Wellflammrohre effizienter herstellen
Messer-Reihenbrenner heizen kräftig ein
Der Weg in eine umweltfreundlichere Zukunft führt hin und wieder über ein Denken in größeren Dimensionen – so wie für die Bosch Industriekessel GmbH aus Gunzenhausen. Dort verrichtet nun eine von Grund auf neu und nach aktuellen Umweltschutzstandards konzipierte Fertigungsmaschine für gewellte Flammrohre in Hochdruckkesselsystemen ihre Arbeit. Dank modernster Wärmtechnik der Messer Cutting Systems GmbH aus Groß-Umstadt tut sie das vollautomatisch mit gesteigerter Leistung und gleichzeitiger Brennstoffeinsparung von 20 Prozent.
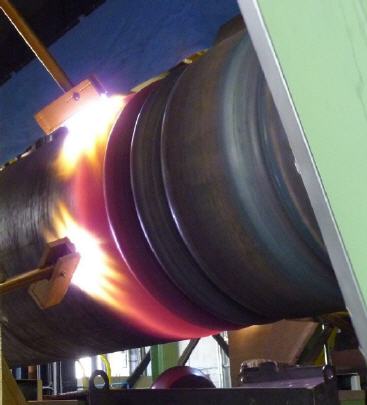
Die traditionsreiche Bosch Industriekessel GmbH in Gunzenhausen stellt seit Generationen hochleistungsfähige Großwasserraumkessel für die Industrie her. Sie ist einer von wenigen autorisierten Herstellern weltweit, die gewellte Flammrohre für überwachungspflichtige Hochdruckkesselanlagen produzieren. „Als einer der führenden Hersteller ist unser Anspruch, stets die beste Technologie bereitzustellen. Noch effizienter und noch umweltfreundlicher sollte daher unsere Flammrohr-Produktion werden. Aus diesem Grund haben wir unsere mittlerweile 20 Jahre alte Anlage ‚in Rente geschickt‘ und 2010 eine neue, vollautomatische Fertigungsmaschine in Betrieb genommen. Messer Cutting Systems lieferte dafür die vier Hochleistungswärmbrenner, die mit einem Acetylen-Sauerstoff-Gemisch betrieben werden. Diese modernen Brenner brachten uns, wie erwartet, einen enormen Leistungsschub – mit weiteren positiven Nebeneffekten“, erläutert Jürgen Thörel, Leiter Qualitätsmanagement bei der Bosch Industriekessel GmbH, die Modernisierung der Produktion in Gunzenhausen.
Enorm beansprucht, maximal belastbar
Überall dort, wo Heißwasser oder Dampf für industrielle Anwendungen benötigt wird, werden Großwasserraumkessel eingesetzt – beispielsweise in der Lebensmittel- und Papierindustrie zur Bereitstellung der Wärme für den Produktionsprozess. Die Bosch Industriekessel GmbH baut ihre Großwasserraumkessel nach dem bewährten Dreizugprinzip, als Einflammrohr- oder als Zweiflammrohrkessel zur Dampferzeugung bis 55.000 kg/h und zur Heißwassererzeugung bis 38.000 kW.
Wahre Leistungsträger und die höchst belasteten Bauteile in diesem Konzept sind Flammrohre: Auf der Feuerungsseite werden sie mit Temperaturen bis nahezu 2.000 Grad Celsius beansprucht, auf der Wasserseite mit maximal 230 Grad Celsius und Drücken bis 30 bar. Um einen optimalen Wärmeübergang zu gewährleisten, dürfen ihre Materialstärken ein bestimmtes Maß nicht übersteigen. Bei Kesseln mit hohen Leistungen und Betriebsüberdrücken werden daher keine glatten, sondern gewellte Flammrohre eingesetzt.
