Vollautomatische Null-Fehler-Produktion
Kosten runter, Kundenzufriedenheit rauf
Unter den Elastomerverarbeitern gewinnen die Schlagworte Automatisierung und „Null-Fehler-Produktion“ deutlich an Bedeutung. Gilt es doch, Ressourcen effektiver zu nutzen und Wirtschaftlichkeit zu verbessern. Basis dieser Strategie ist der Einsatz einer prozessintegrierten Kontrolle mittels Sensorik. Das Credo lautet: Mehr Leistung und optimale Stückkosten oder mehr Liefersicherheit, weniger Prozessrisiko oder allgemein: Kosten drücken und Kundenzufriedenheit steigern. Gerade bei Elastomer-Teilen mit hohen Stückzahlen bietet die Automatisierung sehr gute Prozessgestaltung und gleichzeitig, durch den Einsatz von Sensorik zur Absicherung von Vulkanisierprozessen, ein neues Qualitätsniveau. Das Vulkanisieren gerät so zu einem industriellen Prozess mit einem „Null-Fehler“-Gutteilefluss.
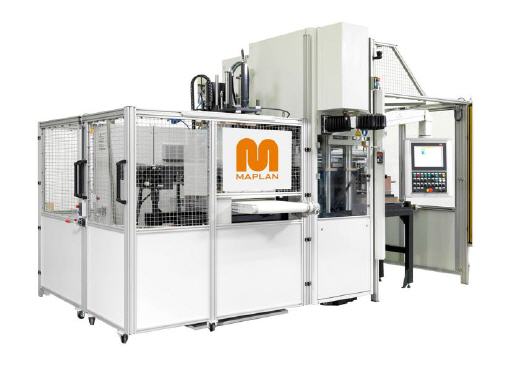
Jüngstes Beispiel dieser Entwicklung ist eine nun ausgelieferte Produktionseinheit an einen bedeutenden Entwicklungspartner der Automobilindustrie für Präzisionsformteile. Für diese Teile werden hohe Anforderungen an Temperatur- und Medienbeständigkeit, sowie ein lebenslanges überzeugendes Rückstellverhalten gestellt. Bei dieser Sonderentwicklung auf Basis einer Maplan MTF400/250editionS mit zwei Hydraulik-Antrieben in Cool-Driveausführung mit Servoantrieb ergab das Lastenheft des Kunden für die Vertriebsingenieure Gerald Kemper und Paul-David Betea von Maplan eine Reihe von Herausforderungen.
Hohes Qualitätssicherungsniveau
Kernstück der Fertigungszelle bildet eine Elastomermaschine MTF400/250editionS von Maplan. Die Maschinenkomponenten ermöglichen in Bezug auf Prozessgestaltung, Energieeffizienz und Prozesssicherheit mit der PC5000touch-Steuerung ein hohes Prozessniveau. Zur vollautomatischen Herstellung von Präzisionsformteilen mit Metalleinlegern war eine Automatisierung zur Metallteileseparierung, Vereinzelung und Zuführung gefordert.
Insgesamt besteht die Automatisierungslösung aus vier Hauptbaugruppen:
- Zuführeinheit für Metallringe
- Vereinzelungs- und Bereitstellungseinheit für Metallringe
- Übergabe- und Bestückungsvorrichtung, sowie
- einer Angussentnahmevorrichtung
Die Inspektionsmodule der Anlage bestehen aus einem Lasersensor zur Angussabfrage und Kameras zur Kontrolle der Formteile an einem Mehrkavitätenwerkzeug. In Bezug auf die Werkzeugtechnik bzw. Ergonomie wurde eine verbreiterte und bedienhöhenoptimierte Schließeinheit gewünscht. In der verbreiterten Schließeinheit finden große Mehrkavitätenwerkzeuge den entsprechenden Raum. Die bedienoptimierte Höhe gewährleistet dem Bediener eine bessere Zugänglichkeit für Kontrolle und Wartung, sowie bei Werkzeugwechseln.
Mit „Fingerspitzengefühl“ für ein anspruchsvolles Elastomer-Verfahren
Das Präzisionsformteil besteht aus Gummi, sowie einem oder auch mehreren Metallringen, die über die Automatisierung einer ausfahrbaren Heizplattenverschiebung im Werkzeug platziert werden. Dazu Paul-David Betea: „Da der gesamte Zyklusablauf vollautomatisch ist, darf es nahezu keine Fehlerquellen geben.“ Zur Steigerung der Wirtschaftlichkeit verwendet der Kunde Mehrkavitätenwerkzeuge mit den entsprechenden Raummaßen.
