Via Kanban zum Produktionserfolg
Der bessere Weg aus der Kostenfalle
Künstliche Engpässe, geringe Flexibilität, hohe Lagerbestände, geringe Liquidität sowie verschwendete Zeit sind die Folge des Einsatzes zu theoretisch und unflexibel angelegter PPS-/ERP-Systeme. Rainer Weber weist in seinem Buch ›Kanban-Einführung‹ nach, dass das Kanban-System einer reinen IT-Lösung weit überlegen ist.
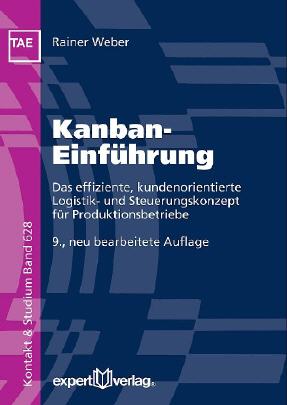
In vielen ERP-/PPS-Systemen wurde hinterlegt, dass Maschinen ständig zu laufen haben und in wirtschaftlichen Losgrößen produziert werden muss. Nur so stimmen die Stundensätze und die Stückzahlen für die Kalkulation. Was jedoch mit den restlichen 800 Teilen geschehen soll, wenn aktuell nur 200 gebraucht werden, ist untergeordnet. In der Folge steigen die Lagerkosten, verringert sich die Liquidität und kommt es zu Engpässen in der Fertigung durch die Produktion nicht benötigter Teile.
In vielen Unternehmen ist in der Produktion aktuell eine Scheinwelt zu besichtigen, die von ungeeigneten ERP-/PPS-Systemen aufrechterhalten wird. Der Grund ist in deren Programmstruktur zu suchen, die durch ein aufwendiges Controlling geprägt ist. Alles und jedes wird über BDE gemeldet und ausgewertet. Jedoch wird nicht geprüft, ob diese Daten tatsächlich stimmen. Ganz zu schweigen davon, dass diese Datenflut hinsichtlich Kunden- und Marktorientierung keine Auswertung erfährt, somit sich das Verhältnis von wertschöpfender Arbeit hin zu nicht wertschöpfender Arbeit immer mehr verkehrt.
Höchste Zeit, die Reißleine zu ziehen und sich von der ERP-/PPS-Schweinwelt zu verabschieden. Wie es besser geht, die eigene Produktion zu entschlacken und wieder schlagkräftig zu machen, zeigt Rainer Weber in seinem Buch ›Kanban-Einführung‹. Der Autor gibt beispielsweise einen Einblick, wie ein Wertstromdesign aussehen muss, um Verschwendung zu erkennen und zu beseitigen. Es gilt, Tätigkeitsschritte zu hinterfragen und möglichst zu eliminieren sowie Formulare zu vereinfachen. Das Ziel ist, das Kanban-System über die ganze Logistikkette einzuführen, das zu selbstauffüllenden Lägern nach dem Min.-/Max.-Prinzip führt.
Mit diesem System ist es beispielsweise möglich, Zahlungsvereinbarungen mit Lieferanten in der Form zu treffen, dass Ware erst dann bezahlt wird, wenn ein Verbrauch entstanden ist. Das Grundprinzip von Kanban lautet, die Ware zum Fliesen zubringen und nicht in großen Mengen ins Lager zu legen. Die Vorteile von Kanban sind vielschichtig. Beispielsweise erlaubt dieses System das frühzeitige Erkennen von Produktionsfehlern, was zu einer besseren Qualität der produzierten Erzeugnisse führt. Dazu sind allerdings hoch qualifizierte Mitarbeiter nötig. Diese können umfassende Arbeitsinhalte handhaben, was wenig Schnittstellen, somit wenig Fehlerquellen ermöglicht.
Mittels Kanban kann die in den letzten Jahren in die Fertigung eingezogene Unsitte, Arbeitspläne immer detaillierter zu erstellen, mit qualifiziertem Personal auf ein vernünftiges Maß zurückgenommen werden. Es genügt, nur noch Meilenstein-Arbeitsgänge festzuhalten. Zudem ist Kanban bestens geeignet, das Lager massiv zu schrumpfen und die Lieferfähigkeit dennoch zu steigern.
