Erfolg mit präziser Messtechnik
Das Tausendstel als neue Referenz
Immer bessere Maschinen sowie Mess-, und Produktionstechnik ermöglichen immer präzisere Produkte. Das Tausendstel scheint mittlerweile sicher beherrschbar. Hermann Diebold, Geschäftsführer der Helmut Diebold GmbH & Co. gewährt Einblick in die Welt kleinster Maße.
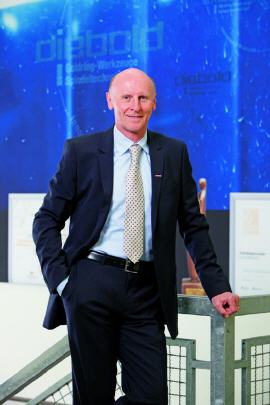
Hermann Diebold, GF der Helmut Diebold GmbH & Co.
Sehr geehrter Herr Diebold, Ihr Unternehmen zählt im Bereich Werkzeugaufnahmen und Spindeltechnik mit zu den Marktführen. Hier ist höchste Präzision gefragt. Wie erreichen Sie diese?
Hermann Diebold: Dazu sind mehrere Faktoren wichtig. Erstens braucht man die dafür qualifizierten Mitarbeiter. Wir bilden seit über 30 Jahren Facharbeiter aus und sind heute mit über 70 Prozent der Belegschaft, die hier ausgebildet wurde, in einer Spitzengruppe technologisch führender Unternehmen angesiedelt. Zweitens braucht man moderne und hochgenaue Maschinen, um höchste Präzision fertigen zu können. Drittens müssen diese Maschinen in einer klimatisierten Umgebung arbeiten. Wir produzieren das ganze Jahr über bei konstanter Temperatur, darüber hinaus temperieren wir das Kühlmittel der Maschinen. Viertens sind hochwertige Messmittel erforderlich, um die kleinsten Toleranzen messen zu können. Und Fünftens muss man sicherstellen können, dass die gemessenen Maße auch stimmen. Also mit anderen Worten: Ein gemessenes Mikrometer muss auch nachvollziehbar ein Mikrometer sein. Seit über zehn Jahren stellen wir Messmittel für die Werkzeugvermessung her und mussten uns bei den Messverfahren und der messtechnischen Einrichtung immer weiter verbessern. Heute arbeiten wir mit einem Messraum der ›Güteklasse 2‹ und den genauesten Messmaschinen, die es auf dem Markt gibt.
Die Temperierung von Fertigungshallen ist auf unterschiedliche Weise machbar. Was haben Sie für ein System installiert?
Diebold: Wir haben ein System installiert, das bis 12 Grad Celsius Lufttemperatur mit freier Kühlung arbeitet. Ist die Luft wärmer, dann nutzen wir Kühlwasser aus dem Fluss, der in der Nähe vorbeifließt. Wenn bei sehr heißen Tagen beides nicht ausreicht, dann benutzen wir unser Klimagerät. Dieses ist etwa drei Monate im Jahr zur Unterstützung notwendig.
Werkzeugmaschinen können mit verschiedenen, genormten Schnittstellen zur Aufnahme der Zerspanungswerkzeuge geordert werden. Welchen Rat haben Sie als Hersteller von Spannmitteln für Käufer neuer Maschinen, wenn diese mit ihrer Neuerwerbung künftig Teile von höchster Genauigkeit produzieren möchten?
Diebold: Stand der Technik ist der HSK-Kegel für den Einsatz auf modernen Werkzeugmaschinen. Er ist weltweit verbreitet und durch die Normung international akzeptiert. Der HSK-Kegel mag nicht die perfekteste Lösung sein, aber durch seine weite Verbreitung und das Wissen der Anwender, wie man den HSK-Kegel anwendungstechnisch gut ausnutzen kann, ist er sicher eine gute Lösung. Bei weiter steigenden Drehzahlen und weiterer Miniaturisierung der Werkzeuge könnten durchaus andere Aufnahmelösungen entstehen.
