Starke Forschung an Universitäten
Wo die Zukunft geboren wird
Die Luft- und Raumfahrtindustrie ist ein wichtiger Techniktreiber. Hier werden nicht selten Ideen geboren, die später auch in anderen Produkten Verwendung finden. Deutschland hat hier eine starke Stellung, wie etwa die beiden Unis in Stuttgart und München zeigen. Hinter den Mauern dieser Hightech-Schmieden werden diesbezüglich Grundlagen vom Feinsten erforscht.
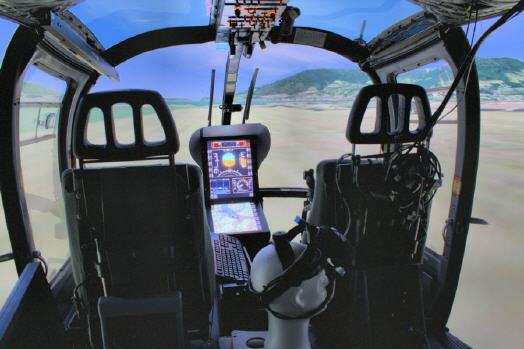
Forschen für mehr Sicherheit
Die TU München verfügt über einen hochmodernen Hubschraubersimulator, mit dessen Hilfe unter anderem Systeme zum Schlechtwetterflug getestet werden können.
Universitäten sind Ideenschmieden. Insbesondere technische Studiengänge sind für Industrienationen extrem wichtig, da die hier getätigte Grundlagenforschung das Gerüst für spätere Produkte bildet, die auf den Weltmärkten künftig für Umsätze sorgen sollen.
Bezüglich der Luft- und Raumfahrttechnik sind in Stuttgart und München exzellente Fakultäten eingerichtet, die junge Leute fit in Sachen Spitzentechnik machen. Dabei wird nicht im luftleeren Raum gelernt und geforscht, sondern an realen Vorzeigeprojekten die Grundlage für ein erfolgreiches Ingenieursleben gelegt. Beispielsweise hat Professor Dipl.-Ing. Rudolf Voit-Nitschmann vom Institut für Flugzeugbau der Uni Stuttgart einen zweisitzigen Motorsegler der Extraklasse ersonnen, der sich im Jahre 2011 zum ersten Mal in die Lüfte erhob: e-Genius. Dieses Flugzeug besitzt eine am Leitwerk angebrachte Luftschraube mit einem für Motorsegler gewaltigen Durchmesser von 2,2 Meter.
Diese Luftschraube wird von einem 72 kW starken und 27 Kilogramm schweren Synchronmotor angetrieben, der von einem 300 Kilogramm wiegenden Lithium-Ionen-Batteriepaket mit einer Gesamtspeicherkapazität von 56 kWh Leistung gespeist wird. Damit kann das Flugzeug ohne fremde Hilfe starten und bei einer Reisegeschwindigkeit von 160 bis 200 km/h eine Entfernung von etwa 400 Kilometer zurücklegen. Der in Benzin umgerechnete Verbrauch ist dabei sensationell niedrig: Nur 0,6 Liter Kraftstoff sind pro Passagier auf 100 Kilometer zu veranschlagen.
Möglich macht dies modernster Leichtbau, der auf CFK fußt und dem mit 16,86 Meter langen Flügeln bestückten Flugzeug eine Leermasse von lediglich 730 Kilogramm verleiht.
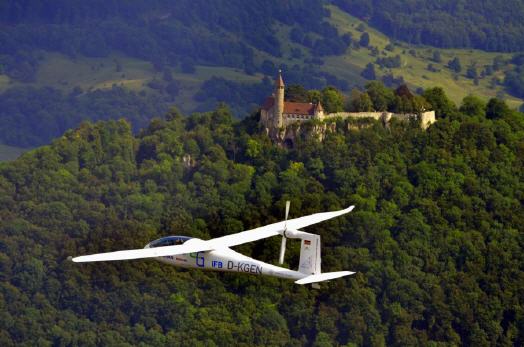
Genial
e-Genius wurde von der Uni Stuttgart in Eigenregie gebaut. Der selbst startende Reisemotorsegler wird von einem Elektromotor angetrieben, ist daher sehr leise und schafft rund 400 km Flugstrecke.
