Almig-Technik spart bares Geld
Kompressoren mit integrierter Wärmerückgewinnung
Die EKW GmbH im nordpfälzischen Eisenberg stellt feuerfeste Werkstoffe her. Mit dem Ziel, die Produktion energieeffizienter zu gestalten, wird das Unternehmen 2015 seinen Betrieb nach dem Energiemanagementsystem ISO 50001 zertifizieren lassen. Weil in vielen Anlagen und Maschinen des Betriebs Druckluft zum Einsatz kommt, hat der Hersteller seine vier mehr als 30 Jahre alten Last-Leerlauf geregelten Kompressoren durch drei direktgetriebene, drehzahlgeregelte Schraubenkompressoren der Baureihe VARIABLE von ALMiG ersetzt. Diese passen sich permanenten Lastwechseln an und vermeiden somit kostenintensive Leerlaufzeiten. Dadurch spart EKW rund 35.000 Euro Strom im Jahr.
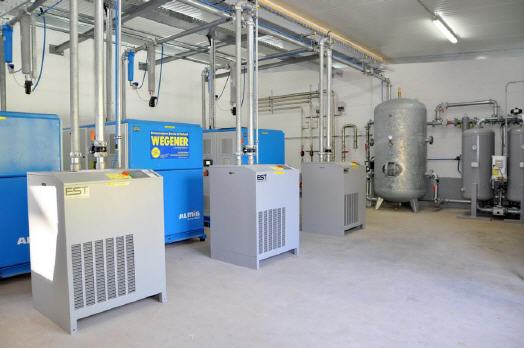
Klebsand ist ein ganz besonderes Material. Mit einem relativ hohen Tonanteil kleben die einzelnen Quarzkörner zusammen, und der Sand wird knetbar – daher der Name Klebsand. Entstanden ist er vor rund 30 Millionen Jahren durch verwitterte Sandsteine, die sich anschließend in Mulden und Senken gesammelt und sedimentiert haben. Das charakteristische an diesem Abbauprodukt ist seine Feuerfestigkeit.
Diese macht den Klebsand so begehrt für die Feuerfestindustrie und die Gießereitechnik. Im nordpfälzischen Eisenberg befindet sich eines der größten Vorkommen Europas. „Der Klebsand, den wir hier abbauen und verarbeiten, ist besonders haftfähig“, beschreibt Axel Deubert, Instandhaltungsleiter bei der EKW GmbH.
Das Unternehmen hieß früher „Eisenberger Klebsandwerke“ und ist seit der Gründung im Jahr 1903 im Familienbesitz. Nach dem neuesten Stand der Technik produziert der Betrieb Feuerbetone, neutrale, basische und saure halbplastische sowie Trockenvibrationsmassen sowie spezifische Werkstoffe für Reparatur- und Spritzarbeiten. Zum Einsatz kommen diese in Stahl- und Eisengießereien sowie in den Industriesegmenten Aluminium, Zement, Kalk, Umwelt, Energie und Chemie. „Mit speziellen Rezepturen können wir unsere Produkte auf individuelle Bedürfnisse unserer Kunden anpassen“, sagt Deubert.
EKW bietet zudem Systemlösungen an, mit denen sich unterschiedliche Schmelz- und Wärmebehandlungsöfen samt Peripherie funktionell auskleiden lassen. Am Hauptstandort arbeiten etwa 150 Mitarbeiter, weltweit zirka 400. In Eisenberg werden darüber hinaus Fertigteile aus eigenem Beton hergestellt. Dazu gehören Tauchrohre und -glocken, Siphonpfannen, Schlackensteine oder Rinnen. EKW hat Tochtergesellschaften in Italien, Frankreich, Slowenien, Brasilien, Malaysia und Mexiko, mehrere Unternehmensbeteiligungen und Partnergesellschaften in Deutschland sowie zahlreiche Vertretungen weltweit.
Auf energieeffiziente Produktion gesetzt
Feiner Sand liegt in der Luft. Axel Deubert läuft durch den Betrieb und zeigt auf die verschiedenen Maschinen und Anlagen. „Unsere Arbeit ist besonders energieintensiv“, beschreibt der Instandhaltungsleiter. „Wir legen deshalb sehr viel Wert auf eine effiziente Prozesstechnologie. Fördertechnik, Mischer, Dosierer, Abfüllanlagen, Palettierer oder Verpackungsanlagen – fast überall kommt Druckluft zum Einsatz.“ Dieser teure Energieträger versorgt beispielsweise die pneumatischen Regelungen, treibt Zylinder an, steuert Ventile und sorgt für den Materialtransport.
