Additive Fertigung mit dem Freeformer
Komplette Bauteilgruppen produzieren
Rasante technische Entwicklungen, kurze Produktlebenszyklen, Variantenvielfalt und der Trend zur Individualisierung erfordern hohe Flexibilität in der Kunststoffverarbeitung. Bereits vor Jahren hat Arburg das Potenzial der industriellen additiven Fertigung erkannt und aus Sicht eines Maschinenbauers neben dem Spritzgießen ein weiteres industrielles Verfahren entwickelt und aufgebaut: Das Arburg Kunststoff-Freiformen (AKF) mit dem Freeformer. Das offene System ist für Kunststoffverarbeiter genauso interessant wie für Designbüros und Prototypenbauer.
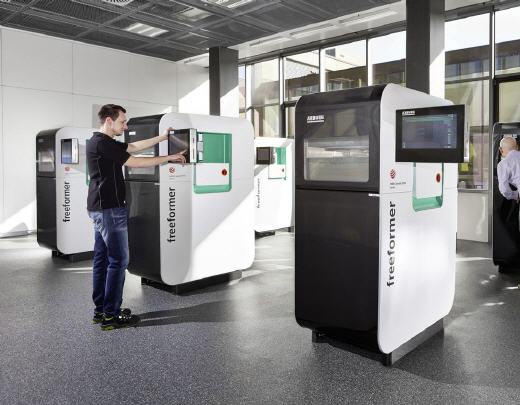
Im Fokus der Anwendungen mit dem Freeformer steht die industrielle additive Fertigung von Funktionsbauteilen. Ein Vorteil des AKF-Verfahrens ist die Möglichkeit, qualifizierte Standardgranulate verwenden zu können. Individuell gefertigte Kunststoffteile für Konsumgüter, medizinische Implantate und Ersatzteile aus Originalmaterial sind nur drei von vielen Bereichen, für die der Freeformer prädestiniert ist. Da es sich um ein offenes System handelt, ist der Anwender unabhängig, er kann eigene Materialien qualifizieren und die Prozessparameter gezielt auf seine jeweilige Anwendung optimieren.
Bereits im Jahr 2004 begann Arburg mit ersten Ansätzen zur Grundlagenforschung, wie sich aus flüssigem Kunststoff kleinste Tropfen erzeugen lassen, um sie werkzeuglos additiv zu verarbeiten. Es folgten Basisversuche und die ersten Patentanmeldungen für das völlig neue Verfahren. Weltpremiere feierte der Freeformer schließlich auf der Messe K 2013 in Düsseldorf. Nach einer Einführungsphase mit Pilotkunden ist das System seit 2015 weltweit im Markt erhältlich. Aufgrund der steigenden Nachfrage ist seit dem Frühjahr 2017 das Arburg Prototyping Center am deutschen Stammsitz in Loßburg in Betrieb. Sechs Freeformer für die industrielle additive Fertigung produzieren dort praktisch rund um die Uhr Musterteile. Damit können die Technologieberater noch schneller auf Anfragen von Kunden reagieren, die sich für einen Freeformer interessieren.
Beim AKF wird ein herkömmliches Kunststoffgranulat ähnlich wie beim Spritzgießen zunächst in einem Plastifizierzylinder aufgeschmolzen. Eine starre Austragseinheit mit spezieller Düse trägt kleinste Tropfen mittels hochfrequenter Piezotechnik im vorgegebenen Takt (60 bis 200 Hertz) schichtweise auf einen über drei Achsen beweglichen Bauteilträger auf. Beim Einspritzen entstehen Massedrücke von bis zu 500 bar. Der Bauteilträger wird so positioniert, dass jeder Tropfen auf die vorher berechnete Stelle gesetzt wird. So entsteht Schicht für Schicht das gewünschte dreidimensionale Bauteil.
