Intelligenter Einsatz von Abwärme
Gasverbrauch um mehr als 25 Prozent gesunken
Die Ferdinand Täfler GmbH & Co KG, eine Tochtergesellschaft der Leipold Gruppe, verstärkt ihren Einsatz für den Klimaschutz: Mit einem neuen Konzept zur Wärmerückgewinnung und -speicherung hat das Unternehmen den Gasverbrauch im vergangenen Jahr um mehr als ein Viertel und die CO2-Emissionen um 55.000 kg reduziert. Ermöglicht wurden die signifikanten Einsparungen durch die Verwertung von Abluft aus der Produktion. Auch bei der Stromnutzung setzt der Mittelständler aus dem niedersächsischen Dransfeld auf Energieeffizienz.
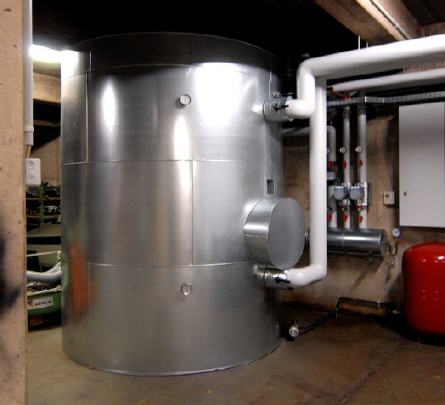
„Die Wärmerückgewinnung ist ein Meilenstein auf unserem Weg, den Energieverbrauch der Unternehmensgruppe sukzessive zu verringern und damit einen Beitrag zum Klimaschutz und zur Steigerung der Wirtschaftlichkeit zu leisten“, erklärt Pascal Schiefer, Geschäftsführer der Leipold Gruppe. Bei der Optimierung des Gasverbrauchs zur Beheizung der Fertigungshallen mit 8.000 qm Fläche wählte Täfler einen innovativen Ansatz: Bereits genutzte Energie soll wiederverwertet werden.
Nach einem Jahr kann bereits eine erste, positive Bilanz gezogen werden. Der Gasverbrauch wurde um mehr als 25 Prozent reduziert und 55 Tonnen CO2-Emissionen vermieden. Zum Vergleich: Jeder Bundesbürger verursacht nach Angaben des Umweltbundesamtes im Schnitt elf Tonnen pro Jahr. Das Prinzip der Energieeinsparung ist einfach: „In der Drucklufterzeugung entsteht in einem großen Umfang Abwärme, die wir in der Vergangenheit nicht genutzt haben“, erklärt Rüdiger Heine, stellvertretender Technischer Leiter im Werk Dransfeld. Dies habe man nun geändert.
Die Kompressoren wandeln nur 15 Prozent der zugeführten elektrischen Antriebsenergie in Druckluft um, der Rest ging bislang als Abluft verloren. Nun wird dieses Nebenprodukt genutzt, um die Fertigungshallen zu beheizen. Die Abluft der Kompressoren wird hierzu abgesaugt und über einen Wärmetauscher einem im Keller befindlichen Pufferspeicher zugeführt. „Inzwischen können wir 50 bis 55 kWh Heizleistung zurückgewinnen – genug für fünf Einfamilienhäuser“, erläutert Heine, der das Projekt federführend betreut. Insgesamt gewinne man 70 Prozent der eingesetzten elektrischen Energie zurück.
Der Speicher mit einem Volumen von 10.000 Litern ist notwendig, da es produktionsbedingt zu Verschiebungen zwischen dem Anfall der Abwärme und den Versorgungsspitzen zur Beheizung der Gebäude kommt. Der eigentliche Clou ist die hydraulische Einbindung des Systems in die mess-, steuer- und regeltechnische Umgebung der Fabrik. „Hierdurch ermöglichen wir ein optimiertes Be- und Entladen des Speichers“, sagt Heine.
Die Temperaturen in der Fertigung werden automatisch auf einem vorgegebenen Wert gehalten. Die Investition in die Wärmerückgewinnung summierte sich auf 45.000 Euro und soll sich bereits nach zwei Wintern rechnen. Hinzu kam ein Brennwertkessel für 25.000 Euro. Die für die Amortisierung der Investitionen erforderliche Ersparnis ist nicht nur auf den Minderverbrauch zurückzuführen. Die Gasbezugsspitze, die für die Berechnung des Leistungspreises bei den Versorgern maßgeblich ist, konnte laut Heine um bis zu 150 kWh gesenkt werden: „Unter dem Strich sparen wir über 20.000 Euro durch den geringeren Verbrauch.“
Die Wärmerückgewinnung ist eine von mehreren Maßnahmen, mit denen Täfler wertvolle Energie spart. Bereits seit 15 Jahren wird die Nutzung von Wasser und Gas vollständig und in Echtzeit erfasst sowie den jeweiligen Verbrauchsstellen zugeordnet. Bei Strom liegt die Quote bei über 85 Prozent. Auf Grundlage dieses Monitorings hat das Unternehmen weitergehende Maßnahmen zur Effizienzsteigerung entwickelt.
„Man muss Transparenz schaffen, um die Potentiale zu erkennen und zu heben“, sagt Heine. Permanent nicht personenbesetzte Bereiche sind beispielsweise mit Präsenzmeldern ausgestattet worden und in dem Rest des Gebäudes wird die Raumbeleuchtung automatisiert nach Helligkeit geregelt. Durch den Einsatz neuer Leuchtstoffröhren konnten weitere zwölf Prozent der für die Beleuchtung genutzten Energie eingespart werden.
Das Team hat bereits weitere Ideen für die effiziente Nutzung der Energie. „Im Sommer könnte die Energie aus der Wärmerückgewinnung zur Kühlung der Produktionshallen genutzt werden“, blickt Heine voraus. Der größte Wunsch aber sei ein eigenes Blockheizkraftwerk.
Mehr Informationen zur Carl Leipold GmbH:
![]() |
Carl Leipold Metallwarenfabrik GmbH |
![]() |
Schiltacher Straße 5 |
![]() |
77709 Wolfach |
![]() |
Tel.: +49 (0)7834 / 83 95-0 |
![]() |
Fax: +49 (0)7834 / 83 95-55 |
![]() |
E-Mail: info@leipold.com |
![]() |
www.leipold.com |
War dieser Artikel für Sie hilfreich?
![]() |
![]() |
![]() |
![]() |
![]() |
Bitte bewerten Sie diese Seite durch Klick auf die Symbole.
Zugriffe heute: 1 - gesamt: 2673.