Wertschöpfung per Automation
Pfiffige Ideen für den Mittelstand
Automatisierung ist Pflicht, soll das eigene Unternehmen an einem Hochlohnstandort langfristig konkurrenzfähig bleiben. Die besondere Herausforderung besteht darin, die zur Unternehmensgröße passenden Automatisierungslösungen zu finden. Eine fundierte Hilfestellung können die Experten des Technologiezentrums der Hochschule Landshut geben, die in ihrer Dingolfinger Lernfabrik insbesondere auf mittelständische Betriebe zugeschnittene Vorschläge unterbreiten können.
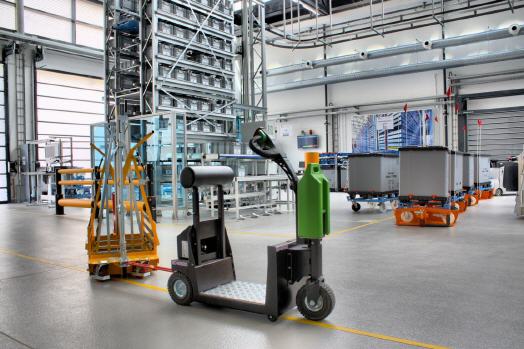
Die Notwendigkeit der Automatisierung in einer globalisierten Welt ist mittlerweile selbst in kleineren Unternehmen erkannt worden, wie etwa CNC-Maschinen dokumentieren, die von einem Roboter bestückt werden. Doch gilt es, weiterzudenken. Mit der Automatisierung des Zerspanungsprozesses ist in der Metallindustrie zwar ein wichtiger Anfang gemacht worden, doch erst dann, wenn vom Wareneingang bis zur Einlagerung und dem Versand eine Logistikkette installiert ist, die von möglichst wenigen Menschen überwacht und bedient wird, ist ein Optimum erreicht, um langfristig selbst gegen Fernost-Marktbegleiter konkurrenzfähig zu bleiben.Es ist verständlich, dass kritische Stimmen Roboter & Co. als Übel betrachten.
Doch wie sich in der Geschichte zeigt, hat Automatisierung stets zu menschlicheren und gut bezahlten Arbeitsplätzen geführt. Dies zeigte sich beispielsweise im Fall der Weber, die 1844 in Schlesien einen Aufstand wagten, weil sie durch die Einführung des lochkartengesteuerten Webautomaten um ihre Arbeitsplätze fürchteten. Doch ist das genaue Gegenteil eingetreten. Die Weber bekamen besser bezahlte Arbeit und konnten ihren Familien dadurch mehr Wohlstand bieten. Ganz abgesehen davon, dass nun gewebte Stoffe qualitativ besser und vor allem preiswerter wurden, sodass sich ab sofort nicht nur der Adel mit schöner Kleidung schmücken konnte.
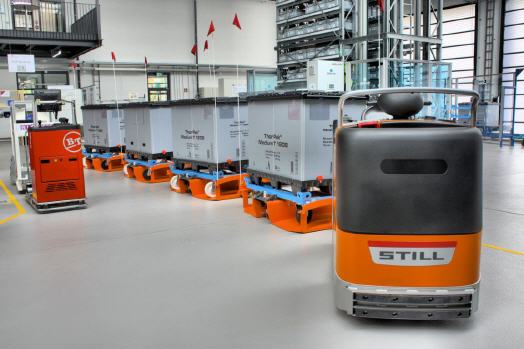
Mit Automation zum Wohlstand
Automatisierung führt letztlich zu einem gesellschaftlichen Gewinn, da damit Arbeitsplätze gesichert werden und mittelfristig zudem neue, besser bezahlte Berufe entstehen, da die Automaten nach höher qualifiziertem Personal für Bau, Überwachung und Wartung verlangen. Nicht zuletzt der demografische Faktor ist damit für Unternehmen beherrschbar, da eine zurückgehende Bevölkerungszahl beziehungsweise der künftig trotz Zuzug sich massiv ausbildende Facharbeitermangel keine existenzbedrohlichen Ausmaße annehmen kann.
Doch gilt es, die Weichen in Richtung Automatisierung jetzt zu stellen, da jedes Zuwarten die Chancen schmälert, weiterhin am Markt zu bestehen. Abgesehen vom sich künftig massiv herausbildenden Personalproblem mahnt die fortschreitende Globalisierung ein rasches Handeln an. Nur wer es schafft, eine flexible, automatisierte Fertigung aufzubauen, wird überleben.
Eine Top-Anlaufstelle um fit für die Zukunft zu werden ist das Dingolfinger Technologiezentrum der Hochschule Landshut. Dort ist eine Lernfabrik besuchbar, in der nicht nur Studenten ausgebildet werden, sondern die auch mittelständischen Unternehmen Orientierungshilfe bietet, wenn es darum geht, die eigene Fertigung auf Automatisierungs- und Verbesserungspotenziale in der Produktionslogistik abzuklopfen.
