Lubrix: Mit Minimalmengen zum Erfolg
Die Schmiertechnik, die sich rechnet
Zuverlässige Zerspanungsprozesse sind Grundvoraussetzung für eine wirtschaftliche Produktion. Doch dies muss nicht in jedem Fall mit einer Überflutungsschmierung einhergehen. Vielfach ist die Minimalmengenschmierung die bessere Wahl, doch müssen vor deren Einführung wichtige Dinge beachtet werden, die oft nur Experten wissen. Diesbezüglich eine Top-Anlaufstelle ist das Unternehmen Lubrix in Kirchheim unter Teck.
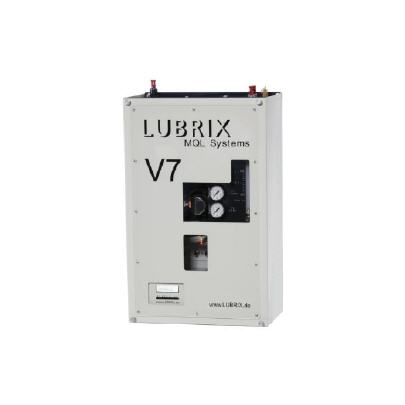
Werkzeugmaschinen sind sehr teure Investitionsgüter, die teilweise siebenstellige Eurobeträge kosten. Kein Wunder, dass zu deren Auswahl umfangreiche Vorbereitungen getroffen werden: Messen werden besucht, Preise und technische Angaben verglichen, Fachzeitschriften gelesen, viele Gespräche geführt und auf der Grundlage der zusammengetragenen Faktensammlung schlussendlich eine Kaufentscheidung getroffen.
Deutlich weniger Aufmerksamkeit bei der Neuinvestition bekommen die dazu nötigen Zerspanungswerkzeuge. Das gleiche Schicksal ereilt viel zu oft die Wahl der passenden Kühlschmierstrategie, mit der künftig die neue Maschine das Material zerspanen soll. Da Werkzeugmaschinen standardmäßig mit Equipment für die Überflutungsschmierung ausgeliefert werden und damit vielfach durchaus gute Ergebnisse erzielbar sind, wird dieses Kühlschmierkonzept für das zu produzierende Teilespektrum der neuen Maschine nur selten infrage gestellt.
Bremsen lösen
Diese Denkweise verhindert jedoch, dass Hochleistungswerkzeugmaschinen in die Lage kommen, ihr wahres Potenzial in die Stückkosten-Waagschale zu werfen. Würden beispielsweise Formel 1-Rennställe ähnlich vorgehen, würden die Motoren lediglich Standard-Öl bekommen und auf der Piste Universalreifen für Regen und Trockenheit zum Einsatz kommen. Solche Rennställe wären sehr bald nur mehr in Motorsport-Geschichtsbänden zu finden, die schenkelklopfenden und schmunzelnden Lesern von deren „Sparsamkeit“ berichten.
Ob Formel 1-Rennstall oder Automobil-Zulieferer – im harten Wettbewerb zählt nur Höchstleistung. Jedes Teil des Rennwagens beziehungsweise der Werkzeugmaschine muss daher auf Optimierungs-Potenzial untersucht werden. Standard-Komponenten an der falschen Stelle können am Ende den Sieg beziehungsweise den Auftrag kosten.Insbesondere im Fall der Serienfertigung von Komponenten sollte daher unbedingt geprüft werden, ob die Überflutungskühlung im Fall des jeweils zu produzierenden Teilespektrums wirklich der Weisheit letzter Schluss ist oder ob die Minimalmegenschmierung nicht die weit bessere Wahl wäre.
Die Vorteile dieser Schmierstrategie sind gewichtig: Weit geringere Beschaffungs-, Lager- und Entsorgungskosten für den Kühlschmierstoff machen sich nicht zuletzt in der Stückkostenrechnung bemerkbar, was die Wettbewerbsfähigkeit spürbar erhöht. Zudem sind die produzierten Späne durch den Einsatz der Minimalmengenschmierung trocken, sodass sich Späne von einem Kostenfaktor zu einem gefragten Wertstoff wandeln, für den Verwerter attraktive Preise bezahlen.