An welche alternativen Aufnahmelösungen denken Sie hier?
Diebold: Man kann zum Beispiel Werkzeuge ohne einen Werkzeughalter als Zwischenstück direkt in die Spindel einschrumpfen. Oder Werkzeugaufnahmen nutzen, die fest mit der Spindel verbunden sind und ein modulares Vorderteil zur Aufnahme der Schneiden haben. Hier hätte man auch noch andere Effekte zu erwarten wie geringere Unwucht und Schwingungsdämpfung.
Damit die Maße beim Zerspanen exakt erreicht werden können, muss die Spannmittel-Schnittstelle die ihr zugedachte Aufgabe perfekt erfüllen. Worauf sollten Käufer diesbezüglich besonders achten?
Diebold: Wir empfehlen allen Anwendern sehr genau darauf zu achten, wo sie ihre Werkzeugaufnahmen beschaffen. Wir werden oft zu Hilfe gerufen, wenn die Schnittstelle „versagt“. Üblicherweise kauft man beim Händler seines Vertrauens ein, dieser kann aber nicht ohne weiteres die normgerechte Genauigkeit der verkauften Werkzeugaufnahmen nachvollziehen. Wenn dann Probleme mit den Genauigkeiten der Werkstücke oder den Standzeiten der Werkzeuge in der Produktion auftreten, kommen die Probleme offensichtlich in den Fokus der Nutzer und der Beschaffer. Dann ist das Kind längst in den Brunnen gefallen und der Anwender muss oft nochmals neu in die Werkzeugaufnahmen investieren.
Spannmittel wollen gepflegt sein, sollen sie ihren Zweck auf Dauer erfüllen beziehungsweise ihre Präzision beibehalten. Haben Sie hier Tipps für die Anwender, dies zu erreichen?
Diebold: Wenn wir unsere Kunden vor Ort beraten, sehen wir oft schon von Weitem, dass die Werkzeugkegel nicht mehr ok, also verschlissen oder mit Eindrücken versehen sind, die das Spannergebnis verschlechtern. In diesen Fällen haben wir dann die passende Messtechnik im Servicekoffer dabei, um zu prüfen, ob die Werkzeughalter normgerecht sind. Dies bieten wir inzwischen als Dienstleistung an, die immer öfter mit der Konsequenz in Anspruch genommen wird, dass oft sogar neue und unbenutzte Werkzeughalter aus der Produktion fremder Mitbewerber ausgesondert werden müssen.
Mittlerweile ist in der Branche das Mikrometer das Maß der Dinge. Wo ist denn eine sinnvolle Genauigkeitsgrenze für Werkzeug- beziehungsweise Messmaschinen?
Diebold: Werkzeugmaschinen werden in ihrer Genauigkeit ständig verbessert. Man kann heute im Bereich ›Fräsen‹ sehr hochwertige Maschinen bekommen, die Fräsgenauigkeiten unter 0,005 mm erreichen. Um die Maschinengenauigkeit nutzen zu können, muss aber das Gesamtpaket stimmen. Die Maschine, die Spindel, die Werkzeugaufnahmen und die Schneidwerkzeuge müssen zwingend von ausgeprägter Genauigkeit sein. Messmaschinen gibt es in verschiedenen Genauigkeitsklassen, je nach Anforderung des Anwenders. Da wir bezüglich der Präzision inzwischen unter einem Mikrometer bei der Produktion unserer Werkzeughalter, Spindelkomponenten und Messtechnikprodukte angekommen sind, müssen unsere Messmaschinen sehr genau sein. Sie sind in der Lage, unter 0,4 my Genauigkeit zu messen, aber dazu muss die Messumgebung, respektive der Messraum der Güteklasse ›2‹ entsprechen. Das bedeutet, dass die Temperaturkonstante in diesem Messraum mit 0,5 Kelvin pro Meter garantiert sein muss. Eine solche Einrichtung ist in der Werkzeugbranche und der Spindelwelt nur äußerst selten anzutreffen.
