Mit Schrumpftechnik zum Erfolg
Spannmittel für hohe Drehzahlen
Der sichere Halt des Fräsers und ein hochpräziser Rundlauf sind die wesentlichen Merkmale der Schrumpftechnik. Diese Technik nutzt die physikalische Eigenschaft der Wärmeausdehnung von Stoffen. Damit dieses Phänomen in der Werkzeugspanntechnik genutzt werden kann, ist viel Wissen seitens der Schrumpfgeräte-Hersteller nötig, was ohne Zweifel das Unternehmen Bilz vorweisen kann.
Die Schrumpftechnik ist ein relativ junger Zweig der Spannmittelindustrie. Dieses Verfahren, Fräswerkzeuge auf alternative Weise zu spannen, entwickelte sich im Zuge der rasanten Techniksprünge in der Werkzeugmaschinenbranche ab den 1990er Jahren. Immer höhere Drehzahlen, Vorschübe und Richtungswechsel durch die Mehrachsbearbeitung brachten herkömmliche Spannmittel zunehmend an ihre Grenzen.
Die ersten Versuche in Sachen Schrumpftechnik machte in Deutschland die Firma Marquart, die die Schrumpffutter mithilfe einer Flamme beziehungsweise eines Heißluftföns manuell aufheizte. Diese wenig industrietaugliche Methode wurde 1993 durch Harold Cook in den USA dahingehend verbessert, dass zum Erhitzen erstmals die elektromagnetische Induktion eingesetzt wurde. Kurze Zeit später erwarb das schwäbische Unternehmen Bilz eine Lizenz von Cook zur Nutzung des Patents und damit zum Vertrieb des „Shrinkers“, dem ersten induktiven Schrumpfgerät überhaupt.
Aus der kontinuierlichen Weiterentwicklung dieses Gerätes wurde im Laufe der Jahrzehnte ein breites Sortiment an Schrumpfgeräten für diverse Einsatzbereiche geschaffen. Eine bahnbrechende Verbesserung stellte die Erkenntnis von Bilz/Innovat dar, dass die Werkzeuge beim Ausschrumpfen gegen das Streufeld abgeschirmt werden müssen. Der Erfolg eines optimalen Schrumpfprozesses liegt mitunter darin, dass lediglich das Futter erhitzt wird, das Werkzeug dagegen kalt bleibt. Diese Abschirmung erreicht Bilz/Innovat durch den Einsatz der patentierten Ferritscheiben, mittels derer es erstmals möglich war, Werkzeuge aller Materialien prozesssicher auszuschrumpfen.
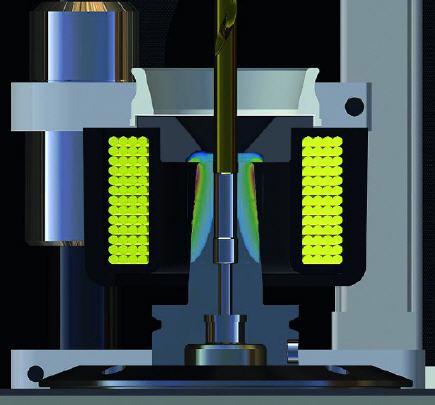
Schrumpf-Pioniere
Der Schrumpftechnik haben sich in der Vergangenheit einige Unternehmen zugewendet. Um Synergieeffekte bei der Weiterentwicklung zu nutzen, schlossen sich die Firmen Bilz, Diebold und Komet im Jahr 2000 gemeinsam mit Marquart zur ThermoGrip-Gruppe zusammen.
Um das manuelle Handling weiterzuentwickeln und sicherer zu gestalten, hat Bilz die von Marquart patentierte Vorweite serienmässig in seine Futter eingearbeitet. Die Vorweite ermöglicht es, dass beim Erhitzen des Futters zum Einschrumpfen das Werkzeug automatisch durch sein Eigengewicht in das Futter hineingleitet und sich selbst zentriert.