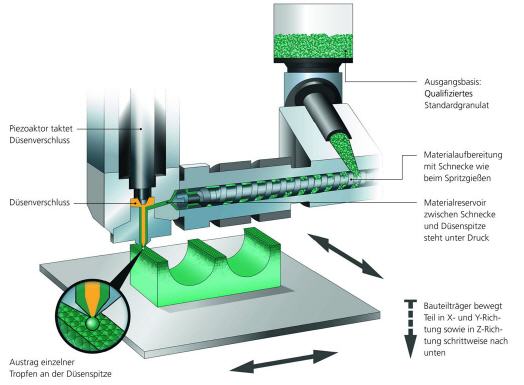
Die Bauteiloberfläche entspricht der eines grob strukturierten Spritzteils. Je kleiner die Düse ist, desto kleiner sind die Tropfen und desto feiner wird die Oberflächenstruktur. Messungen der Zugfestigkeit zeigen, dass die Qualität von Bauteilen für die meisten Funktionsteile und Kleinserien vollkommen ausreicht.
Prinzipiell kann jedes Material plastifiziert werden. Die Aufgabe besteht jedoch darin, aus dem jeweiligen Ausgangskunststoff auch gute Teile zu bauen. Um zu prüfen, ob und wie ein neues Material verarbeitet werden kann, sind zahlreiche Tests und Prüfverfahren erforderlich. Zu den wichtigsten Parametern zählen Verarbeitungstemperatur und Temperaturbeständigkeit.
Hinzu kommen die schichtweise Geometriezerlegung (Slicing) und die automatische Aufbereitung der 3D-CAD-Daten nach qualitäts- und materialabhängigen Kriterien zu einem anlagenspezifischen NC-Programm. Hier fließen Aspekte wie Kanten-, Füll-, Festigkeitsstrategie und Bauraumtemperatur ein. Ergebnis sind voroptimierte Prozessdaten für die einzelnen Materialtypen, die aber auch individuell eingegeben oder verändert werden können und sich gezielt auf die jeweilige Anwendung optimieren lassen.
Die Steuerung des Freeformers hat Arburg ebenfalls selbst entwickelt. Das Bedienpanel besteht aus einem leistungsstarken Industrie-PC mit Multi-Touchscreen, der intuitiv gesteuert wird. Die für den schichtweisen Aufbau der Teile notwendigen Parameter generiert die von Arburg eigen entwickelte Software.
Standardmäßig ist der Freeformer mit zwei Austragseinheiten ausgestattet. Der Bauraum bietet Platz für Teile, die bis zu 154 x 134 x 230 Millimeter groß sind. Die zweite Einheit kann für eine zusätzliche Komponente genutzt werden, um z. B. ein Bauteil in verschiedenen Farben, mit spezieller Haptik oder als Hart-Weich-Verbindung zu erzeugen.
Interessant ist auch das Thema Gewichtsreduktion und Leichtbau. Beispielsweise können bionisch optimierte Bauteile konstruiert und hergestellt werden, ohne fertigungstechnische Zwänge, wie sie beim Spritzgießen gegeben sind, berücksichtigen zu müssen. Ein weiterer Vorteil ist die Möglichkeit zur Funktionsintegration, indem die additive Produktionstechnik Teilefertigung und Montage in nur einem Arbeitsgang kombiniert.
Alternativ lassen sich mit der zweiten Austragseinheit Strukturen aus einem wasserlöslichen Stützmaterial aufbauen und auf diese Weise auch ungewöhnliche oder sehr komplexe Bauteilgeometrien realisieren. Das Angebot an Stützmaterialien für den Freeformer baut Arburg kontinuierlich aus. Neben dem wasserlöslichen Armat 11 gibt es seit Mai 2017 zusätzlich das in Natronlauge lösliche Armat 21. Dieses Stützmaterial ist einfach zu verarbeiten und thermisch stabil. Es verfügt über sehr gute Tropfenbildung und Haftungseigenschaften sowie eine gute Ausbildung von Grenzflächen zum Baumaterial.
