Vom Pulver zur scharfen Schneide
Meisterhaft zur Top-Wendeschneidplatte
Wendeschneidplatten, Fräser und Bohrer werden überwiegend aus Hartmetall hergestellt. Bei diesem hochspezialisierten Bereich der Pulvermetallurgie wird das Material mechanisch verdichtet, anschließend in einem Ofen gesintert und danach zu gebrauchsfähigen Schneidwerkzeugen veredelt. Ein Spezialist auf diesem Sektor ist das Unternehmen Horn, das sich mit hochwertigen Zerspanungswerkzeugen weltweit einen hervorragenden Namen gemacht hat.
Der erste Hochleistungs-Zerspanungswerkstoff wurde bereits im Jahre 1900 unter der Bezeichnung ›Schnellarbeitsstahl HSS‹ (HighSpeedSteel) vorgestellt. Da große Schnittgeschwindigkeiten eine hohe Härte und große Vorschübe – vor allem beim unterbrochenen Schnitt – eine hohe Zähigkeit des Zerspanungswerkstoffs erfordern, folgten bis zum Ende des 20. Jahrhunderts weitere Entwicklungen, alle mit dem Ziel, die Härte und Zähigkeit der Schneidstoffe zu steigern.
Die Suche nach einer optimalen Kombination beider Materialeigenschaften brachte neue Schneidstoffgruppen wie Hartmetalle, Cermets, Schneidkeramiken, superharte Schneidstoffe wie kubisches Bornitrid sowie polykristalline und monokristalline Diamanten auf den Markt.
Mit diesen Entwicklungsschritten verbesserte sich auch die Härte der Schneidwerkstoffe. HSS erreicht etwa 800 HV30, Diamant 10 000 HV30 und die unterschiedlichen Hartmetalllegierungen weisen Härtegrade von 800 bis 2 800 HV30 auf. Letztere sind dank ihrer überzeugenden Abstimmung von Härte und Zähigkeit deshalb vorwiegend dort im Einsatz wo besonders starker Verschleiß in Verbindung mit Schlagbeanspruchung zu erwarten ist.
Hartmetall ist ein Kompositwerkstoff. Seine wichtigsten Bestandteile sind extrem harte Karbide wie Wolframkarbid sowie ein zähes metallisches Bindemittel, meistens Kobalt. Die anwendungsorientierte Kombination dieser und weiterer Bestandteile führt zu den herausragenden Eigenschaften bei der Zerspanung.
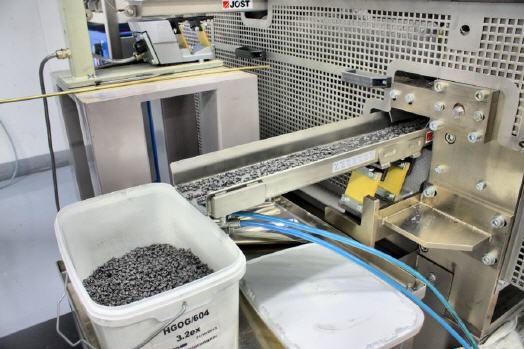
Herausfordernde Prozesskette
Wolfram stammt zu über 50 Prozent aus chinesischen Lagerstätten. Das Kobalt für die Bindephase kommt unter anderem aus der Republik Kongo. Die instabilen Rohstoffmärkte und der davon beeinflusste Preis wirken sich deshalb ganz anders auf die Beschaffung aus, als bei den Bestandteilen anderer Zerspanungswerkstoffe.
Wegen des hohen Schmelzpunktes von Wolfram, der bei 2 000 bis 4 000 Grad Celsius liegt, lassen sich Karbide schmelztechnisch nicht verarbeiten. Hartmetall-Produkte müssen deshalb auf pulvermetallurgischem Wege hergestellt werden. Dieser Prozess erfolgt in der Regel in drei Schritten: Herstellen der metallurgischen Legierung aus Metallpulver und Metallkarbid-Pulvergemisch, Pressen des Pulvergemischs in die gewünschte Form und Sintern der Presslinge zum kompakten und harten Hartmetall.
Bei vielen Schmelzprozessen scheiden sich die Verunreinigungen als Schlacke von der gewünschten Schmelzlegierung ab. Dieser Vorteil lässt sich bei der pulvermetallurgischen Fertigung nicht nützen, da die Karbide beim Sintern nicht aufgeschmolzen werden. Das führt dazu, dass sich jede Verunreinigung im Pulvergemisch als Fehler im Endprodukt auswirkt. Äußerste Sorgfalt ist deshalb eine Grundvoraussetzung beim Mischen und Verarbeiten bis hin zum Sintern – vergleichbar der Herstellung von Hochleistungskeramiken.