Prozesssicherheit durch Lasersensor
An der Maschinenvorderseite wurde ein Lasersensor auf der Angussentnahmevorrichtung installiert. Diese Vorrichtung fährt bei jedem Zyklus in die Schließeinheit der Maschine ein, um die Angüsse zu greifen und diese dann aus der Maschine nach dem „Pick-and-Place-Prinzip“ zu entnehmen. Beim Wiederherausfahren aus der Maschine tastet der Lasersensor die Angussplatte ab, um zu prüfen, ob beispielweise ein Anguss nicht entformt wurde. Die Zuführung der Metallringe erfolgt aus einem Vibrationsbunker heraus. Dieser Bunker fördert sequenziell Ring um Ring. Außerdem separiert er den oder die Ringe lagerichtig auf eine Vereinzelungsstrecke, sodass diese Ringe in einer Vorlagematrix für den nächsten Zyklus bereit stehen.
Automatisierung trifft auf Null-Fehler-Produktion
Die Werkzeugplatte mit den fertigen Präzisionsformteilen wird elektrisch zur Maschinenrückseite verschoben. Zur QS-Prüfung sitzen zwischen dem hinteren Shuttle und der Maschine hochauflösende Kameras. Die Kameras überprüfen die Positionierung aller Formteile auf der Werkzeugplatte beim Einfahren. Wenn die Platte erneut in die Maschine einfährt, wird überprüft, ob die Formteile auch sauber ausgedrückt wurden. Das Bauteil erfordert eine „sensible Behandlung“: Aufgrund der Form der Präzisionsformteile ist ein schräges Ausdrücken von oben zwingend erforderlich. Die Teile fallen auf ein darunter liegendes Förderband, welches diese anschließend in die Fertigteilebox befördert. Derartige Konzeptionen sind ein konsequenter Schritt in Richtung „Null-Fehler-Produktion“.
Der Trend zur Automation in der Elastomertechnik
„Der Trend zur Automation mit verknüpfter Sensorik zur Absicherung des Prozesses nimmt Fahrt auf. Kundenspezifische Anforderungen nehmen bei Maplan in den letzten drei Jahren deutlich zu“, kommentiert Paul-David Betea. Bedingt durch die hohe Globalisierung der Elastomertechnik, insbesondere in Automotive, tritt der Effekt in allen Weltregionen auf. Paul-David Betea erläutert dazu: „In Bezug auf die Automatisierungs- und Sensorikkomponenten ergibt sich, natürlich in Abhängigkeit der gewünschten Anforderung, ein geschätzter durchschnittlicher Mehraufwand von bis zu 50% zur üblichen Anlageninvestition. Gerade für Werkzeuge mit hohen Stückzahlen, bzw. vielen Kavitäten ergibt sich jedoch ein signifikant höheres Qualitätsniveau bei sehr schneller Amortisation.“
Die Integration von Automation und Sensorik in eine neue Elastomeranlage hat eine sehr nachhaltige Auswirkung auf die Wirtschaftlichkeit. Dies natürlich und vor allem auch über den gesamten Lebenszyklus einer Produktionsanlage. Bedienfehler werden vermieden oder Prozessabweichungen frühzeitig erkannt. Die Störgrößen werden in Richtung „Null-Fehler-Produktion“ beherrschbar. Während bei konventionellen Anlagen die Qualität nach dem Produktionsprozess überprüft werden muss, also „offline“, kann eine vollautomatische Anlage während der laufenden Produktion qualitätssichernd wirken („In-line“-QS). Das reduzierte Risiko von n.i.O.-Teilen im Teilefluss bedeutet somit ein hohes Maß an Sicherheit und möglichen Kosteneinsparungen. Ein stabiler Gutteilefluss sorgt für ein gutes Gefühl bei allen Beteiligten der Abnehmerkette: Bei Verarbeitern, Herstellern und Verwendern.
Mehr Informationen:
![]() |
MAPLAN GmbH |
![]() |
Schoellergasse 9 |
![]() |
A-2630 Ternitz |
![]() |
Tel.: ++43/2630/357 06-0 |
![]() |
E-Mail: office@maplan.at |
![]() |
www.maplan.at |
War dieser Artikel für Sie hilfreich?
![]() |
![]() |
![]() |
![]() |
![]() |
Bitte bewerten Sie diese Seite durch Klick auf die Symbole.
Zugriffe heute: 1 - gesamt: 2497.