Kombilösung steigert die Wirtschaftlichkeit
Kennametal setzt auf Kern und Erowa
Werkzeugspezialist Kennametal erhöht in seiner Produktion den Automatisierungsgrad und steigert damit den Anteil der mannlosen Fertigung. Dafür setzt das Unternehmen auf die Kombination des hochpräzisen Bearbeitungszentrums KERN Micro mit dem Erowa Robot Compact 80 für den automatischen Werkstückwechsel. Erste Erfolge in Form verbesserter Wirtschaftlichkeit haben sich bereits eingestellt.
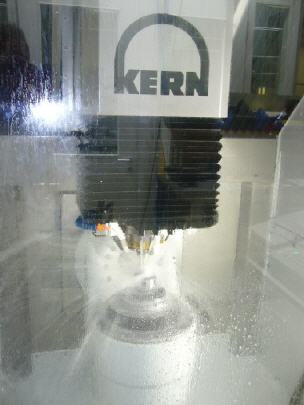
Der US-amerikanische Werkzeughersteller Kennametal hatte schon eine Kern Historie, als man sich 2015 bei der Kennametal Produktions GmbH & Co KG in Nabburg entschloss, die KERN Micro mit dem Erowa Robot Compact 80 zu erwerben. Zuvor hatte das Unternehmen im Entwicklungsbereich schon mehrere KERN Evo in Deutschland, in den USA und in Indien im Einsatz. In Nabburg setzen die Werkzeugprofis nun erstmals eine KERN Micro für die Serienfertigung ein. Mit der Maschine von Kern Microtechnik aus dem oberbayerischen Eschenlohe erhöhen sie den Automationsgrad und steigern gleichzeitig die Präzision.
Produziert werden auf der Maschine seit dem Frühjahr 2016 Schneidkörpersitze für ein spezielles Bohrwerkzeug. Die zylindrischen Werkstücke haben Durchmesser bis zu 32 mm und messen in der Länge bis zu 300 mm. Bearbeitet wird nur die Stirnseite. Die Herausforderung dabei: eine möglichst geringe Ausspannlänge und automatischer Werkstückwechsel. Mit der von Kern gemeinsam mit dem Anwender maßgeschneidert entwickelten Lösung ist Michael Forster, Prozesstechnikspezialist bei Kennametal, hochzufrieden: „Der Aufbau ist einmalig. Wir können das Trägerwerkzeug durch die Drehdurchführung der 4/5 Achse schieben und so einspannen, dass nur die zu bearbeitende Schnittstelle für den Schneidkörper herausschaut. Dadurch steht fast der komplette Arbeitsraum zur Verfügung und wir können auch sehr lange Werkzeuge zur Bearbeitung verwenden.“
Die Automatisierung mit dem Erowa Robot Compact 80 für PM 128 Paletten zahlt sich durch zusätzliche Einsparungen aus: Das System erlaubt es, bis zu 54 Werkstücke ohne Eingriff eines Maschinenbedieners zu fertigen. Die KERN Micro hält dafür 186 Plätze im Werkzeugkabinett bereit. Bei einer Bearbeitungszeit von etwa einer Viertelstunde pro Werkstück, reicht das für zirka 12 Stunden mannlosen Betrieb. Mit seinem Team tastet sich Forster Schritt für Schritt an diese Marke heran. Steigerungen der Maschinenlaufzeit ergeben sich, da der Zeitaufwand für den – zuvor manuellen – Werkstückwechsel stark sinkt. Dabei werden die Nebenzeiten um drei bis vier Minuten pro Werkstück verkürzt.
Damit bietet sich für Kennametal die Möglichkeit, das Fräszentrum entweder über eine Schicht komplett mannlos arbeiten zu lassen, oder aber die Zahl der Maschinen, die ein Bediener betreut, zu erhöhen.
Die Präzision der Bearbeitung mit dem von Kern entwickelten Fräsprogramm ist mit 3 µm merklich besser als die geforderten 5 µm. Damit ist Kennametal bestens für die Produktion des Nachfolgeprodukts gerüstet, das noch einmal erhöhte Genauigkeitsanforderungen mit sich bringt.
Mehr Informationen zur Kern Microtechnik GmbH:
![]() |
KERN Microtechnik GmbH |
![]() |
Olympiastraße 2 |
![]() |
82438 Eschenlohe |
![]() |
Tel.: +49 (0) 88 24 / 91 01-0 |
![]() |
Fax: +49 (0) 88 24 / 91 01-1 24 |
![]() |
E-Mail: kern@microtechnik.com |
![]() |
www.kern-microtechnic.com |
War dieser Artikel für Sie hilfreich?
![]() |
![]() |
![]() |
![]() |
![]() |
Bitte bewerten Sie diese Seite durch Klick auf die Symbole.
Zugriffe heute: 2 - gesamt: 2821.