IFAM: Per Siebdrucktechnik zum 3D-Teil
Innovativer 3D-Druck lässt staunen
Um Teile auf additive Art herzustellen, stehen verschiedene Verfahren zur Verfügung. Geht es beispielsweise um belastbare Teile aus Metall, werden diese häufig aus Metallpulver hergestellt, die von einem Lasterstrahl miteinander verschmolzen werden. Insbesondere für kleine Teile mit winzigen Geometriemerkmalen hat das Fraunhofer-Institut für Fertigungstechnik und Angewandte Materialforschung ›IFAM‹ eine echte Alternative ersonnen: das 3D-Metall-Drucken.
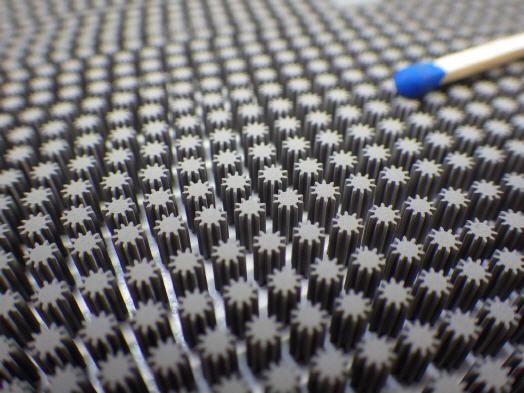
Das MIM-Verfahren hat sich für die Produktion winziger Metallteile mit anspruchsvoller Geometrie bewährt. Hier wird eine mit Metallpulver angereicherte Paste in eine Spritzgussform unter hohem Druck eingebracht und auf diese Weise feste Metallteile gewonnen, die nach dem Sintern ihre Gebrauchsfestigkeit erhalten.Forscher des Fraunhofer-Instituts IFAM haben diese Idee aufgegriffen und weiterentwickelt.
Auf der Grundlage der im Druckgewerbe heimischen Siebdrucktechnik haben sie eine staunenswerte Technik ersonnen, die es erlaubt, schichtweise filigranste Strukturen aufzubauen, wie sie in der Filtertechnik, in Wärmetauschern aber auch in der Medizin- sowie der Messtechnik benötigt werden. Es lohnt sich daher für viele Unternehmen, einen Blick auf dieses Verfahren zu werfen, um die Eignung für eigene Zwecke zu ergründen.
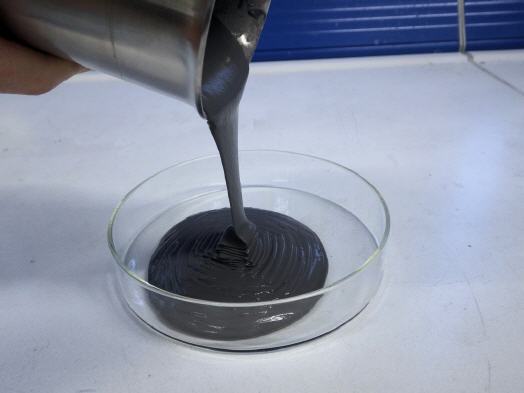
Ideal für Einfaches
Mit dem 3D-Metall-Drucken ist es zwar nicht ohne Weiteres möglich, aufwendige 3D-Konturen zu erzeugen, deren Kontur sich mit der Dicke ändert, doch für Strukturen, die mit zunehmender Höhe gleich bleiben ist das Verfahren bestens geeignet. Es ist nicht nötig, eine Spritzgussform herzustellen. Vielmehr wird die Kontur in 2D via CAD-System erzeugt, in entsprechender Zahl auf die Fläche kopiert und aus den Daten ein Film belichtet, der von einem spezialisierten Dienstleister schlussendlich dazu dient, ein Sieb herzustellen, das für den 3D-Metall-Druck verwendet wird.
