Geboren aus sehr feinem Staub
Keramikteile additiv herstellen
Die additive Fertigung hat sich bereits einen großen Markt erobert. Ob Konstruktionsmuster oder Ersatzteil für Turbinentriebwerke, immer zahlreicher werden diejenigen Werkstücke, die nicht mehr durch Zerspanen hergestellt werden. Sogar aus Keramik lassen sich mittlerweile Teile im 3D-Druck herstellen, wie das Unternehmen WZR ceramic solutions GmbH seit 2010 demonstriert.
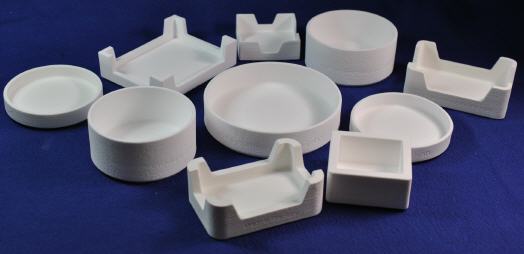
Geht es um die Produktion hochtemperaturbeständiger Bauteile, kommt man am Werkstoff ›Keramik‹ nicht vorbei. Der technische Werkstoff ist besonders dort in seinem Element, wo es heiß hergeht. Aber auch die außergewöhnliche Abriebfestigkeit des Materials ist seit jeher geschätzt, weshalb aus diesem Material Hitzeschutzkacheln für Raumfahrzeuge ebenso hergestellt werden, wie Gleit- und Kugellager für Getriebe oder Wendeschneidplatten zum Schlichten von schwer zerspanbaren Stählen.
Besonders interessant ist, dass sich Keramik auch im 3D-Druck-Umfeld verarbeiten lässt. Dass dies hervorragend funktioniert, hat das Unternehmen WZR schon oft unter Beweis gestellt. Die Experten liefern Bauteile für Brennträger ebenso wie Gießkerne, Katalysatorträger oder Designteile. In diesem Prozess kommt Keramikgranulat mit Korngrößen von nur 10 bis 50 Mikrometer zum Einsatz, das im Pulverbettverfahren schichtweise verfestigt wird.
Während beim additiven Fertigen von Metallbauteilen meist ein Laserstrahl die Metallpulverkörnchen aufschmilzt und sich diese somit verbinden, kommt zum Verbinden des Keramikpulvers eine Art Klebstoff zum Einsatz, der über Düsen, ähnlich einem Tintenstrahldrucker, auf die Oberfläche des Keramikpulvers aufgesprüht wird. Kapillarkräfte erzeugen im Anschluss eine saugende Wirkung, die den Klebstoff tief in das Pulver eindringen lassen, sodass die einzelnen Pulverkörnchen sicher benetzt werden.
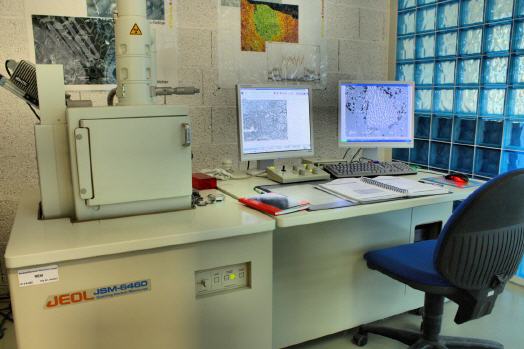
Interessant ist die dahinterstehende Technik, die den Klebstoff auf das Keramikpulver sprüht. WZR nutzt dazu wahlweise zwei Verfahren, die auch bei 3D-Tintenstrahldruckern zum Einsatz kommen: die Bubble-Jet-Technologie sowie das Piezo-Verfahren.
Beim Bubble-Jet-Verfahren wird ein kleines Metallplättchen in kürzester Zeit auf mehrere Hundert Grad erhitzt, wodurch eine Dampfblase innerhalb der Tinte, beziehungsweise dem Klebstoff entsteht. Diese Dampfblase presst dann einen Klebstofftropfen aus der Düse auf das Keramikpulver.
Die Piezo-Technik hingegen nutzt Schwingungen eines Piezo-Kristalls, die durch elektrische Impulse entstehen. Diese Schwingungen werden auf eine Membran gelenkt, wodurch Klebstoff impulsweise aus dem Druckkopf gepresst wird. Die Experten von WZR entwickeln beide Verfahren weiter, da jede Technik ihre speziellen Vorteile hat. Aktuell sind Druckköpfe mit unglaublichen 1 000 Düsen im Einsatz, die besonders detailreiche Keramik-Bauteile durch das ausgesprochen präzise Aufsprühen des Klebstoffs erlauben.
Die Schichtdicke von additiv gefertigten Keramikteilen liegt aktuell zwischen 50 und 150 Mikrometer. Das perfekte Aufbringen dieser Schichten ist eine besondere Herausforderung und alles andere als trivial. Vor allem wenn man bedenkt, dass mit zunehmender Feinheit des Pulvers dessen „Fließfähigkeit“ abnimmt. Der Grund liegt darin, dass Keramikpulver nicht aus kleinen Kügelchen besteht, sondern aus geometrischen Elementen, deren Kontur unstrukturiert ist. Sie ähneln somit dem sogenannten ›Split‹ aus Granit.
Da Körper mit derartigen Strukturen sich gegenseitig verhaken, musste eine besondere Konstruktion zum Aufbringen der Keramikpulverschichten ersonnen werden. Es wären durchaus feinere Schichtdicken unterhalb von 50 Mikrometer denkbar, doch steigen zum einen die Materialkosten stark an, je feiner das Pulver ist, zum anderen sind bei der Verarbeitung feinerer Pulversorten zusätzliche Maßnahmen beim Verarbeiten sowie der Logistik zu treffen.
