Per Multitasking zur Energieeffizienz
Drehen und Fräsen in einer Maschine
Die Ansprüche an Turbomaschinen für Luftfahrt und Energieerzeugung steigen. Mehr Effizienz er-fordert ein höheres Temperaturniveau, das extrem feste und zähe Werkstoffe voraussetzt. Das Fraunhofer-Innovationscluster ‚TurPro‘ entwickelt neue Bearbeitungsformen für diese Werkstoffe. Die ‚UniCen 1000‘-Dreh/Fräszentren von A. Monforts Werkzeugmaschinen mit ihrer dämpfenden hydrostatischen Führung bieten ideale Voraussetzungen für solche Bearbeitungsaufgaben.
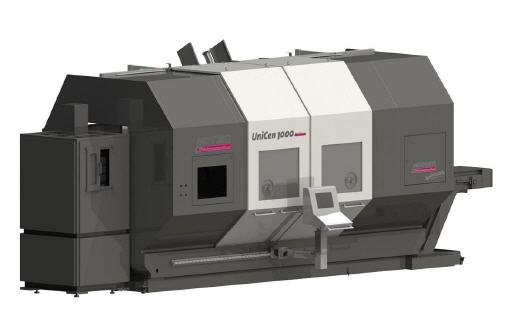
Trotz des Vormarsches alternativer Energieformen, Turbomaschinen werden noch lange Zeit wesentlicher Bestandteil der Energieerzeugung sein. Zumal beispielsweise Biogasanlagen den gleichen Kraftwerkspark erfordern wie fossil betriebene Kraftwerke. Auch Flugzeuge werden noch lange auf Schubtriebwerke angewiesen sein, die allerdings ebenfalls immer effizienter werden müssen.
Die Entwicklung der notwendigen Fertigungstechnologien hat sich das Fraunhofer-Innovationscluster ‚TurPro‘ des Instituts für Lasertechnik ILT und des Instituts für Produktionstechnologie IPT in Aachen zum Ziel gesetzt. In diesem Cluster, gefördert vom Land Nordrhein-Westfalen, arbeiten große OEM wie Siemens Power Generation, MAN Diesel & Turbo, Rolls-Royce und MTU Aero Engines mit vielen Zulieferbetriebe zusammen.
Die in diesem Bereich eingesetzten Werkstoffe wie Chromnickel , Nickelbasis und Titanlegierungen leiten Wärme schlecht ab und sind äußerst zäh. Das führt zu einem schnellen Verschleiß der Werkzeuge und hohen Anforderungen an die Stabilität der Maschinen. Hinzu kommt: Während früher Schaufeln und Rotoren einzeln gefertigt und dann zusammengesetzt wurden, bestehen sie bei den neuen energieeffizienten und ressourcenschonenden Turbinentypen aus nur noch einem integralen Bauteil (BLISKs oder BLINGs Blade integrated disk/ring). Die Schaufeln werden aus einer vollen Scheibe gedreht und gefräst. Dadurch verringert sich die Masse am Fuß der Schaufel, die Bauteile werden leichter und die Schaufeln können dichter stehen – der Wirkungsgrad steigt.
Damit entfällt aber auch die bisherige Trennung zwischen den Dreh und Frästeilen. Dr. Dominic Deutges, Leiter Neue Technologien der A. Monforts Werkzeugmaschinen GmbH in Mönchengladbach: „Die Bearbeitungsmaschinen müssen deshalb möglichst wirtschaftlich beide Verfahren in einer Maschine bereitstellen, um einen teuren und qualitätsgefährdenden Transfer der Bauteile zwischen verschiedenen Maschinen möglichst zu vermeiden.“ Zudem stießen konventionelle Revolverdrehmaschinen bei der Konturbearbeitung an ihre Grenzen. Komplexe Geometrien wie Hinterschneidungen erforderten eine flexibel anstellbare Werkzeugaufnahme. Das Konsortium setzt deshalb auf Multitaskingmaschinen, die Drehen und Fräsen vereinigen.
Besonders gute Voraussetzungen böten hierfür die Dreh/Fräszentren ‚UniCen 1000‘ von Monforts, die viele OEM und Zulieferer dieser Branche, aber auch das Projekt ‚TurPro‘, einsetzen. Drei Eigenschaften der Maschinen, die es für Bearbeitungslängen bis zu 800, 1500 und neuerdings auch 2500 mm gibt, sind ausschlaggebend: hohe Steifigkeit für die sichere Bearbeitung schwieriger Werkstoffe, gute Dämpfung gegen Schwingungen und Dauergenauigkeit für gleichbleibende Produktqualität. Dr. Deutges: „Dafür sorgt die hydrostatische Rundführung der Z-Achse. Der Schlitten mit dem Werkzeugträger läuft auf einer massiven Säule mit einem dünnen Ölfilm, der den metallischen Kontakt verhindert.“ Außerdem würden so Stick-Slip-Effekte, vor allem bei kleinen Verfahrwegen, vermieden.
Der Ölfilm sichere nicht nur Wartungs- und Verschleißfreiheit, sondern verleihe der Maschine auch beste Dämpfungseigenschaf-ten. Die bei der Schwerzerspanung auftretenden Schwingungen würden am Ausbreiten gehindert, was die Werkzeuglebensdauer deutlich verlängere. Sinnvoll sei der Einsatz der Maschine auch, um hochproduktive, aber konventionell gelagerte High-Speed-Cutting-(HSC)-Fräsmaschinen von der Schruppbearbeitung und dem damit einhergehenden Verschleiß zu entlasten.
Eine schwenkbare Motorfrässpindel ermöglicht die fünfachsige (X, Y, Z, B und C) Fräsbearbeitung, wie sie beispielsweise für das Herausarbeiten der Schaufeln im Integralbauteil BLISK benötigt wird. „Wir können die B-Achse außerdem interpolierend zum Drehen einsetzen und so Konturen herstellen, bei denen konventionelle Revolvermaschinen passen müssen.“ Aber auch der Späneabtransport erfordert neue Lösungen, da die typischen Werkstoffe zur Bildung besonders langer Späne neigen.
Hochdruck-Kühlschmiermittel, die bei der UniCen 1000 über eine innere Zuführung mit bis zu 120 bar oder über eine äußere Zuführung mit bis zu 350 bar zugeführt werden können, bieten eine Lösung. Dr. Deutges: „Der Kühlmittelstrahl wird zwischen Werkzeug und Span gepresst und kühlt direkt am Ort der Wärmeentstehung. Der Span bricht entweder durch den thermischen Schock oder er wird einfach mechanisch weggeschossen.“ Dies verhindere nicht nur die Bildung langer Späne, sondern ermögliche auch deutlich höhere Schnittgeschwindigkeiten.
Mehr Informationen zu Monforts:
![]() |
A. Monforts Werkzeugmaschinen GmbH & Co. KG |
![]() |
Schwalmstraße 301 |
![]() |
41238 Mönchengladbach |
![]() |
Tel.: +49 2161 9461-0 |
![]() |
E-Mail: sales@monforts-wzm.de |
![]() |
www.monforts-werkzeugmaschinen.de |
War dieser Artikel für Sie hilfreich?
![]() |
![]() |
![]() |
![]() |
![]() |
Bitte bewerten Sie diese Seite durch Klick auf die Symbole.
Zugriffe heute: 2 - gesamt: 2451.