"Schleifen" mit dem Laserstrahl
Scharfe Schneiden auf bessere Art
Diamant ist der härteste bekannte Werkstoff. Künstlich hergestellt kommt Diamant in der Zerspanung immer öfters zum Einsatz, da steigende Ansprüche etwa in Motoren und Getrieben zu immer schwerer zerspanbaren Stahl- und Leichtmetalllegierungen führen. Sehr häufig werden die dazu nötigen Diamant-Werkzeuge durch Schleifen in Form gebracht. Doch nun schickt sich ein Werkzeug an, an die Stelle teurer Schleifscheiben zu rücken, damit Zerspanungswerkzeuge noch schärfere und langlebigere Schneiden bekommen: Der Laserstrahl.
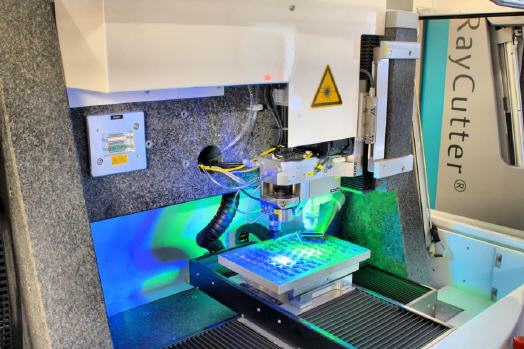
Moderne Schneidstoffe zerspanen heute selbst schwer zerspanbare Materialien mit einer Leichtigkeit, die staunen lässt. Sogar vor gehärtetem Stahl schrecken diese Schöpfungen aus den Forschungslabors der Schneidstoffhersteller nicht zurück und erreichen trotz widriger Umstände beachtliche Standzeiten. Doch ist das Ende der Fahnenstange noch lange nicht erreicht. Schließlich werden Konstrukteure nicht müde, ihre Produkte noch zuverlässiger zu bauen. Zu nennen wäre beispielsweise der Bau von Verbrennungsmotoren, die heute in der Lage sind, die im Benzin steckende Energie noch sparsamer in Bewegung umzusetzen.
Motorentechniker haben dazu die bisher genutzten Laufbuchsen aus dem Motorblock verbannt und setzen auf Beschichtungen, die direkt auf die Bohrung des Zylinderraums aufgebracht werden. Diese Beschichtungen sind extrem hart, da hier Siliziumnitrid ein Bestandteil des Beschichtungsmaterials ist. Dieses Material kann daher nur mit teuren Diamantwerkzeugen sinnvoll bearbeitet werden. Diamantwerkzeuge sind nur mit ausgeklügelte Verfahren herstellbar, schließlich handelt es sich hier um das härteste Material, das derzeit bekannt ist. Und dieses Material will wie das berühmte ›rohe Ei‹ behandelt werden.
Der Grund: Je höher die Härte eines Stoffes ist, desto höher ist auch seine Sprödigkeit. Glas beispielsweise besitzt eine Mohshärte zwischen 5 und 7. Es ist in geringen Grenzen elastisch und bricht, wenn diese Grenzen überschritten werden. Diamant besitzt die Mohshärte 10 und ist daher noch viel spröder und unelastischer. Aus diesem Grund müssen Schleifmaschinen besonders schwingungsfrei laufen, um einen sauberen Schliff am Diamant zu bekommen beziehungsweise um zu vermeiden, dass einige Diamantkörnchen durch unzulässige Druckkräfte von der Schneidkante abplatzen.
Doch trotz aller Technik: Beim Schleifen trifft eine Diamant-Schleifscheibe auf einen Diamant-Rohling, aus dem die gewünschte Form eines Zerspanungswerkzeugs herausgearbeitet werden soll. Ergo treffen Diamanten auf Diamanten, die sich durch gleiche Härte natürlich nicht wechselweise durchschneiden können. Die Folge ist, dass sich die kleinen Diamantkörnchen gegenseitig aus der Schleifscheibe beziehungsweise dem Rohling herausreißen. Obwohl sich dem Auge eine makellose Oberfläche präsentiert, zeigt der Blick ins Mikroskop, dass an zahlreichen Stellen mikrometerfeine Löcher im Material vorhanden sind. Die Folge ist, dass die Standzeit so geschärfter Diamant-Zerspanungswerkzeuge nicht in die Bereiche vordringen kann, die ohne dieses Manko zu schaffen wäre.
Aus diesem Grund setzt so mancher Schneidwerkzeughersteller nicht auf Schleif- sondern auf Drahterodiermaschinen, um seine PKD-Schneidwerkzeuge herzustellen. Dieses Verfahren arbeitet mit Funkenüberschlägen. Dabei bricht jeder Funke ein kleines Stück aus dem zu bearbeitenden PKD-Rohling heraus und gibt diesem so Stück für Stück die gewünschte Form. Doch auch hier gibt es, genau wie beim Schleifen, ein Problem: Die thermische Schädigung durch Hitze. Der Diamant verliert dadurch einen Teil seiner Härte.