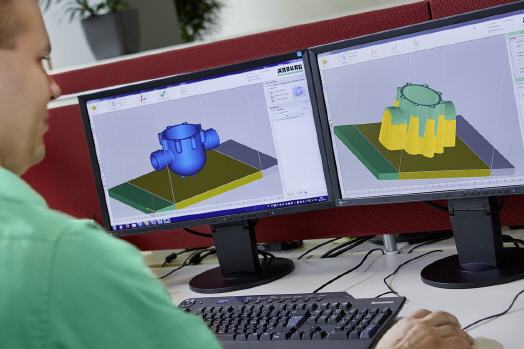
Hinsichtlich Branchen und Einsatzbereichen sind dem Freeformer prinzipiell kaum Grenzen gesetzt. In der Medizintechnik kann er z. B. für die additive Fertigung von Modellen zur Operationsvorbereitung sowie persönlich angepasste Implantate eingesetzt werden, im Automobilbau für Vorserienteile in kleinen Stückzahlen.
Vorteile hinsichtlich Nachhaltigkeit erzielt die additive Fertigung dadurch, dass sich vor Ort tagesaktuell nach Bedarf in variantenreichen Kleinserien bis hin zu Losgröße 1 fertigen lässt. Dadurch kann man auf zusätzliche Logistikkosten und -zeiten verzichten. Das ist gerade auch hinsichtlich steigender Individualität und Variantenvielfalt der Produkte ein wichtiger Aspekt. So lassen sich z. B. Ersatzteile sowie Betriebsmittel wie Montagevorrichtungen und Greifer für Automation schnell, flexibel und kostengünstig nach Bedarf produzieren.
Arburg selbst fertigt mit dem Freeformer dessen eigenen Komponenten in Serie, z. B. das Gehäuse seines Hauptschalters und Transportsicherungen für den Versand. In Kleinserien à 70 Stück entstehen aus dem Hochtemperatur-Kunststoff Polyetherimid (PEI) 0,09 Gramm leichte Abstandshalter, die Arburg bei der Fertigung seiner Allrounder-Spritzgießmaschinen verbaut.
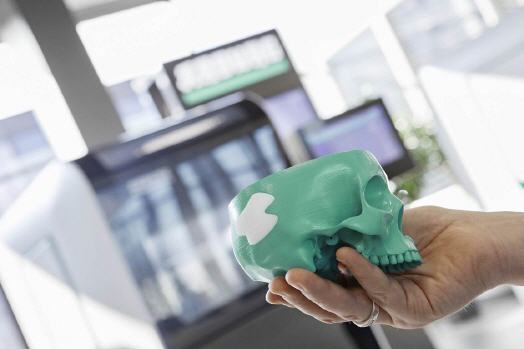
Hinzu kommt die Möglichkeit der Integralbauweise: Komplette Bauteilgruppen können im bereits montierten Zustand produziert werden.
Das Spektrum an Bauteilen, die der Freeformer in den vergangenen Monaten additiv gefertigt hat, umfasst z. B.:
- Nautilus Gear mit gegeneinander beweglichen, Zahnrädern aus einem PC/ABS-Blend mit Flammschutz.
- Eine über Gelenke bewegliche Seilrolle samt Gehäuse und Befestigungshaken aus Bio-PA.
- Aufgabenspezifisch angepasste 2K-Greiferfinger aus PA10 und elastischem TPE.
- Implantat aus resorbierbarem medizinischem Polylactid (Resomer), das sich nach definierter Zeit von selbst im Körper auflöst.
- Luftkanäle aus für die Luft- und Raumfahrt zugelassenem Originalmaterial PC (Lexan 940).
