Via MMS zu höheren Standzeiten
Aufbauschneiden verhindern
Ölmenge, Volumenstrom und Druck des MMS-Aerosols können direkt in der digitalen Prozesskette eingespiesen werden. Dies bietet gegenüber konventionellen Kühlschmierstoffen einen deutlichen Vorteil. Weiter lassen sich mit der optimalen Kombination von MMS-Öl und -Werkzeugen sowohl eine Produktivitätssteigerung als auch eine Erhöhung der Werkzeugstandzeit realisieren. Mit der Steigerung des Vorschubs und der Schnittgeschwindigkeit von 130 m/min auf 390 m/min in rostfreiem Stahl (1.4307) stieg beispielsweise die Produktivität um über 70 Prozent, wie ein Versuch im Technologiecenter von Blaser Swisslube eindrucksvoll belegt.
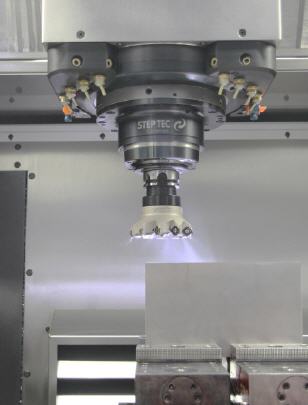
Kühlschmierstoffe, Minimalmengenschmierung und Kältemittel-Komponenten sind ein komplexes Thema. Unabhängig der Methode sind die Hauptziele der Zerspanungsindustrie hohe Prozesssicherheit und Produktivität. Neben diesen wirtschaftlichen Punkten spielen auch Umweltschutzaspekte eine zunehmend wichtige Rolle. Diese führen bestenfalls auch zu Einsparungspotential im Hinblick auf Energie und weiterer Ressourcen.
Alle KSS-bezogenen Schmiermethoden, inkl. MMS, haben eine gemeinsame Charakteristik: kontinuierliches zielgerichtetes Einbringen des Kühlschmierstoffs in die Schnittzone. Dies muss präzise auf die Frei- und Spanfläche des Schneidwerkzeugs erfolgen. Am besten erreicht man dies mithilfe der internen KSS-Zufuhr.
Verfahren und Vorteile bei der Minimalmengenschmierung (MMS)
Beim MMS-Verfahren entsteht ein Aerosol, welches aus einer Öl-Luft-Mischung besteht. Diese Mischung bildet einen Schutzfilm, welcher die Reibung reduziert und dem Verschleiss des Werkzeugs direkt entgegengewirkt. Eine Kühlung des Schneidwerkzeugs wird mithilfe von erzwungener Konvektion durch die Pressluft, angefeuchteten Oberflächen und Verdampfungsenthalpie erreicht, resp. gesteuert.
Verfahren wie Hochgeschwindigkeitsschneiden (HSC) oder Hochvorschubschneiden (HFC) sind die Voraussetzung für ein erfolgreiches Schneiden mit MMS. In diesem Fall sind für ein MMS-optimiertes Schneideverfahren kleinere konstante Umschlingungswinkel erforderlich, um die aufs Werkzeug einwirkende Hitze zu reduzieren.
In den letzten Jahren ist es zu einer intensiven Entwicklung bei MMS-Geräten, Zufuhrsystemen und bei den Schneidwerkzeugen selbst gekommen. Im Vergleich zur Nassbearbeitung stellt die MMS eine flexiblere Anwendung dar, da die Flüssigkeit in kleineren Mengen zugeführt wird. Aufgrund dieser Flüssigkeitsreduzierung muss jedoch die kontinuierliche und zielgerichtete Zufuhr des MMS-Aerosols zum Schneidwerkzeug genau überwacht werden. Der geringere Energieverbrauch, die Sauberkeit von Bauteilen und Spänen und die gute Materialverträglichkeit sind weitere Vorteile dieser Methode.
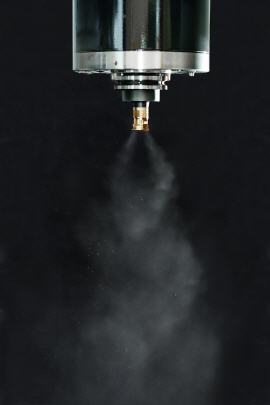
MMS und die Industrie 4.0
Die Integration von MMS und modernen MMS-Systemen in die digitale Prozesskette lässt sich einfacher und rascher umsetzen, als mit herkömmlichen KSS. Das regelmässige Messen der unterschiedlichen Parameter wie z.B. Konzentration, pH-Wert, etc. entfällt komplett. Da es sich beim MMS hauptsächlich um Öl handelt, stellt auch die Erkennung von Verunreinigungen, Partikelgrössen, etc. kaum Probleme dar.
