Die energiesparende Schneide
Doktorarbeit mit großem Potenzial
Ob Drehen, Fräsen oder Bohren – seit über 100 Jahren wird rund um den Schneidkeil geforscht. Immer bessere Zerspanungswerkzeuge sind seither entstanden, die dank neu entwickelter Schneidstoffe sowie raffinierter Geometrien und leistungsstarker Beschichtungen immer höhere Standzeiten aufweisen, daher immer anspruchsvollere Materialien zerspanen können. Es schien, als wäre in diesem Bereich mittlerweile alles erforscht. Dass dem nicht so ist, hat 2016 Dr.-Ing. Hans-Henrik Westermann von der Projektgruppe ›Regenerative Produktion‹ des Fraunhofer IPA in Bayreuth mit seiner Dissertation bewiesen.
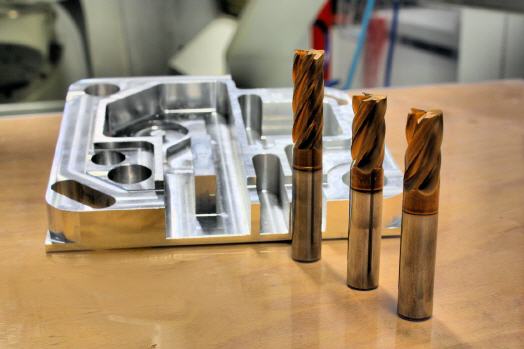
Technische Meilensteine und Erfindungen basieren nicht selten auf der aufmerksamen Beobachtung der Umgebung beziehungsweise der Natur. Wer neugierig ist und Dinge hinterfragt, hat gute Chancen, einen Volltreffer zu landen, der die Menschheit nach vorne bringt. Weniger die Menschheit als vielmehr die zerspanende Zunft wird von der Neugierde des Dr.-Ing. Hans-Henrik Westermann profitieren, der sich vor einigen Jahren zur Brotzeit die Frage stellte, warum sein zwar scharfes, doch lediglich mit einer geraden Klinge ausgestattetes Messer so schlecht in Brot eindringen kann.
Herausgekommen ist ein sensationelles Schneidenkonzept für Fräswerkzeuge, das heute vom Unternehmen WNT unter dem Namen ›S-Cut‹ vertrieben wird. Ehe es jedoch so weit war, mussten gewaltige Klippen überwunden werden, wozu auch die abweisende Reaktion der etablierten Fräswerkzeughersteller gehörte. Auf der Suche nach Kooperations- und Forschungspartnern bekam Dr. Westermann von den Platzhirschen zu hören, dass so ein Konzept technisch gar nicht umsetzbar sei, dass man seine eigene Forschung habe und dass der Markt so was sowieso gar nicht will.
Skepsis war groß
Erstaunliche Aussagen, die man in einer eigentlich innovationsfreudigen Branche nicht vermutet hätte. Immerhin wird für die Zerspanung etwa 20 Prozent der für den Betrieb einer Werkzeugmaschine benötigten Energie aufgewendet. Wenn es gelänge, diesen Wert zu senken, würde sich dies selbstverständlich auch auf der Kostenseite positiv bemerkbar machen. Sogar Gutachter waren von der Idee, den Energieverbrauch von Fräsern beim Zerspanen zu senken, nicht überzeugt, weshalb der Griff zu Forschungsgeldern zunächst versperrt war.
Überall scheint sich Skepsis breit gemacht zu haben, ob in einem seit über 100 Jahren intensiv beforschten Bereich noch nennenswerte Entdeckungen zu erwarten sind, die den Einsatz beträchtlicher Mittel rechtfertigen würden.Doch ließ sich der hoffnungsfrohe Forscher davon nicht abhalten, suchte weiter und fand schließlich ein Unternehmen aus Niederbayern, das die Chancen dieser Zusammenarbeit erkannte. Es handelt sich um die Maier GmbH, die in Oberschneiding, einem Ort unweit von Deggendorf und Straubing, hochwertige Fräswerkzeuge produziert, die unter dem Namen ›Head-Master‹ vertrieben werden.
