Ein System, alle Geschäftsfelder
Alicona-Messsystem steigert Wertschöpfung
Bei Rohde & Schwarz ist Qualitätssicherung ein wertschöpfender Prozess. Durch die Erkenntnisse, die mit InfiniteFocus für die Fertigung gewonnen wurden, hat man die Prozesssicherheit erhöht, Produktionskosten gespart und Arbeitsabläufe optimiert. Den Profit bringt die universelle Einsetzbarkeit des Systems.
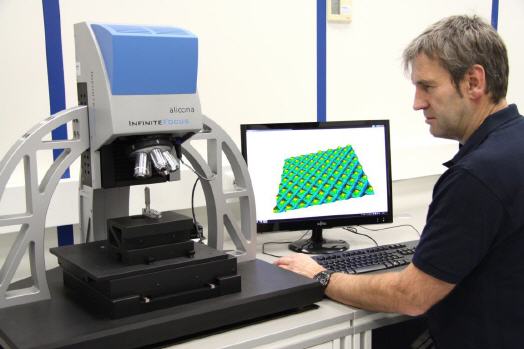
Ein Messsystem, das unabhängig von Form, Größe, Material oder Beschichtung von Bauteilkomponenten für eine hohe Fertigungstiefe in allen Geschäftssegmenten geeignet ist: Seit Rohde & Schwarz InfiniteFocus im Einsatz hat, ist aus dieser Vision gelebtes Qualitätsmanagement geworden. Europas größter Produzent von elektronischer Messtechnik beliefert Mobilfunkhersteller und Netzbetreiber, Elektronikhersteller, TV-Anstalten et cetera.
„Um unseren hohen Qualitätsstandard zu halten, erbringen wir alle wichtigen Wertschöpfungsbeiträge selbst. Das beinhaltet auch die Fertigung von mechanischen Komponenten“, erklärt Gerhard Kokott, Leiter des Qualitätsmanagements-Werk Teisnach. „InfiniteFocus wird für die komplette Bandbreite der Anwendungen aus dem Teilespektrum eingesetzt. Das umfasst die Qualitätssicherung von Werkzeugmitteln in der Umformtechnologie bis hin zur 3D-Messung von Dreh- und Frästeilen.“ Kokott weiter: „Die Flexibilität und universelle Einsatzmöglichkeit des Messsystems sind ein enormer Gewinn für uns. Nach weniger als einem Jahr haben wir mit InfiniteFocus die Prozesssicherheit erhöht, Fertigungsprozesse optimiert, Produktionskosten gespart und Arbeitsabläufe perfektioniert.“
Werkzeugmessung in der Umformtechnologie
Zur spanlosen Produktion zählt unter anderem das Umformen von Blech. Rohde & Schwarz fertigt auf diese Weise Miniaturschalter, die Bestandteil von Eichstandards für elektronische Messgeräte sind.
In eine Blechoberfläche wird mit einem Prägestempel eine definierte Reliefstruktur eingearbeitet, die für einen zuverlässigen Schaltkontakt mit hoher Kontaktsicherheit ohne „Verschweißen“ sorgt. „Wir prägen eine so genannte Waffelstruktur ins Blech. Das Prägewerkzeug fertigen wir mit einer hochpräzisen Mikrofräsmaschine selbst. Wir sprechen hier von einer pyramidenförmigen Struktur mit einer Grundfläche von 70µm x 70µm und einer Höhe von 35µm, die in die Werkzeugoberfläche gefräst wird. Das sind Dimensionen, die mit taktilen Tastsystemen nicht mehr zugänglich sind, geschweige denn in der nötigen Genauigkeit gemessen werden können“, beschreibt Kokott.
Für die exakte Messung der Form des Prägestempels wird InfiniteFocus eingesetzt. „Wir verifizieren den richtigen Abstand der einzelnen Bahnen durch die Messung der Täler und Spitzen. Außerdem messen wir diverse Winkel und bestimmen die richtige Teilung“, so Gerhard Kokott. Ergänzend wird das optische System auch für die stichprobenartige Messung des bearbeiteten Blechs eingesetzt. Der Fokus der Qualitätssicherung liegt allerdings „auf der Messung des Stempels und damit auf der Werkzeugfreigabe. Diese Optimierung war vor allem deshalb möglich, da wir jetzt in der Lage sind, Fertigungsdimensionen im µm-Bereich hochauflösend und wiederholgenau zu messen. Wir starten schneller mit der Produktion und binden deutlich weniger Personal“, fasst der Leiter des Qualitätsmanagements zusammen.