Um die Schrumpftechnologie benutzerfreundlicher zu gestalten, hat Bilz die für die jeweiligen Futter notwendigen Schrumpfparameter (Zeit und Leistung des Spulenstroms) ermittelt. Die Maxime hierfür lautet: ›so viel wie nötig und so wenig wie möglich‹. Wird zu wenig Energie eingebracht, funktioniert das Ein- und Ausschrumpfen nicht. Mit zu viel Energie wird das Futter überhitzt und damit über Kurz oder Lang zerstört. Diese Parameter sind standardmäßig in den Bilz-Schrumpfgeräten hinterlegt, sodass der Bediener mit der Auswahl des richtigen Futtertyps sicher sein kann, dass das Schrumpfen korrekt durchgeführt wird.
Genauso wichtig wie das korrekte Erhitzen ist das gezielte Abkühlen des Schrumpffutters.
Hierfür gibt es völlig unterschiedliche Methoden: So mancher Hersteller setzt auf das Anblasen von Luft, andere auf die Kontaktkühlung oder die Flüssigkeitskühlung. Bilz setzte zu Beginn auf die Kontaktkühlung bei der zusätzlich ein Kühlkörper, der von Kühlluft durchströmt ist, über das erhitzte Futter gestülpt wird. Heute setzt Bilz vorwiegend auf die effektivere Flüssigkeitskühlung, die Bilz daher bei vielen gängigen Geräten einsetzt. Das Futter wird mit einer speziellen Kühlflüssigkeit besprüht und durch Verdunstungskälte abgekühlt. Dieser Kühlflüssigkeit ist gleichzeitig ein Schmiermittel beigemischt, um das Futter vor Rost durch Handschweiß des Bedieners zu schützen.
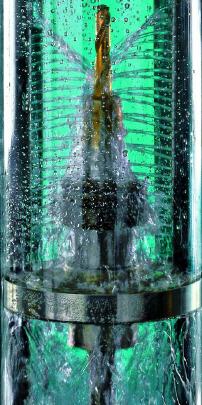
Schrumpffehler vermeiden
Bei der manuellen Eingabe der Schrumpfparameter besteht die Möglichkeit, dass der Bediener eine falsche Futtertype und somit falsche Parameter für den Schrumpfprozesses wählt. Dies kann dazu führen, dass ein Werkzeug nicht ein- oder ausgeschrumpft werden kann oder das Schrumpffutter überhitzt und im Extremfall sogar zerstört wird.
Zur Auswahl der jeweils genau richtigen Schrumpfparameter für das aktuelle Futter bietet Bilz verschiedene Lösungen: Die Identifikation der Futtertypen kann über Barcodes auf externen Tabellen, über einen QR-Code an einer geeigneten Stelle am Schrumpffutter oder wahlweise über den Einbau eines RFID-Chips im Schrumpffutter erfolgen. Alle diese Methoden haben das gemeinsame Ziel: das sichere Ein- und Ausschrumpfen der Werkzeuge aus den Schrumpffuttern und somit die Prozesssicherheit zu erhöhen. Jede dieser Lösungen hat ihre Vorzüge, sodass der Nutzer die für ihn passende Variante wählen kann.
Wird eine dieser Lösungen implementiert, kann die Steuerung der Bilz-Schrumpfgeräte für die manuelle Eingabe gesperrt werden, sodass nur die maschinell eingelesenen Schrumpfparameter angenommen werden.
Die umfassendste Lösung bietet das RFID-System, da über den im Futter eingesetzten Chip zahlreiche Zusatzinfos abrufbar sind. Außerdem kann der Code im Laufe der Zeit nicht durch Abnutzung unleserlich werden.
Ein weiterer Pluspunkt ist die Möglichkeit einer komfortablen Anbindung an eine Werkzeugdatenbank. Hinzu kommt, dass die Identifikations-Nummer jedes einzelnen RFID-Chips weltweit einmalig ist, sodass die eindeutige Zuordnung der Schrumpfparameter zu einem ganz bestimmten Werkzeug garantiert ist.
