Geboren aus sehr feinem Staub
Via Laserschmelzen zum Produkt
Die zerspanende Fertigung war lange Zeit vorherrschend wenn es darum ging, mechanische Bauteile hoher Qualität und Maßgenauigkeit zu produzieren. Immer bessere generative Verfahren schicken sich an, die Dominanz von Fräsmaschine & Co. aufzubrechen. Mit dem selbstentwickelten Laserschmelzverfahren ist das Unternehmen ›Concept Laser‹ ganz vorne zu finden, wenn es darum geht, Teile aus Metallpulver herzustellen.
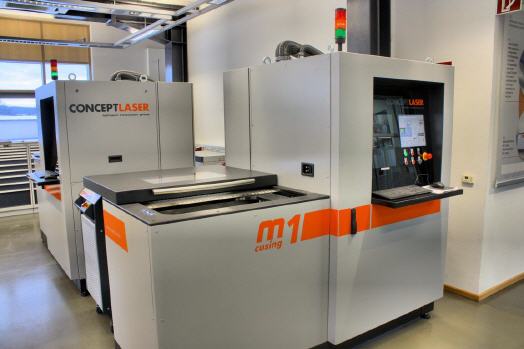
Ob Schneemann, Sandburg oder tropfende Kerze, nahezu jeder hat sich schon mit generativen Fertigungsverfahren beschäftigt. Obwohl die Idee scheinbar auf der Hand liegt, auch Teile für die Industrie auf diese Weise herzustellen, gibt es jede Menge technische Probleme bei der Umsetzung. Die Grundlage ist noch relativ einfach: Es gilt, ein Material, das flüssig, pulverförmig oder fest sein kann, an bestimmten Stellen wie ein Mauerwerk aufzubauen.
Die technische Umsetzung dieser Aufgabenstellung hat zu zahlreichen Verfahren geführt, die landläufig unter dem Begriff ›3D-Drucken‹ zusammengefasst sind. Technisch unterscheiden sie sich jedoch teils gewaltig. Ebenso wie sich die damit produzierten Werkstücke in ihrer technischen Gebrauchsgüte unterscheiden.
Da gibt es zum Beispiel Geräte, die rein mit normalem Papier arbeiten, das Blatt für Blatt zugeschnitten und zusammengeklebt wird. Andere Verfahren verwenden Gips, der an bestimmten Stellen mit einer wasserähnlichen Flüssigkeit besprengt wird und wieder andere Verfahren nutzen einen Laser, der flüssigen Kunststoff durch seine Hitze an bestimmten Stellen aushärtet und so Schicht für Schicht das gewünschte Teil erzeugt.
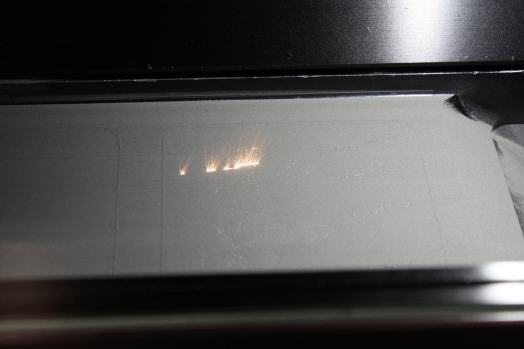
Funktionsteile einmal anders
Alle diese Verfahren eignen sich bestens, wenn es darum geht, schnell zu Anschauungsmodellen und Designmuster zu kommen. Geschicktes Konstruieren erlaubt es sogar, diese Modelle mit Funktionen zu versehen, sodass sich beispielsweise Getriebezahnräder drehen und Klappen bewegen. Sobald es jedoch um Funktionsteile geht, die in realer Umgebung getestet werden sollen, kommen diese Verfahren an ihre Grenzen.
Prototypen- und Kleinserienteile für den echten Einsatz, etwa in Getrieben oder Triebwerken, können nur per Laserschmelzen hergestellt werden. Bei diesem Verfahren wird Metallpulver durch einen Laserstrahl erhitzt und zum Schmelzen gebracht. Das geschmolzene Material verbindet sich auf diese Weise mit dem darunterliegenden Material. Nachdem eine Schicht bearbeitet wurde, wird eine neue Metallpulverschicht aufgetragen und der Prozess beginnt von Neuem. Diese Technik ist mittlerweile derart ausgereift, dass es zwischen generativ und herkömmlich hergestellten Teilen aus Metall nahezu keinen Unterschied mehr gibt. Ob Zugfestigkeit, Härte oder Dehnbarkeit, alle Parameter sind nahezu identisch. Nahezu deshalb, da lasergeschmolzene Bauteile herstellungsbedingt noch eine ganz geringe Porosität aufweisen, die jedoch für die Gebrauchstüchtigkeit der so hergestellten Teile keinerlei Nachteil nach sich zieht.