Besteht die Gefahr, dass alleine aus Marketinggründen die aktuelle Grenze der Messtechnik unterschritten wird, obwohl keine technischen Vorteile mehr zu erwarten sind?
Diebold: Nach meiner Meinung nicht. Man kann aktuell erreichbare Fräsprozesse in Punkto ›Genauigkeit‹, ›Drehzahl‹ und ›Miniaturisierung der Werkzeuge‹ noch deutlich weiter verbessern. Bei sehr hohen Drehzahlen im Bereich von 60 000 bis 100 000 U/min kann man zum Beispiel Fräsen durch Schleifen ersetzen oder zumindest ergänzen und damit ganz andere Herstellprozesse umsetzen. Wir sehen das bei den Spindelkomponenten die wir herstellen. Die Toleranzen der einzelnen Bauteile, die zu einer Motorspindel zusammenmontiert werden summieren sich sehr wohl. Wir können am Wachstum und am Unwuchtverhalten einer Spindel sehr gut quantifizieren, wie das Verhalten der Spindeln dann in der Maschine sein wird.
Sie haben Einstellmeister im Programm. Diese werden nur in größeren Zeitabständen benutzt. Was ist bei deren Lagerung zu beachten?
Diebold: Es stimmt, dass Einstellmeister nur unregelmäßig benötigt werden. Aber die Mehrzahl unserer Kunden benutzen diese Einstellmeister laufend in der Produktion, um ihre Messgeräte einzustellen. Hier gibt es dann durch das taktile Messen gewisse Abnutzungen und die Einstellmeister müssen regelmäßig überprüft und gegebenenfalls nachgearbeitet oder sogar erneuert werden. Das Gleiche gilt auch für unsere Kegelmessgeräte, die sehr filigran aufgebaut sind und aus vielen beweglichen mechanischen Bauteile bestehen. Diese können durch Kühlmittel, das an den zu prüfenden Werkstücken anhängt, verkleben und müssen deshalb regelmäßig gewartet werden, um Fehlmessungen zu vermeiden. Die Wartungszyklen kann jeder Anwender selber festlegen. Bei den Anwendern sehen wir oft Messmittel aus unserer Produktion, die aus unserer Sicht „abgelaufen“ und für eine Kalibrierung oder Wartung fällig sind. Wir haben jetzt eine Seriennummernverwaltung installiert, die es uns ermöglicht, die Anwender an eine fällige Kalibrierung zu erinnern und diesen Service durchführen zu lassen. Wir erwarten dadurch eine zukünftig deutlich höhere Zahl an Kalibrierungs-Zertifikaten die wir ausstellen werden.
Sie vertreiben auch ein Kegelmessgerät, das mit einem einzigen Meßvorgang gleich mehrere Messpunkte misst. Ein Beispiel, dass es nicht immer CNC-Technik sein muss?
Diebold: Das ist richtig. Mit unserem Kegelmessgerät kann man alle Funktionsmaße am HSK-Kegel messen und im gleichen Messvorgang auch die Innenkontur prüfen. Die Kegellinie und die Kegelform in Bezug zur Plananlage sind wichtig. Entscheidend beim HSK-Kegel sind aber auch die Spannschulterschräge und die Auswerfertiefe, da der HSK-Kegel beim Spannen deformiert wird und deshalb zum Wechseln mit Kraft ausgestoßen werden muss. Noch wichtiger ist aber die Spannschulterschräge für die Spannklauen des Einzugssystems. Ist diese Spannschulter unrund oder in der Lage fehlerhaft, dann wird das Werkzeug nicht korrekt in die Spindel eingezogen. Die Folge ist, dass sich der Rundlauf erheblich verschlechtert. Dies kann ein Händler, wie vorhin bereits gesagt, in der Regel nicht nachmessen, er ist da voll auf seinen Lieferanten angewiesen. Und genau hier treffen wir immer wieder auf die angesprochenen Probleme bei den Anwendern, wenn diese ungenügend genaue Werkzeugaufnehmen erworben haben.