Das Unternehmen wurde Technologiepartner und wichtige Stütze auf der Suche nach der besseren Schneidengeometrie für Fräswerkzeuge. Damit die Ergebnisse der unterschiedlichen Fräserschneiden gleich in der Praxis getestet werden konnten, wurden zudem fünf Anwender sowie mit der Firma RSB Schleifdienst GmbH aus dem oberfränkischen Dörfles-Esbach, ein Nachschleifbetrieb mit ins Projekt geholt.
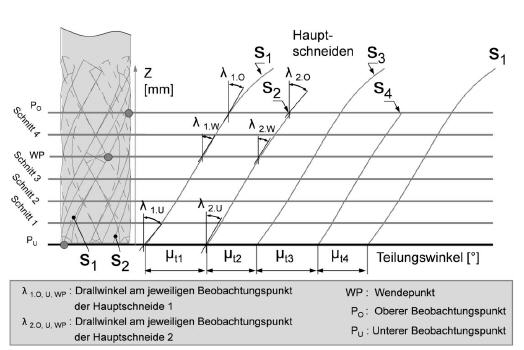
Mit Elan ans Werk
Mit den Partnern im Rücken startete Dr. Westermann sein Projekt, indem er zunächst zahlreiche Fräser von verschiedenen Anbietern orderte, um mittels einer identischen Fräsaufgabe deren Energieaufnahme festzustellen. Überraschenderweise wurde bei diesen Versuchen eine Abweichung im Energieverbrauch von bis zu 18 Prozent festgestellt. Auch die Standzeiten waren sehr unterschiedlich. Es musste also Hersteller geben, die einer optimalen Fräserschneide bereits näher gekommen waren, als andere. Dies war der Beweis, dass es sich lohnt, genauer auf die Fräserschneide zu schauen, um mit einem wissenschaftlich-systematisch optimierten Design noch mehr aus dieser herauszuholen. Von diesen Ergebnissen überzeugt, gaben die zunächst skeptischen Gutachter ihre Zustimmung für Forschungsgelder, wodurch der Weg zur Entwicklung einer innovativen, energieverbrauchsoptimierten Fräserschneidengeometrie nun endgültig frei war. Ausgestattet mit einer zweijährigen Projektförderung der Bayerischen Forschungsstiftung aus München, begannen die Arbeiten im Juli 2013.
Zunächst galt es ein Testteil zu entwickeln, damit die Auswirkungen von Profilabwandlungen der neuen Schneidengeometrie exakt nachvollzogen werden konnten. Es musste also ein Werkstück ähnlich dem NAS-Teil für Fünfachsmaschinen entworfen werden, um die Fräsergebnisse auf einer nachprüf- und wiederholbaren Grundlage aufzubauen. Besagtes NAS-Teil ist für diesen Zweck unbrauchbar, da es unter anderem konvexe und konkave Kugelabschnitte enthält, um das Regelverhalten der Antriebe von CNC-Maschinen zu testen. Also musste etwas völlig Neues ersonnen werden. Das Resultat der Überlegungen von Dr. Westermann ist ein Referenzwerkstück aus dem Vergütungsstahl Ck 60, das für 2D-Fräsarbeiten mit einem Schaftfräser von 16 Millimeter Durchmesser optimiert ist. Dieses Referenzwerkstück kann sicher bald zum Standard der Industrie gehören wenn es gilt, die Leistung von Fräsern zu testen.
Mittels der CAD-Software ›Pro/Engineer‹ ging es dann daran, ein möglichst weitgefasstes und variables CAD-Profil der Fräserform zu erstellen, um durch das Ändern von Parametern rasch zu abgewandelten Schneidengeometrien zu kommen. Unterstützt wurde die Profilerstellung durch die Unternehmenspartner mittels der Schleifsoftware ›Numroto‹ von NUM, die eine exakte Modellierung der vom CAD-System gelieferten Profilform vornehmen kann und so den Facharbeiter in die Lage versetzt, festzustellen, ob das Profil überhaupt herstellbar ist und wo es eventuell zu Kollisionen beim Schleifprozess kommt.
