Widias neue KM4X-Spindelschnittstelle
Für eine optimale Spindelleistung
Das bewährte KM-Schnellwechselsystem wurde von der internationalen Organisation für Normung (ISO) als ISO-Norm ISO 26622 anerkannt. Jetzt stellt WIDIA die neueste Generation seiner Spindelschnittstelle vor: KM4X.
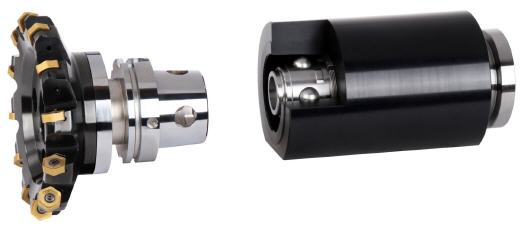
Bei der Bearbeitung zäher Werkstoffe wie Titan ist eine Spindelschnittstelle erforderlich, die eine optimale Nutzung der verfügbaren Leistung ermöglicht. Die Maschinenbediener stehen dabei vor der Herausforderung das Zeitspanvolumen zu maximieren, um die Produktionseffizienz zu verbessern, und müssen dabei die niedrigen Schnittgeschwindigkeiten und erheblich höheren Schnittkräfte berücksichtigen.
Zur Bewältigung dieser Herausforderung haben die Werkzeugmaschinenhersteller im Laufe der Jahre an der Verbesserung der Steifigkeit und Dämpfung von Maschinenspindeln und Maschinengefügen gearbeitet, um unerwünschte Vibrationen zu minimieren, die die Qualität des Werkstücks und die Standzeit des Werkzeugs beeinträchtigen. Trotz der gesteigerten Produktivität, die man mit diesen Verbesserungen erzielte, lag die Schwachstelle schon immer bei der Spindelschnittstelle selbst.
Bei einigen Werkzeugsystemen sind beträchtliche Anzugsmomente möglich. Doch durch die Schnittkräfte entstehen auch Biegemomente, die die Einschränkungen der Schnittstelle überschreiten, bevor die Grenzwerte für das Anzugsmoment erreicht werden. Die KM4X-Technologie besitzt eine dreimal höhere Biegesteifigkeit im Vergleich zu anderen Werkzeugsystemen. So können Anwender mit ihren verfügbaren Hochleistungsbearbeitungszentren die Schnittgeschwindigkeiten und Vorschübe selbst bei schwierigen Bearbeitungen erhöhen, und damit das Leistungspotenzial der Werkzeugmaschine voll ausschöpfen.
Der weitere Einsatz von Erickson-Werkzeugaufnahmen einschließlich Steilkegel- und HSK-Aufnahmen, Zylinderschaftverlängerungen und entsprechendes Zubehör wird durch eine einfache Nachrüstung vorhandener Werkzeugmaschinen mit KM4X ermöglicht. Dies bietet den zusätzlichen Vorteil, die Bearbeitungskapazität zu steigern, ohne in neue Maschinen und Anlagen investieren zu müssen.
Überblick über vorhandene Spindelschnittstellen
Die Werkzeug-Spindel-Schnittstelle muss hohen Belastungen standhalten, ohne dabei an Steifigkeit einzubüßen. Im Regelfall wird das maximal mögliche Zeitspanvolumen durch die maximal zulässige Werkzeugauslenkung oder durch das Auftreten von Rattern begrenzt.
In den vergangenen Jahrzehnten wurden mehrere unterschiedliche Spindelschnittstellen entwickelt bzw. optimiert. Aufgrund seiner günstigen Kosten-Nutzen-Position entwickelte sich der 7/24 ISO-Steilkegel zu einem der beliebtesten Systeme auf dem Markt. Obwohl der Steilkegel erfolgreich in zahlreichen Anwendungen eingesetzt wurde, machten die eingeschränkte Präzision und die Drehzahlbegrenzung ein weiteres Marktwachstum unmöglich.