Bisher standen der EKW GmbH vier Last-Leerlauf geregelte Kompressoren zur Verfügung mit einer Laufzeit von inzwischen knapp 30 Jahren. Die Wartung dieser Anlagen übernahm die EKW Instandhaltung sowie die G. Wegener GmbH aus dem benachbarten Fußgönheim. Die Kompressoren mussten immer häufiger gewartet werden und das zahlte sich bald nicht mehr aus. „Dazu kam, dass die Drucklufterzeugung und -aufbereitung nicht zentral erfolgte – und das sollte geändert werden“, sagt Manfred Rankel, der bei Wegener im technischen Vertrieb arbeitet. Als schließlich eine Anlage ganz ausfiel und ein Ersatzkompressor geliehen werden musste, entschied sich der Werkstoffhersteller für eine neue Lösung.
Neben Wartung und Service bietet die G. Wegener GmbH auch Projektmanagement und Verkauf. Zudem ist das Unternehmen Vertriebspartner der ALMiG Kompressoren GmbH aus dem schwäbischen Köngen sowie der FST GmbH Filtrations-Separations-Technik aus dem nordrheinwestfälischen Essen. Schnell kristallisierte sich für Rankel heraus, dass sich für diese Anwendung drehzahlgeregelte, direkt angetriebene Kompressoren eignen. Bei EKW schwankt der Bedarf an Druckluft erheblich, weil die Bearbeitungszentren nicht permanent laufen.
„Im Vergleich mit Anlagen, die im Last-Leerlauf geregelt werden, sparen die drehzahlgeregelten schon allein damit rund 30 Prozent Energie ein“, erklärt Rankel. Nach eingehender Analyse entschied man sich für drei Schraubenkompressoren der Baureihe VARIABLE 130. Diese öleingespritzten Schraubenkompressoren lassen sich zwischen 4,30 und 20 Kubikmeter Druckluft pro Minute regeln. Die Bereitstellungsleistung beträgt damit 60 Kubikmeter pro Minute. Der Betriebsdruck ist stufenlos wählbar zwischen fünf und 13 bar. Die Antriebsleistung beträgt jeweils 130 Kilowatt.
Stets auf den Bedarf abgestimmt
Als Steuerung kommt die neue ALMiG Air Control P zum Einsatz. Mit integrierter Verbundsteuerung kann sie bis zu fünf Kompressoren im Grundlastwechselbetrieb regeln. Der Bediener kann sie einfach über Touchscreen und zwei Funktionstasten handhaben. Alle betriebsrelevanten Parameter kann er kontinuierlich überwachen. Weil die Steuerung alle drei Anlagen synchronisiert, lassen sich die Energievorteile der Drehzahlregelung voll nutzen. „Die Kompressoren erzeugen nur so viel Druck und Volumenstrom, wie tatsächlich gebraucht wird“, erläutert Rankel. „Dieser wird konstant gehalten. Steigt der Verbrauch an die Maximaldrehzahl, wird ein weiterer Kompressor zugeschaltet – oder es laufen alle drei Anlagen.“
Eine Drehzahlreserve wird stets beibehalten, so dass keine Druckschwankungen durch Zu- und Wegschalten der Kompressoren entstehen. In der Hauptlastphase laufen die Anlagen mit gleicher Drehzahl synchron. In der Schwachlastphase kann je nachdem nur ein Kompressor laufen. Dieser passt sich automatisch an das Verbrauchsprofil an. Da sich die Maschinen im mittleren Drehzahlbereich befinden, sind sowohl der Energiebedarf als auch die Geräuschemission geringer. Zudem werden die Bauteile weniger belastet, was sich positiv auf die Lebensdauer der Kompressoren auswirkt.
„Wir haben alle Energieflüsse systematisch erfasst und den gesamten Energieverbrauch sämtlicher Anlagen, Einrichtungen und Prozesse gemessen“, sagt Deubert. Mit dieser energieeffizienten Drucklufterzeugung kann EKW jetzt die Energiekosten langfristig senken – und noch von weiteren Vorteilen profitieren. „Wir haben uns als KMU freiwillig verpflichtet, den Betrieb nach ISO 50001 zertifizieren zu lassen“, berichtet der Instandhaltungsleiter. Wird dieses Energiemanagementsystem konsequent umgesetzt, lässt sich der Energiebedarf um bis zu 20 Prozent und mehr senken. Erreichen Unternehmen dieses Ziel, profitieren sie zusätzlich von Fördermitteln des Bundes und können ihre Steuern und Abgaben deutlich reduzieren. „Die neuen Kompressoren von ALMiG unterstützen uns dabei, die besonderen Auflagen zu erfüllen“, freut sich Deubert.
Trockene Druckluft und eine Wärmequelle
„Besonders interessant für uns ist der Kältetrockner, der in dieser Baureihe in einem eigenständigen Gehäuse integriert ist“, sagt Deubert. Seine Kennwerte sind auf die jeweilige Anlage exakt angepasst. Das hatten die alten Anlagen nicht, was zu einer feuchten Druckluft und bei verschiedenen Maschinenteilen zu Korrosion führte. Die trockene Luft wirkt sich damit positiv auf die Standzeit der Werkzeuge und Maschinen aus. Die Druckluft kommt zunächst in ein Sammelrohr mit großem Querschnitt und großer Oberfläche. Hier findet eine weitere Abkühlung und Ausscheidung des freien Kondensats über einen Zyklonabscheider statt.
