Gewindeformen vorangetrieben
Zeiteinsparungen bis zu 75 Prozent
Das Gewindeformen ist ein schon länger etabliertes Verfahren, um besonders feste Gewinde in unterschiedliche Materialien einzubringen. Diese Idee hat Emuge weiterentwickelt. Unter dem Namen ›Punch Tap‹ wird eine staunenswerte Innovation vermarktet, die Fachleute aufhorchen lässt.
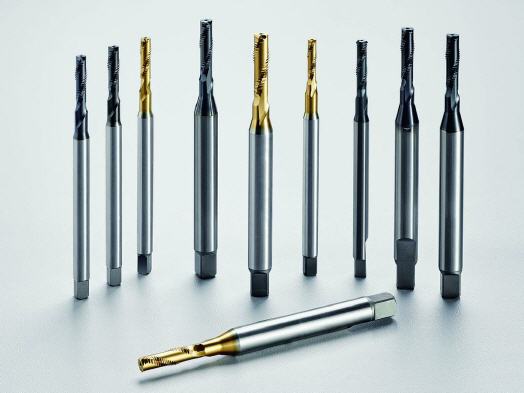
Es zeigt sich immer wieder, dass selbst jahrelang etablierte Verfahren noch lange nicht das Optimum sind. Es ist immerzu möglich, neue Meilensteine zu setzen. Das Hinterfragen einer Technik, die Unzufriedenheit mit einem Verfahren oder dessen Unwirtschaftlichkeit sind oft Auslöser, um neue Wege zu besseren Alternativen zu entdecken.
So eine Alternative hat Emuge unter dem Markennamen ›Punch Tap‹ auf den Markt gebracht. Diese Innovation ist gerade dabei, insbesondere in der Serienfertigung altbewährte Methoden der Gewindeherstellung abzulösen. Nicht zuletzt die wesentlich kürzere Bearbeitungszeit bis zur Fertigstellung eines Gewindes ist ein gewichtiges Argument, das für Punch Tap spricht. Darüber hinaus werden die Gewinde nicht geschnitten, sondern geformt.
Geschnittene Gewinde haben den Nachteil, dass die dazu nötigen Gewindebohrer das Material zerspanen, um die charakteristische Wendelform des Gewindegangs aus dem Material herauszuarbeiten. Auf diese Weise werden die Fasern unterbrochen. Die Folge ist, dass die axiale Belastungsfähigkeit des Gewindes leidet. Aus diesem Grund werden hochbelastete Gewinde spanlos mittels Gewindeformer hergestellt. Dadurch, dass diese Werkzeuge das Material nicht zerspanen sondern verformen, werden die Fasern nicht unterbrochen, sondern verdichtet, was die Festigkeit des so hergestellten Gewindes erhöht.
Für viele Werkstoffe geeignet
Mittels des Gewindeformens können Gewinde in die meisten Metalle eingebracht werden. Der große Vorteil des Verfahrens ist, dass keine Späne entstehen, die sich nachteilig auf den Fertigungsprozess auswirken können. Zudem besitzen die Gewindeformer eine höhere Standzeit als Gewindebohrer und erzeugen an den Gewindeflanken eine qualitativ bessere Oberfläche.
Mit Punch Tap ist es nun möglich, den Prozess der Innengewindefertigung auf eine neue Wirtschaftlichkeitsstufe zu stellen: Beispielsweise konnten in der Serienfertigung von Motorblöcken mit den Punch Tap -Werkzeugen bereits Zeiteinsparungen von 0,7 Sekunden pro Gewinde realisiert werden. Dies ist den wesentlich kürzeren Werkzeugwegen durch den extrem kurzen Bewegungsablauf zu verdanken.
Anders als klassische Gewindebohrer und –former, die Windung für Windung des Gewindes zeitaufwendig herausarbeiten, sorgt die besondere Form des Punch Tap-Werkzeugs dafür, dass das Gewinde damit in einem Bruchteil der Zeit hergestellt wird. Der Ablauf vollzieht sich wie folgt: Das Werkzeug fährt in die Vorbohrung auf einer helikalen Bahn bis zur Nenntiefe des Gewindes, dort angekommen dreht es sich um 180 Grad nach links sowie um die Gewindesteigung nach oben, um sich danach auf der gleichen helikalen Bahn linksdrehend wieder aus der Gewindebohrung zurückzuziehen.