Für diesen Zweck wird auf einen Aluminiumrahmen ein dünnes Niro-Stahlgewebe unter Spannung aufgezogen und mit einer fotoempfindlichen Schicht beschichtet. Nach dem Belichten wird das Gewebe mit einem Lösemittel gereinigt, woraufhin sich an der nicht belichteten Stelle der Lack ablöst und das feinmaschige Metallgewebe freigelegt wird.
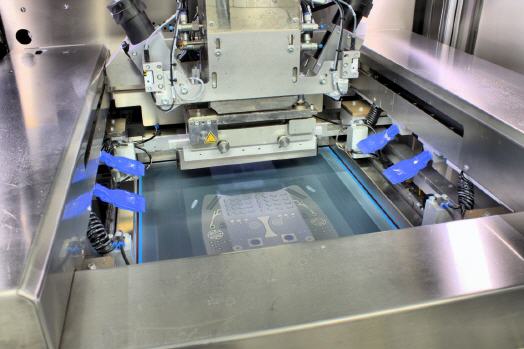
Paste mit Know-how
Das Geheimnis der Funktionsfähigkeit des Verfahrens liegt in genau diesem Gewebe, dessen Fadenstärke zwischen 18 und 50 Mikrometer beträgt, während die Öffnungen circa 50 bis 200 Mikrometer groß sind. Die Größe der Metallkörner ist diesen Maßen angepasst, sodass sie problemlos durch die Öffnungen passen. Zudem ist die Konsistenz der Paste so formuliert, dass diese bei jedem Auftragen auf eine neue Schicht sicher haftet, jedoch nicht an den Rändern des bereits aufgebauten Teils herunterfließt und auch nicht am Gewebe klebt, was bei dessen Rückzug am beschichteten Teil sichtbar wäre.
Wie im Druckgewerbe wird das Gewebe unter Spannung auf das Substrat – in diesem Fall besteht es aus Keramik – aufgedrückt und die Paste mit einem Kunststoffschieber unter Druck über die Folie verteilt. Wo das Gewebe offen ist, wird in diesem Prozess Material abgelagert. Ist die gesamte Fläche bestrichen, wird die Folie angehoben und das Trägermaterial mit der eben aufgebrachten Pastenschicht aus dem Arbeitsbereich in einen Ofenbereich gefahren, wo die Schicht etwa 20 Sekunden getrocknet wird. Nach dem erneuten Einfahren in den Arbeitsbereich wiederholt sich der Zyklus so lange, bis die gewünschte Teilehöhe erreicht ist.
Bemerkenswert ist, dass durch einfaches Wechseln des Drucksiebes problemlos geschlossene Hohlkörper produziert werden können.
Auf diese Weise sind beispielsweise Wärmetauscher herstellbar, deren Struktur im Inneren so geformt werden kann, dass eine möglichst große Oberfläche erzeugt wird, um den Wirkungsgrad des Wärmetauschers optimal zu gestalten. Damit ein Siebwechsel keinen Einfluss auf die Genauigkeit der aufzubauenden Teile hat, ermittelt eine automatische Messvorrichtung die exakte Lage des Siebs und korrigiert, wenn nötig, den Schlitten.Staunenswert auch die Wirtschaftlichkeit des Verfahrens. Unter Zugrundelegung einer Gesamtproduktionszeit von 30 Sekunden pro Schicht ist ein drei Millimeter hohes Teil bei einer Schichtdicke von 15 Mikrometer nach circa 100 Minuten fertig.
Ist das Teil entsprechend klein, so sind in dieser Zeit hunderte oder tausende Teile gleichzeitig produziert worden. Wem dies noch zu wenig ist, kann sich von Ekra Automatisierungssysteme GmbH eine Anlage produzieren lassen, die nach dem Rundtaktprinzip arbeitet, weshalb der Trockenvorgang hauptzeitparallel geschieht, somit der Beschichtungsvorgang ohne Wartezeit erfolgt.