Schon 1996 konnten die Stuttgarter mit ›Icaré II‹, einem Solarflugzeug, zeigen, dass Flugzeugtechnik nicht unbedingt mit Lärm und Gestank verbunden sein muss. 2005 kam man auf die Idee, es einmal mit Wasserstoff zu probieren. Herausgekommen ist das Projekt ›Hydrogenius‹, das am 24. Juli 2007 der interessierten Fachpresse vorgestellt wurde.
Alternativ angetriebenen Fluggeräte werden in Zukunft zumindest für den Transport weniger Personen auf kurzer Distanz interessant sein. Auch die Anwohner von Flughäfen werden mit Freude vernehmen, das künftig sich wohl vermehrt Flugschüler mit ihren Fluglehrern auf lautlosen Schwingen in die Lüfte erheben werden. Der Grund: Der Betrieb derart angetriebener Flugzeuge ist im Vergleich zu sparsamen Trainingsflugzeugen mit Verbrennungsmotor wesentlich kostengünstiger.
Diese Sparsamkeit ist nicht zuletzt dem Werkstoff CFK geschuldet, dessen Verarbeitungsmöglichkeiten ebenfalls in Stuttgart, genauer am Institut für Flugzeugbau, erforscht werden. Unter der Leitung von Prof. Dr.-Ing. Peter Middendorf haben hier schon einige wichtige Erkenntnisse zur Handhabung und Verarbeitung von CFK den Weg in die Serienfertigung gefunden. Doch ist es noch ein weiter Weg, bis bezüglich Umgang und Verarbeitung der Kohlefaser ein ähnliches technisches Niveau erreicht wird, wie es beispielsweise für Stahl schon lange der Fall ist.
So ist die Automatisierung bisher nur teilweise gelungen. Nach wie vor ist viel Handarbeit nötig, um CFK-Matten in funktionsfähige Bauteile zu veredeln, weshalb die Stückkosten dieser Teile höher sind als diejenigen identischer Teile aus Metall. Aus diesem Grund wird bereits bei der Konstruktion darauf geachtet, dass sich Flugzeugteile mit Maschinen erzeugen lassen, die sich bereits in der Textilindustrie bewährt haben. So ist es mit sogenannten Flechtmaschinen möglich, einzelne CFK-Fasern zu Geflechtschläuchen zusammenzuflechten, die dann weiterverarbeitet werden.
Die so erzeugten CFK-Schläuche werden über eine Form gezogen, die derjenigen des benötigten Bauteils entspricht. Hier erfolgt der Harzauftrag mit nachfolgender Aushärtung. Das Problem ist die Entfernung des Kerns, nachdem das Harz trocken ist. Hier behilft man sich beispielsweise mit geteilten Kernen, die gegenläufig auseinandergeschoben werden. Ist dies nicht möglich, verwendet man beispielsweise Kerne aus Wachs, die nach dem Aushärten des CFK-Bauteils durch Wärme einfach aus der Form herauslaufen.
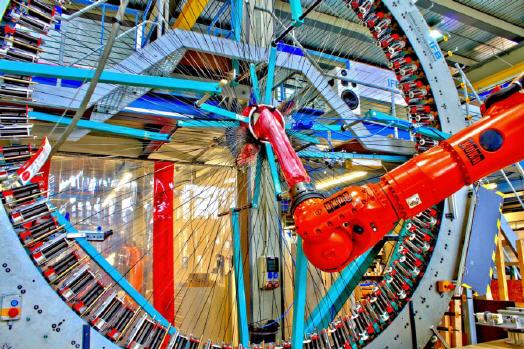
Stricken, statt biegen
Damit CFK-Fasern künftig nicht mehr von Hand zu Bauteilen veredelt werden müssen, forscht man an der Universität Stuttgart daran, diesen Prozess zu automatisieren.
Durch diese zeitraubenden Schritte ist nicht mit einer raschen Durchdringung des automobilen Massenmarktes zugunsten von CFK-Teilen zu rechnen, da hier der dort übliche Fließbandtakt von ein bis drei Minuten nicht einzuhalten wäre. Das Material wird daher aktuell hauptsächlich für höherpreisige Automobilmodelle genutzt und dort auch nur für ausgewählte, relativ einfache Teilegruppen, um Gewicht zu sparen. Hinzu kommt, dass auch der Preis dieser Faser dazu beiträgt, dass sie sich noch nicht auf breiter Front durchsetzen konnte.
