KM4X-Spindelschnittstelle für maximale Leistung
Schwierige Werkstoffe einfach zerspanen
Maschinenbediener müssen das Zeitspanungsvolumen maximieren, um Produktionseffizienz zu erreichen. Werkzeugmaschinenhersteller haben im Laufe der Jahre an der Verbesserung der Steifigkeit und Dämpfung von Spindeln und Maschinengefügen gearbeitet, um unerwünschte Vibrationen zu minimieren. Trotz der gesteigerten Produktivität, lag der Schwachpunkt schon immer bei der Spindelschnittstelle selbst. Kennametal führte zur Lösung dieses Dauerproblems das bewährte KM-Schnellwechselsystem ein.
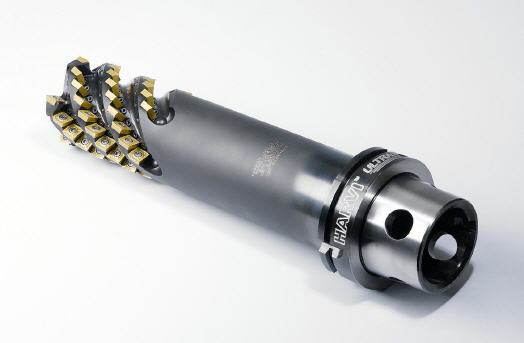
Bei einigen Schnittstellen sind beträchtliche Anzugsmomente möglich. Doch durch die Schnittkräfte entstehen auch Biegemomente, die die Beschränkungen der Schnittfläche überschreiten, bevor die Grenzwerte für das Anzugsmoment übertroffen werden. Die hohe Klemmkraft und die kontrollierten Passungsmaße des KM4X-Systems hingegen sorgen für eine robuste Verbindung, extrem hohe Steifigkeit und ein geringeres Biegemoment, und ermöglichen so eine deutlich verbesserte Bearbeitungsleistung bei Titan.
KM4X besitzt eine dreimal höhere Widerstandsfähigkeit gegenüber Biegemomenten als andere vergleichbare Werkzeugsysteme. So können die Anwender auf vorhandenen Hochleistungsbearbeitungszentren auch bei sehr anspruchsvollen Bearbeitungen die Schnittgeschwindigkeiten und Vorschübe erhöhen und damit das Potenzial der Werkzeugmaschine voll ausschöpfen.
Zusätzlich ermöglicht der Einsatz von KM4X auf bereits vorhandenen Werkzeugmaschinen die Bearbeitung von mehr Teilen pro Zeiteinheit. Dadurch können eventuell geplante Investitionen in neue Maschinen vermieden werden.
Überblick über vorhandene Spindelschnittstellen
Die Werkzeug-Spindel-Schnittstelle muss hohen Belastungen widerstehen, ohne dabei an Steifigkeit einzubüßen. Im Regelfall bestimmt eine zu große Werkzeugauslenkung und beginnende Vibrationen die Grenze der möglichen maximalen Zerspanungsrate für einen bestimmten Werkstoff.
In den vergangenen Jahrzehnten wurden mehrere unterschiedliche Spindelschnittstellen entwickelt beziehungsweise optimiert. Aufgrund seiner günstigen Kosten-Nutzen-Position entwickelte sich der 7/24 ISO-Steilkegel zu einem der beliebtesten Systeme auf dem Markt. Obwohl er erfolgreich in zahlreichen Anwendungen eingesetzt wurde, machten die eingeschränkte Präzision und die maximal möglichen Drehzahlen ein weiteres Marktwachstum unmöglich.
Der Einsatz mit einem Kegel- und Flächenkontakt war eine bedeutende Weiterentwicklung des normalen 7/24-Steilkegels. Durch den Flächenkontakt erzielt der 7/24-Vollkegel eine höhere Präzision auf der Z-Achse. Zugleich entstehen durch diese Kombination aber auch Nachteile, nämlich in Form von Steifigkeitsverlust bei höheren Drehzahlen oder hohen Seitenlasten. Die meisten Werkzeuge auf dem Markt sind Vollwerkzeuge eingesetzt auf Maschinenspindeln, die eine relativ geringe Einzugs-Spannkraft besitzen. Die Steifigkeit der Verbindung ist begrenzt, da die radialen Abmessungen minimal gehalten werden müssen. Die erforderlichen Toleranzen für einen gleichmäßigen Flächenkontakt sind daher ausgesprochen eng. Dadurch entstehen hohe Fertigungskosten.
Anfang der 80er Jahre stellte Kennametal das KV-System vor, eine kürzere Ausführung eines Steilkegels mit Drei-Kugel-Mechanik, die in einer konischen Bohrung aktiviert wird. Es folgten weitere Ausführungen, die auch mit Kegel-/Flächenkontakt angeboten wurden. 1985 riefen Kennametal und Krupp WIDIA ein gemeinsames Programm zur Entwicklung eines universellen Schnellwechselsystems ins Leben. Dieses System ist heute als KM bekannt und wurde als ISO 26622 genormt. Die polygonale Kegelflächenverbindung ›PSC‹, die inzwischen auch nach ISO 26623 genormt wurde, sowie das HSK-System vom Anfang der 90er Jahre wurden zunächst in Europa eingesetzt. Später wurden sie nach DIN 69893 und anschließend auch ISO 121 genormt.
Warum ist die Beschränkung der Biegefähigkeit so wichtig?
Die Bearbeitung schwierig zu zerspanender Werkstoffe wie Titan erfolgt aufgrund der Wärmeentwicklung bei der Zerspanung mit relativ niedrigen Schnittgeschwindigkeiten. Daher haben Werkzeugmaschinenhersteller im Laufe der Jahre an der Verbesserung der Steifigkeit und Dämpfung von Spindeln und Maschinengefügen gearbeitet. Es wurden Spindeln mit besonders hohem Drehmoment bei geringen Drehzahlen entwickelt.
Das Drehmoment und die begrenzte Biegefähigkeit der Spindelschnittstelle müssen den Spezifikationen der Werkzeugmaschine und den Anforderungen für eine höhere Produktivität entsprechen. Dies wird besonders bei Schaftfräser-Anwendungen deutlich, bei denen die Projektionslänge in der Regel größer ist und die Biegefähigkeit der Spindelschnittstelle den einschränkenden Faktor darstellt.
Beispiel: Ein Wendeschneidplatten-Fräser mit spiralförmiger Schneide, 250 mm Projektion von der Spindelfläche und 80 mm Durchmesser erzielt ein Biegemoment von 4620 Nm bei einem Anzugsmoment unter 900 Nm.
Als kritischste Parameter einer Spindelschnittstelle mit Kegel-/Flächenkontakt wirken die Spannkraft und das radiale Übermaß. Durch eine maximale Spannkraft bei entsprechend gewählten Übermaßwerten kann die Steifigkeit der Schnittstelle weiter erhöht werden.
Mehr Informationen zur Kennametal GmbH:
![]() |
Kennametal GmbH |
![]() |
Wehlauerstr. 73 |
![]() |
90766 Fürth |
![]() |
Tel.: 0911-9735-0 |
![]() |
Fax.: 0911-9735-388 |
![]() |
ebusiness.service@kennametal.com |
![]() |
www.kennametal.com |
War dieser Artikel für Sie hilfreich?
![]() |
![]() |
![]() |
![]() |
![]() |
Bitte bewerten Sie diese Seite durch Klick auf die Symbole.
Zugriffe heute: 1 - gesamt: 2527.