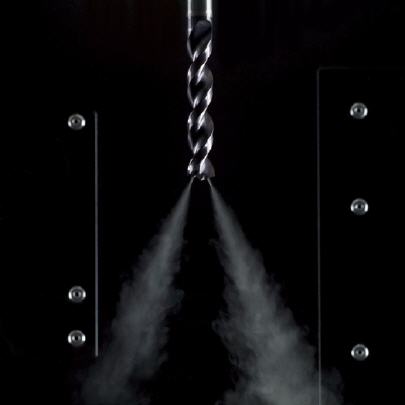
Beratung vor dem Kauf
Doch sind Anlagen zur Minimalmengenschmierung nicht mal eben im Vorbeigehen zu beschaffen. Wer seine Wettbewerbsfähigkeit durch den Einsatz dieser Technik auf Dauer sicherstellen will, muss hier auf genau die gleiche Weise vorgehen, wie es für die Beschaffung einer Werkzeugmaschine selbstverständlich ist. Es sind sehr viele Parameter zu berücksichtigen, die über den Erfolg der Investition in die Minimalmengenschmierung entscheiden. Dieses Wissen hat man in der Regel als Neueinsteiger nicht im Haus, weshalb unbedingt Fachleute hinzugezogen werden müssen, damit der MMS-Einsatz zu einer Erfolgsstory wird.
Eine Top-Anlaufstelle in Sachen Minimalmengenschmierung ist das Unternehmen Lubrix, das sich seit 2001 ausschließlich mit diesem Thema beschäftigt. Kostenlos breiten die Experten ihr diesbezügliches Wissen aus: Egal ob am Werkstück Gewinde einzubringen sind, tiefe Bohrungen verlangt werden, Messerköpfe mit einem Schnitt eine bestimmte Oberflächenqualität erreichen müssen oder Passungen zu reiben sind – die Fachleute von Lubrix kennen den Weg zum Erfolg.
Sie wissen, wie man entsprechende Technik zum Zerstäuben von Ölen baut, damit dieses Öl problemlos in Leitungen bis zu 40 Meter weit an die Werkzeugschneide transportiert werden kann. Die dahinterstehende Technik ist wahrlich beeindruckend. Es gilt, einen Ölnebel mit circa 0,8 Mikrometer kleinen Öltröpfchen zu erzeugen, der als ›Aerosol‹ bezeichnet wird. Diese kleinen Partikelgrößen sind notwendig, damit lange Transportwege in der Zuführung überwunden werden können, ohne dass das Öl in teilweise rechtwinklig abgewinkelten Kanälen sich an der Schlauchwandung niederschlägt oder Fliehkräfte in schnell rotierenden Werkzeugen oder Spindeln zum Problem werden. Sogenanntes ›Wandöl‹ ist zu vermeiden. Das Aerosol verhält sich dank der extrem winzigen Öltröpfchen ähnlich wie Zigarettenrauch. Nicht zuletzt dadurch erklärt sich dessen gute Transportierbarkeit in den zuführenden Leitungen.
Raffinierte Technik
Aus diesem Grund wird in den modernen MMS-Systemenvon Lubrix die Zerstäubung des Öls mittels eines Luftstroms realisiert, ähnlich dem Venturi-Prinzip. Auf diese Weise wird sichergestellt, dass die benötigten winzigen Öltröpfchen entstehen und zudem jederzeit die je nach Werkzeug erforderliche Schmierstoffmenge bereitgestellt werden kann. Damit dies klappt, sind die von Lubrix produzierten Aggregate in der Lage, Volumenströme an Schmierstoff-Aerosol von 10 bis zu mehreren Tausend Liter pro Minute bereitzustellen. Der Anwender hat daher die Gewissheit, dass sein Zerspanungsprozess in jedem Fall mit der erforderlichen Menge Öl gefahren wird.