CFK-Teile sind teilweise bis zu 500 Prozent teurer, als Teile aus traditionellen Werkstoffen. Die Vorteile dieser Faser werden jedoch in der Luftfahrtindustrie an möglichst vielen Bauteilen genutzt. In dieser Branche werden Zusatzkosten von mehreren 100 Euro pro einem Kilogramm Gewichtseinsparung akzeptiert, da diese Mehrkosten durch den geringeren Treibstoffverbrauch beziehungsweise die höhere Nutzlast relativ zügig wieder zurückfliesen.
Aus diesem Grund ist auch das neueste Airbus-Modell, der A 350, zu 50 Prozent aus CFK gefertigt. Insbesondere die Flügel und das Leitwerk bestehen aus der Hochleistungsfaser. Interessant ist, dass es große Preisunterschiede zwischen der Faser selbst gibt, da verschiedene CFK-Qualitäten zu kaufen sind. Am unteren Ende liegen Fasern, die eine hohe Filamentzahl aufweisen und von einfacher Qualität sind. Ein Kilogramm davon schlägt mit etwa 15 bis 16 Euro zu Buche. Am oberen Ende liegen hingegen Fasern, die sehr steif und fest sind, daher auch 500 bis 1000 Euro pro Kilogramm kosten und deshalb in der Regel nur in der Raumfahrt zum Einsatz kommen.
Neuland musste auch bezüglich der Reparaturmöglichkeit von CFK-Teilen beschritten werden. Insbesondere dann, wenn CFK mit anderen Werkstoffen zu einem Verbund gefügt wird, versagen herkömmliche Methoden der Schadensanalyse. Wenn beispielsweise einem Flugzeugmechaniker der Schraubendreher versehentlich auf den Flugzeugflügel fällt, kann dieser bereits schwer beschädigt sein, selbst wenn äußerlich kein Schaden erkennbar ist. In diesem Fall kommt Ultraschall zum Einsatz, um festzustellen, ob der Flügel repariert werden muss.
Auch bezüglich der Reparatur gibt es Forschungsbedarf, denn anders als bei einem Aluminiumflügel kann hier nicht ein Stück passendes Alublech zugeschnitten und aufgenietet werden. Vielmehr werden hier etwa Roboterprojekte verfolgt, die passende Öffnungen in die schadhafte Stelle einbringen, in die dann maßgefertigte Gegenstücke eingeklebt werden. Natürlich darf der Flügel dadurch nicht geschwächt werden, weshalb Reparaturen an CFK-Teilen ausschließlich ausgebildete Spezialisten durchführen.
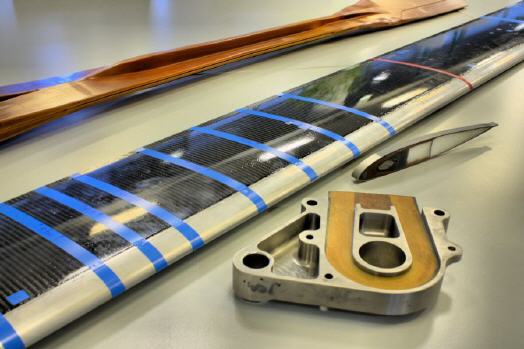
Kostensparend
Überwachungssensoren sollen es künftig ermöglichen, Hubschrauberrotoren nach tatsächlichem Verschleiß auszutauschen.
Kopfzerbrechen bereitet auch das Recycling gebrauchter CFK-Teile. Hier ist aktuell der Trend zu erkennen, den bindenden Harz bei Temperaturen über 200 Grad Celsius zu verbrennen. Zurück bleibt die reine Carbonfaser, der solche Temperaturen nicht schaden, da Carbon erst jenseits der 1 000 Grad-Grenze Schaden nimmt. Parallel zu den Problemen des Leichtbaus wird natürlich untersucht, wohin sich der Markt für Fluggeräte entwickeln wird, denn Flugzeuge lassen sich nur verkaufen, wenn Sie ihre Aufgabe so wirtschaftlich wie möglich verrichten.