Unter der Leitung von Prof. Dr. Markus Schneider wurde in Dingolfing eine Musterfabrik errichtet, die Vorbildcharakter hat. Hier sind vom Wareneingang über die Fertigung bis zum Warenausgang alle Kettenglieder abgebildet, die dafür sorgen, die Durchlaufzeiten massiv zu senken und zudem einer abnehmenden, sowie alternden Facharbeiterschaft ergonomisch sinnvoll zur Hand gehen.Von der Anordnung der Lagerräume bis zum Ablauf des Produktionsprozesses stehen die Landshuter beziehungsweise Dingolfinger Experten mit Rat und Tat zur Seite.
Von 15 namhaften Unternehmen stammen die Exponate der Lernfabrik, in der der Lean-Gedanke allgegenwärtig ist. Lehre, Forschung und praktische Anwendung werden hier in ihrer ganzen Bandbreite abgedeckt. Dabei wird jedoch nicht jede Modeerscheinung in Sachen ›Automatisierung‹ kritiklos angepriesen. Ehe bestimmte Produkte oder Verfahren empfohlen werden, wird gerechnet und recherchiert. So kommt es, dass das Industrie 4.0-Ziel einer völlig menschenleeren Fabrik in den Bereich der Fabel verwiesen wird, da laut Professor Schneider der Mensch auch in einer automatisierten Umgebung unverzichtbar bleibt.
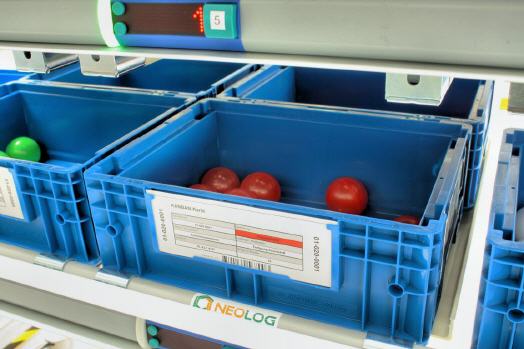
Automation gezielt anstreben
Ähnlich ist es mit dem Ziel, dass sich künftig das Rohmaterial den Weg durch die Fabrik selbst sucht und den Maschinen via RFID sagt, was an ihm zu machen ist. Das gewünschte Produkt würde nach dieser Idee ohne menschlichen Eingriff entstehen. Berechnungen und Simulationen zeigen jedoch, dass sich im Vergleich zur Lean-Produktion die Durchlaufzeiten erhöhen, die Produkte also teurer in der Herstellung werden.
In der Lernfabrik werden daher Wege verfolgt, die wirklich Sinn machen. Es gilt, praxisgerechte Verfahren zu erforschen und nach vorne bringen, um im harten Wettbewerb bestehen zu können. Daher wird beispielsweise das RFID-System mit dem Kanban-System gekoppelt. Mit dieser cleveren Idee wird sichergestellt, dass die richtigen Produkte garantiert in der richtigen Zeit an der richtigen Stelle lagern, somit zur richtigen Zeit die richtigen Produkte montiert werden können.
Wer das Kanban-System noch nicht kennt: Dies ist ein lagerbestandreduzierendes, rein papierenes Steuersystem, das ohne EDV auskommt. Herzstück sind Karteikarten, die wichtige Kenndaten, wie etwa Teilebezeichnung, Lagerort oder Stückzahl enthalten. Diese Karteikarte sorgt dafür, dass leere Kisten neu gefüllt und an den Bestimmungsort gebracht werden. Der Clou sind Stecktafeln, in die die Karteikarten der leeren Behälter gesteckt werden, um die Logistik zu veranlassen, die Teile zu beschaffen. Je weiter oben die Karte eingesteckt wird, desto dringender ist die Beschaffung. Dieses optische Signal gibt dem Fertigungsleiter sofort kund, wo er Prioritäten setzen muss. Das in der Lernfabrik installierte Logistiksystem ist daher ideal für kleinere Unternehmen, aber nicht nur für diese.
Selbstverständlich können Unternehmen aber auch ein PPS-System einsetzen, sollte dazu Bedarf bestehen. In der Lernfabrik steht dazu das Produkt ›Leanion‹ vom Unternehmen UWS zur Verfügung. Diese Software ist eine PPS-Lösung für die Fertigungssteuerung nach dem Lean-Gedanken und bindet den Industrie 4.0-Ansatz mit ein. Ein Realtime Location System der Firma Ubisens hilft jederzeit die aktuelle Lage etwa einer Teilekiste zu bestimmen. Zu diesem Zweck sind in der Lernfabrik voneinander unabhängige Zonen vorhanden, die von an der Decke angebrachten Sensoren überwacht werden. Diese Zonen sind an beliebiger Stelle einrichtbar und können mit einer minimalen Größe von nur 1 x 1 Meter besonders klein ausfallen.
