Bass: Stilvolle Top-Gewindewerkzeuge
Edle Spitzentechnik für Zerspaner
Auf den ersten Blick unterscheiden sich Gewindewerkzeuge verschiedener Hersteller nicht wesentlich voneinander – gleiche Gewinde vorausgesetzt. Die Unterschiede werden auch auf den zweiten Blick nur schwer erkennbar, da sich diese hauptsächlich durch die Vergütung, die Geometrie und die Oberflächenpräparation zeigen. Diesbezüglich hat das Unternehmen Bass Spitzenqualität zu bieten.
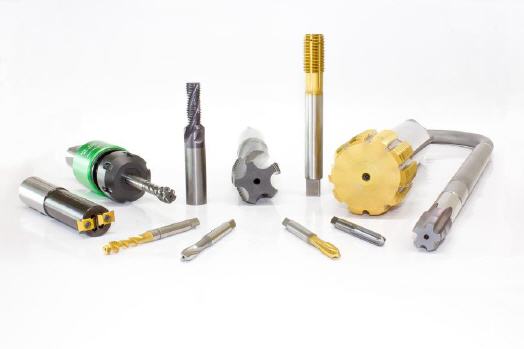
Gewindebohrer, -fräser und -furcher von Bass
Die Produzenten von Gewindewerkzeugen haben eine besondere Verantwortung: Ihre Produkte kommen in der Regel erst ganz am Ende der Wertschöpfungskette zum Einsatz, wenn aus einem Stück Halbzeug ein fast fertiges Präzisionsbauteil entstanden ist, dessen Wert durch die Arbeitskosten nicht selten einen fünfstelligen Bereich erklimmt. Zu diesem Zeitpunkt müssen alle Prozesse absolut sicher funktionieren, soll in dieser späten Phase nicht teurer Edelschrott beispielsweise durch abbrechende Gewindebohrer oder nicht maßhaltige Gewinde entstehen.
Für das Einbringen von Gewinden in teure Bauteile setzen daher mit spitzem Bleistift rechnende Fertigungsleiter ausschließlich auf absolute Spitzenqualität beim Einkauf der dafür vorgesehenen Gewindebohrer. „Billig“ hat hier absolut nichts zu suchen, will man teure Schäden vermeiden.
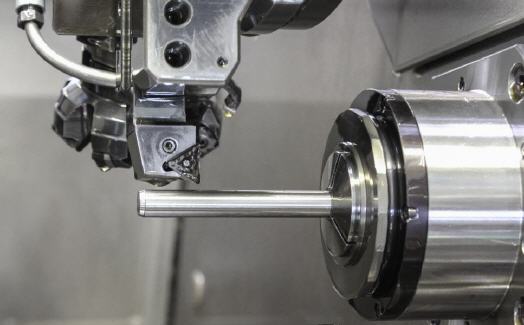
Vorbearbeitung der Gewindebohrerrohlinge
Trumpfen mit Qualität
Diesbezüglich eine absolute Top-Adresse ist das Unternehmen Bass, das die komplette Produktionskette der Gewindebohrerfertigung im Haus hat. Zusammen mit einer 100-Prozent-Prüfung garantiert dies, dass der Anwender ausschließlich Top-Qualität erwirbt, die für maßhaltige Gewinde sorgt. Egal ob Gewindebohrer, Gewindefurcher oder Gewindefräser, das Unternehmen liefert Produkte für alle genormten und nicht genormten Gewinde, die in der Feinmechanik ebenso eingesetzt werden wie im Maschinenbau oder der Luft- und Raumfahrttechnik.
Dafür verwendet das innovative Unternehmen pulvermetallurgisch hergestellte Schnellarbeitsstähle und Hartmetalle. Das pulverförmige Grundmaterial wird beispielsweise durch Verdüsen flüssiger Stähle gewonnen und besitzt eine Korngröße von unter zehn Mikrometer.
