Laserjob: Höchstpräzision für Röntgenteleskope
Ausgeklügelter Prozess erfüllt alle Anforderungen
Streulichtblenden für Röntgenoptiken, wie sie in der Weltraumforschung benötigt werden, bestehen aus anspruchsvollen Werkstoffen und sind mit höchster Präzision zu fertigen. In einem ausgeklügelten Prozess werden von der LaserJob GmbH, Fürstenfeldbruck Bleche verschweißt, justiert und vom Max-Planck-Institut für Extraterrestrische Physik (MPE) messtechnisch kontrolliert.
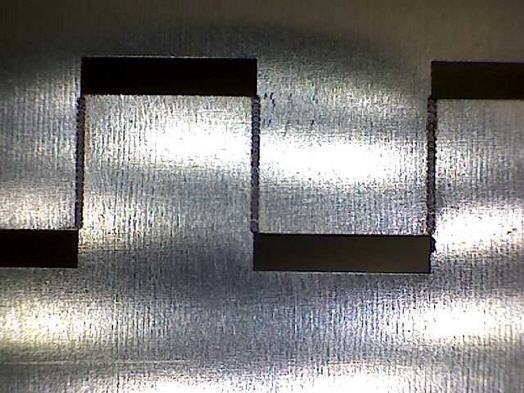
Verzahnte Schweißnaht
Eine Verzahnung ermöglicht die genaue Einstellung des Durchmessers.
Die Weltraummission ›eROSITA‹ hat zum Ziel, die Verteilung der Galaxienhaufen im Weltraum zu untersuchen. Dabei wird ein Verbund von sieben Röntgenteleskopen den Himmel durchmustern und im Vergleich zur bisherigen ›Rosat‹-Mission etwa 30-mal bessere Ergebnisse liefern. Das komplette Instrument wird maßgeblich vom Max-Planck-Institut für Extraterrestrische Physik (MPE) in Garching bei München gebaut.
Das Spiegelsystem ist so konzipiert, dass die Photonen unter sehr kleinen Winkeln auf die Röntgenspiegel treffen und fokussiert werden. Eng mit dem Spiegelsystem verknüpft ist eine Streulichtblende, die eine Abschirmung für alle Röntgenphotonen darstellt. Das Spiegelsystem besteht aus 54 konzentrischen, ineinandergeschachtelten Spiegelschalen. Die Streulichtblende – im Englischen auch ›baffle‹ genannt – besteht ebenfalls aus 54 einzelnen Ringen. Diese werden aus ›Invar‹-Blechen in einem von MPE und LaserJob entwickelten Verfahren gefertigt.
Im ersten Arbeitsgang wird die Abwicklung der Baffle-Schalen in Laserschneidtechnik hergestellt. Die Stirnseiten, die später zu verschweißen sind, erhalten eine spielfreie ineinander passende verzahnte Struktur.
Biegemaschine und Schweißnahtversuche
Mit einer Rundheitstoleranz von ± 0,05 mm und eine Positionstoleranz von 0,04 mm hat das Baffle sehr hohe Anforderungen zu erfüllen. Diese Herausforderung konnte nur durch eine intensive und langjährige Zusammenarbeit der beteiligten Partner gemeistert werden.
Die Invar-Bleche werden in einer Biegemaschine vorgeformt. Dies ist notwendig, um eine Vorspannung auf das Blech zu übertragen, damit später beim Schweißen die Rundheitstoleranz eingehalten werden kann. Die 0,125 mm dicken Invar-Bleche haben eine Länge von 1123 bis 240 mm, im gerollten Zustand einen Durchmesser von 360 bis 76 mm und eine Höhe von 50 bis 110 mm. Sie werden auf Formzylinder aufgespannt und mit Kaptonband fixiert.
Für jedes einzelne Invar-Blech gibt es einen speziellen Formzylinder, der in der Höhe und im Durchmesser dem zukünftigen Baffle entspricht. Um die Invar-Bleche so zu schweißen, dass die hohe Anforderung an die Rundheit von ± 50 μm erfüllt werden kann, wurde nach zahlreichen Versuchen schließlich eine verzahnte Kontur gewählt. Diese bietet den Vorteil, dass durch die verzahnten Enden der Durchmesser exakt an den Zylinder angepasst werden kann. Verschweißt werden die Bleche mit einem gepulsten Nd:YAG-Laser, der die Enden mit einer Schweißnaht von 0,2 mm verzugsfrei verbindet.
Die Schneidtoleranz im verzahnten Bereich liegt bei ± 5 μm. Um eine derartige Präzision zu erreichen, ist neben einem sehr exakten Vorrichtungsbau auch eine hochpräzise Maschinentechnik nötig. LaserJob setzt dazu auf selbstentwickelte Anlagen, die über eine hervorragende Positioniergenauigkeit verfügen. Die Umgebung der Maschine ist klimatisiert, um Ungenauigkeiten durch Temperaturdrift zu vermeiden.
Integration und Feinjustage
Im Labor des MPE wurde ein Integrations- und Messstand aufgebaut. Hier können bei sehr sauberer Umgebung die einzelnen Baffle-Schalen in eine Stützstruktur integriert werden. Dazu werden sie in die Schlitze der 16 Speichen eingesetzt und von zwei Seiten eingeklebt. Mit optischen Sensoren wird die Rundheit der integrierten Baffle-Schalen gemessen. Anschließend wird das Baffle mit der Röntgenoptik verbunden, unter optischer Kontrolle justiert und schließlich verklebt.
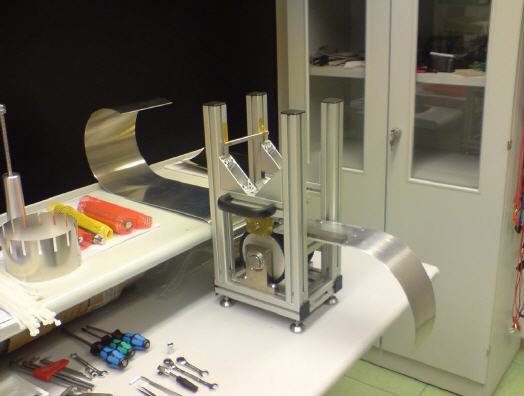
Gewusst wie
Die ›Invar‹-Bleche werden vorgeformt, um eine Vorspannung zu übertragen, um beim Schweißen die Rundheitstoleranz einzuhalten.
Mehr Informationen zur LaserJob GmbH:
![]() |
LaserJob GmbH |
![]() |
Liebigstraße 14 |
![]() |
82256 Fürstenfeldbruck |
![]() |
Tel.: +49 (0) 8141 52778-0 |
![]() |
Fax: +49 (0) 8141 52778-69 |
![]() |
E-Mail: info@laserjob.de |
![]() |
www.laserjob.de |
War dieser Artikel für Sie hilfreich?
![]() |
![]() |
![]() |
![]() |
![]() |
Bitte bewerten Sie diese Seite durch Klick auf die Symbole.
Zugriffe heute: 1 - gesamt: 2600.