Über einen an der Teilekiste angebrachten Tag kann jederzeit festgestellt werden, ob sich diese Kiste an der richtigen Stelle befindet. Treten Abweichungen vom geplanten Soll-Ablauf auf, wird der Planer ereignisgesteuert informiert und kann eingreifen. Dieses als ›LOS1‹ (Layout based Order Steering) bezeichnete System wurde von Prof. Dr. Schneider konzeptioniert. Platzmangel ist wohl das drängendste Problem, dem sich vor allem kleine Unternehmen zu stellen haben. Auch hier gibt es in Dingolfing einiges zu sehen, um den Mangel zu lindern. In der Lernfabrik ist es möglich, angelieferte Warenträger vom Typ ›Thorpak‹ direkt auf ein Rollgestell zu verbringen, die Kiste in ein Regal zu stellen oder den Inhalt alternativ in ein Hochregallager einzulagern.
Die auf dem Rollengestell abgelegten Warenträger können wiederum auf eine Transporteinheit geschoben werden, die Bestandteil eines Routenzugs ist. Auf diese Weise können Teile vom Wareneingang sehr einfach an entfernt liegende Produktionsbereiche transportiert werden.Die Kommissionierzone gehört zu den wichtigsten Zonen in einer automatisierten Produktionsumgebung. Hier werden alle für die Montage wichtigen Teile ebenso in Kisten verpackt, wie Rohmaterialien für die noch ausstehende Zerspanung. Damit die Bestückung korrekt erfolgt, gibt es unterschiedlichste Systeme, die hier unterstützen. In der Lernfabrik ist beispielsweise jede Kiste von einem Sensor überwacht, um zu verhindern, dass versehentlich ein Produkt aus einer falschen Kiste entnommen wird. Darüber hinaus wird die Lagerfachkraft von einer LED-Anzeige informiert, wie viele Teile sie aus der freigegebenen Kiste entnehmen darf.

Kampf dem Zeitdieb
Größere Teile werden nicht extra ausgepackt und umgelagert, sondern direkt den Thorpak-Behältern entnommen, um diese etwa zerspanend zu bearbeiten. Hier sind drehbare Vorrichtungen die passende Lösung: Aus eine Kiste werden die Teile entnommen, während die zweite Kiste mit den fertig bearbeiteten Werkstücken zur Abholung durch den Routenzug bereitsteht. Eine Kippvorrichtung erlaubt eine ergonomische Bereitstellung von Materialien.
Interessant auch die Abtrennung der Fahrbereiche für den Routenzug. Hier wurde auf den Anfahrschutz des Unternehmens A-Safe gesetzt, das für diese robusten Komponenten den Kunststoff ›Memaplex‹ verwendet, der nicht nur sehr stabil ist, sondern sich im Fall einer Kollision in die Ausgangsform zurückbildet. Wer keinen derartigen Routenzug benötigt, findet womöglich am Transportroboter ›ARC3‹ von Servus Gefallen. Dies ist ein System, das bis zu 50 Kilogramm schwere Boxen, Kartons, Trays oder Werkstückträger vom Wareneingang in die Produktion und danach zum Warenausgang transportiert.
Nicht zuletzt in der Montageabteilung kann dieses System für die zuverlässige Bereitstellung benötigter Teile sorgen. Wie die Lernfabrik zeigt, hat sich in Sachen Montagearbeitsplatz viel getan. Alles ist griffgünstig angeordnet, optimal ausgeleuchtet und auf das Nötigste reduziert. Werden einmal besondere Werkzeuge oder Verschleißteile benötigt, so kann dies über ein direkt daneben stehendes Konsignationslager geschehen. In solchen Ausgabeautomaten lagert ein Fremdlieferant seine Produkte ein, die erst nach der Entnahme dem belieferten Unternehmen in Rechnung gestellt werden.
Da die Lernfabrik eine reale Produktion nachbildet, ist natürlich auch ein Shopfloor-Management Board vor Ort, in dem sich der Besucher oder der Student informieren kann, dass eine automatisierte Produktion selbst ohne große EDV kein Blindflug ist, daher nicht zuletzt für kleine und mittlere Unternehmen keine Utopie bleiben muss. Man muss sich nur trauen und beizeiten umfassend informieren, damit eine runde Planung das Vorhaben zum Erfolg führen kann. Der erste Schritt sollte daher nach Dingolfing führen, damit Experten der Hochschule Landshut den Grundstein zum Erfolg legen können.
Download:
Diesen Artikel können Sie hier im PDF-Format herunterladen [476 KB] .
Mehr Informationen:
![]() |
Hochschule für angewandte Wissenschaften Landshut |
![]() |
Am Lurzenhof 1 |
![]() |
84036 Landshut |
![]() |
Tel. +49 871 506-0 |
![]() |
Fax. +49 871 506-506 |
![]() |
E-Mail: info@haw-landshut.de |
War dieser Artikel für Sie hilfreich?
![]() |
![]() |
![]() |
![]() |
![]() |
Bitte bewerten Sie diese Seite durch Klick auf die Symbole.
Zugriffe heute: 18 - gesamt: 12628.