Das Geheimnis liegt darin, dass keine einbaufertigen Teile vorgehalten werden, sondern universelle Rohlinge, die auf Anforderung zur gewünschten Variante veredelt werden. Damit dies klappt, müssen Produkte entsprechend konstruiert werden, um möglichst viele, ähnliche Gleichteile zu bekommen, die idealerweise mittels eines parametrischen CNC-Programms auf einer CNC-Maschine fertigbearbeitet werden. In der Folge finanziert sich eine dafür nötige CNC-Maschine durch den Abbau des Lagerbestands praktisch von selbst. Durch Kanban werden demnach Gemeinkosten in Einzelkosten umgewandelt.
Die Einführung eines Kanban-Systems hat aber auch Auswirkungen auf die bisher gewohnte Einteilung von Teilen, die als ABC-Analyse bekannt ist. Wurde bisher eine Einteilung durch Multiplikation von Menge und Preis vorgenommen, so zählen im Kanban-System vielmehr der absolute Preis des betrachteten Teils sowie dessen Dauer der Wiederbeschaffungszeit in Wochen. Die Folge daraus ist, dass geringwertige B- und C-Teile mit langen Lieferzeiten dadurch zu A-Teilen werden, damit keinesfalls der Wertschöpfungsprozess unterbrochen wird, wenn diese Teile benötigt werden.
In der Summe seiner Besonderheiten ist Kanban reinen IT-gestützten Bestandsführungsverfahren überlegen. Das Kanban-System vermeidet Fehlmengen und sorgt für Flexibilität sowie Liefertreue. Das Geheimnis liegt darin, nicht schneller, sondern anders zu Produzieren.
Das Kanban-System ist nach dem Saugprinzip aufgebaut: Aufträge werden nur dort ausgelöst, wo auch Abgänge zu verzeichnen sind. Auf diese Weise wird automatisch nur das gefertigt, was auch benötigt wird. Allerdings ist zu beachten, dass Kanban-Teile nur solche Teile sind, die rund sechs bis acht Mal pro Jahr angefasst werden und die Wiederbeschaffungszeit nicht über fünf Tagen liegt. Aufträge, die größer sind, müssen wie normale Betriebsaufträge mit Liefertermin erfasst werden, da sonst das Kanban-System leergesaugt wird und in der Folge zusammenbrechen würde.
Rainer Weber zeigt in seinem Buch sehr ausführlich diejenigen Schritte, die nötig sind, um Kanban erfolgreich im eigenen Unternehmen einzuführen. Im Buch sind beispielsweise Berechnungsbeispiele für die Festlegung von Kanban-Mengen sowie für die Wiederbeschaffungszeit zu finden. Zudem wird erläutert, wie Behälter und Kisten im Kanban-System gekennzeichnet sein müssen und wie eine Kanban-Karte überhaupt aufgebaut ist.
Der Autor empfiehlt, die RFID-Technik, W-Lan sowie eine Scan-Vorrichtung zu nutzen um die Abläufe prozesssicher zu gestalten. Interessant ist, dass ein ERP-/PPS-System zwar genutzt werden kann, doch bereits Excel ausreicht, um mit Kanban erfolgreich zu arbeiten. Dass sich der Umstieg sehr lohnt, weist der Autor nach: Umsätze steigen, Lieferzeiten sowie Durchlaufzeiten sinken und die Termintreue steigt auf bis zu 99 Prozent.
Mehr Informationen:
![]() |
Titel: Kanban-Einführung |
![]() |
Autor: Rainer Weber |
![]() |
Verlag: Expert-Verlag |
![]() |
ISBN: 978-3-8169-3385-4 |
![]() |
Jahr: 2017 |
![]() |
Preis: 39 Euro |
![]() |
www.expertverlag.de |
War dieser Artikel für Sie hilfreich?
![]() |
![]() |
![]() |
![]() |
![]() |
Bitte bewerten Sie diese Seite durch Klick auf die Symbole.
Zugriffe heute: 17 - gesamt: 950.