MMC: Schrittweise bis zur Polierqualität
Präzisionswerkzeuge von MMC Hitachi Tool
Lichtoptiken aus Kunststoff erfordern besonders hohe Ansprüche an die Werkzeugoberfläche. Formconsult aus dem thüringischen Schmalkalden hat gemeinsam mit MMC Hitachi Tool Bearbeitungsstrategien entwickelt, die zeigen, dass sich auch sehr kleine und anspruchsvolle Konturen äußerst wirtschaftlich bis auf Fertigmaß fräsen lassen. Die Finishbearbeitung übernimmt ein 0,5-mm-Kugelfräser, das Ergebnis ist eine Top-Oberfläche in Polierqualität.
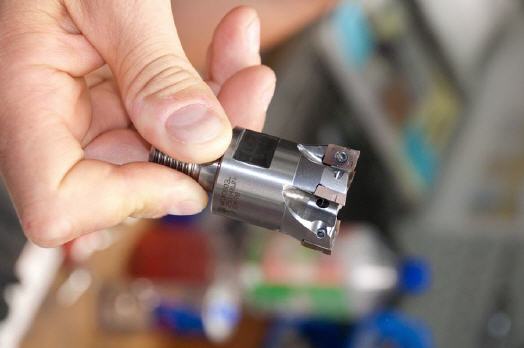
Formconsult betrachtet die enge Zusammenarbeit mit Technologiepartnern als sehr wichtig für den Projekterfolg. So auch bei Fräswerkzeugen. Seit etwa sieben Jahren kommen bei Formconsult superpräzise VHM-Werkzeuge (Vollhartmetall) sowie Wendeplattenfräser von MMC Hitachi Tool – mit steigender Tendenz – zum Einsatz. Das Know-how des japanischen Herstellers sollte auch im Fall des 2K-Werkzeugs zum Spritzen der Lichtoptik entscheidend zum Projekterfolg beitragen. Dabei stellte sich die Frage, wie man mit einem bereits gebauten und recht gut funktionierenden Werkzeug noch bessere Ergebnisse erzielen kann? Schließlich übernehmen Kunststoffteile immer raffiniertere optische Aufgaben, befeuert durch LEDs und andere Hightech-Lichtquellen. Damit steigen auch die Anforderungen an die Oberflächen rapide an.
„Dies bedeutet, dass wir bei den Einsätzen oder den Schiebern ständig auf der Suche nach neuen Werkstoffen sind, ebenso nach neuen Möglichkeiten beim Fräsen. Wie im aktuellen Fall für ein drittes, mittig angeordnetes Bremslicht, geht es fast immer darum, die über das Werkzeug im Kunststoff abgebildeten optischen Eigenschaften ausschließlich durch Fräsen herzustellen“, erläutert Jürgen Vierling, Prokurist und Leiter der Werkzeugfertigung bei Formconsult. „Und zwar mit einer hervorragenden Oberfläche, möglichst in Polierqualität. Denn diese ist entscheidend für den Glanz des Kunststoffs und damit für die optische Wirkung.“
Die Herausforderung ist dabei, dass die Lichtoptik in diesem Fall aus über hundert, nur wenige Millimeter große, unterschiedlich geformte Facetten besteht. Klassisches Polieren würde hier zu einer Geometrieverfälschung führen, da man dann keine scharfen Kanten mehr hat, sondern kleine Radien, was sich negativ auf die Lichtbrechung und damit auf die Streuung auswirkt. Darum wollte man in Schmalkalden vor etwa einem halben Jahr durch Testreihen recherchieren, wie sich noch bessere Oberflächenqualitäten durch Fräsen herstellen lassen.
Im Rahmen eines Benchmarks wurden verschiedene Werkstoffe, unter anderem der hochzähe Warmarbeitsstahl Böhler W400 VMR (1.2343) oder ganz aktuell der speziell für abrasive Kunststoffe ausgelegte, pulvermetallurgische Formenstahl Elmax getestet. Auf zwei Maschinen sind zahlreiche Tests mit allen möglichen Fräsertypen diverser Hersteller – auch von MMC Hitachi Tool – und unterschiedlichen Schnittwerten gefahren worden.
