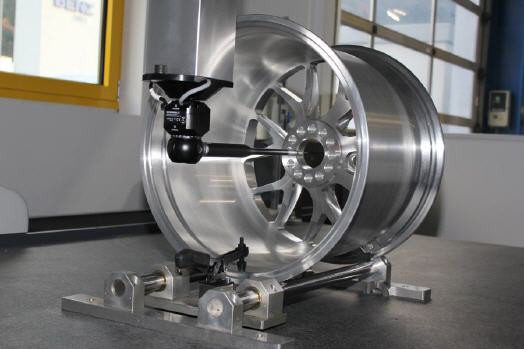
Alle Räder von BBS werden 100% geprüft
Mehr Informationen zu FANUC FA Deutschland GmbH:
![]() |
FANUC FA Deutschland GmbH |
![]() |
Bernhäuser Straße 22 |
![]() |
73765 Neuhausen a.d.F. |
![]() |
Tel.: (+49) (0)7158 187 - 400 |
![]() |
Fax: (+49) (0)7158 187 - 455 |
![]() |
E-Mail: info@fanuccnc.de |
![]() |
www.fanuccnc.de |
War dieser Artikel für Sie hilfreich?
![]() |
![]() |
![]() |
![]() |
![]() |
Bitte bewerten Sie diese Seite durch Klick auf die Symbole.
Zugriffe heute: 1 - gesamt: 2739.