Kreuzfahrtschiffe edler Machart
Feinster Schiffbau aus Papenburg
Kreuzfahrten waren schon immer beliebt. Durch den weltweit steigenden Wohlstand wird dieser Markt in den kommenden Jahren weiter an Volumen zulegen, was Werften, die sich mit dem Bau von Kreuzfahrtschiffen beschäftigen, volle Auftragsbücher beschert. Die im norddeutschen Städtchen Papenburg ansässige Meyer Werft ist mit diesem Trend gewachsen, hat ständig in modernste Schiffsbautechnik investiert und zählt daher zum unangefochtenen Marktführer im Bau edler Kreuzfahrtschiffe.
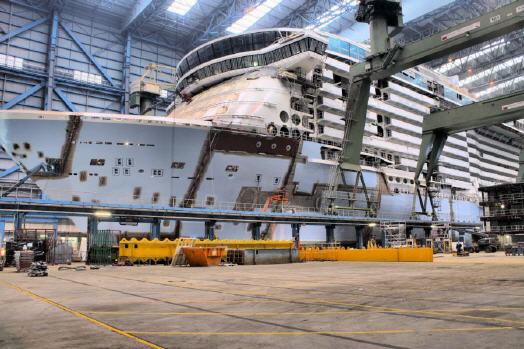
Werften haben es in Deutschland schwer, gegen Produktionsstandorte zu bestehen, die geringere Lohnkosten in die Waagschale werfen können. Insbesondere Südkorea und China punkten mit günstigem Lohnniveau sowie weit geringeren Energie- und Materialkosten. Wer jedoch genau hinsieht, stellt fest, dass in diesen Ländern überwiegend relativ einfache Schiffe, wie etwa Tanker oder Containerfrachter gebaut werden. Den Bau von Kreuzfahrtschiffen kann man hier nur selten registrieren, wenn überhaupt.
Warum dies so ist, können Besucher auf der Meyer Werft in Erfahrung bringen.Hier bekommen sie nicht nur modernsten Schiffbau im XXL-Format zu sehen, sondern erfahren darüber hinaus, dass an möglichst vielen Gewerken teure Handarbeit durch Hightech-Maschinen ersetzt wurde. Das 1795 gegründete Unternehmen hat es mit dieser Strategie geschafft, zum Big-Player im Bereich Kreuzfahrtschiffbau aufzusteigen. Das innovative Unternehmen hat mit lediglich 3300 eigenen Leuten und circa 1000 Zulieferern seit dem Umzug im Jahre 1975 an den jetzigen Produktionsstandort über 40 Luxusliner unterschiedlicher Größenklasse für Reedereien aus aller Welt gebaut. Beispielsweise hatten Schiffe der Aida-Flotte und der Norwegian-Reihe in Papenburg ihren Stapellauf.
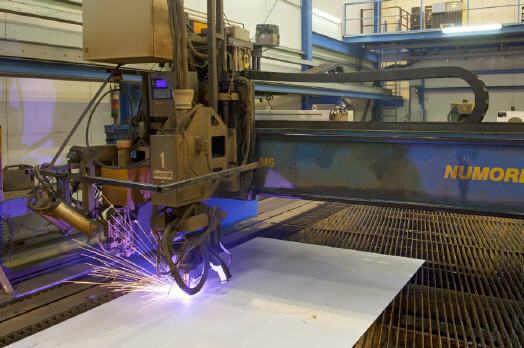
Eine Klasse für sich
Es hat sich unter den potenziellen Kunden herumgesprochen, dass die Experten der Meyer Werft nicht nur Schiffbau vom Feinsten zelebrieren, sondern den beim Verkaufsgespräch zugesagten Liefertermin auf den Tag genau einhalten. Dies bedeutet, dass Kreuzfahrtunternehmen bereits Buchungsprospekte und Online-Auftritte in Auftrag geben können, in denen der Abreisetag mit dem neuen Schiff explizit genannt wird. Dabei muss man sich immer vor Augen halten, dass man es hier mit einem Großprojekt zu tun hat, bei dem es gilt, per ausgefeilter Logistik tonnenweise Bleche, Rohre, Kabel, Schrauben, Gläser, Farbe, Kunststoffe und noch vieles mehr passend auszuschneiden, zu biegen, zu beschriften zu verschweißen oder einzubauen. Nicht zu vergessen die Zulieferer, die ihrerseits Teile mitbringen und vor Ort montieren.