Der aus diesem Pulver gewonnene Stahl hat ein ausgesprochen homogenes Gefüge mit einer Vielzahl von vorteilhaften Eigenschaften.Dies stellt sicher, dass daraus hergestellte Zerspanungswerkzeuge keine „Achillesferse“ besitzen, an denen ein stärkerer Verschleiß als anderswo an der Schneide des Werkzeugs auftritt.
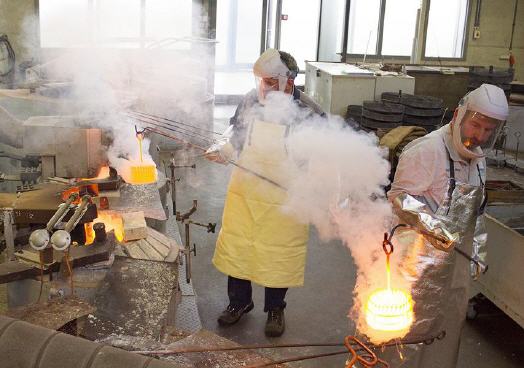
Zum Härten sind mehrere Salzbäder im Einsatz
Vorteil mit Pulver
Das Pulver wird unter Druck und Hitze zu einem absolut homogenen Gefüge mit einer extrem feinen Struktur verbunden. Metallpulver jeder Art kann so problemlos zu einem kompakten und festen Körper verpresst werden, der im Gegensatz zu erschmolzenem Material weniger Spannungen kennt. Zwar verfügt der Rohling immer noch über winzige Hohlräume, die via Sintern sich jedoch nahezu vollständig schließen, da das zusammengepresste Material in diesem Prozess schrumpft.
Überhaupt ist die Pulvermetallurgie eine höchst interessante Wissenschaft. Diese aus Pulver geschaffenen Stähle warten mit überragenden Eigenschaften bezüglich Schnitthaltigkeit und Warmfestigkeit auf. Das Herstellen von Werkzeugen und Werkstücken aus Metallpulver ist schon lange bekannt und auch bei Wendeschneidplatten und sogenannten MIM-Teilen gängige Praxis.
Im modernen Maschinenpark von Bass erhalten die PM-Rohlinge per Zerspanen ihre Grundkontur. Dafür sind Maschinen renommierter Maschinenbauer im Einsatz. Diese sorgen dafür, dass das 1947 gegründete Unternehmen stets lieferbereit bleibt.
Ebenso wie die aus herkömmlichen Werkzeugstählen gefertigten Gewindebohrer werden pulvermetallurgisch hergestellte Gewindebohrer wärmebehandelt. Das sogenannte ›Härten‹ ist für Gewindebohrer ein wichtiger Schritt, damit diese Werkzeuge eine sehr hohe Standzeit bekommen und nicht schon nach wenigen Gewinden ausgetauscht werden müssen. Für diesen Zweck hat Bass eine hochmoderne Salzbadanlage in Betrieb.
Das Salzbadhärten hat den großen Vorteil, dass die von flüssigem Salz umspülten Rohlinge gleichmäßig und ohne Sauerstoffoxidation auf eine Härtetemperatur von bis zu 1.200 Grad Celsius erwärmt werden können. Nachdem diese Temperatur erreicht ist, werden die paketweise in das Salzbad eingetauchten Gewindebohrer in einem weiteren Salzbad abgeschreckt und die restliche Temperatur anschließend unmittelbar an der Luft über mehrere Minuten hinweg abgebaut. Auf diese schonende Weise werden Verzug oder Härterisse vermieden. Insgesamt fünf Bäder hat das Unternehmen Bass im Einsatz, die für eine absolut gleichmäßige Qualität aller von Bass gefertigten Gewindewerkzeuge sorgen.