Da das Punch Tap-Gewindewerkzeug auch Helikal-Gewindeformer genannt, mit innovativer Geometrie versehen ist, erfolgt in der Linksdrehung um über 180 Grad eine plastische Verformung des Materials. Dadurch wird der Werkstoff des Werkstücks kaltverfestigt, was einen ununterbrochenen Faserverlauf erzeugt. Dies führt dazu, dass das so erzeugte Gewinde über ähnliche Festigkeitswerte verfügt, wie diese entstehen, wenn klassische Gewindeformer zum Einsatz kommen. Optisch fällt auf, dass das Gewinde einen unausgeformten Kern besitzt und zudem Helikalnuten sichtbar sind.
Diese entstehen durch das auf der helikalen Bahn erfolgte Eintauchen des PunchTap-Gewindewerkzeugs in die Kernlochbohrung. Wichtig ist zudem, dass die Bohrungen sauber mit einem 90 Grad-Kegelsenker angesenkt werden, ehe das PunchTap-Werkzeug zum Einsatz kommt. Es wird empfohlen, sich bezüglich der Senkungsgröße an der DIN-Norm 76-1:2004-06 zu orientieren. Beispielsweise wird dort vorgeschlagen, für ein Gewinde M6 einen Senkdurchmesser von 6,3 Millimeter Durchmesser einzubringen.
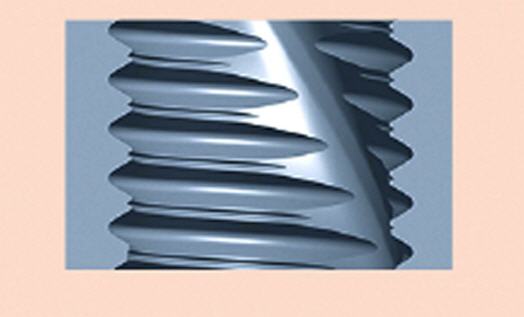
Wichtige Voraussetzungen
Um Punch Tap zu nutzen, wird zwingend eine Maschine benötigt, die hard- und softwareseitig für dieses Verfahren geeignet ist. Dazu gehört eine stabile Hauptspindel, die in der Lage ist, große, in axialer Richtung wirkende Zug- und Druckkräfte aufzunehmen. Diese Frage muss unbedingt mit dem Hersteller der Maschine vorab abgeklärt werden.
Selbstverständlich muss auch die Aufnahme dafür ausgelegt sein, die beim Helikal-Gewindeformen auftretenden hohen axialen Kräfte und Drehmomente wegzustecken. Hier besteht ansonsten die Gefahr, dass das Punch Tap-Werkzeug aus der Aufnahme herausgezogen wird. Schrumpffutter beispielsweise sind zum Spannen der Punch Tap -Werkzeuge nicht geeignet. Optimal auf Punch Tap abgestimmt ist hingegen die Punch Tap -Aufnahme PT-Synchro von Emuge. Diese baut auf der ER-Spannzange auf, die eine hervorragende Rundlaufgenauigkeit besitzt und ein hohes Anzugsmoment erlaubt. Zusätzlich verfügt diese Aufnahme über eine Auszugs- und Verdrehsicherung für das Punch Tap-Werkzeug.
Nicht minder wichtig ist eine stabile Werkstückspannung des zu bearbeitenden Werkstücks. Eine stabile Spannung wird benötigt, um die hohen Zug- und Druckkräfte des Werkzeuges aufzunehmen. Auch das Werkstück selbst muss über eine Mindeststeifigkeit an derjenigen Stelle verfügen, an der mittels Punch Tap ein Gewinde eingebracht werden soll. Sehr dünnwandige Bauteile, welche zur Durchbiegung neigen, sind daher nicht für Punch Tap geeignet.
Weiterhin ist zu prüfen, ob die Steuerung der Maschine über einen Zyklus für Punch Tap verfügt, damit dieses Verfahren genutzt werden kann. Falls dies nicht der Fall ist, muss geklärt werden, ob sich die Steuerung mit diesem Zyklus nachrüsten lässt. Aktuelle Steuerungen von Siemens und Heidenhain sowie viele weitere Maschinen-und Steuerungshersteller können diesen Support bieten und nachrüsten. Wie bereits erwähnt, gibt es von der Maschinenstabilität bis zur Werkstückspannung diverse Hürden zu überwinden, damit Punch Tap zuverlässig genutzt werden kann.