Dieses streng durchorganisierte Gewerk kann nur von Computern und passenden Programmen überblickt werden, weshalb hier eine entsprechend leistungsfähige EDV zum Einsatz kommt. Beispielsweise werden die per CAD erstellten Zeichnungen in CNC-Befehle für insgesamt fünf Plasmaschneidanlagen übersetzt, die über einen Arbeitsraum von je 12x4 Meter verfügen und ohne menschliches Zutun mit Blechen bestückt werden. Diese erhalten anschließend passende Durchbrüche und werden zudem beschriftet, damit in späteren Arbeitsgängen die Schweißfachleute erkennen, wo diese Bleche jeweils einzubauen sind.
Doch bis es soweit ist, durchlaufen die Bleche noch eine ausgeklügelte, ebenfalls vollautomatische Schweißanlage, wo diese teils zu einem großen Bauteil per Laser verschweißt werden und teils darauf warten, weiterverarbeitet zu werden. Auf diese Weise entstehen sehr rasch große Blechfelder, die durchaus bis zu 30x30 Meter messen können. Auf diese Felder werden anschließend vollautomatisch an den exakt vom Schiffskonstrukteur vorgesehenen Stellen Versteifungsprofile und die zuvor zwischengelagerten Bleche platziert, die nun als Trennwände fungieren. Diese Bauteile werden, ebenfalls vollautomatisch, per Laser-Hybridschweißen untereinander verbunden.
Die Qualität der erzeugten Schweißnähte ist schlicht sensationell. Ein Mensch könnte diese Nähte nie in gleicher Perfektion zustandebringen. Nichtsdestotrotz arbeiten Maschinen natürlich auch nicht fehlerfrei, weshalb Prüfer das Ergebnis noch kontrollieren und im Fall einer Auffälligkeit fehlerhafte Schweißnähte sofort ausbessern, was selbstverständlich extrem selten durchgeführt werden muss.Während in einer anderen Anlage die unterschiedlichsten Rohre für Frisch- und Abwasser sowie Klimaanlage und Hydrauliköl zugeschnitten und gebogen wurden, wird das eben frisch verschweißte Segment von einer imposanten, 40x40 Meter großen Wendeeinrichtung um 180 Grad gedreht. Dadurch bekommen die Monteure die Möglichkeit, die nun angelieferten Rohre, Kabel und das sonstige Installationsmaterial nicht über Kopf, sondern bequem am Boden zu montieren.
Auf diese effiziente Art und Weise werden sehr rasch mehrere Tausend Segmente und Einheiten produziert, die zusammengenommen die Kabinen, Speisesäle, Kinos, Wellnessräume, Theater oder Schiffskasinos ergeben und zusammengebaut nach Art eines überdimensionalen Lego-Baukastens ein Schiff von imposanter Größe ergeben, auf dem bis zu 4188 Passagiere Platz haben.
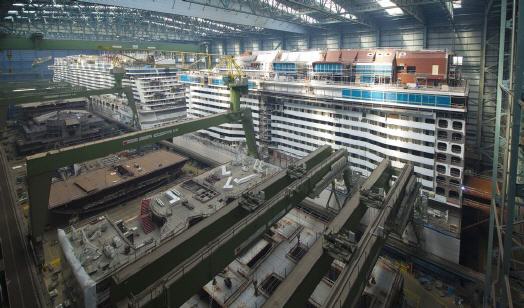
Von der Titanic lernen
Gegen diese Ozeanriesen wirkt selbst die Titanic bescheiden, die damals Platz für immerhin rund 2500 Passagiere bot. Aus deren Untergang wurden wichtige Lehren gezogen. Heutige Schiffe sind ganz anders konstruiert, sodass der Status ›Unsinkbarkeit‹ zumindest für moderne Kreuzfahrtschiffe aus der Meyer Werft nicht nur ein Werbeversprechen ist. Die durchdachte Konstruktion ist es auch, die es erlaubt, ein derart großes Luxusschiff in weniger als einem halben Jahr zu bauen. Aus der Meyer Werft kommen pro Jahr zwei Schiffe von der Größe einer ›Ovation of the Seas‹. Diese ist 347 Meter lang, 41,7 Meter breit und 70 Meter hoch.