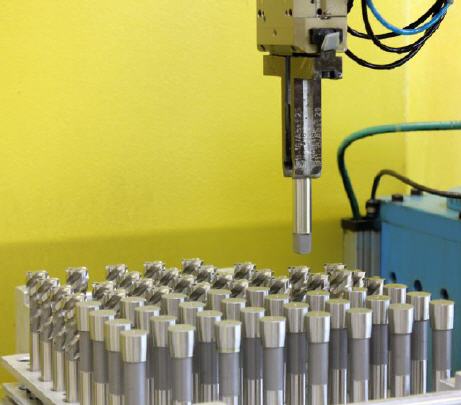
Vollautomatisch Schleifen mit Roboterbestückung
Moderne Schleiftechnik
Nach dem Härten treten die Gewindebohrer den Gang zum Schleifen an, wo sie für ihre eigentliche Aufgabe ertüchtigt werden. Es gibt keine Kontur, die die hochmodernen Schleifmaschinen nicht in die Rohlinge zaubern können. Wer sich beispielsweise einen Gewindefurcher von Bass einmal näher ansieht, dem fällt das interessante Profil auf.
Waren solche Werkzeuge früher eher wie eine Schraube geformt, kann ein Bass-Gewindefurcher heute mit mehreren Nuten versehen sein. Dies dient einer besseren Zuführung des Kühlschmierstoffs an die Bearbeitungsstelle. Das Ergebnis dieser Maßnahmen zeigt sich beim Gewindefurchen durch absolut maßhaltige Gewinde mit hoher Festigkeit, da das Material umgeformt und dabei verdichtet, jedoch nicht zerspant wird.
Roboter in der Maschine sorgen dafür, dass der Schleifprozess autonom stattfinden kann. Erst nachdem eine ganze Charge geschliffen ist, meldet die Maschine per Lichtsignal die Abarbeitung des Auftrags und ein Bediener sorgt für Nachschub an Rohlingen beziehungsweise veranlasst den Weitertransport der geschliffenen Gewindewerkzeuge zum Kennzeichnen des Schaftes.
Doch damit ist noch lange nicht Schluss. Je nach Modell bekommen die fertig geschliffenen Gewindebohrer noch eine Beschichtung. Das passiert allerdings bei einem Dienstleister, der zusammen mit Bass eine Schicht mit besonderen Eigenschaften ersonnen hat, die speziell auf die Anforderungen bei der Gewindebearbeitung zugeschnitten wurde. Interessant auch die umweltfreundliche Entsorgung des Schleifschlamms: Dieser wird via Pipeline zusammen mit dem Kühlschmierstoff direkt aus den einzelnen Maschinen gesaugt und in einer Aufbereitungsanlage von Kühlschmierstoff befreit und anschließend zu Briketts gepresst, was eine Verringerung des Feuchtegrades auf nur noch 12 Prozent zur Folge hat. Auf diese Weise werden wertvolle Ressourcen optimal geschont und Restmaterialien einer geldwerten Verwertung zugeführt.
In diesem hocheffizienten Prozess erblicken hochwertige Werkzeuge rund um die Herstellung von Gewinden das Licht der Fertigungswelt. Das Know-how von Bass ist beeindruckend: Es wurden schon Sonderlösungen für das kontinuierliche Fertigen von Muttern ersonnen, die nach Fertigstellung durch die Maschinenspindel hindurch in ein Behältnis geleitet werden. Aber auch hier gilt, dass Top-Qualität zunächst seinen Preis hat, der Kauf sich jedoch spätestens bei der Betrachtung der günstigeren Kosten pro Gewinde als Schnäppchen herausstellt. Ein Angebot also, an dem man nicht vorbeigehen sollte.
Mehr Informationen:
![]() |
BASS GmbH & Co. KG |
![]() |
Technik für Gewinde |
![]() |
Bass-Strasse 1 |
![]() |
97996 Niederstetten |
![]() |
Tel.: +49 7932 - 892-0 |
![]() |
Fax: +49 7932 - 892-87 |
![]() |
E-Mail: info@bass-tools.de |
![]() |
www.bass-tools.com |
War dieser Artikel für Sie hilfreich?
![]() |
![]() |
![]() |
![]() |
![]() |
Bitte bewerten Sie diese Seite durch Klick auf die Symbole.
Zugriffe heute: 19 - gesamt: 13398.