Die Qualitätsnorm DIN 9001 ist eigentlich als Anleitung gedacht, Qualität zu erreichen. Nirgendwo steht, dass sich danach arbeitende Unternehmen einem teuren Audit unterziehen müssen. Warum geben dann Unternehmen alle paar Jahre irre Summen aus, um bestätigen zu lassen, dass sie nach dieser Norm arbeiten?
Diebold: Nach Norm zu arbeiten ist eine Sache, einen messbaren Nutzen daraus zu ziehen ist die andere. Wir sind zertifiziert und haben daraus viel gelernt, weil wir uns nicht nur an der Norm entlanggehangelt haben, sondern darin einen kontinuierlichen Verbesserungsprozess sehen. Am Anfang gab es viele Punkte zu verbessern, inzwischen ist für uns ein Update der Zertifizierung oder eine Verlängerung kein großer Aufwand mehr. Ich komme in vielen Firmen rum und wir arbeiten auch mit vielen Firmen zusammen, ich sehe aber oft schnell unerledigte Dinge vor Ort in Firmen aller Branchen, für die wir kein ISO-Zertifikat bekommen würden. Also Transparenz und genau festgelegte Prozesse machen sich nach meiner Meinung für jedes Unternehmen bezahlt, wenn man die Prozesse lebt und sich nicht nur damit befasst, wenn gerade die Zertifizierung ansteht.
Das soll ja der Sinn der DIN 9001 sein, Qualität zu erreichen. Doch schon Philip B. Crosby, der mittlerweile verstorbene „Qualitätspapst“ warnte vor dem Zertifizierungswahn. Er beklagt, dass damit der Wettbewerb ausgehebelt wird und Unternehmen unter einem immensen Bürokratieberg ersticken.
Diebold: Die Norm sieht sicher sehr nach Bürokratie aus und wenn man nicht entsprechend vorgeht, können die Kosten leicht aus dem Ruder laufen. Auch wir haben viel Geld dafür ausgegeben, aber ohne Zertifikat würde ich mich aus Wettbewerbsgründen nicht an den Markt trauen.
Es spricht absolut nichts dagegen, nach einer Qualitätsnorm zu arbeiten. Es kann jedoch nicht sein, dafür immense Summen zu verlangen, damit ein Zertifikat ausgestellt wird, das einen selbstverständlichen Sachverhalt bestätigt. Gibt es nicht zu denken, dass auf dem Rücken von Unternehmen, insbesondere von Startups, Geschäfte gemacht werden?
Diebold: Nun ist der Aufwand für uns nicht kriegsentscheidend. Da wir eine sehr schlanke Organisation mit kurzen Wegen haben, ist der Zertifizierungsaufwand für uns überschaubar. Aber Sie haben schon recht, lieber Herr Fottner, dass hier bürokratische Aufwände da sind, die nicht unmittelbar zur Verbesserung der Qualität der Produkte beitragen. Und von Bürokratie werden wir ja momentan gerade nicht verschont, ich möchte nur mal an das Formularwesen wegen Einhaltung des Mindestlohns erinnern, den wir in der Präzisionsindustrie ja wohl korrekt einhalten und um einen hohen Faktor überschreiten. Wenn man von Milliardenbeträgen ausgeht, die dem Staat durch Schwarzarbeit entgehen, wäre das ein besserer Ansatz für Gleichbehandlung der Arbeitenden Bevölkerung.
Da bin ich ganz bei Ihnen. Der zuvor bereits erwähnte amerikanische Erfinder der ›Null-Fehler-Strategie‹, Philip B. Crosby, schreibt in seinem lesenswerten Buch ›Qualität ist und bleibt frei‹, dass Qualität nichts mit starren Normen, hingegen sehr viel mit fähigen und wertgeschätzten Mitarbeitern im Unternehmen zu tun hat. Nochmals: Sind daher QM-Zertifikate angesichts der Rückrufe von Automobilen, zusammenbrechender U-Bahn-Schächte und mangelhafter Pflege in Altenheimen nur teures Blendwerk?