Insgesamt wurden 150 Labormuster von Fräsern mit verschiedenen Profilformen und Schneidengeometrieparametern angefertigt und ihr Verhalten mithilfe einer CNC-Maschine an zahlreichen Referenzwerkstücken geprüft. Da jeder Fräser mit dem gleichen CNC-Programm zum Einsatz kam, konnten die Stärken und Schwächen der jeweiligen Parameterkombination exakt festgehalten werden. Es wurde die Oberflächengüte des gefrästen Teils bewertet , die Standzeit des Fräsers ermittelt und der Energieverbrauch zur Herstellung des Testwerkstücks gemessen.
Bei diesen experimentellen Untersuchungen stellte sich heraus, dass der Drall- sowie der Teilungswinkel entscheidende Komponenten waren, die Leistung eines Fräswerkzeugs zu steigern. Es ist zwar schon länger bekannt, dass diese Winkel durchgreifenden Einfluss auf die Leistungsfähigkeit des Werkzeugs, die Standzeit und die Oberflächengüte haben, doch wurde von Dr. Westermann der Ansatz vertieft verfolgt. Beispielsweise ging er auch der Frage nach, wie sich der Schneidkantenradius auf die Schnittleistung (Pc) auswirkt. Dabei stellte sich heraus, dass Schneidkanten dann zu höheren Schnittleistungen führen, wenn sie mit einem zu großen Radius versehen wurden.
Interessant ist die Tatsache, dass – ausgehend von einer unverrundeten Schneidkante – die Schnittleistung zunächst sinkt, je größer der Schneidkantenradius wird. Ab einer bestimmten Größe des Schneidkantenradius kehrt sich der Trend um und die Schnittleistung nimmt wieder zu. Es konnte dabei festgestellt werden, dass Schneidkanten mit einem Schneidkantenradius zwischen 10 und 30 Mikrometer den positivsten Effekt auf die Schnittleistung haben, was einen reduzierten Energiebedarf sowie eine höhere Standzeit bedeutet. Zudem wurde festgestellt, dass größere (positive) Spanwinkel von größeren Schneidkantenradien profitieren.
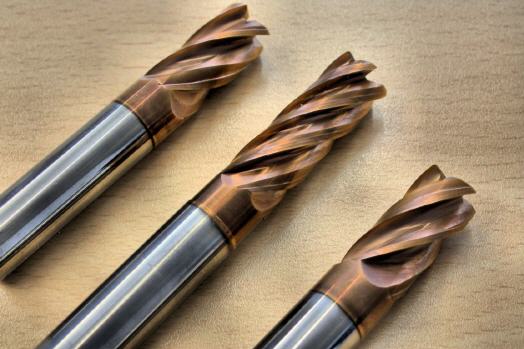
Doch Dr. Westermann war mit diesen Erkenntnissen noch nicht zufrieden. Er setzte nun sein Augenmerk auf den Freiwinkel, wobei er feststellte, dass es eine Wechselwirkung zwischen Schneidkantenradius und Freiwinkel gibt. Er stellte zudem fest, dass der Schneidkantenradius in seiner optimalen Größe zusammen mit dem optimalen Frei- beziehungsweise Spanwinkel zur kleinsten Rautiefe führt. Seine Erkenntnisse mündeten in eine neue Fräsergeneration, die – nicht wie bisher vorwiegend anzutreffend – über einen Spanwinkel von bis zu acht Grad verfügen, sondern Spanwinkel von mindestens acht Grad und mehr aufweisen. Derartige Fräswerkzeuge führen in Verbindung mit einem passenden Schneidenradius zu geringeren Schnittleistungen, benötigen also weniger Energie zum Zerspanen, zeigen ein verbessertes Verschleißverhalten und erzeugen höhere Oberflächengüten.
Der entscheidende Schritt hin zum innovativen, energiesparenden Fräser war die Erkenntnis, sich vom konstanten Span- sowie vom konstanten Drallwinkel zu verabschieden. Es wurde eine zum Patent angemeldete mathematische Funktion entwickelt, die es erlaubt, Fräserschneiden zu schleifen, in denen beide Winkel pendelnd an der Schneide entlanglaufen. Diese Funktion bewirkt, dass sich der Spanwinkel des Fräsers auf der ganzen Schneidenlänge zwischen 8 und 18 Grad bewegt. Ausgehend von einem Anfangswert verringert sich der Drallwinkel bis zu einem Wendepunkt, um von dort wieder kontinuierlich zuzunehmen.