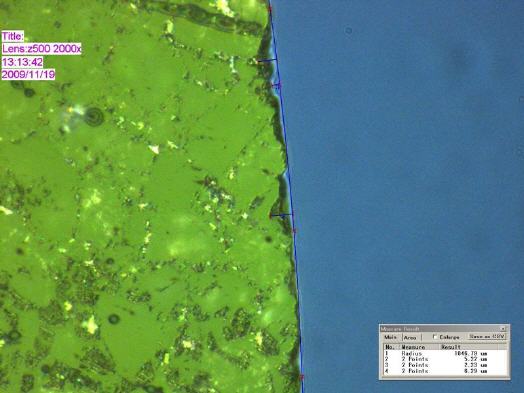
Schleifschäden
Geschliffene Diamantwerkzeuge besitzen Mikroausbrüche, die der Standzeit sehr abträglich sind.
Echter Quantensprung
Diesem Problem haben sich die Entwickler des Unternehmens Laserpluss AG angenommen und einen dritten Weg ersonnen, Diamant präzise und ohne die genannten Nachteile zu bearbeiten. Wie so oft wenn herkömmliche Werkzeuge versagen, meldet sich eine Allzweckwaffe zu Wort: Der Laser. Diese besondere Form des Lichts überrascht immer wieder mit außergewöhnlichen Eigenschaften. Die Laserpluss AG hat es mit diesem nie verschleißenden „Werkzeug“ geschafft, Diamant absolut präzise und ohne negative Seiteneffekte, wie etwa Mikroausbrüche von Diamantkörnchen oder das Einbringen schädlicher Hitze, zu bearbeiten.
Versuchsreihen zeigen, dass derart hergestellte Dreh- oder Fräswerkzeuge bis unmittelbar vor der Versagensgrenze gleichbleibende Vorschubkräfte aufweisen. Ein Hinweis darauf, dass es keinen schleichenden Verschleiß an den Schneidkanten gibt, sondern die Schneidkante bis zum Standzeitende unverändert zur Verfügung steht. Ein Novum, das bis dato nur wenig bekannt ist.
Der Grund für dieses überragende Schneidkantenverhalten ist in der Tatsache zu sehen, dass der Laserstrahl in der Lage ist, Diamant wirklich zu verdampfen. Die Schneidkante wird also nicht durch herausgebrochene Diamantkörnchen an verschiedenen Stellen geschwächt. Ergo gibt es auch keine Stellen, von denen sich ein verstärkter Schneidkantenverschleiß ausbreiten kann.
Wer per Laser bearbeitete PKD-Fräser zum ersten Mal in Augenschein nimmt und diesen Fräser mit einem diamantgeschliffenen Fräser vergleicht, hat den Eindruck, dass der diamantgeschliffene Fräser die weit bessere Oberflächengüte aufweist. Dies ist jedoch ein optischer Effekt, der hier den Betrachter irritiert. Fakt ist, dass eine per Laser erzeugte Schneide eine viel höhere Gleichmäßigkeit aufweist und eine unverfälschte Diamantstruktur besitzt, da diese nicht durch Hitzeeinwirkung beeinträchtigt wurde, wie es beim Schleifen der Fall ist.
Dies ist eine überraschende Erkenntnis, schließlich ist der Laser bekannt, mit seiner Hitze auch dicksten Stahl zu zerschneiden. Das Geheimnis liegt hier darin, dass beim Schärfen der PKD-Schneidkanten ein gepulster Laser verwendet wird. Diese Pulse sind extrem kurz und die Pausen ausreichend lang, sodass sich keine messbare Hitze im Diamant ausbreiten kann, was eine Gefügeumwandlung bewirken könnte. Die Abstimmung von Laserleistung, Vorschub, Laserpuls und Pause zwischen den einzelnen Laserpulsen ist das besondere Know-how des Unternehmens Laserpluss AG. Dieses Wissen wurde über viele Jahre erarbeitet und verfeinert.
Die gewonnenen Erkenntnisse flossen unter anderem in die Modelle ›PreCutter‹ und ›RayCutter‹ ein, die sich optimal zum Schärfen von Diamantwerkzeugen eignen. Dabei ist der PreCutter speziell zum schnellen Vorschneiden gedacht, während der RayCutter sich der präzisen Endbearbeitung widmet. Beide Modell besitzen einen extrem robusten Aufbau aus temperaturträgem Granit, Glasmaßstäben mit Nanometerauflösung sowie einen hochpräzisen Antrieb über Linearmotoren.
Die Frage, warum das Modell ›RayCutter‹ sich besonders für die Fertigbearbeitung von Diamantschneiden eignet, klärt ein Blick auf die Strahlführung dieses Modells: Der Laserstrahl wird nicht senkrecht auf die Schneidkante gelenkt, sondern über Spiegel zunächst umgelenkt, sodass der Strahl in einem Winkel von 15 Grad zur Schneide steht. Dadurch sind problemlos unterschiedliche Freiwinkel herstellbar, die sich je nach zu bearbeitendem Material zwischen fünf und zehn Grad bewegen. Mehr noch: Dadurch ist es sogar möglich, die Freifläche bogenförmig zu erstellen, was der Kantenstabilität und Genauigkeit zugutekommt.