Was Kunden sehr schätzen, wenn sie mit dem Freeformer die additive Fertigung in ihr Unternehmen holen, ist die Flexibilität des offenen Systems. Dies zeigt sich zum Beispiel bei der Neuentwicklung von Produkten direkt aus 3D-CAD-Daten. Konstruktive Änderungen lassen sich sofort umsetzen und die nächste Generation des Prototyps, Designmusters oder eines laufenden Produktes selbst herstellen. Hinzu kommt die Designfreiheit: Selbst Hinterschnitte und komplexe Geometrien, die spritztechnisch nicht entformbar wären, sind möglich.
Um mit additiven Fertigungsverfahren Serienteile in möglichst optimaler Qualität zu erhalten, muss aber die Bauteilkonstruktion dem Verfahren und Herstellprozess gerecht werden. In diesem Kontext sind noch Fragen im Sinne von Konstruktionsrichtlinien offen. Ein weiteres großes Themenfeld für die Serientauglichkeit ist die Vorhersagbarkeit von Qualitätsmerkmalen der in Losgröße 1 produzierten Teile, die von vielen variierbaren Slice- und Prozessparametern abhängen.
Bei der additiven Fertigung von „echten“ Funktionsbauteilen sind mechanische Werte wie Zug- bzw. Reißfestigkeit, Dichte oder auch Veränderungen in der Chemie des Ausgangsmaterials von entscheidender Bedeutung. In diesem Kontext erarbeitet Arburg in Kooperation mit namhaften Forschungseinrichtungen derzeit Fortschritte für den Freeformer und das AKF-Verfahren.
Über die additive Fertigung von Einzelteilen und Kleinserien hinaus lassen sich durch Kombination von additiver Fertigung, Spritzgießen und Industrie 4.0-Technologien Großserienteile veredeln und Kundenwünsche direkt in die Wertschöpfungskette einbinden. Wie eine solche kundenspezifische Individualisierung von Großserienteilen funktioniert, zeigte Arburg z. B. auf der K 2016 sowie Hannover Messe 2017 am Beispiel einer informationstechnisch vernetzten, räumlich verteilten Produktion „smarter“ Kofferanhänger.
Der Freeformer lässt sich auch z. B. mit einem mobilen Kuka Sieben-Achs-Roboter „iiwa“ automatisieren, wie erstmals auf der Fakuma 2016 gezeigt. Dazu wurde er mit einer Euromap-Schnittstelle 67 ausgestattet, über die er mit dem Robot-System kommunizierte. Das Öffnen und Schließen der Haube erfolgte vollautomatisch, der Bauteilträger wurde ebenfalls angepasst.
Fazit:
Die 3D-Drucktechnik erschließt neue Möglichkeiten in der Kunststoffverarbeitung und findet derzeit den Weg in die industrielle Anwendung. Der für die additive Fertigung ausgelegte Freeformer bietet weit mehr als einfache 3D-Drucker. Mit dem offenen System lassen sich funktionsfähige Kunststoffteile auf Basis von 3D-CAD-Daten ohne Werkzeug additiv aus qualifizierten Standardgranulaten fertigen, eigene Materialien einsetzen und die Prozessparameter anpassen. Mit einer solchen industriellen additiven Fertigung lässt sich der Weg zum Serienbauteil und damit zum Markt beschleunigen. Durch Individualisierung von Großserienprodukten können zudem Kunststoffteile so veredelt werden, dass Hersteller daraus einen Mehrwert generieren.
Mehr Informationen zur ARBURG GmbH + Co KG:
![]() |
ARBURG GmbH + Co KG |
![]() |
Arthur-Hehl-Straße |
![]() |
72290 Loßburg |
![]() |
Tel.: +49 7446 33-0 |
![]() |
Fax: +49 7446 33-3365 |
![]() |
E-Mail: contact@arburg.com |
![]() |
www.arburg.com |
War dieser Artikel für Sie hilfreich?
![]() |
![]() |
![]() |
![]() |
![]() |
Bitte bewerten Sie diese Seite durch Klick auf die Symbole.
Zugriffe heute: 18 - gesamt: 10984.