Im Gegenteil, Laserschmelzen gestattet die Konstruktion von Bauteilen, die wesentlich leichter sind, als durch Drehen und Fräsen hergestellte Teile. Es sind sogar Konturen möglich, die mit zerspanenden Verfahren überhaupt nicht umsetzbar sind. Doch so leicht es sich liest, es war ein langer Weg, bis via Metallpulver gebrauchstüchtige Prototypenteile hergestellt werden konnten. Das Problem war nämlich, dass lange Zeit nur Teile herzustellen waren, die viel zu grobkörnig ausfielen und daher nur über eine geringe Festigkeit verfügten. Kein Wunder, dass sie deshalb bei Belastung wie ein Keks zerbrachen.
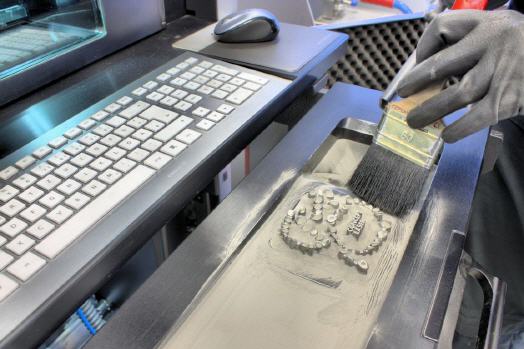
Gewusst wie!
Der Grund für die Porosität: Das Pulver wurde nicht durchgeschmolzen, sondern die einzelnen Körnchen nur in einen teigigen Zustand gebracht, wodurch diese sich zwar verbanden, die Festigkeit jedoch sehr zu wünschen übrig ließ. Der Prozess ist ähnlich dem Sintern, wie er heute noch für die Herstellung von Wendeschneidplatten angewendet wird. Der Grund, warum Wendeschneidplatten nicht zerbrechlich sind, liegt am zugesetzten Bindemittel. Bei der Wendeschneidplattenherstellung ist nämlich Kobalt in der Pulvermischung vorhanden, das beim Sintern komplett schmilzt und die Karbide von Titan, Tantal und Wolfram, die lediglich teigig werden, umschließt, weshalb die Festigkeit dieses Produkts hier gegeben ist.
Im Jahre 2 000 knallten jedoch im Bayerischen Lichtenfels die Korken. War es dem Unternehmen Concept Laser doch endlich gelungen, eine Laserschmelzanlage zu entwickeln, die Teile von hoher Qualität produzierte. Dies war eine Weltpremiere, die seither nicht nur den Werkzeugbau revolutionierte. ›Lasercusing‹ nennen die Lichtenfelser ihre Innovation in Sachen Laserschmelzen von Metall. ›Cusing‹ ist ein Kunstwort und setzt sich aus dem ersten Buchstaben von ›Concept Laser‹ und den letzten fünf Buchstaben von ›Fusing‹ zusammen.
Die Entwickler unter der Leitung von Geschäftsführer Frank Herzog haben ihren Facharbeitern genau über die Schulter geschaut und deren Fachwissen in die neue Technik verpflanzt, um zum Erfolg zu kommen. Schweißspezialisten beispielsweise schweißen bei kritischen Teilen in der Regel keine ununterbrochene Naht, da der Wärmeeintrag das Teil verziehen würde. Sie schweißen hier ein kleines Stück und dort ein kleines Stück. Durch die Abwechslung kann das Teil immer wieder abkühlen, was den Verzug des Werkstücks verhindert. Exakt diese Vorgehensweise wurde in die Lasercusing-Anlagen verpflanzt. Wer den Maschinen beim Arbeiten zusieht, stellt fest, dass der Laser in raschem Wechsel an verschiedenen Stellen sein Werk verrichtet. Dadurch kann die Wärme immer wieder entweichen, was Wärmeverzug und Gefügeveränderung verhindert.
Doch ist dies noch lange nicht alles, was eine Anlage besitzen muss, um zum Laserschmelzen zu taugen. Schweißer wissen, dass manche Metalle nur mit Schutzgas zu schweißen sind. Der Grund ist, dass der Luftsauerstoff sich beim Schweißen mit dem Metall verbinden würde und die Naht dadurch porös, schwach und somit fehlerhaft wäre. Auch beim Laserschmelzen ist Sauerstoff unerwünscht. Die Anlagen haben daher eine luftdichte Arbeitskabine, die mit Schutzgas gefüllt werden kann. Je nach Material kann dies Argon (bei Titan) oder Stickstoff (bei allen anderen Metallen) sein.Doch damit nicht genug. Beim Laser entsteht sogenannte ›Schmauche‹, die giftig und explosiv ist. Diese wird mittels eines besonderen Absauggeräts abgesaugt und in ein Wasserbad geleitet, wo der Rauch gebunden und unschädlich gemacht wird.