So vielfältig wie die Anwendungen von Hartmetall-Werkzeugen, so vielfältig sind auch die zu ihrer Herstellung benötigten Formen. Sie reichen von Kugeln für Kugelschreiberspitzen bis zu Hochdruckkolben für die Kunststoffindustrie mit 1 000 mm Länge, 130 mm Durchmesser und 200 kg Gewicht. Um diese Formenvielfalt wirtschaftlich herstellen zu können, kommen aktuell die vier Formgebungsverfahren Axialpressen, Spritzgießen, Strangpressen und Blockpressen mit Nachformen zur Anwendung.
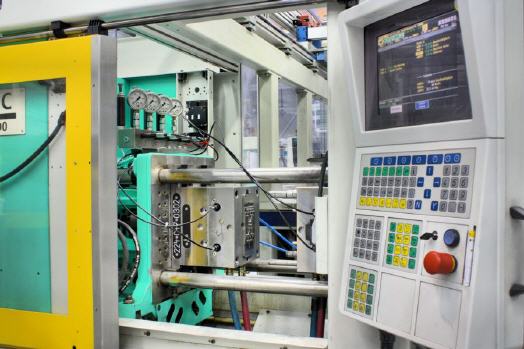
Mit Druck zum Rohling
Zur Fertigung von Wendeschneidplatten wird das mit einem Plastifizierungsmittel vermischte Hartmetallpulver mit einem Druck von 1,3 bis 2,3 Tonnen/cm⊃2; in einer Formpresse zum Fertigteil gepresst. Die so entstehenden Rohlinge sind äußerst bruchempfindlich und werden daher ohne weitere Bearbeitung von Handhabungssystemen direkt auf den Sinterplatten abgelegt und dem Sinterofen zugeführt.
Durch Spritzgießen lässt sich eine hohe Zahl von Freiheitsgraden realisieren. Das Verfahren kommt deshalb vorwiegend bei komplex geformten Wendeschneidplatten zur Anwendung. Das Hartmetallgranulat wird bei 130 bis 150 Grad Celsius in die Kavitäten der Spitzgießwerkzeuge gespritzt. Nach einer Abkühlphase stößt die Maschine das so geformte „Spritzbild„ aus. Anschließend werden die Wendeschneidplatten-Rohlinge mechanisch, beispielsweise mittels Laser, vom Anguss trennt.
Die Wendeschneidplatte gelangt danach zur weiteren Bearbeitung, wo der Anguss separiert und wiederverwendet wird.Stabförmige Hartmetallteile entstehen durch Strangpressen. Bei dieser Umformung wird das Gemisch aus Pulver und Presshilfsmitteln mittels eines großen Druckkolbens durch die Öffnung eines Strangpresswerkzeugs gedrückt und dabei verfestigt. Dabei entstehen Hartmetallstangen unterschiedlicher Querschnitte, die je nach Erfordernis auf Länge getrennt werden. Für große Hartmetallteile, Einzelteile und kleine Losgrößen wird das Hartmetallpulver in einer isostatischen oder monostatischen Presse bei 2.000 bis 2.500 bar in Grünlingblöcke oder -stangen gepresst.
Die Grünlinge weisen in etwa die Konsistenz von Kreide auf, sie können daher durch Drehen, Fräsen, Bohren und Schleifen weiterbearbeitet werden. Bei der Horn Hartstoffe GmbH kommen alle vier Formgebungsverfahren zum Einsatz. Entsprechend den wachsenden Einsatzmöglichkeiten und den Fortschritten in der Verfahrenstechnik werden sie kontinuierlich weiterentwickelt um den zukünftigen Anforderungen an komplexe Produktgeometrien in wirtschaftlicher Weise gerecht zu werden.
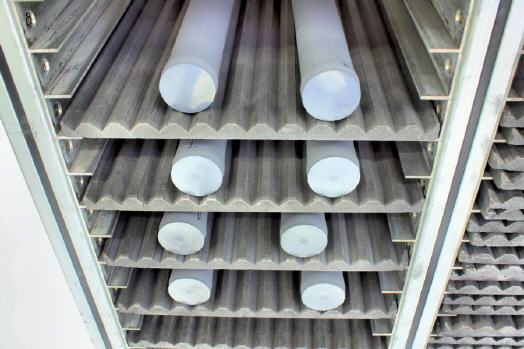
Sintern sorgt für Härte
Das Vorsintern löst die Presshilfsmittel bei 200 bis 500 Grad Celsius aus den Hartmetall-Presslingen. Der zweite thermische Prozessschritt ist das Sintern. Bei diesem metallurgisch wichtigsten Arbeitsgang werden die Teile bei genau abgestimmten, zeit- und temperaturgesteuerten Gasbedingungen im Ofen auf 1300 bis 1600 Grad Celsius erhitzt. Die metallische Bindephase (Kobalt) schmilzt und vernetzt sich mit den Karbiden, sodass ein dichtes Hartmetall entsteht.
