Wandöl ist ab sofort Geschichte
Revolution mit dem ›Jetsleeve 2.0‹
Seit seiner Markteinführung im Jahre 2008 hat sich der Jetsleeve von Diebold als echter Problemlöser überall dort beliebt gemacht, wo es galt, tiefe Kavitäten zu fräsen oder exotisches Material mit kleinsten Fräsern zu bearbeiten. Abgebrochene Fräser wegen klemmender Späne wurden Geschichte und drastisch verbesserte Standzeiten zum Normalfall. Mit dem Jetsleeve 2.0 steht nun ein Nachfolger mit noch besseren Fähigkeiten parat, der zudem dank seiner Konstruktion das lästige Wandöl vermeidet.
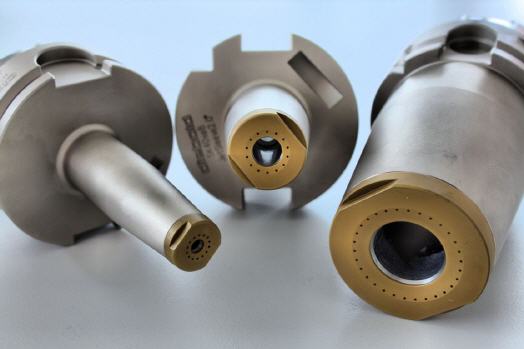
Jetsleeve-Varianten:
Jetsleeve-Schrumpffutter gibt es in verschiedenen Ausführungen. Auf diese Weise lassen sich viele Bearbeitungsprobleme fallweise und sachgerecht lösen.
Innovationen werden nicht durch Regierungsanweisungen geboren, sondern erblicken dann das Licht der Welt, wenn der Markt danach verlangt oder sich Erfinder von ihrer Idee einen satten Gewinn erhoffen. Die freie Marktwirtschaft garantiert, dass Innovationen in großer Zahl ersonnen werden, die als Gesamtheit eine ganze Branche nach vorne bringen. So geschehen im Jahre 2008, als der Jetsleeve von Diebold zum ersten Mal das Licht der Fertigungswelt erblickte. Seither können Werkzeug- und Formenbauer sich über das problemlose Zerspanen tiefer Kavitäten und über wesentlich höhere Standzeiten ihrer Fräswerkzeuge freuen.
In der Folge der neuen Möglichkeiten purzelten die Stückkosten, minimierte sich der Kühlmittelbedarf und wurden exotische Materialien plötzlich wesentlich leichter zerspanbar. Mit Fug und Recht kann gesagt werden, dass der Jetsleeve einen nicht unerheblichen Anteil daran hat, dass zahlreiche europäische Werkzeug- und Formenbauer ihre Wettbewerbsfähigkeit gegenüber fernöstlicher Konkurrenz trotz nicht unerheblichem Lohngefälle behaupten konnten. Der Einsatz des Jetsleeve hat zudem dazu geführt, dass durch den Einsatz von Minimalmengenschmierung die Luft in den Fertigungshallen nicht mehr in gleicher Weise mit Ölnebel geschwängert wird, wie es bei Überflutungskühlung der Fall ist.
Ein Fakt, der insbesondere den dort beschäftigten Facharbeitern gesundheitlich zugutekommt. Die geringere Menge anhaftendes Restöls macht sich natürlich auch in der Reinigungszeit der produzierten Teile bemerkbar. Zudem erhöht sich durch dir geringere Menge eingeschleppten Öls die Standzeit des Reinigungsmittels in den Reinigungsanlagen, sodass auch hier sehenswerte Einsparungen gegeben sind. Somit ist es nicht vermessen, den Jetsleeve als „Grünes Produkt“ zu betrachten. Dessen Einsatz im MMS-Bereich hat seit 2008 ungezählte Tonnen Schmier- und Reinigungsmittel eingespart, die folglich auch nicht entsorgt werden mussten.
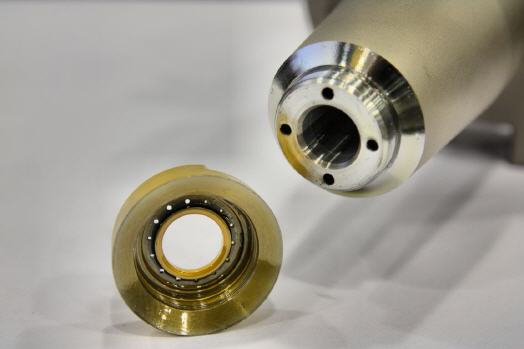
Clever:
Über innenliegende Bohrungen strömt das Kühl- beziehungsweise Schmiermedium in die Ringnut der Düsenkappe, von wo es über kleine Düsenbohrungen direkt auf die Schneide des Fräsers gelenkt wird.
Großer Fortschritt
Neue Fertigungsherausforderungen sind auch für die Werkzeugmaschinenbauer Ansporn zu Innovationen. Seit 2008 hat sich hier viel getan. Was früher als ›Eilgang‹ bezeichnet wurde, ist heute eine Vorschubgeschwindigkeit. Waren damals nur wenige bar Kühlmitteldruck üblich, spritzt der Kühlschmierstoff heute mit bis zu 120 bar aus der Düse. Die Maschinen wurden im Laufe der Zeit immer agiler und leistungsstärker, um die Möglichkeiten der neu entwickelten Schneidstoffe auszureizen, beziehungsweise trotz steigender Löhne und Abgaben die Stückkosten im Zaum zu halten.