Dies ist nur möglich, weil eine logistische Meisterkette jede Art von Leerlauf unterbindet und die Schiffskonstruktion den schnellen Baufortschritt optimal unterstützt. So werden beispielsweise die Passagierkabinen von den Zulieferbetrieben in Modulform komplett mit Bett, Teppich, Schränken, Bad, Toilette et cetera angeliefert, in den jeweiligen Schiffssektor eingeschoben und befestigt. Nachdem noch die Strom- und Wasserleitungen an den Schiffskreislauf angeschlossen sind, ist das Modul betriebsbereit und könnte Passagiere aufnehmen. Dies ist jedoch erst nach Abnahme des Schiffes auf See der Fall. Solange am Schiff noch gebaut wird, bleiben die Module geschlossen, damit kein Schmutz die teuere Einrichtung ruiniert.
Auf der Meyer Werft passieren viele Dinge parallel. Während ein fast fertiges Schiff seiner Auslieferung entgegensieht, wird wenige Meter daneben bereits am Skelett des nächsten Luxusliners gearbeitet. Werden dort Kabinenmodule montiert, wird daneben geschweißt und geflext. Es ist faszinierend zu beobachten, wie feinfühlig die verschiedenen Arbeitsschritte ineinandergreifen, um ein Spitzenprodukt nach dem anderen zu produzieren. Die Konstrukteure müssen viele Dinge berücksichtigen, die ein hochwertiges Schiff ausmachen. Schiffe sind schließlich nicht mit Bauwerken aus Ziegel oder Spannbeton zu vergleichen, die Jahr für Jahr an der gleichen Stelle stehen.
Ein Kreuzfahrtschiff hingegen ist in verschiedenen Klimazonen unterwegs. Der metallene Schiffsrumpf wird in der Mittagssonne am Äquator extrem aufgeheizt und dehnt sich dadurch aus. Am Polarkreis jedoch zieht sich das Metall wegen der dort herrschenden grimmigen Kälte zusammen. Hinzu kommt der Wellengang, der mal sanft, mal heftig ausfallen kann, was zum Verwinden des Schiffskörpers führt. Und in allen diesen Fällen muss die Inneneinrichtung beziehungsweise deren Technik perfekt funktionieren. Keine Scheibe darf aus dem Gummirahmen fallen, kein Aufzug steckenbleiben, keine Türe klemmen und kein Teppich sich lösen. Hier liegt eines der Geheimnisse der Meyer Werft: Die sehr große Zahl leistungsstarker Zulieferer.
Jedes Unternehmen bringt seine Kernkompetenz ein, die zu einem Spitzenprodukt führen. Egal ob Klima- oder Wasseraufbereitungsanlage, Navigationssystem, Antriebsmotor oder Funksystem – nur beste Qualität wird in Schiffe aus der Meyer Werft eingebaut, damit die Passagiere sich rundum wohl und geborgen fühlen. Ein besonderes technisches Highlight sind die mitgeführten Entsalzungsanlagen, die dafür sorgen, dass stets frisches Trinkwasser für jeden Passagier zum Baden, Duschen und Trinken zur Verfügung steht.
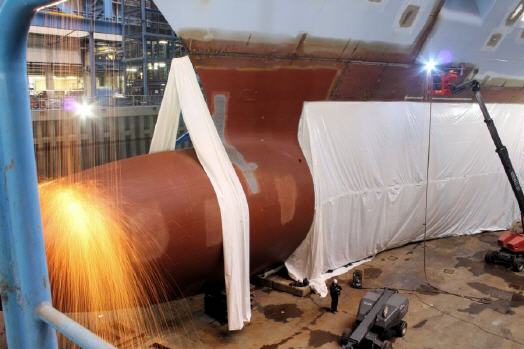
Schiffbau perfektioniert
Die Liebe zum Schiffsbau geht so weit, dass die Antriebskomponenten nicht einfach montiert werden. Vielmehr werden diese Komponenten bei geflutetem Trockendock mit dem Schiffskörper verbunden, da nur so ein optimales Austarieren möglich ist. Lästige Schwingungen beim Lauf von Motoren werden so minimiert, was insbesondere den Passagieren zugutekommt, die ihre Kabine im unteren Bereich des Schiffes haben.