Zusammen mit einer ungleichen Schneidenteilung ergeben sich dadurch Zerspanungseigenschaften, die ihresgleichen suchen. Der Grund liegt darin, dass durch die über die ganze Schneidenlänge differentielle Änderung des Drallwinkels und den während des Fräsens gleichbleibenden Zahnvorschubs sich eine Spanungsdicke ergibt, die nicht konstant ist. Dadurch ist der Schnittkraftverlauf nicht sägezahnförmig, wie es bei herkömmlichen Fräsern der Fall ist, sondern im weitesten Sinn eher einer Sinuskurve ähnlich. Kraftspitzen, die wiederum zu Zug- und Druckspannungen an der Schneidkante führen, werden dadurch stark minimiert, was der Standzeit sowie der Oberflächengüte durch eine größere Laufruhe zugutekommt.
Durch dieses „weichere“ Fräsen erklärt sich zudem der wesentlich geringere Energiebedarf für die Zerspanungsarbeit. Die Einsparungen bewegen sich durchaus im zweistelligen Prozentbereich. Darüber hinaus können derart optimierte Fräser mit höherer Schnittgeschwindigkeit eingesetzt werden und Vorschubgeschwindigkeiten lassen sich um bis zu 25 Prozent erhöhen. In der Folge reduziert sich die Arbeitszeit ebenfalls zweistellig.
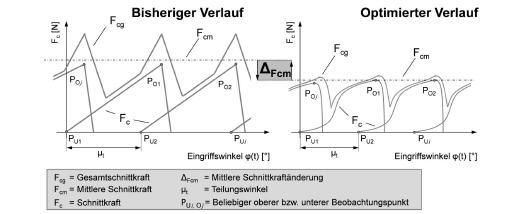
Im Rahmen seines Projektes, das im Jahr 2016 mit dem Hans Jürgen Warnecke-Innovationspreis des Fraunhofer IPA ausgezeichnet wurde, hat Dr. Westermann anhand von zehn Musterbeispielen durchgerechnet, wie hoch die Kosteneinsparungen wären, wenn es sich um Serienteile handeln würde, die ein ganzes Jahr produziert werden. Herausgekommen ist, dass mit dem Einsatz des innovativen Vollhartmetall-Schaftfräsers Einsparungen von mehreren tausend Euro jährlich möglich sind.
Dies zeigt deutlich, dass es sich rechnet, dem Thema ›Energieeinsparung‹ auch bei der Zerspanung viel Aufmerksamkeit zu schenken.
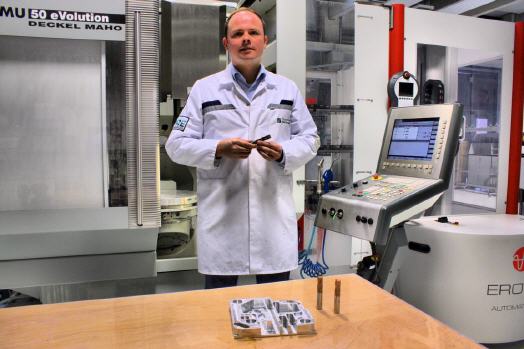
Dr.-Ing. Hans-Henrik Westermann
Mehr Informationen zum Fraunhofer IPA:
![]() |
Fraunhofer-Institut für Produktionstechnik und Automatisierung IPA |
![]() |
Nobelstrasse 12 |
![]() |
70569 Stuttgart |
![]() |
Telefon: +49 711 970-00 |
![]() |
Telefax (Zentrale) +49 711 970-1399 |
![]() |
www.ipa.fraunhofer.de |
War dieser Artikel für Sie hilfreich?
![]() |
![]() |
![]() |
![]() |
![]() |
Bitte bewerten Sie diese Seite durch Klick auf die Symbole.
Zugriffe heute: 17 - gesamt: 12621.