Diebold: In den genannten Fällen wurden wohl gravierende Fehler gemacht. Wir im Hause Diebold haben nach wie vor die Null-Fehler-Strategie und prüfen alles sehr intensiv. Schon aus dem einfachen Grund, dass man in der Präzisionswerkzeugindustrie nicht an 10 000 guten Teilen gemessen wird, sondern an dem einen schlechten Teil, das man bedauerlicherweise geliefert hat. Nach über 30 Jahren in der Praxis weiß ich, wovon ich spreche. Hier kann man sich heute mehr denn je einen Wettbewerbsvorteil erarbeiten, was gerade in unserem Segment sehr wichtig ist, weil es immer einen Nachahmer gibt, der glaubt, ein Produkt billiger machen zu können. Wir bei Diebold überzeugen hingegen durch außerordentlich gute Qualität, was unseren Erfolg ausmacht.
Viele Firmen haben ihre Eingangkontrollen reduziert, da sie davon ausgehen, dass die Produkte eine Qualitätskontrolle beim Hersteller durchlaufen haben. Oft werden jedoch maßlich fehlerhafte Teile später in der Produktion dennoch entdeckt. Diese sind dann unter Umständen bereits verbaut. Eine absolut fehlerfreie Produktion ist also noch lange kein Standard. Wo liegen die Schwachstellen?
Diebold: Die Schwachstellen sind offensichtlich, wenn ich ein gekauftes Produkt verbaue ohne sicher zu sein, dass alle Teile in Ordnung sind. Wir stellen Hochfrequenzspindeln her, bei denen 50 Prozent des Wertes Kaufteile sind: Motor, Lagerung, Spannsystem, Sensorik et cetera. Auf alles müssen wir Garantie geben. Also können wir hier keine Kompromisse eingehen und prüfen alles zu 100 Prozent. Das Versagen eines gekauften Bauteils wäre viel teurer als die doch aufwendige Kontrolle.
Die Automatisierung beim Fertigen und Prüfen der Einzelteile könnte helfen, die Fehlerquote der montierten Baugruppen zu senken. Andererseits sind Facharbeiter wesentlich flexibler im Fall von Störungen. Wie wird sich die Arbeitswelt in diesem Bereich künftig darstellen?
Diebold: Roboter sollen den Mitarbeitern die Arbeit erleichtern. Ein gut ausgebildeter Technologe ist mir eigentlich zu schade für Material-Handlingsaufgaben. Wenn sich Messprozesse automatisieren lassen, ist das sicher eine feine Lösung. Da wir uns aber bei allen unseren Teilen im my-Bereich bezüglich der Genauigkeit befinden, sind Automatisierungslösungen bisher im Vergleich zum menschlichen Können gescheitert. Wir könnten es uns leichter machen und einfach „innerhalb der Norm“ fertigen, unser Anspruch ist aber höher und deshalb können wir auch bestätigen, dass wir mit den Genauigkeiten unserer Produkte eine gewisse Sonderstellung einnehmen. Das war ein langer und teurer Weg, verbunden mit viel Training und Investitionen, aber nur so können wir weitere Herausforderung für die Steigerung der Genauigkeiten von Bauteilen meistern.
Fähige Menschen sind der einzige Rohstoff, den Deutschland in nennenswertem Umfang besitzt. In Baden Württemberg und anderen Bundesländern mit links orientierter Regierung wird das Bildungswesen massiv verwässert. Stichworte sind: ›Gender‹ und ›Abi für alle‹. Eine Gefahr für den Industriestandort Deutschland, da künftig wohl immer mehr fehlbeschulte junge Leute auf den Arbeitsmarkt kommen?
