IFB: Gefaltet und nicht verformt
Blechumformung der anderen Art
Leichtbau ist das Gebot der Stunde. Ob Auto oder Flugzeug – Ideen sind gefragt, wie diese Verkehrsmittel noch leichter werden können, um teuren Sprit zu sparen oder noch mehr Nutzlast zu befördern. Der menschliche Knochen zeigt, was diesbezüglich die Natur auf dem Kasten hat. Dr. Klett vom Institut für Flugzeugbau der Uni Stuttgart hat einen nicht minder interessanten Ansatz für den Leichtbau entdeckt: Technisches Origami.
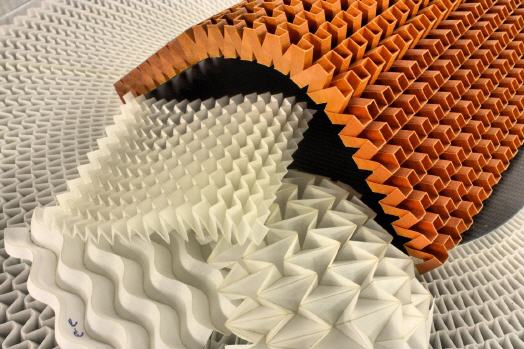
Vater des technischen Origamis ist Dr. Yves Klett
Sandwichbauweisen sind schon lange bekannt, um ein technisches Produkt leicht und doch stabil zu konstruieren. Das einfachste Beispiel ist die Wellpappe, die wohl schon jeder in der Hand gehabt hat. Hier wird zwischen zwei Deckschichten aus Pappe eine gewellte Pappbahn eingearbeitet, die durch die Wellenform große Kräfte aufnehmen kann und so das Material bestens qualifiziert, um damit stabile Kartons herzustellen. Diese sind ideal für den Umzug oder zum Transport von empfindlichen Fertigprodukten der Industrie geeignet. Das Geheimnis dieser Eigenschaft liegt in den kleinen Bögen der Wellpappe, die in der Lage sind, verhältnismäßig große Kräfte abzuleiten.
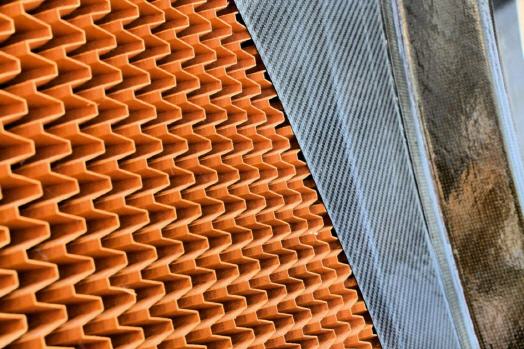
Besonders im Flugzeugbau punktet die Falttechnik
Altbekannte Eigenschaft
Wie gut sich kleine oder große Bögen eignen, teils riesige Lasten zu stemmen, ist sowohl den alten Römern, aber auch späteren Baumeistern nicht unbekannt gewesen, wie die heute noch stehenden Gebäude, Kirchen, Brücken und Aquädukte dokumentieren. Die seit Jahrtausenden bewährte Idee der Kraftableitung schickt sich nun an, in der modernen Technik Fuß zu fassen. Diesbezüglich forschen weltweit zahlreiche Institute, Universitäten und Unternehmen an neuen Lösungen, Leichtbau mit Stabilität zu kombinieren.
Insbesondere in der Luft- und Raumfahrt, aber auch im Schiffsbau sowie der Automobiltechnik sind stets Ideen willkommen, das Gewicht zu verringern, um den Kraftstoffverbrauch zu senken oder die Nutzlast zu erhöhen.Auch die Natur kennt das Prinzip, mit einfachen Formen großen Kräften standzuhalten. Dazu genügt der Gang auf die heimische Wiese. Hier sind beispielsweise das Wiesenschaumkraut und der Schachtelhalm anzutreffen, die beide einen hohlen Stängel haben, der von Querstreben stabilisiert wird.
Eine ganz besondere Idee zur Gewichtsreduzierung wurde an der Universität Stuttgart geboren. Dort hat sich Dr. Yves Klett aufgemacht, einen hochstabilen Sandwichkern durch simples Falten von Platten aus dünnem Metallblech, Kunststoff oder gar Papier herzustellen. Im Jahre 2003 wurde mit der Forschung begonnen, hinter der verblüffenderweise die Idee des Origami steckt. Origami wird hauptsächlich in Fernost ausgeübt und dort zu einer staunenswerten Kunst entwickelt, mit der es möglich ist, aus lediglich einem Blatt Papier etwa einen Kranich zu falten.