Wärmetechnik im Großformat
„Umso wichtiger ist es, bei der Produktion auf höchste Fertigungsqualität zu achten. Dazu gehört unter anderem, das Bauteil optimal mit definiertem Wärmeübergang aufzuheizen. Mit unseren vier wassergekühlten Reihenbrennersystemen SUPERTHERM RT-A 300 konnte Bosch die Produktionsleistung erhöhen“, erklärt Reiner Kolb, Projektleiter bei der Messer Cutting Systems GmbH aus Groß-Umstadt.
Jeder der vier SUPERTHERM-Brenner hat eine integrierte Zündflamme sowie eine eigene Gasversorgungstafel. Darüber lässt sich nach Kundenwunsch beziehungsweise den sicherheitstechnischen Notwendigkeiten entsprechend die Gaszufuhr regeln. Alle Gasversorgungselemente sind zum automatisierten Betrieb der Segment-Reihenbrenner in Verbindung mit einer Brennersteuerung im Schaltschrank montiert.
Da es die bisher größte Anlage dieser Art ist, waren einige Vorbereitungen zu treffen, um einen reibungslosen und erfolgversprechenden Ablauf zu gewährleisten. „Intensive Vorbesprechungen, in denen die Anforderungen und gewünschten Ziele der Großanlage abgesteckt wurden, ließen uns die entsprechende Ausstattung zusammenstellen und in das Gesamtkonzept integrieren“, erläutert Reiner Kolb von Messer Cutting Systems. Schon nach sechs Monaten Bauzeit konnte die Wellrohrmaschine in Betrieb gehen.
Vollautomatisch zum besten Ergebnis
Mit Hilfe der Messer-Flächenbrennersysteme wird das zu bearbeitende Material auf circa 900 Grad Celsius erwärmt, woraufhin der vollautomatische Warmumformprozess startet. Ein ausgeklügeltes Überwachungssystem sorgt für erstklassige Regelungsqualität und höchste Wiederholgenauigkeit. Dabei werden sämtliche relevanten Prozessdaten automatisch in das Firmennetzwerk übertragen und archiviert. Ein lückenloser Qualitätsnachweis ist somit sichergestellt. Nach dem Umformprozess muss das Wellrohr von Rückständen und Zunder befreit werden. Auch das erfolgt ohne jegliche Eingriffe des Bedienpersonals.
Der vollautomatische Betrieb, die kürzere Produktionszeit und der geringere Energieverbrauch senken die Stückkosten und ermöglichen höchste Qualität zu wettbewerbsfähigen Preisen. Durch das geschlossene Wasserkühlsystem sind geringe Korrosionsraten und eine lange Maschinenlebensdauer gewährleistet. „Das Zusammenspiel fein aufeinander abgestimmter Prozesse und Optimierungen verbessert gleichzeitig die Ökobilanz: Wir nutzen die Abluftwärme für die Heizungsanlage, die Kühlwasserwärme wird für einen neu installierten Luftvorhang verwendet und die modernen Flächenbrennersysteme von Messer reduzieren die Emissionen drastisch – bei einer Brennstoffeinsparung von 20 Prozent. Besser hätte es für uns und die Umwelt doch kaum laufen können!“, fasst Jürgen Thörel, Leiter Qualitätsmanagement bei der Bosch Industriekessel GmbH, zusammen.
Mehr Informationen zu Messer Cutting Systems:
![]() |
Messer Cutting Systems GmbH |
![]() |
Otto-Hahn-Straße 2-4 |
![]() |
64823 Groß-Umstadt |
![]() |
Tel.: +49 60 78 787 0 |
![]() |
Fax: +49 60 78 787 150 |
![]() |
E-Mail: info@messer-cs.de |
![]() |
www.messer-cs.de |
War dieser Artikel für Sie hilfreich?
![]() |
![]() |
![]() |
![]() |
![]() |
Bitte bewerten Sie diese Seite durch Klick auf die Symbole.
Zugriffe heute: 1 - gesamt: 3801.