Anschließend wird die Druckluft im „Sommerbetrieb“ mit Vorfilter, Kältetrockner, Feinstfilter aufbereitet. Die Aufbereitungskomponenten stammen von der FST Filtrations-Separations-Technik. Der Anbieter hochwertiger, energieeffizienter und betriebssicherer Lösungen entwickelt, projektiert und fertigt Druckluftfilter und Adsorptionstrockner in allen Größen und Varianten. Diese bieten besonders niedrige Differenzdrücke und durch die robuste Bauweise eine hohe Betriebssicherheit.
Im „Winterbetrieb“ wird ein Adsorptionstrockner nachgeschaltet und liefert einen Drucktaupunkt von mindestens -25 Grad Celsius. Dies hat einen großen energetischen Vorteil, da die Druckluft in dieser Qualität nur über die kalten Tage benötigt wird. Ansonsten reicht die Druckluftqualität für die Steuerungsteile aus. Durch die Taupunktsteuerung des Adsorptionstrockners können erhebliche Energieeinsparungen erzielt werden, da der Adsorptionszyklus der tatsächlichen Auslastung des Trockners vollautomatisch angepasst wird. Das heißt, die Häufigkeit der Umschaltung wird der Betriebssituation angepasst, der Regenerationsluftbedarf und somit die Energiekosten minimiert. FST lieferte zudem den Adsorptionstrockner. EKW erhielt damit eine maßgeschneiderte Lösung, die die Anforderungen optimal erfüllt.
Wärme sinnvoll genutzt
Die Kompressoren sind werkseitig mit Wärmetauscher und Wasserregelventil zur Heizwassererwärmung auf 70 Grad Celsius ausgestattet. „Diese Wärme werden wir ganz klar nutzen“, verspricht Deubert. „Denn somit können wir weiter Energie einsparen.“ Sie lässt sich zum Beispiel speichern, um damit in den kalten Wintermonaten die Produktionsräume zu heizen. Außerdem können Bauteile aus Beton vorgetrocknet werden. Weiterhin lassen sich elektrisch angetriebene Kältemaschinen betreiben, indem die Wärme Kältemittel verdampft. Noch sei aber alles in der Planungsphase.
Um die neue Druckluftstation zentral aufzustellen, hat EKW ein neues Gebäude errichtet. Die Planung der Druckerzeugungsanlage übernahm Manfred Rankel: „Wir haben die Kompressoren installiert und in Betrieb genommen. Es wurden auch alle Leitungen neu verlegt und die Hauptversorgungsleitung als Ring aufgebaut.“ Weil diese aus Edelstahl sind, besitzen sie sehr glatte Oberflächen und sind witterungsbeständig. Die Leitungen wurden zum Teil im freien verlegt. Das reduziert Reibung und somit kommt es zu weniger Druckverlusten. Die Planung der Infrastruktur mit Gebäude kam von Axel Deubert. Auch wird eine neue übergeordnete Steuerung mit Energieverbrauchszählern installiert, die Druckluft und Strom erfasst.
Axel Deubert ist zufrieden. „Mit dem Einsatz der ALMiG-Kompressoren und der Aufbereitung der Firma FST werden wir nicht nur erhebliche Energiekosten im Jahr sparen können. Wir haben jetzt eine hohe Verfügbarkeit der Druckluft“, resümiert er. Aber natürlich spielen auch die längeren Wartungsintervalle eine große Rolle. Und das betrifft nicht nur die Kompressoren, sondern alle Anlagen, die mit Druckluft betrieben werden. „Der gesamte Ablauf von der ersten Messung bis zur Fertigstellung und Inbetriebnahme lief reibungslos“, sagt Deubert. Weil die Drucklufterzeugung so problemlos läuft und noch Ressourcen frei sind, wird die Anbindung des gesamten Werkes geplant. Dann würde die Druckluftanlage von ALMiG auch zweischichtig laufen und drei separate Kompressoren mit Leistungen von 7,5 Kilowatt könnten entfallen. Somit könnte EKW in Zukunft auch mehr Abwärme nutzen.
Mehr Informationen:
![]() |
ALMiG Kompressoren GmbH |
![]() |
Adolf-Ehmann-Straße 2 |
![]() |
73257 Köngen |
![]() |
Tel.: +49 (0)7024 – 9614 – 0 |
![]() |
Fax: +49 (0)7024 – 9614 – 106 |
![]() |
E-Mail: info@almig.de |
![]() |
www.almig.de |
War dieser Artikel für Sie hilfreich?
![]() |
![]() |
![]() |
![]() |
![]() |
Bitte bewerten Sie diese Seite durch Klick auf die Symbole.
Zugriffe heute: 1 - gesamt: 3660.