Dieser Entwicklung musste sich auch der Jetsleeve stellen, der im MMS- und im KSS-Bereich nutzbar ist. Es zeigte sich, dass die zuvor verwendete Aluminiumhülse den starken Kühlmitteldrücken nicht gewachsen war. War der Jetsleeve auf Anlagen mit wenig Kühlmitteldruck jahrelang problemlos im Einsatz, so wurde nun mit steigenden KSS-Drücken eine Schwachstelle offenbar: Die winzigen Austrittsbohrungen an der Stirnseite wurden regelrecht ausgewaschen. In der Folge vergrößerten sich die Bohrungen, wodurch sich auch der Bohrungswinkel änderte. Das Resultat war, dass der Mediumstrahl nicht mehr exakt die Schneide an der vorbestimmten Höhe traf.
Durch immer höher drehende Frässpindeln wurde zudem ein weiteres Problem erkennbar: die Bildung von Wandöl. Hohe Drehzahlen führten beim alten Jetsleeve dazu, dass sich das Kühlschmiermedium wie in einer Zentrifuge im Inneren der Aluminiumhülse ansammelte. In der Folge war die Schmierung nicht mehr zuverlässig mit der eingestellten Ölmenge sichergestellt. In der Ruhestellung der Spindel kam es zudem zu einem Abfluss des an der Hülseninnenwand anhaftenden Öls, das sich nun am Hülsenboden sammelte. Sobald nun die Spindel wieder startete und der Druckluftstrom einsetzte, wurde diese Ölmenge komplett ins Freie geblasen, was an einer „Nebelwolke“ sichtbar wurde.
Die Diebold-Konstrukteure mussten daher den Jetsleeve an die Fähigkeiten neuer Werkzeugmaschinen anpassen. Herausgekommen ist der Jetsleeve 2.0, der optimal mit modernen Werkzeugmaschinen harmoniert. Der neue Jetsleeve – ein Schrumpffutter mit innovativer Schmiermediumführung – wurde komplett überarbeitet. So wird beispielsweise kein Aluminium mehr verwendet. Vielmehr besteht der Düsenring des neuen Jetsleeve aus Warmarbeitsstahl, der zusätzlich TiN-Beschichtet ist.
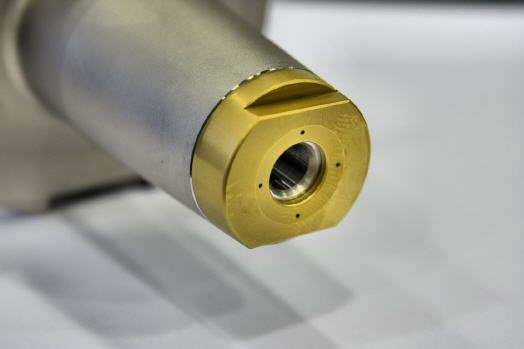
Praxisgerecht:
Speziell für den Einsatz in der Minimalmengenschmierung haben die Experten von Diebold eine Jetsleeve-Variante im Portfolio, die verhindert, dass sich das Öl bei hohen Drehzahlen an der Bohrungswand durch den Fliehkrafteffekt ansammelt.
Für höchste Drücke geeignet
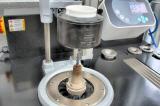
Einfache Handhabung:
Jetsleeve-Schrumpffutter werden unterschiedlos zu anderen Schrumpffuttern identisch gehandhabt.
Resultat ist eine besondere Robustheit und Widerstandsfähigkeit. Dies zeigt sich nicht zuletzt in den Bohrungen des Düsenrings, die nun laut Diebold selbst mit höchsten KSS-Drücken zurechtkommen. Eine weitere Besonderheit ist der komplett andere Aufbau des Jetsleeve. Die Alu-Hülse wich dem bereits erwähnten Düsenring, wodurch nun auch das Einschrumpfen der Fräser wesentlich vereinfacht wurde. Musste beim alten Jetsleeve noch die Alu-Hülse zum Aufbau des Induktionsfeldes entfernt werden, so kann dank des Düsenrings aus Stahl der Ein- oder Ausschrumpfvorgang unmittelbar gestartet werden.
Das Kühlschmiermedium strömt nun nicht mehr durch eine Hülse, sondern direkt in eine kleine Kammer zwischen Schrumpffutter und Düsenring, von wo es durch die kleinen Bohrungen des Düsenrings austritt. Diese Bohrungen sind übrigens in einem der Fräserlänge angepassten Winkel eingebracht, damit das Medium an einer genau definierten Stelle auf die Fräserschneide trifft. Für die zuverlässige MMS-Schmierung mit bis zu 50 000 U/min musste noch tiefer in die Trickkiste gegriffen werden. Hier sind lediglich vier Bohrungen im Düsenring eingebracht. Diese wurden jedoch derart exakt positioniert, dass die Bohrung des Düsenrings perfekt über der Bohrung des Schrumpffutters liegt.
Auf diese Weise funktioniert eine MMS-Schmierung selbst bei höchsten Drehzahlen. Damit die Versorgung mit der eingestellten Menge Medium sichergestellt ist, wurde darauf geachtet, dass sich der Querschnitt der durch den Mediumverteiler verlaufenden Kanäle nicht ändert. Resultat ist, dass sogenanntes „Wandöl“ nicht mehr auftreten kann.

Mehr Informationen zu Diebold:
![]() |
Diebold Goldring Werkzeuge GmbH & Co. |
![]() |
An der Sägmühle 4 |
![]() |
72417 Jungingen |
![]() |
Telefon 07477 871-0 |
![]() |
Fax 07477 871-30 |
![]() |
E-Mail: kontakt@hsk.com |
![]() |
www.hsk.com |
War dieser Artikel für Sie hilfreich?
![]() |
![]() |
![]() |
![]() |
![]() |
Bitte bewerten Sie diese Seite durch Klick auf die Symbole.
Zugriffe heute: 38 - gesamt: 14749.