Dies bedeutet, dass pro Flug möglichst viele Passagiere sowie Fracht unterzubringen sind, damit der Flug zum lohnenden Geschäft wird. Am Münchner Lehrstuhl für Luftfahrsysteme hat man unter der Leitung von Prof. Mirko Hornung den Trend analysiert und in die Zukunft extrapoliert. Herausgekommen ist ein Turboprop-Flugzeugkonzept für Kurzstrecken bis etwa 2 000 Kilometer, das insbesondere für den asiatischen Markt gedacht ist. In diesem Konzept werden 450 Personen und jede Menge Nutzlast Platz finden.
Doch die Münchner machen nicht nur theoretische Ausarbeitungen, sondern haben mit dem unbemannten Kleinflugzeug ›Impulls‹ ein Testgerät entwickelt, um praxisnahe Grundlagenforschung zu betreiben. Hier öffnet sich vom Leichtbau über den Antrieb mittels Brennstoffzelle bis zur Entwicklung von Sensoren für zivile Überwachungsaufgaben ein weites Betätigungsfeld. Impulls ist komplett aus CFK gefertigt und wiegt daher lediglich 30 Kilogramm bei 10 Kilogramm Nutzlast. Die flexible Konstruktion erlaubt das einfache und rasche Bestücken mit unterschiedlichen Versuchsträgern, was die kostengünstige Durchführung mehrerer Versuche an einem Tag ermöglicht.
Am Lehrstuhl für Hubschraubertechnologie hingegen wird unter der Leitung von Prof. Manfred Hajek erforscht, wie der ideale Rotor eines Hubschraubers auszusehen hat und wie dessen Lebensdauer verlängert, beziehungsweise das Lebensdauerende bestimmt werden kann. Diese mit Fliehkräften von bis zu 1 000 g belasteten Bauteile werden aktuell nach Ablauf einer bestimmten Zahl Flugstunden getauscht, was bei schonender Nutzung des Hubschraubers oft unnötig ist.
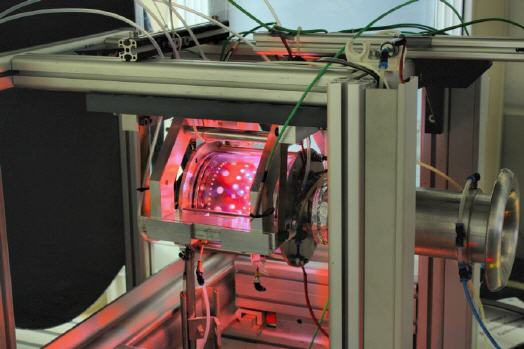
Pulver mit Zukunft
Neue und additiv gefertigte Bauteile werden zunächst in kleinen Triebwerken auf Herz und Nieren geprüft. Die Gasturbine der TU München schafft 120.000 min-1 und wird bis zu 800 Grad Celsius heiß.
Auch die Luftraumsicherheit ist am Institut ein Thema. Dazu steht ein moderner Hubschraubersimulator zur Verfügung, mit dessen Hilfe beispielsweise ein Allwettersystem entwickelt wird, mit dem Piloten künftig auch bei Schlechtwetter zu Hilfseinsätzen aufbrechen können. Der Clou des Systems ist, dass selbst in dichtem Nebel ein Flug möglich wird, da eine Datenbrille dafür sorgt, dass der Pilot die Umgebung erkennen kann und so gefahrlos sein Ziel findet.
Der Lehrstuhl für Flugantriebe wiederum sorgt dafür, dass sich der Hubschrauber überhaupt in die Lüfte erheben kann. Hier werden unter der Leitung von Dr. Andreas Hupfer Triebwerksbauweisen auf Optimierungspotenzial untersucht. Insbesondere die neuartigen additiven Herstellungsverfahren stehen hier im Fokus der Forscher, um Bauteile mit innovativen Geometrien und neuen Funktionen integral anzufertigen. Mittels eigener Triebwerks- und Brennkammerprüfstände lassen sich die Bauteile auf ihre Eignung und Zuverlässigkeit prüfen.Deutschland muss sich also keineswegs verstecken, wenn es um Spitzenforschung im Bereich Luft- und Raumfahrt geht. Jedem angehenden Studenten seien die beiden Unis ans Herz gelegt, um danach beruflich voll durchzustarten.
Mehr Informationen:
War dieser Artikel für Sie hilfreich?
![]() |
![]() |
![]() |
![]() |
![]() |
Bitte bewerten Sie diese Seite durch Klick auf die Symbole.
Zugriffe heute: 6 - gesamt: 1404.