Zudem ist die von Lubrix verwendete Technik derart robust, dass die Anlagen problemlos rund um die Uhr viele Jahre ohne notwendige Wartungseingriffe betrieben werden können.Doch dieses Wissen alleine ist erst die halbe Miete. Damit MMS problemlos funktioniert, müssen nicht nur das MMS-System an sich, sondern auch passende Werkzeuge zum Einsatz kommen, die mit entsprechend platzierten Austrittsbohrungen versehen sind, um das Öl-Luft-Gemisch direkt an die Schneide des Zerspanungswerkzeugs zu leiten. Gerade dieses Wissen um fachgerechte Auslegung ist noch viel zu wenig verbreitet, weshalb bei ersten MMS-Gehversuchen ohne dem Hinzuziehen einer Fachberatung sich oft wenig Erfolg einstellt und MMS enttäuscht aufgegeben wird.
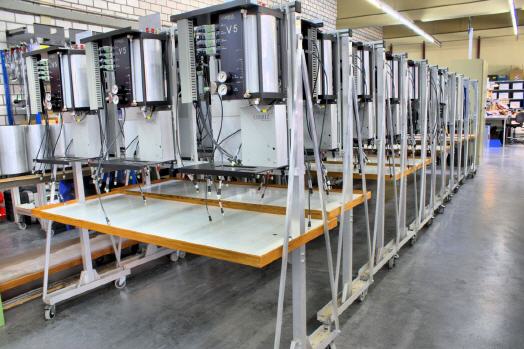
Passende Werkzeuge sind Pflicht!
Die Experten von Lubrix empfehlen, für die Minimalmengenschmierung Werkzeuge zu verwenden, die vom Hersteller für den Einsatz der MMS-Technologie gedacht sind. Der Grund liegt darin, dass damit der durch das Innere des Werkzeugs geleitete Kühlmittelstrom zu jeder Zeit an jede Stelle beziehungsweise an jede Schneide des Zerspanungswerkzeugs gelangen kann. Durch die besonders gestalteten Werkzeuge verteilt sich das Kühlschmier-Medium automatisch mehr oder weniger an alle Stellen des Werkzeuges. Kommt die MMS-Technik zum Einsatz, so sind schlechte Werkstückoberflächen, außerhalb der Toleranz liegende Passungen oder niedrige Standzeiten der Werkzeuge das Resultat falsch gewählter Zerspanungswerkzeuge.
Werden im Fall einer Ersatzbeschaffung neue Werkzeuge gekauft, sollte daher darauf geachtet werden, ob diese MMS-tauglich sind. Da MMS-Werkzeuge in der Regel auch für die KSS-Bearbeitung tauglich sind, kann auf die Vorhaltung gleicher Werkzeuge in verschiedenen Ausführungen (für MMS oder KSS) verzichtet werden. MMS-taugliche Werkzeuge unterscheiden sich hauptsächlich in der Lage der Austrittsbohrungen für den Kühlmittelstrom. Diese Bohrungen sind bei MMS-Zerspanungswerkzeugen in der Regel direkt auf die Schneide gerichtet. Werden Gewindebohrer, Reibahlen oder Messerköpfe für die MMS-Schmierung genau in Augenschein genommen, kann dieser Fakt sehr schnell bestätigt werden.
Bei Bohrern gibt es wegen deren Bauart jedoch eine Ausnahme: Hier weist die Sprührichtung der quasi hinter der Schneide angebrachten Austrittsbohrung nicht direkt auf die Schneide, sondern auf den Bohrungsgrund. Das hier auftretende Aerosol erreicht durch den sich verteilenden Luftstrom und die Drehbewegung des Bohrers jedoch in jedem Fall die Schneide und kann dort seine schmierende und kühlende Aufgabe erfüllen.
Standzeitsteigerung ist Serie
Untersuchungen haben gezeigt, dass mit MMS eingesetzte Bohrwerkzeuge oft eine längere Standzeit besitzen. Die Suche nach der Ursache etwa bei Stahlwerkstoffen ergab, dass das Kühlen mit KSS zu starken Temperaturschwankungen an der Werkzeugschneide führt, die dadurch Haarrisse bekommt. Diese führen zu schnellerem Verschleiß der Schneide. Diese Temperaturschwankungen gibt es in dieser Ausprägung beim Einsatz der MMS-Technik nicht, da das Temperaturniveau an der Schneidoberfläche stabiler bleibt. Dadurch ergibt sich am Ende eine verlängerte Standzeit der Bohrer.