Zu diesen Herausforderungen haben sich die PunchTap-Entwickler von Emuge einige Lösungen einfallen lassen, die sich auf der Softwareseite zeigen: es gibt drei Prozessvariationen, um im Fall unumgänglicher Parameter, wie etwa kritischer Werkstückaufspannung oder der Bearbeitung unterschiedlichster Nichteisenwerkstoffe doch noch zum gewünschten Erfolg zu kommen.
Die unter den Namen ›PT1.0 performance‹, ›PT1.5 medium‹ und ›PT2.0 soft‹ zur Verfügung stehenden Zyklusvarianten unterscheiden sich durch die Art der Bewegungsabfolge, um das Gewinde zu formen. Der schnellste Zyklus ist die Variante ›PT1.0‹. Diese eignet sich für sehr stabil gespannte Werkstücke. Hohe Bauteilstabilität vorausgesetzt, ist es damit möglich – im Vergleich zum Gewindeformen – bis zu 75 Prozent an Bearbeitungszeit einzusparen.
Dieser Prozess arbeitet in nur drei Schritten: Eintauchen in die Bohrung in helikaler Bahn, Drehen des Punch Tap-Werkzeugs um 180 Grad sowie Verfahren um die Steigung nach oben, Rückzug aus der Bohrung in der helikalen Bahn wie beim Eintauchen.
Die Zugkraft im Blick
Die Variante ›PT1.5‹ ist für Teile geeignet, die über eine nicht so hohe Bauteilstabilität verfügen. In diesem Zyklus wurde der Prozessschritt ›Druckentgraten‹ mit aufgenommen. Dies bedeutet, dass nach der Formung des Gewindes – durch die schon erwähnte Drehung um 180 Grad nach links bei gleichzeitigem axialen Verfahren um die Steigung nach oben – das Werkzeug nicht sofort aus der Bohrung zurückgezogen wird, sondern zunächst in axialer Richtung geringfügig in die Bohrung eingetaucht wird. Dies führt dazu, dass der in der Helikalnut gebildete Grat abgeschert wird, wodurch beim nachfolgenden Herausziehen des Werkzeugs weniger Zugkraft auf die Spindel wirkt.
Zwar kostet der zusätzliche Schritt ein wenig Zeit, doch ist dieser Zyklus mit bis zu 72 Prozent Zykluszeitverkürzung immer noch weit schneller als ein reiner Gewindeformprozess. Bei der Variante ›PT2.0‹ wird zusätzlich zum Prozessschritt ›Druckentgraten‹ noch der Prozessschritt ›Gewindenachformen‹ eingeschoben. In diesem Fall wird das PunchTap-Werkzeug um 180 Grad nach rechts sowie um die Steigung in die Bohrung hineinbewegt, wodurch das Gewinde nachgeformt und eventuell noch vorhandener Grat endgültig entfernt wird.
In der Folge werden Zugkräfte um bis zu 90 Prozent reduziert, weshalb sich diese Variante auch für weniger stabile Bauteile eignet.Zwar fallen die per Punch Tap hergestellten Gewinde optisch durch ihre Helikalnut im Gewinde auf, doch zeigen Untersuchungsergebnisse der TU-Dortmund, dass die Festigkeitswerte dieser Gewinde ähnlich derjenigen sind, die durch traditionelles Gewindeformen hergestellt wurden. Es gibt daher viele Gründe, sich das Verfahren einmal näher anzusehen, um es für die eigene Fertigung zu nutzen.
Mehr Informationen zu Emuge:
![]() |
EMUGE-FRANKEN Werk Richard Glimpel GmbH & Co. KG |
![]() |
Fabrik für Präzisionswerkzeuge |
![]() |
Nürnberger Straße 96-100 |
![]() |
91207 Lauf |
![]() |
Tel.: (09123) 186-0 |
![]() |
Fax: (09123) 1 43 13 |
![]() |
E-Mail: info@emuge-franken.com |
![]() |
www.emuge-franken.com |
War dieser Artikel für Sie hilfreich?
![]() |
![]() |
![]() |
![]() |
![]() |
Bitte bewerten Sie diese Seite durch Klick auf die Symbole.
Zugriffe heute: 19 - gesamt: 9182.