Ersatzteile on demand
Ersatzteillogistik für Abfüllanlagen verändert
Anwender des 3D-Metalldrucks entdecken zunehmend die neuen Möglichkeiten und Freiheiten, die eine additive Fertigung eröffnet. 3D-Konstruktionen führen zu neuen Produktlösungen. Bisweilen werden Fertigungs- und Logistikkonzepte völlig neu aufgesetzt. Jung & Co. Gerätebau GmbH, Spezialist für Edelstahlkomponenten, setzt auf die additive Fertigung, um Ersatzteile für Getränkeabfüllanlagen schneller verfügbar zu haben. Thomas Lehmann, Geschäftsführer von Jung & Co., spricht über das Einsatzgebiet und die Vorteile des 3D-Metalldrucks.
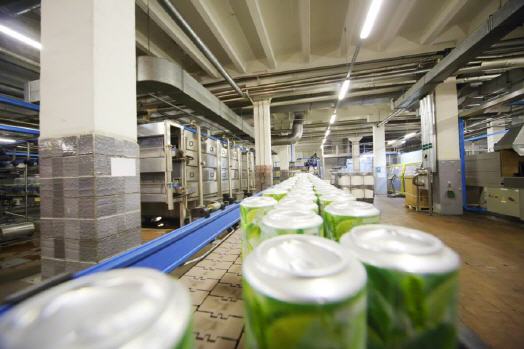
Wenn es um die Bearbeitung von Edelstahl bzw. Edelstahllegierungen, verschiedene Aluminiumlegierungen oder Titan geht, gibt es gute Gründe, die für Jung & Co. sprechen. Der Verarbeiter von Edelstahl verfügt über Werkstoff-Know-how, modernste CNC-Maschinen und unterstützt durch kompetente Beratung. Eine effiziente Fertigungsplanung und konsequente Qualitätssicherung in der Auftrags- und Baugruppenfertigung zählen zum Leistungsprofil. Das Spektrum reicht von der Getränke- und Lebensmittelindustrie, der Pharma- und Chemietechnik, dem Anlagenbau, und der Luftfahrt bis zur Förderindustrie fossiler Brennstoffe. Eine Spezialität ist die Fertigung von Ersatzteilen aus Edelstahl für Getränkeabfüllanlagen.
Know-how-Transfer sorgt für echte Synergien
Bei Jung & Co. steht die Anwendung der Werkstoffe Edelstahl, Aluminium und Titan im Vordergrund. Dieses Know-how konnte in 40 Jahren auf zahlreiche Branchen übertragen werden. Die klassischen Methoden der Zerspanung wurden nun um die additive Fertigung des Metalllaserschmelzverfahrens erweitert. In der Fertigung steht eine M2 cusing Multilaser von Concept Laser. Thomas Lehmann: „Eine Lösung in Edelstahl entsteht bei uns verfahrensübergreifend und konsequent ausgerichtet auf die Applikation. Die Teile oder Baugruppen entstehen bei uns konventionell zerspant, hybrid gefertigt oder komplett additiv. Der Kunde erhält ein Präzisions-Endprodukt aus einer Hand im Full-Service.“
Beispiel Getränkeindustrie
Nach ersten Erfahrungen mit der additiven Fertigung ging Jung & Co. einen Schritt weiter. Das Zauberwort lautete: „Ersatzteile on demand“. Thomas Lehmann dazu: „Anfangs dachten unsere Kunden: Was für eine verrückte Idee. Viel zu teuer. Geht gar nicht. Wir mussten also erst mal Überzeugungsarbeit leisten.“ Das Konzept „Ersatzteile on demand“ ging auf, weil die wirtschaftlichen Fakten nicht zu leugnen waren. Die Idee der additiven Fertigung von Ersatzteilen für Getränkeabfüllanlagen ging auf.
Getränkeabfüllanlagen im Dauereinsatz
Eine Abfüllanlage in der Getränkeindustrie sollte mit hoher Verfügbarkeit glänzen. Wichtig ist oft die Flexibilität der Abfüllanlage, denn es müssen unterschiedliche Größen von Flaschen oder Dosen abgefüllt werden. Aufgaben der Abfüllanlagen sind: Flaschen oder Dosen zuführen, abfüllen, verschließen und letztendlich diese an die Post-Processing-Stationen zu übergeben. Nach Lebensmittelrecht stehen Sauberkeit und Hygiene ganz oben im Anforderungsprofil.