Diebold: Wir bei Diebold und ich persönlich verwende sehr viel Zeit für dieses Thema. Wir arbeiten sehr eng mit den Schulen zusammen und wollen diesen auch helfen, die Zeiten der politischen Unsicherheit zu durchstehen. Ich möchte hier nicht im Einzelnen darauf eingehen, was ich für bedenklich halte, wir stellen uns einfach der Situation und machen das Beste daraus. Bisher funktioniert es gut, ich kann aber noch nicht genau einschätzen, inwieweit die Demoskopie hier negativ zuschlagen wird und wir keinen geeigneten Nachwuchs mehr bekommen werden. Wenn es aber so kommt, wird es weitreichende Konsequenzen für unser Unternehmen haben. Meine Söhne sind 12 und 15 Jahre alt, stecken mitten in der Schulausbildung und spüren natürlich auch, wie sich die Schullandschaft verändert. Sie schnuppern ständig Unternehmerluft. Wir reden häufig und intensiv über dieses Thema und verfolgen gemeinsam die Presse. Die beiden haben dann auf jeden Fall frühzeitig erfahren, auf welche Situation sie gefasst sein müssen, wenn sie eines Tages in die Firma einsteigen werden. Ich bin auch bewusst Elternbeirat in beiden Klassen geworden, um an der Entwicklung der Schullandschaft dranzubleiben. Und Sie dürfen mir glauben, dass ich offensiv über diese Thema rede, wenn ich Landespolitiker persönlich treffe.
CO2-Zertifikate soll verknappt und massiv verteuert werden. Es besteht die Gefahr, dass dadurch die stahlerzeugende Industrie aus Europa abwandert. Eine mögliche Folge wird sein, dass hochwertige Stähle nur mehr mit großen Lieferzeiten verfügbar sind. Was bedeutet das für Ihr Unternehmen?
Längere Lieferzeiten wären natürlich problematisch. Auch heute haben wir schon erhebliche Probleme, das erforderliche Material zu beschaffen. Da wir viele hochwertige Sonderteile herstellen, ist eine gute Verfügbarkeit von erstklassigem Material sehr wichtig. Wenn wir das nicht schaffen, dann können wir mit der Herstellung von außergewöhnlichen Teilen im High Tech-Bereich nicht mehr erfolgreich sein. Und mit ›commodity products‹ können wir in Deutschland bekanntlich ja schon lange kostenmäßig nicht mehr mithalten.
Die additive Fertigung schickt sich an, immer mehr Bereiche zu erobern. Zunehmend bessere Technik macht Produkte möglich, die sich nicht mehr von traditionell durch Zerspanen hergestellte Produkte unterscheiden. Wie schätzen Sie diese Technik für Ihr Produktspektrum ein?
Da wird es sicher zukünftig interessante Produkte geben, wenn man mehrstufige oder modulare Produkte mit entsprechender Innenkontur herstellen möchte. Aber viele Neuerungen die wir jetzt schon haben, brauchen einfach ihre Zeit, bis sie vom Markt erkannt, akzeptiert und dann auch in der Breite eingesetzt werden. Wir befassen uns intensiv mit der Trockenbearbeitung oder zumindest mit intelligenter Kühlmittelzuführung durch Werkzeughalter. Erstaunlicherweise hat sich die Stimmung in der Serienfertigung wohl gedreht und man geht wieder auf Schwallspülung zurück.
Herr Diebold, vielen Dank für das Interview.
Download:
Diesen Artikel können Sie hier im PDF-Format herunterladen [331 KB] .
Mehr Informationen zu Diebold:
![]() |
Diebold Goldring Werkzeuge GmbH & Co. |
![]() |
An der Sägmühle 4 |
![]() |
72417 Jungingen |
![]() |
Telefon 07477 871-0 |
![]() |
Fax 07477 871-30 |
![]() |
E-Mail: kontakt@hsk.com |
![]() |
www.hsk.com |
War dieser Artikel für Sie hilfreich?
![]() |
![]() |
![]() |
![]() |
![]() |
Bitte bewerten Sie diese Seite durch Klick auf die Symbole.
Zugriffe heute: 17 - gesamt: 12042.