Bei Elmax handelt es sich um einen Chrom-Molybdän-Vanadium-legierten Spezialstahl, der – trotz hoher Korrosionsbeständigkeit – äußerst verschleißfest ist. Bei den ersten Versuchen, diesen 58 HRC harten Formenstahl zu fräsen, kam es allerdings immer wieder zu Werkzeugproblemen, die hauptsächlich auf die extrem schnell verschleißenden Schneiden zurückzuführen waren. Auch mit der erzielten Oberflächenqualität war man in Schmalkalden nicht ganz zufrieden. In enger Zusammenarbeit mit MMC Hitachi Tool wurde schließlich eine Lösung gefunden, die alle überzeugte. Bei der Finishbearbeitung fiel die Entscheidung für den extrem kurzen PN-beschichteten MMC Hitachi Tool-Kugelfräser (EPHPB-2005-1-PN) mit 0,5 mm Durchmesser (Radiustoleranz +/- 0,003 mm).
Als wichtig für die Oberflächenqualität stellte sich heraus, dass sich die Schnittwerte im mittleren Bereich bewegen und die Maschine konstant denselben Vorschub fährt. Eine Vorschubgeschwindigkeit (vf) von 350 mm/min kristallisierte sich als optimal heraus. Jedoch sollte man hierüber nicht vergessen, dass die Auswahl und Qualität des Fräswerkzeugs sowie die Definition der Bearbeitungswerte zwar extrem wichtig sind, aber nicht der allein bestimmende Faktor – für das Bearbeitungsergebnis ist das Gesamtsystem entscheidend. Also das optimale Zusammenwirken von Maschinenkinematik, Spindel, Spannmittel, Werkzeug und Frässtrategie. Für die Finishbearbeitung eines ganzen Feldes wurden 95 min benötigt. Besonders stolz waren sowohl Formconsult wie auch MMC Hitachi Tool darauf, dass der Kugelfräser nicht etwa sieben oder acht Stunden, sondern unglaubliche 30 Stunden durchgehalten hat.
„Wichtig ist uns, dass wir hinsichtlich Prozesssicherheit und Werkzeugstandzeit ebenfalls ein kräftiges Stück vorangekommen sind. Im Vergleich zu den Politurabstufungen fällt die Oberfläche unter Seidenglanzpolitur, die wir ausschließlich durch Fräsen erreicht haben“, zieht Jürgen Vierling ein positives Fazit. „Zusammengefasst kann man sagen, durch unsere Tests, die wir gefahren haben, können wir unseren Kunden ein noch hochwertigeres Werkzeug liefern. Ohne den exzellenten Support von MMC Hitachi Tool wäre dies allerdings kaum umzusetzen gewesen.“
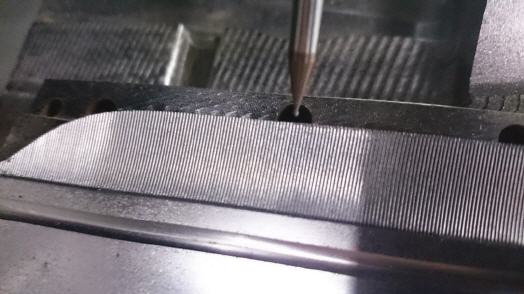
Mehr Information zu Hitachi Tool:
![]() |
Hitachi Tool Engineering Europe GmbH |
![]() |
Itterpark 12 |
![]() |
40724 Hilden |
![]() |
Tel.: +49 (0) 21 03 - 24 82-0 |
![]() |
Fax: +49 (0) 21 03 - 24 82-30 |
![]() |
E-Mail: info@hitachitool-eu.com |
![]() |
www.hitachitool-eu.com |
War dieser Artikel für Sie hilfreich?
![]() |
![]() |
![]() |
![]() |
![]() |
Bitte bewerten Sie diese Seite durch Klick auf die Symbole.
Zugriffe heute: 2 - gesamt: 1730.