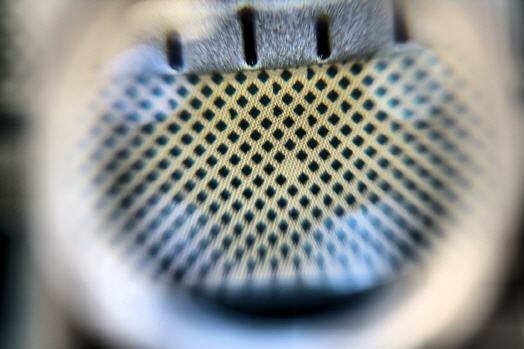
Für alle Metalle
Interessant ist, dass es nahezu keine Einschränkungen bezüglich der mit diesem Verfahren zu verwendete Metalle gibt, da grundsätzlich alle Eisen- und Nichteisenmetalle verwendet werden können, die in Pulverform beschaffbar sind.
Nachdem die Teile aufgebaut sind, sind diese empfindlich gegen Krafteinwirkung. Sie müssen daher per Sintern auf Gebrauchsfestigkeit gebracht werden. In diesem Prozess kommen Temperaturen im Bereich von 80 Prozent der Schmelztemperatur des jeweiligen Metalls zur Anwendung. Zwar ist beim Sintern ein Schwund von etwa 15 Prozent zu veranschlagen, doch kann dies bereits bei der Konstruktion des Teils berücksichtig werden, womit es möglich wird, dass das Endprodukt die gewünschten Maße erhält.
Anzumerken ist, dass die vom IFAM ersonnene 3D-Metall-Drucktechnik ungeschlagen ist, wenn es um das Erzeugen filigranster Konturen geht. Der Grund liegt in der Verwendung feinster Pulver, deren Körnerdurchmesser 10 bis 15 Mikrometer beträgt.
Diese kleinen Körnchen sind momentan mit der Lasertechnik nicht verarbeitbar. Die Konturen von lasergeschmolzenen Teilen sind daher weniger filigran, weil gröberes Pulver verwendet werden muss. Der Mittenrauwert Ra der Teileoberfläche beträgt circa zwei Mikrometer, was für viele Zwecke völlig ausreichend ist.
Es gibt noch viele Ideen, die in dieses Projekt einfließen werden. So planen die Fraunhofer-Experten, in einer späteren Ausbaustufe eine optische Kontrolle zu implementieren, die jede aufgetragene Schicht kontrollieren kann, um fehlerhafte Teile zu verlässig zu erfassen. Bereits jetzt überzeugt das Anlagenkonzept und wartet auf Chancen, sich zu beweisen. Es wird sich lohnen, diesbezüglich das IFAM zu kontaktieren.
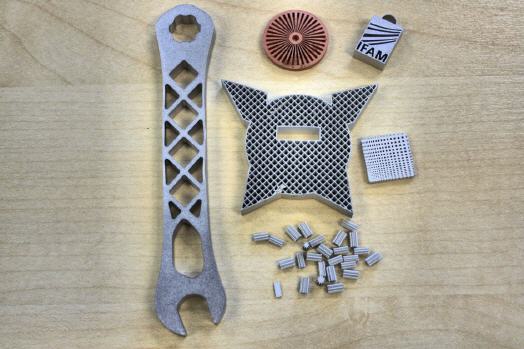
Download:
Diesen Artikel können Sie hier im PDF-Format herunterladen [223 KB] .
Mehr Informationen:
![]() |
Fraunhofer-Institut für Fertigungstechnik |
![]() |
und Angewandte Materialforschung IFAM |
![]() |
Winterbergstraße 28 |
![]() |
01277 Dresden |
![]() |
Tel.: 0351 2537-300 |
![]() |
Fax: 0351 2537-399 |
![]() |
E-Mail: info@ifam.fraunhofer.de |
![]() |
www.ifam.fraunhofer.de |
War dieser Artikel für Sie hilfreich?
![]() |
![]() |
![]() |
![]() |
![]() |
Bitte bewerten Sie diese Seite durch Klick auf die Symbole.
Zugriffe heute: 17 - gesamt: 11443.