Es gibt also viele Vorteile auf der Haben-Seite, die für den Einsatz der Minimalmengenschmierung sprechen. Fairerweise muss aber erwähnt werden, dass sich beim Zerspanen von sehr zähen Werkstoffen wie etwa Aluminium-Knet-Legierung eine Standzeitverlängerung der Werkzeuge nicht immer realisieren lässt. Da jedoch die Vorteile, wie etwa die trockenen Späne, großes Gewicht in der Kostenkalkulation haben, wird der Aufpreis für MMS-taugliche Werkzeuge akzeptiert.
Natürlich haben sich die Verantwortlichen von Lubrix intensiv Gedanken gemacht, auf welcher Basis das Öl beschaffen sein muss, um den hohen Anforderungen zu genügen: Es muss für die MMS-Anlagen optimal verwendbar sein, darf nicht schäumen, kleben und Bakterien keine Heimat geben, muss frei von Toxiden und zudem gesundheitlich so weit als möglich unbedenklich sein. Das Ergebnis dieser Überlegungen war, ein Öl auf synthetischer Basis zu nutzen. Von pflanzlichen Ölen wurde im Laufe der Jahre immer mehr Abstand genommen, da ein Naturprodukt qualitativen Schwankungen unterworfen ist, die im industriellen Umfeld problematisch sein können.
Überhaupt haben die Experten von Lubrix alles rund um MMS gründlich durchdacht, sodass die Technik jahrelang zuverlässig funktioniert. So werden in allen Lubrix-Systemen beispielsweise die Luftvolumenströme zum Werkzeug automatisch geregelt. Eine ausgefeilte Prozessüberwachung gibt sowohl eine Fehlermeldung im Klartext am MMS-System, als auch über Signale an der Werkzeugmaschine selbst aus. Außerdem sorgen auf Kundenwunsch moderne Feldbussysteme für den problemlosen Anschluss der Lubrix-Anlagen an moderne Steuerungen von Werkzeugmaschinen.
Ist einmal die Entscheidung gefallen, ein MMS-System von Lubrix zu beschaffen, so bekommt der Anwender eine Anlage, die auf die Bauart derjenigen Werkzeugmaschine ausgerichtet ist, an der sie später ihren Dienst verrichten wird. Zu diesem Zweck hat Lubrix eigene Prüfstände entwickelt, die in der Lage sind, reale Werkzeugmaschinen zu simulieren. Auf das Zusammenspiel der Kommunikation vom MMS-System zur Steuerung der Werkzeugmaschine wird das Lubrix-Gerät exakt abgestimmt, sodass die komplette Produktionsanlage beim Kunden vom ersten Augenblick an perfekt arbeitet.
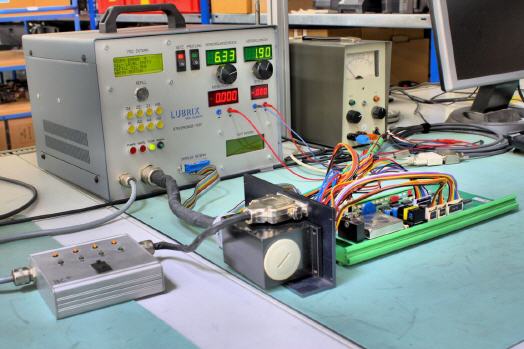
Mehr Informationen:
![]() |
LUBRIX GmbH |
![]() |
Heinkelstraße 7-9 |
![]() |
73230 Kirchheim Teck |
![]() |
Tel.: 07021 482900 0 |
![]() |
Fax: 07021 720950 |
![]() |
E-Mail: info@lubrix.de |
![]() |
www.lubrix.de |
War dieser Artikel für Sie hilfreich?
![]() |
![]() |
![]() |
![]() |
![]() |
Bitte bewerten Sie diese Seite durch Klick auf die Symbole.
Zugriffe heute: 25 - gesamt: 11967.