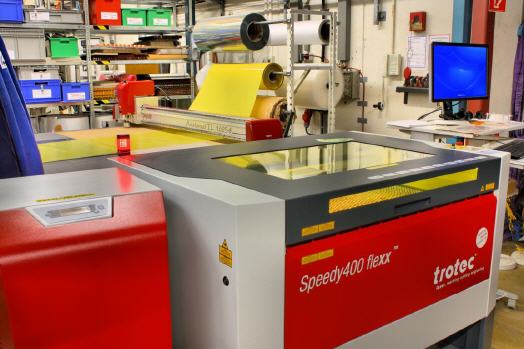
Die Faltlinien werden per Laser eingebracht
Revolution in Sachen Leichtbau
Auch in Stuttgart werden optisch und technisch ansprechende Kunstwerke erschaffen, die in naher Zukunft den Leichtbau revolutionieren sollen. Allerdings kommt hier modernste Technik zum Einsatz, um etwa den Sandwichkern für Flugzeug- oder Automobilteile zu falten. Dr. Klett hat über zehn Jahre daran gearbeitet, aus simplen Blechtafeln eine hochkomplexe Struktur herauszuarbeiten, die in der Lage ist, höchste Kräfte aufzunehmen. Die von ihm ersonnenen Computerprogramme sind mit derart raffinierten Formeln bestückt, dass sich sogar Teile falten lassen, die nach Fertigstellung automatisch die Form eines Rohrs annehmen.
Die Anwendung der Falttechnik hat viele Vorteile: Die so hergestellten Produkte sind sehr preisgünstig und besitzen, im Gegensatz zu Wabenmustern, eine offene Struktur. Dies bedeutet, dass durch solcherart produzierte Sandwichkerne problemlos elektrische Kabel verlegt werden können. Auch die Zufuhr von Frischluft ist durch die Struktur der gefalteten Kerne unkompliziert möglich. Auf diese Weise werden typische Probleme von Sandwichplatten mit Wabenmustern vermieden, die geschlossen sind und daher durch die Möglichkeit der Kondenswasserbildung schon einmal von Schimmel befallen werden. Es ist daher kein Wunder, dass insbesondere die Luftfahrtindustrie großes Interesse an der Innovation aus Stuttgart hat.
Ein weiterer Pluspunkt der Falttechnik ist der nur geringe Energieeinsatz für jeden Arbeitsgang. Auch Sportgerätehersteller sollten sich das Produkt einmal näher ansehen. Können mit dieser Technik doch beispielsweise Ski oder Snowboards wesentlich leichter und dennoch ohne Kompromisse bezüglich der Stabilität konstruiert werden. Dabei kommt dem Konstrukteur zugute, dass beim Falten keine Verformung stattfindet, da hier ein isometrischer Prozess stattfindet. Dies bedeutet, dass Längen sich nicht verändern, mithin keine Dehnung oder Streckung stattfindet, wie dies bei herkömmlicher Blechumformung der Fall ist. Zudem ist der Konstrukteur nicht an bestimmte Materialkombinationen gebunden. Holz ist ebenso möglich, wie Aluminium oder Kunststoff. Möglich ist, was Sinn macht und vom Kunden bezahlt wird.
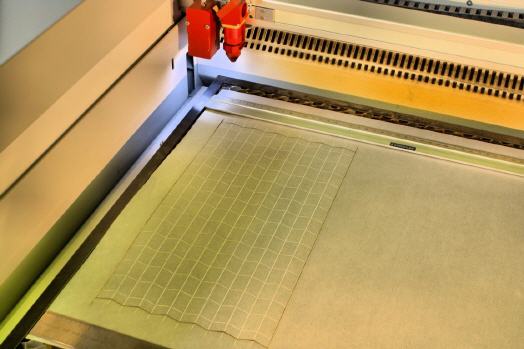
In wenigen Sekunden ist das Faltmuster aufgebracht
Pfiffige Idee
Für die eigentliche Herstellung eines gefalteten Wabenkerns hat sich Dr. Klett raffinierte Methoden einfallen lassen: Für das Einbringen der Faltlinien in dünnes Blech oder in einen Papierbogen wird eine Laseranlage verwendet, deren Laserleistung an das zu bearbeitende Material optimal anpassbar ist. Dies ist nötig, da ja nur ein „Anritzen“ der Oberfläche gewünscht ist und das Teil nicht durchgeschnitten werden soll.