Edelstahl zählt daher zu den bevorzugten Materialien der Branche. Produktionsraten von 40.000 – 80.000 Flaschen oder Dosen pro Stunde sind keine Seltenheit. Die Branche „lebt“ Geschwindigkeit. Bei einem Stillstand knickt die Wirtschaftlichkeit schnell ein. Fehlersuche, Ersatzteil anfordern, Versand und Einbau – das kann im schlimmsten Fall ein paar Tage dauern und zu Lieferverzögerungen an den Handel führen. Je nach Größe und Abfüllleistung der gesamten Abfüllstraße kostet eine Stunde Produktionsausfall ab ca. 4.000 EUR bis hin zu ca. 30.000 EUR.
So oder so muss der Abfüller dann auf andere Abfüllstraßen ausweichen und diese erst einmal auf die Gebinde anpassen. Für einen Produktionsleiter sind dies Stresssituationen, die er und seine Mitarbeiter natürlich gerne vermeiden.
Thomas Lehmann: „Wir haben den Kunden gesagt: Das muss nicht so sein. Additiv gefertigte Edelstahl-Bauteile können bei Bedarf gedruckt werden und auch noch konstruktiv optimiert werden. Da haben die meisten Kunden erst einmal ungläubig geschaut, weil wir mit so einer revolutionären Idee auftraten.“ Faktisch konnte Jung & Co. die altgedienten Kunden der Getränkeindustrie schnell auf das Additive Manufacturing einstellen.
Thomas Lehmann erwähnt dazu das Beispiel eines Dosenfüllventils für Getränkeabfüllanlagen.
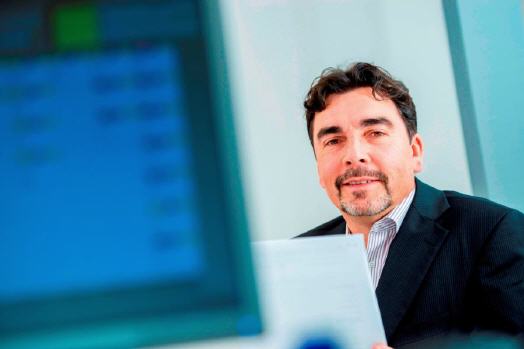
Weniger Bauteile in der Baugruppe
Thomas Lehmann, der sich schon frühzeitig mit dem Laserschmelzen von Edelstahl in Zusammenarbeit mit dem Technologiepionier Concept Laser beschäftigte, war klar: Eine additive Lösung kann hohe Geometriefreiheit bedeuten, bei gleichzeitiger verfahrensgerechter CAD-Konstruktion. Zudem können Bauteile oder ganze Baugruppen als One-Shot-Konzeption entstehen. Benötigt der Abfüller ein neues Dosenfüllventil, so kann das Bauteil nach CAD-Daten zeitnah gefertigt und beim Kunden verbaut werden, um so die Stillstandszeiten drastisch zu senken.
Thomas Lehmann: „Der 3D-Metalldruck ermöglicht kurze Stillstandszeiten für die Getränkeabfüller, die so bislang unmöglich erschienen. Mit einer neuen 3D-Konstruktion und der schnellen Verfügbarkeit spart der Kunde Geld und Zeit.“
Das von Lehmann gewählte Beispiel bezieht sich auf ein Füllventil einer Dosenfüllanlage. Die Fertigung von Ersatzteilen für Getränkeabfüllanlagen zählt zu den Spezialitäten der Pinneberger. Viele dieser Ersatzteile sind keine Standardkomponenten, sondern kundenspezifische Lösungen. Herkömmlich gefertigt, besteht die Baugruppe aus sieben Bauteilen aus Edelstahl 1.4404, die um notwendige Dichtungen ergänzt werden müssen. Die Edelstahlkomponenten mussten in der Präzisionszerspanung auf CNC-Maschinen zunächst gefräst oder gedreht und dann manuell montiert werden. Anschließend legte man sich die Baugruppe auf Lager, um – im Falle eines Falles – schnell reagieren zu können und die Abfüllanlage wieder hochfahren zu können.
„Das Dosenfüllventil wurde so umkonstruiert, dass es in einem Arbeitsgang auf einer M2 cusing Multilaser hergestellt werden konnte. Dadurch entfallen die Abdichtungen und Schnittstellen, die sonst durch das Zusammenfügen zwangsläufig entstehen. Der Entfall der Montage ist nicht nur kostengünstiger, sondern bietet auch zeitliche Vorteile für unsere Kunden. Die Herstellung des Bauteiles auf konventionelle Weise dauert ca. 8 bis 10 Wochen inklusive der Beschaffung des benötigten Feingussteiles, während die additive Herstellung ca. 1 Woche benötigt. Im Prinzip können wir so Ersatzteile on demand herstellen und punktgenau dann liefern, wenn der Bedarf urplötzlich gegeben ist. Die Vorteile, die sich bei einem solchen Präzisionsteil auftun sind für uns als Hersteller und für unsere Kunden als Anwender gleichermaßen sehr interessant, wenn man Revisions- oder Stillstandszeiten möglichst kurz halten möchte.“
Zudem müssen Ersatzteile nicht im Voraus gekauft und gelagert werden, weshalb weniger Kapital gebunden wird.