Insbesondere bei der Verarbeitung von Titan besteht Explosionsgefahr. Die Lasercusing-Anlagen werden daher auf der Grundlage der Atex-Richtlinien geprüft. Anlagen von Concept Laser sind grundsätzlich auf höchste Sicherheit und Komfort ausgelegt. Aus diesem Grund müssen die Teile auch nicht im Maschineninneren mühsam und gesundheitsbelastend entnommen werden. Vielmehr wurde allen Maschinen eine Einrichtung spendiert, die das Herausfahren der Produktionseinheit erlaubt, wodurch ein bequemes Entnehmen und Entstauben des Teils möglich wird.
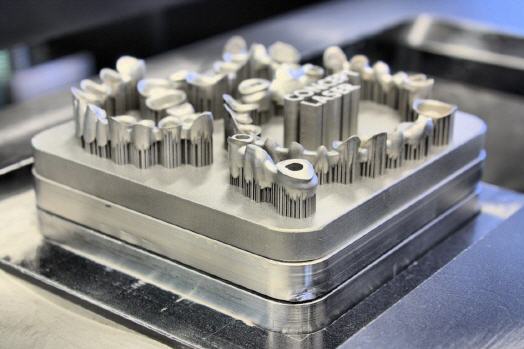
Ressourcenschonend
Der nicht verwendete Metallstaub, der eine Stärke von 40 bis 65 Mikrometer aufweist, kann gesammelt und erneut verwendet werden. Natürlich ist trotz des „springenden“ Lasers das Teil nie ganz spannungsfrei, weshalb das Teil nach dem Laserschmelzen noch den Arbeitsgang ›Spannungsfreiglühen‹ über sich ergehen lassen muss.
Laserschmelzen ist ein tolle Sache. Damit sind Konturen möglich, die früher undenkbar waren. Im Werkzeugbau beispielsweise können nun die Kühlkanäle, ähnlich der Adern beim Menschen, unmittelbar an die Wand der Werkstückform eingebracht werden. Dadurch ist eine um 30 Prozent effektivere Kühlung möglich, was es erlaubt, die Taktzeiten beim Spritzgießen zu erhöhen. Diese Taktzeiterhöhung kann dazu genutzt werden, kleinere Spritzgussformen mit weniger Teilen pro Schuss zu bauen, ohne dass die Teilestückzahl pro Stunde sinkt. In der Folge genügt eine kleinere und billigere Spritzgießmaschine für die Produktion.
Durch konturnahes Kühlen können die Stückkosten daher stark sinken.Doch mit dem Laserschmelzen geht noch viel mehr. Einbaufertige Prototypen für Raketentriebwerke und Motorenteile sind damit ebenso machbar, wie Kleinserien von Schmuck oder individuelle Medizinteile für Unfallopfer.
Wir sind gerade Zeuge, wie eine neue Technik die Fertigung komplett revolutioniert. Es sollte nicht wundern, wenn eines Tages sogar verschlissene Teile für den eigenen Oldtimer oder der alten Sammleruhr nicht mehr beim Schrotthändler oder auf Liebhaberbörsen gesucht, sondern vom Dienstleister frisch aus Pulver in kurzer Zeit nach Hause geliefert werden.
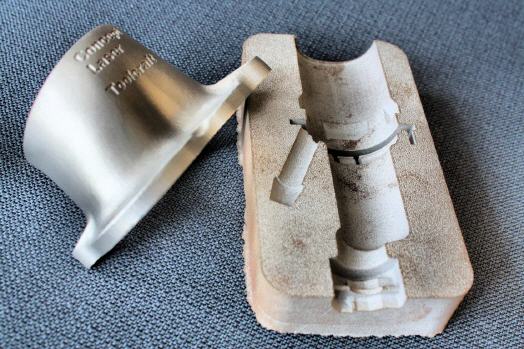
Mehr Informationen zu Concept Laser:
![]() |
CONCEPT Laser GmbH |
![]() |
An der Zeil 8 |
![]() |
96215 Lichtenfels |
![]() |
Tel.: +49 (0) 9571 / 949-238 |
![]() |
Fax: +49 (0) 9571 / 949-239 |
![]() |
E-Mail: info@concept-laser.de |
![]() |
www.concept-laser.de |
War dieser Artikel für Sie hilfreich?
![]() |
![]() |
![]() |
![]() |
![]() |
Bitte bewerten Sie diese Seite durch Klick auf die Symbole.
Zugriffe heute: 18 - gesamt: 12805.