Messung von Mikropräzisionskomponenten
Etwa jedes zweite Handy weltweit wird mit Messtechnik von Rohde & Schwarz geprüft. „Diesen hohen Marktanteil wollen wir in Zukunft noch weiter ausbauen“, so der Elektronikkonzern. Zum entsprechenden Maßnahmenkatalog zählen auch höhere Investitionen in die Messtechnik, denn „die Güte unserer Produkte hängt im hohen Maße von der Präzision der mechanischen Komponenten ab“, erklärt Karl Stockbauer aus der Prüfmittelkonstruktion. Er ist unter anderem für die Einführung von neuer Prozesstechnologie verantwortlich.
Für ihn ist InfiniteFocus ein wichtiges Element, das die Fertigung im µm-Bereich ermöglicht hat: „Dieses Messgerät hat uns den Einstieg in eine neue Technologie eröffnet. Es zeigt uns die reale Topographie einer Oberfläche. Das Wissen um kleinste Maße, Höhenstufen, Formabweichungen, Rauheiten etc. hat uns in der Mikropräzisionsfertigung dorthin gebracht, wo wir heute stehen.“
Durch die vollständige Formmessung aus jedem Blickwinkel, den automatischen Vergleich der Ist-Geometrie mit CAD-Daten oder die Messung von Geometrien wie Hinterschliff und Rundlauftoleranz wurden völlig neue Erkenntnisse über eigene Fertigungskapazitäten gewonnen. Dabei profitiert das Unternehmen nicht nur von den hochauflösenden, wiederholgenauen Ergebnissen, sondern auch vom hohen Bedienerkomfort. Kurze Messzeiten, einfache Handhabung, umfassende Dokumentationsmöglichkeiten, intuitives Datenhandling und die dichte 3D-Visualisierung machen das System zu einem „gerne und viel genutzten Messgerät“, wie es heißt.
Es ist unter anderem gelungen, die Qualitätssicherung effizienter zu machen. Gerhard Kokott: „Die Teilequalifikation war in der Vergangenheit nur durch aufwendiges Messen mit mehreren Maschinen und mehrfachem Umspannen möglich. Jetzt ist der Nachweis über die richtige Fertigung denkbar einfach. Mit nur einer Messung erhalten wir sämtliche Funktionsparameter unserer Oberfläche. Rauheit und Form müssen nicht länger mit zwei verschiedenen Systemen gemessen werden.“
Steile Flanken, starke Reflexionen und unterschiedliche Beschichtung
Bauteile mit komplexen Formen sind bei Rohde & Schwarz tägliche Praxis. „Oberflächen sind heute oft Träger von unterschiedlichen Funktionen“, erklärt Kokott. „Das bedeutet für die Fertigung, spezielle und oft auch komplexe Formen produzieren zu müssen. Typischerweise handelt es sich dabei auch um Bauteile mit steilen Flanken, die Einschnitte oder Kerben aufweisen. Diese Merkmale haben ebenfalls eine definierte Funktion.
Für die Messung derartiger Geometrien kommt nur ein System infrage, das auch bei und auf diesen Flanken aussagekräftige Ergebnisse erzielt. Mit InfiniteFocus haben wir hier einen echten Treffer gelandet!“ Ähnliche Erfolge berichtet der QM-Leiter über die Oberflächenmessung von Bauteilen aus unterschiedlichen Materialien oder Beschichtungen. „Viele unserer Teile erhalten in der eigenen Galvanik Oberflächen aus Gold beziehungsweise Silber, was unterschiedliche Reflexionen zur Folge hat. Auch unter diesen Bedingungen erzielen wir schnell und einfach hochgenaue Ergebnisse. Das gilt auch für die Messung von mechanisch und chemisch beziehungsweise galvanisch bearbeiteten Oberflächen. Wir messen sogar lackierte Komponenten und verifizieren auf diese Weise, ob es sich um eine grob-, mittel- oder feinkörnige Struktur handelt.“
Mehr Informationen zur Alicona Imaging GmbH:
![]() |
Alicona Imaging GmbH |
![]() |
Teslastrasse 8 |
![]() |
A-8074 Grambach |
![]() |
Tel: +43 316 4000 700 |
![]() |
Fax: +43 316 4000 711 |
![]() |
Email: info@alicona.com |
![]() |
www.alicona.com |
War dieser Artikel für Sie hilfreich?
![]() |
![]() |
![]() |
![]() |
![]() |
Bitte bewerten Sie diese Seite durch Klick auf die Symbole.
Zugriffe heute: 1 - gesamt: 3137.