Bei der MMS-Bearbeitung werden die Menge des zugeführten Öls und der Pressluft (Volumenstrom und Druck) in modernen MMS-Systemen erfasst. Diese Daten können direkt mit dem Produkt und den Prozessdaten in der digitalen Prozesskette integriert werden. Somit können alle kritischen Prozessvariablen, vom Schneidwerkzeug bis zu Werkzeugmaschine, Zufuhr, Geschwindigkeit und Schmierstoffversorgung zum gewünschten Zeitpunkt überwacht werden.
Angaben wie z. B. Pressluftverbrauch und der damit verbundene Stromverbrauch und -verlust, können laut Dr. Ivan Iovkov. angepasst und abgeschätzt werden. Aerosolqualität und Ölanteilmessung beim Düsenaustritt stellen zwar komplexere Aufgaben dar, welche jedoch durch individuelle Anpassung seitens des Maschinenbedieners für das jeweilige Werkzeug gelöst werden können.
Das folgende Beispiel von Hochgeschwindigkeitsschneiden in Edelstahl (Inox) zeigt eindrücklich das Potential einer MMS-Strategie.
Erfolgreicher MMS-Versuch im Technologiecenter von Blaser Swisslube
Die Fräsoperation im 1.4307 wurde bis anhin meist trocken bearbeitet. Ziel des Versuches war, mittels MMS das Verfahren zu optimieren und einen Mehrwert zu erzielen. Zu Beginn wurden verschiedene Fraisa-Fräswerkzeuge und MMS-Produkte von Blaser Swisslube miteinander verglichen. Anschliessend wurden die verschiedenen Verfahren mit der optimalen Werkzeuggrösse und dem optimalen MMS-Öl beurteilt.
Ein Überblick über das gesamte Verfahren ist essentiell für eine optimale MMS-Bearbeitung. Darunter fällt das MMS-Gerät selbst, das Aerosol wie auch Vorbereitung und -Zufuhr. Auch die Werkzeugausstattung muss für die MMS-Zufuhr geeignet sein. Nur wenn ein konstantes und konsistentes Aerosol mit gutem Sprühverhalten in der Werkzeug-Austragsdüse erzeugt wird, können Verbesserungen erreicht werden.
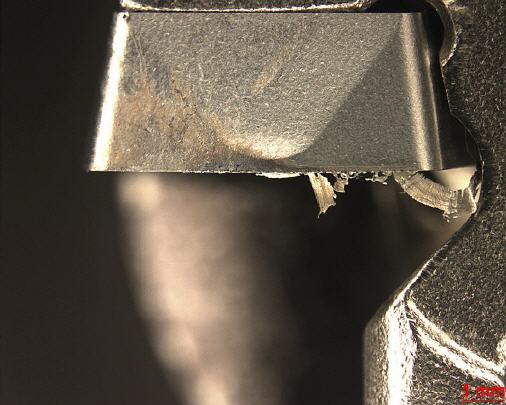
Resultat: Erhöhung der Werkzeugstandzeit und Produktivität
Während dem durchgeführten Test überzeugte das MMS-Produkt Vascomill MMS FA2 und erreichte eine Erhöhung der Werkzeugstandzeit um 243 Prozent bei einer Steigerung der Vorschub- und Schnittgeschwindigkeit. Letztere wurde von 130 m/min auf 390 m/min erhöht. Die Produktivität stieg dadurch gesamthaft um 70 Prozent. Weiter konnte dank der optimalen MMS-Strategie die Aufbauschneide an der Schneidekante verhindert werden.
Titanbearbeitung mit MMS
Materialien, die sich nur schwer bearbeiten lassen, wie z. B. Titan und Inconel, stellen die MMS-Anwendung vor eine grosse Herausforderung. Hervorragende Werkzeugstandzeiten und Schnittgeschwindigkeiten können zwar beim Gewindeformen und beim Titanschneiden erreicht werden. Beim Fräsen und Bohren sind die entsprechenden Werkzeuge und Bearbeitungsstrategien jedoch noch nicht definiert. In diesem Bereich bleiben einige offene Fragen. Es sind weitere Forschungen, ein tieferes Verständnis der Bearbeitungsprozesse sowie deren Weiterentwicklung erforderlich.
Mehr Informationen zur Blaser Swisslube AG:
![]() |
Blaser Swisslube AG |
![]() |
Winterseistrasse 22 |
![]() |
CH-3415 Hasle-Rüegsau |
![]() |
Tel.: +41 34 460 01 01 |
![]() |
E-Mail: contact@blaser.com |
![]() |
www.blaser.com |
War dieser Artikel für Sie hilfreich?
![]() |
![]() |
![]() |
![]() |
![]() |
Bitte bewerten Sie diese Seite durch Klick auf die Symbole.
Zugriffe heute: 26 - gesamt: 9035.