Bei diesem Dichtsintern schrumpft das Volumen der Teile um 40 bis 50 Prozent. Der Längenschwund beträgt etwa 20 bis 25 Prozent. Die Berücksichtigung dieses Schwundes schon bei der Herstellung der Werkzeugform stellt besonders hohe Anforderungen an den hauseigenen Werkzeug- und Formenbaubau. Bei Horn wird jede Sinterfahrt sortenrein gefahren, dadurch müssen keine Kompromisse bei der metallurgischen Qualität der Hartmetallprodukte eingegangen werden.
Der gesinterte Rohling wird nun in die Schleiferei weitergeleitet, wo Roboter die Rohlinge zum Schleifen in eigens für diesen Zweck umgebaute Fünfachs-Bearbeitungszentren des Fabrikates ›DMG‹ einlegen. Horn hat sich für diese Eigenbautechnik entschieden, da trotz des Angebots verschiedener Hersteller keine Schleifmaschine zu bekommen war, die den eigenen Ansprüchen vor allem hinsichtlich Automatisierung, Meßtechnik und Einbindung in den internen Datenfluss genügte.Da auch Hartmetall alleine keine Wunder beim Zerspanen schwer zerspanbarer Metalle vollbringen kann, erhalten diese Werkzeuge entsprechend des Einsatzzweckes eine Beschichtung im PVD-Verfahren (Sputtertechnologie).
Mit modernsten Maschinen lassen sich alle derzeit gängigen Beschichtungen wie TiAlN, TiN und TiAlCN sowie die Eigenentwicklungen von Horn aufbringen. Bei etwa 400 bis 600 Grad Celsius werden je nach Werkzeug 1,5 bis 10 µm dicke Hartstoffschichten aufgebracht, ein Prozess, der je nach Schichtdicke 7 bis 14 Stunden dauert.
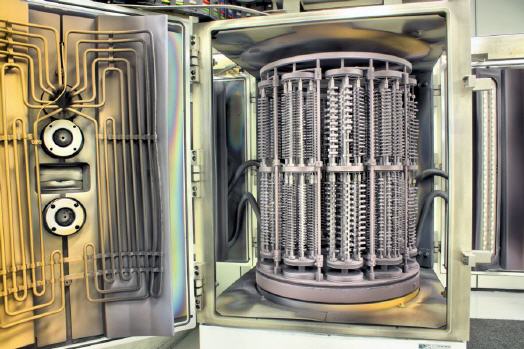
Stück für Stück Qualität
Dadurch, dass Horn alle entscheidenden Schritte zur Herstellung hochwertiger Wendeschneiplatten selbst ausüben kann, ist die Sicherheit gegeben, höchste Qualität zu liefern. Unterstrichen wird dies zusätzlich durch eine extrem leistungsfähige Qualitätskontrolle, in der sowohl vollautomatisch als auch teilweise manuell die produzierten Wendeschneidplatten geprüft werden. Und das zu 100 Prozent.
Dadurch gibt es keine ausgelieferte Wendeschneidplatte, die nicht geprüft und für den harten Arbeitsalltag tauglich erklärt wurde. Dennoch ist das Unternehmen Horn in der Lage, Sonderwerkzeuge in nur fünf Tagen, nach Zeichnungsfreigabe durch den Kunden, und Standardwerkzeuge in lediglich 24 Stunden zu liefern.
Da Horn die Prozesskette vom Pulver bis zur Beschichtung im eigenen Haus hat, bietet es sich an, die komplette Infrastruktur auch im Fall besonderer Aufgaben in Anspruch zu nehmen. Egal ob Rohlinge oder Fertigteile nach Kundenzeichnung, Horn ist der ideale Partner, wenn es um Hartmetallfälle einfacher oder kniffliger Art geht, was die eigenen Produkte von Horn sehr überzeugend dokumentieren.
Mehr Informationen zur Paul Horn GmbH
![]() |
Hartmetall-Werkzeugfabrik |
![]() |
Paul Horn GmbH |
![]() |
Horn-Straße 1 |
![]() |
72072 Tübingen |
![]() |
Telefon: 07071 7004-0 |
![]() |
Fax: 07071 7289-3 |
![]() |
E-Mail: info@de.horn-group.com |
![]() |
www.horn-group.com/de |
War dieser Artikel für Sie hilfreich?
![]() |
![]() |
![]() |
![]() |
![]() |
Bitte bewerten Sie diese Seite durch Klick auf die Symbole.
Zugriffe heute: 18 - gesamt: 8759.