Auch beim eigentlichen Bauvorgang ist besonderes Wissen gefragt: Es kommt darauf an, eine exakte Menge Klebstoff auf die einzelnen Schichten aufzutragen. Zudem hat sich herausgestellt, dass es von Vorteil ist, auf der Werkstückaußenseite mehr Klebstoff aufzutragen als im Innenteil. Es ist also viel Erfahrung nötig, um beim 3D-Druck von Keramik gebrauchstüchtige Teile zu produzieren.
Nach dem 3D-Druck besitzt das Werkstück noch keine Gebrauchsfestigkeit. Diese ergibt sich erst nach dem sogenannten Sintern. Bei diesem Prozess werden die Keramikteile auf 1 400 bis 1 700 Grad Celsius erhitzt, woraufhin der Klebstoff verdampft und sich die Keramikpartikel zu einer festen Struktur verbinden. Bei diesem Prozess schrumpft das Teil um 5 bis 20 Prozent je nach Rezeptur und Keramikmaterial. Dieser Schwund muss vom Konstrukteur berücksichtigt werden, sollen maßgenaue Teile aus dem Ofen kommen. Wird dies beachtet, sind problemlos Werkstücke mit einer Endgenauigkeit von ± 0,1 Millimeter herstellbar.
Zusätzlich ist zu bedenken, dass beim gerade beschriebenen Prozess kein absolutes Schließen der Poren vonstattengeht. Nach der Wärmebehandlung weisen die Teile eine Porosität zwischen 20 und 50 Prozent auf. Dies ist jedoch gerade für Filter und Katalysatoren erwünscht. Sind dichtere Strukturen gefragt, so müssen dem Kleber feine Partikel zugemischt werden, die dann die Hohlräume zwischen den Keramikkörnchen ausfüllen. Auf diese Weise ist ein dichtes Gefüge erreichbar.
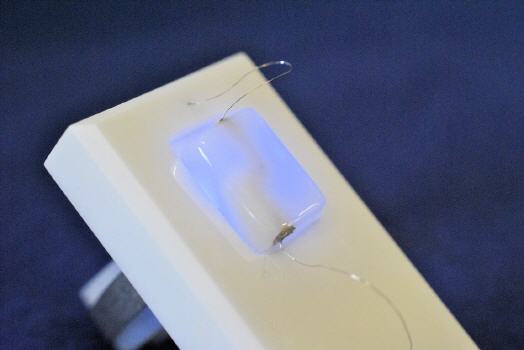
Mittels des sogenannten Multi-Material-3D-Drucks ist WZR in der Lage, mehrere Materialien gezielt kombiniert zu verarbeiten. Damit sind Strukturen möglich, wie sie bereits in ähnlicher Weise beim Herstellen von Prozessoren und Speicherbausteinen üblich sind. Natürlich sind die geometrischen Dimensionen keinesfalls vergleichbar, doch ist es mit dieser Technik möglich, leitfähige Strukturen zu erzeugen. Dazu werden dem aufgespritzten Klebstoff leitfähige Partikel beigemischt, um auf diese Weise Lagen zu erzeugen, die elektrischen Strom leiten können. Dazu eignet sich beispielsweise Silber, das die höchste Leitfähigkeit aller Metalle besitzt.
Dies eröffnet ganz neue technische Möglichkeiten. Mit dieser Technik sind zum Beispiel Strukturen aus Keramik möglich, die dank eines Metallkerns als Antenne fungieren können. Durch die rundum vorhandene Isolation kann deren Abstrahlcharakteristik auch nicht durch Berühren beeinflusst werden. Dank dieser Eigenschaft besitzen solche Antennen einen hohen Wirkungsgrad und können dadurch entsprechend klein gebaut werden. Sie eignen sich deshalb vorzüglich für den Einsatz in kleinen Consumer-Geräten.Selbstredend, dass das WZR neben anderen Prüf- und Analysegeräten auch über ein sogenanntes Rasterelektronenmikroskop verfügt, um die Qualität seiner Produkte sicherzustellen. Das Equipment steht auch anderen Unternehmen als Dienstleistung zur Verfügung. Somit ist WZR der erste Ansprechpartner, wenn es um technische Keramik geht.
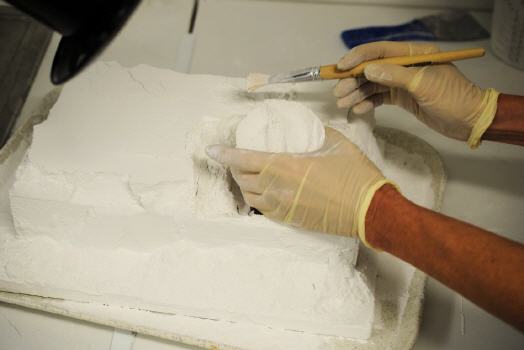
Mehr Informationen zum Werkstoffzentrum Rheinbach:
![]() |
Werkstoffzentrum Rheinbach GmbH |
![]() |
Lise-Meitner-Straße 1 |
![]() |
53359 Rheinbach |
![]() |
Tel.: 0049 (0) 22 26/ 16 98 10 |
![]() |
Fax: 0049 2226 1698-66 |
![]() |
E-Mail: info@wzr.cc |
![]() |
www.wzr.cc |
War dieser Artikel für Sie hilfreich?
![]() |
![]() |
![]() |
![]() |
![]() |
Bitte bewerten Sie diese Seite durch Klick auf die Symbole.
Zugriffe heute: 18 - gesamt: 11149.