Gilt es, dickere Papiere oder Metallbleche zu verarbeiten, so kommt ein großer, speziell ausgerüsteter Plotter zum Einsatz, der mit seinen Werkzeugen die passenden Biegelinien in das Material einprägt. Diese Technik bewirkt, dass das für den Sandwichkern benötigte Material mechanisch nicht beschädigt wird und dadurch die ursprünglichen Eigenschaften erhalten bleiben.
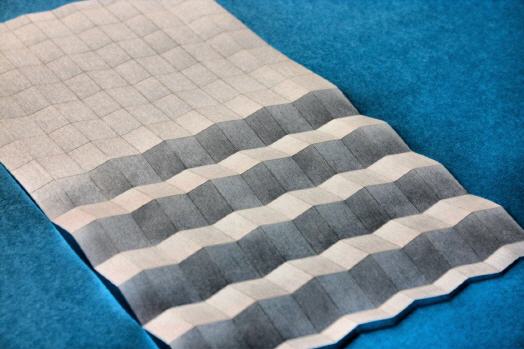
Von Hand wird das Papier gefaltet und geformt
Werkzeuge für Komplexes
Egal ob Laser oder Plotter, nach dem Einbringen der Biegelinien ist in beiden Fällen Handarbeit angesagt, um das so präparierte Material in die gewünschte Kernform zu bekommen. Wird eine bestimmte Komplexität des Musters überschritten, so kommt das menschliche Geschick an Grenzen. In diesem Fall müssen Werkzeuge ersonnen werden, die den Faltvorgang übernehmen. Auch diesbezüglich hat das Falt-Team aus Stuttgart bereits Lösungen erarbeitet. Es hat interessante Methoden zur Praxisreife geführt, um bestimmte Faltmuster maschinell im Serienmaßstab zu produzieren.
Dies ist besonders für Automobilproduzenten von Interesse, um ausgewählte Bauteile besonders leicht und stabil zu machen, ohne gleich auf das teure Material ›CFK‹ zurückzugreifen.Das Falten hat eine große Zukunft, da mit dieser Technik Produkte denkbar sind, die heute noch aus Vollmaterial oder aus verformten Blechen hergestellt werden.
Es lohnt sich, das eigene Produktspektrum diesbezüglich in Augenschein zu nehmen und bei passenden Kandidaten einfach einmal mit der Universität Stuttgart Kontakt aufzunehmen. Dort erfährt man, dass nicht nur der Leichtbau von dieser Technik profitiert, sondern auch Bereiche, die auf den ersten Blick nicht für das Falten in Betracht kommen.
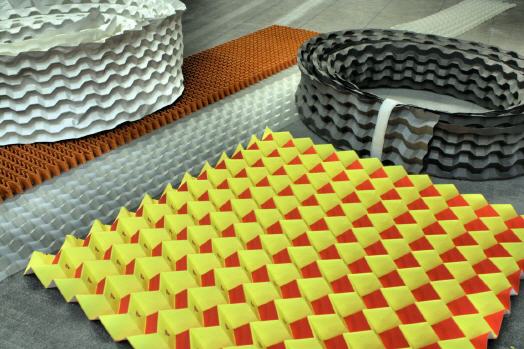
Sogar das Falten von Endlosband ist möglich
Mehr Informationen:
![]() |
IFB Institut für Flugzeugbau |
![]() |
Universität Stuttgart |
![]() |
Dr.-Ing. Yves Klett |
![]() |
Pfaffenwaldring 31 |
![]() |
70569 Stuttgart (Vaihingen) |
![]() |
Tel.: +49-711-685-62409 |
![]() |
Fax: +49-711-685-62449 |
![]() |
E-Mail: klett@ifb.uni-stuttgart.de |
![]() |
www.ifb.uni-stuttgart.de |
War dieser Artikel für Sie hilfreich?
![]() |
![]() |
![]() |
![]() |
![]() |
Bitte bewerten Sie diese Seite durch Klick auf die Symbole.
Zugriffe heute: 16 - gesamt: 1420.