Auch in Sachen Umweltschutz hat die Meyer Werft viel zu bieten. Beispielsweise werden die Abgase der Motoren nicht ungehindert in die Umwelt geblasen, sondern mehrstufig gereinigt, ehe sie den Weg ins Freie antreten dürfen. Sogar durch eine Art Wasserfall werden die Rauchgase geleitet, wodurch grobe Schwebstoffe aus dem Rauch entfernt werden. Durch alle diese Maßnahmen werden Passagiere nicht mehr mit lästigen, übelriechenden Abgasen beim Relaxen auf dem Sonnendeck belästigt.
Wer Schiffe der Meyer Werft genau betrachtet, stellt fest, dass diese keine Öffnungen mehr besitzen, über die herkömmliche Schiffe ihre Problemstoffe entsorgen. Weder werden Abwässer dem Meer zugeleitet, noch Küchenabfälle über diesen früher üblichen Weg entsorgt. Vielmehr wird beispielsweise das Trinkwasser aufbereitet und für die Toilettenspülung genutzt, Reststoffe hingegen werden an einem Hafen entsorgt. Für den Schiffsrumpf wird eine besonders umweltfreundliche Farbe auf Siliconbasis verwendet. Insgesamt werden 300 Tonnen Farbe in vier Schichten auf den Schiffskörper aufgetragen, Unterwasser ist die besonders glatt, deshalb können sich daran keine Meerestiere festhaften. Dadurch genügt es, den Anstrich lediglich alle fünf Jahre aufzufrischen.
Über das ganze Schiff sind mehr als 1 000 Überwachungskameras installiert, die nicht nur der Sicherheit der Passagiere dienen, sondern auch dem Kapitän helfen, das Schiff sicher im Hafen zu rangieren. All diese Technik wird natürlich vorher getestet, ehe zum ersten Mal Passagiere das Schiff genießen dürfen. Dies übernimmt das Unternehmen DNV GL, eine Art TÜV für Schiffe.
An fünf Tagen wird auf hoher See das Schiff auf Herz und Nieren untersucht, werden das GPS sowie die Kompasse geeicht und müssen alle Maschinen beziehungsweise Anlagen im Dauerlauf zeigen, dass sie auch in Extremfällen durchhalten. Danach steht dem Schiff die weite Wasserwelt offen, die es dank der hochwertigen Verarbeitung über viele Jahrzehnte bereisen wird.
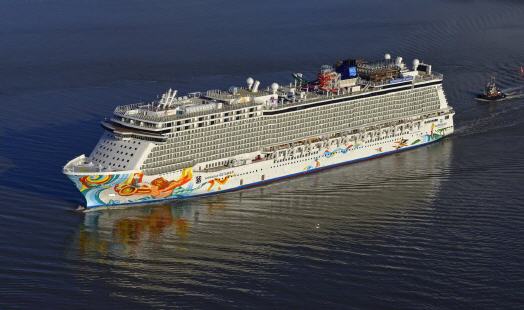
Download:
Diesen Artikel können Sie hier im PDF-Format [559 KB] herunterladen.
Mehr Informationen:
![]() |
MEYER WERFT GmbH & Co. KG |
![]() |
Industriegebiet Süd |
![]() |
26871 Papenburg |
![]() |
Tel: 0 49 61 / 81-0 |
![]() |
Fax: 0 49 61 / 81-43 00 |
![]() |
E-Mail: info@meyerwerft.de |
![]() |
www.meyerwerft.de |
War dieser Artikel für Sie hilfreich?
![]() |
![]() |
![]() |
![]() |
![]() |
Bitte bewerten Sie diese Seite durch Klick auf die Symbole.
Zugriffe heute: 21 - gesamt: 6322.