Ein weiterer Vorteil dieser Konstruktion ist die wesentlich einfachere Ansteuerung der Achsen, deren Bewegung sich – im Gegensatz zu einer Fünfachsmaschine – nicht überlagern. Zusammen mit der Wasserkühlung bestimmter Maschinenteile ist diese Maschine in der Lage, die vorgegebene Kontur der Schneide mikrometergenau einzuhalten. Die auf diese Weise hergestellten Zerspanungswerkzeuge verblüffen selbst gestandene Zerspanungsspezialisten ob ihrer Standzeiten und Schnittgüten immer wieder aufs Neue.
Erfreulich ist, dass der Laser nicht übermäßig viel Zeit benötigt, um einen PKD-Rohling in ein präzises Zerspanungsprodukt zu verwandeln. Im Schnitt vergehen gerade einmal zehn Minuten, bis die Endkontur erreicht ist. Und das Schöne ist, dass der Laser sich nicht abnützt und daher etwa ein Stufenwerkzeug ohne Abrichtarbeit, mithin also mannlos hergestellt werden kann. Da auch kein Kühlschmierstoff benötigt wird, ist der Prozess sehr sauber.
Als Laserquelle wird ein Diodenlaser verwendet, der lediglich zehn Watt Leistung besitzt. Dies genügt, da die Kraft des Lasers auf einen kleinen Punkt von etwa 0,02 Millimeter konzentriert wird, was an dieser Stelle zu einem großen Energieeintrag führt, der das getroffene Material verdampfen lässt. Eine Kühlung ist nicht nötig, da zum einen der Impuls extrem kurz ist und zum anderen das verdampfende Material die eingebrachte Hitze mit sich abführt.
Im Betrieb werden von der Maschine Geschwindigkeiten zwischen 20 und 30 Millimeter pro Sekunde erreicht, wobei pro Sekunde 10.000 Laserimpulse auf den Diamantrohling einprasseln. Die Zustellung pro Bahn beträgt nur wenige tausendstel Millimeter, sodass weder große Hitze noch irgendwelche Drücke oder Momente auf den Rohling einwirken können. Die so erstellten Schneidwerkzeuge sind also Spitzenprodukte, die ihresgleichen suchen. Insbesondere Sonderwerkzeuge profitieren von dieser Technik, da damit Formen möglich werden, die allenfalls per Erodieren herstellbar sind, wobei jedoch hier, anders als beim Lasern, das Problem der Gefügeumwandlung durch Hitze gegeben ist.
Es lohnt sich also, diesbezüglich die Errungenschaften von Laserpluss näher in Augenschein zu nehmen. Das Unternehmen ist in der Lage viele Wünsche zu erfüllen, da die Fertigung der Laserquelle im eigenen Haus erfolgt, was Flexibilität verspricht. Aber auch wer nicht im Bereich der Zerspanungswerkzeuge heimisch ist, sollte einen Blick in das Portfolio des Unternehmens werfen, denn auch zum Markieren werden interessante Lösungen angeboten. So lassen sich beispielsweise Lastwagenfedern durch ihr Schwingungsverhalten nur schwer markieren. Ein Problemfall für den die Laserpluss AG bereits die fertige Lösung in der Schublade hat.
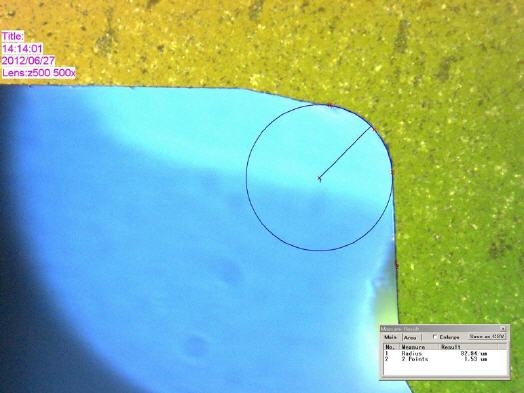
Scharf dank Lasertechnik
Lasergeschnittene Schneiden besitzen keine Kantenbrüche oder überhitzte Zonen, was für höchste Standzeiten sorgt.
Mehr Informationen:
![]() |
LASERPLUSS AG |
![]() |
Hauptstraße 279A |
![]() |
55743 Idar-Oberstein |
![]() |
Tel.: 0 67 81 - 98 66 40 |
![]() |
Fax: 0 67 81 - 98 66 4 99 |
![]() |
E-Mail: info@laserplussag.de |
![]() |
www.laserplussag.de |
War dieser Artikel für Sie hilfreich?
![]() |
![]() |
![]() |
![]() |
![]() |
Bitte bewerten Sie diese Seite durch Klick auf die Symbole.
Zugriffe heute: 1 - gesamt: 2978.