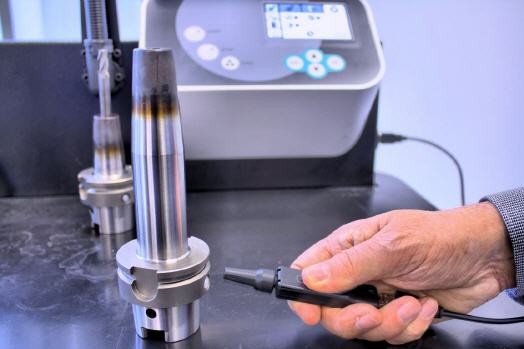
Staunenswerte Erkenntnis
Immer wieder ist zu vernehmen, dass Fräswerkzeuge aus Schrumpffuttern herausgezogen werden. Dies hat einen ganz besonderen Grund: In der Forschungsarbeit, die von B. Denkena und D. Heinisch an der Leibnitz Universität Hannover durchgeführt wurde, hat sich herausgestellt, dass der eigentliche Grund für das Herausziehen von Fräsern aus Schrumpffuttern in Mikrobewegungen der Futter liegt, die durch Schwingungen ausgelöst werden.
Dieses Phänomen tritt nur auf, wenn die Anregungsfrequenz (beim Fräser also Zähnezahl x Umdr. pro sec.) der ersten biegekritischen Eigenfrequenz des Systems aus Spindel, Spannfutter und Werkzeug entspricht. Die Übereinstimmung von Anregungs- und Eigenfrequenz wird Resonanz genannt, beziehungsweise aufgrund der teilweise fatalen Wirkung auch Resonanzkatastrophe. Die Eigenfrequenz ist sehr stark von der Masse des Futters abhängig. Je mehr Masse ein Futter hat, desto größer wird die Eigenfrequenz.
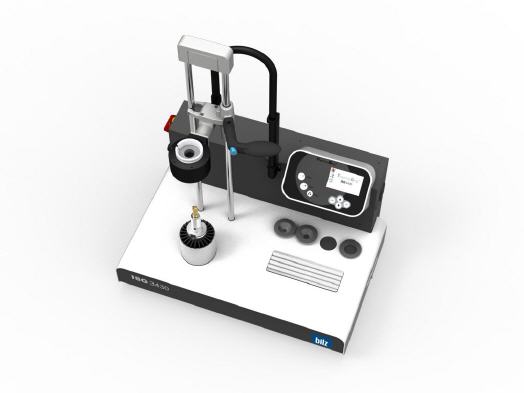
Masse verhindert Herausziehen
Speziell in der Schwerzerspanung ist daher unbedingt darauf zu achten, dass verstärkte, also massige Schrumpffutter verwendet werden. Damit werden nicht nur die hohen auftretenden Dreh- und Biegemomente beherrscht, sondern die Eigenfrequenz des Systems liegt deutlich oberhalb der Anregungsfrequenz, sodass eine Resonanzkatastrophe nicht auftreten kann.
Damit ist garantiert: der Fräser wird nicht aus dem Futter gezogen. Mehr Masse ist demnach das Geheimnis, auch ohne Auszugssicherung mittels Schrumpffutter problemlos das HPC-Fräsen mit hohen Schnitt- und Vorschubgeschwindigkeiten durchzuführen.
Fazit: Schrumpffutter eignen sich ideal für nahezu alle Zerspanungsarbeiten. Voraussetzung ist der korrekte Umgang mit dieser Technik, dann winken als Lohn nicht nur perfekt zerspante Werkstücke, sondern auch Spannzeuge für prozesssichere Werkzeugspannung, die nahezu keinen Verschleiß zeigen und somit fast unendlich oft nutzbar sind.
Download
Diesen Artikel finden Sie auch in Heft 4/2019 auf Seite 14. Zum besagten Heft führt ein Klick auf den nachfolgenden Button!
Mehr Informationen zu Bilz:
![]() |
Bilz Werkzeugfabrik GmbH & Co.KG |
![]() |
Vogelsangstrasse 8 |
![]() |
73760 Ostfildern |
![]() |
Tel. +49 711 348010 |
![]() |
Fax: +49 (0711) 34 81 256 |
![]() |
E-Mail: info@bilz.de |
![]() |
www.bilz.de |
War dieser Artikel für Sie hilfreich?
![]() |
![]() |
![]() |
![]() |
![]() |
Bitte bewerten Sie diese Seite durch Klick auf die Symbole.
Zugriffe heute: 19 - gesamt: 8178.