Der Einsatz des Steilkegels mit Kegel- und Flächenkontakt war eine bedeutende Weiterentwicklung des normalen 7/24-Steilkegels. Durch den Flächenkontakt erzielt der 7/24-Vollkegel eine höhere Präzision auf der Z-Achse. Zugleich entstanden durch diese Kombination aber auch Nachteile in Form von Steifigkeitsverlust bei höheren Drehzahlen oder großen Seitenkräften. Die meisten Werkzeuge auf dem Markt sind Monoblock-Werkzeuge für Maschinenspindeln, die eine relativ geringe Einzugsspannkraft besitzen. Die Steifigkeit der Verbindung ist begrenzt, da das radiale Passungsübermaß minimal gehalten werden muss. Die erforderlichen Toleranzen für einen gleichmäßigen Flächenkontakt sind daher ausgesprochen eng. Dies bedingt hohe Fertigungskosten.
Anfang der 80er stellte Kennametal das KV™-System vor, eine kürzere Ausführung eines Steilkegels mit einer Drei-Kugel-Spanmechanik, die mittels einer konische Bohrungsfläche aktiviert wurde. Es folgten weitere Ausführungen, die mit Kegel- und Flächenkontakt angeboten wurden. 1985 riefen Kennametal und Krupp WIDIA ein gemeinsames Programm zur Entwicklung eines universellen Schnellwechselsystems ins Leben. Dieses System ist heute als KM™ bekannt und wurde vor kurzem als ISO 26622 genormt. Die polygonale Kegelflächenverbindung PSC, die inzwischen auch nach ISO 26623 genormt wurde, sowie das HSK-System von Anfang der 90er Jahre wurden zunächst in Europa eingesetzt. Später wurden sie nach DIN 69893 und anschließend auch ISO 121 genormt.
Warum ist die größere Biegesteifigkeit so wichtig?
Die Bearbeitung schwierig zerspanbarer Werkstoffe wie Titan erfolgt aufgrund der Wärmeentwicklung bei der Zerspanung mit relativ niedrigen Schnittgeschwindigkeiten. Daher haben Werkzeugmaschinenhersteller im Laufe der Jahre an der Verbesserung der Steifigkeit und Dämpfung von Spindeln und Maschinengefügen gearbeitet. Es wurden Spindeln mit besonders hohem Drehmoment bei geringen Drehzahlen entwickelt.
Das Drehmoment und die begrenzte Biegefähigkeit der Spindelschnittstelle müssen den Spezifikationen der Werkzeugmaschine und den Anforderungen für eine höhere Produktivität entsprechen. Dies wird besonders bei Schaftfräser-Anwendungen deutlich, bei denen die Auskraglänge in der Regel größer ist und die begrenzte Biegesteifigkeit der Spindelschnittstelle den einschränkenden Faktor darstellt. Beispiel: Ein Wendeschneidplatten-Fräser mit spiralförmiger Schneide und 250 mm (9.84 in.) Auskragung von der Spindelfläche und 80 mm (3.15 in.) Durchmesser erzielt ein Biegemoment von 4620 Nm (3407.5 ft. lbs.) bei einem Anzugsmoment unter 900 Nm (663.8 ft. lbs.). 900 Nm (663.8 ft. lbs.).
Als entscheidende Parameter einer Spindelschnittstelle mit Kegelfläche wirken die Einzugsspannkraft und das radiale Passungsübermaß des Steilkegels. Durch eine maximale Einzugsspannkraft bei entsprechend gewählten Übermaßwerten kann die Steifigkeit der Verbindung weiter erhöht werden. Die hohe Einzugsspannkraft und das kontrollierten Passungsmaße des KM4X-Systems hingegen sorgen für eine robuste Verbindung mit einer extrem hohen Steifigkeit und einem geringen Biegemoment, und ermöglichen so eine deutlich verbesserte Leistung bei der Titanbearbeitung.
Mehr Informationen zu Widia Deutschland:
![]() |
Widia Deutschland |
![]() |
Tel.: (49) 6172 737-0 |
![]() |
Fax: (49) 6172 78490 |
![]() |
E-Mail: w-de.service@widia.com |
![]() |
www.widia.com |
War dieser Artikel für Sie hilfreich?
![]() |
![]() |
![]() |
![]() |
![]() |
Bitte bewerten Sie diese Seite durch Klick auf die Symbole.
Zugriffe heute: 1 - gesamt: 3267.