Neue Bauteillösungen und hohe Reproduzierbarkeit
Die Baugruppenentwicklung war dennoch ein kleiner Kraftakt. Die Belastungsanforderungen einer hochdynamischen Abfüllanlage sind entsprechend anspruchsvoll, wie man bei Jung & Co. sehr gut weiß. Daher wurde das Dosenfüllventil intensiven Lasttests unterzogen. Daneben gab es Topologieoptimierungen und Anpassungen der Konstruktion sowie Untersuchungen des Nachbearbeitungsaufwandes und der Teileentspannung.
Thomas Lehmann: „Die Bauteilentwicklung ist ein spannender Prozess. In der Entwicklung tauchen neue Optionspfade auf, die man zielgerichtet erschließen kann. Das fertige 3D-Bauteil sieht nicht nur anders aus als das konventionelle, sondern es ist auch ca. 35 % leichter. Meistens kann es auch deutlich mehr. Dies kann man sehr gut einpreisen, weil es darauf ankommt, welche Effekte sich in Zeit und Geld unter dem Strich einstellen.“
Der additive Ansatz führt letztendlich zu überarbeiteten Lösungen, die leistungsgesteigert sein können. Nach Auskunft von Jung & Co. sind die Möglichkeiten vielschichtig: Es können Leichtbauansätze oder Funktionsintegrationen, wie z.B. Kühlen, Temperieren oder Sensorik, einbezogen werden. Daneben sind auch hybride Fertigungsansätze von Relevanz. So können einfache Geometriebereiche konventionell zerspant werden, während komplexe Geometriebereiche eines Bauteils additiv gefertigt werden können.
Ein wichtiger Punkt ist auch die hohe Reproduzierbarkeit. Einmal gefundene Prozessparameter gewährleisten gleichbleibendes Qualitätsniveau inklusive der mitgelieferten Dokumentation.
Thomas Lehmann: „Die zahlreichen Aspekte des 3D-Metalldrucks bedürfen im Kundengespräch einer genauen Analyse der Leistungsanforderungen. Erst im Dialog entstehen Lösungswege, die, abgestimmt auf das Verfahren, zu neuen Lösungen führen, die mehr können als die bisherigen Bauteile. Auf der Kostenseite ist letztlich entscheidend, was das Teil kann und wie schnell es verfügbar ist.“
In der Getränkeindustrie gab es bei den Abfüllern noch ein wichtiges Kernargument für die additive Fertigung: Bei konventionellen Gussteilen aus Edelstahl sind Lunker in der Lebensmittelindustrie als Verschmutzungsfallen nicht gerade beliebt. Thomas Lehmann: „Lunker gilt es in diesem Einsatzgebiet zu vermeiden, was ein weiterer wichtiger Vorteil des 3D-Metalldruckverfahrens ist.“
Aussichten des 3D-Metalldrucks bei Jung & Co.
Die additive Fertigung ergänzt seit dem Jahre 2015 das CNC-Fertigungsspektrum bei Jung & Co. Derzeit wird auf einer M2 cusing Multilaser mit 2 x 400 W-Laserquellen von Concept Laser additiv gefertigt. Ein Ausbau der Fertigung steht an, weil sich die Nachfrage positiv entwickelt.
Thomas Lehmann: „Der Bedarf an 3D-gedruckten Metallbauteilen dürfte kontinuierlich und stabil ansteigen. Es freut mich sehr, dass viele unserer Kunden die Vorzüge additiver Bauteile erkennen. Es freut mich aber genauso, dass wir im Hause unsere Mitarbeiter und vor allem die Auszubildenden mit der neuen Technik vertraut machen können. Als mittelständisches Unternehmen ist der Hinzugewinn an Know-how immer ein wichtiges Argument im Kundendialog.“
Darüber hinaus plant Jung & Co. noch im laufenden Jahr die Anschaffung eines mobilen Laserscanners. Damit kann ein völlig neuer Weg in der schnellen Ersatzteilversorgung der Kunden durch das Unternehmen beschritten werden. Durch eine Laservermessung kann das betreffende, zu ersetzende Bauteil vor Ort in der Anlage beim Kunden digital dargestellt werden. Nach dem Online-Datenversand der entsprechenden 3D-Dateien zu Jung & Co. kann dort die Fertigung auf der Laserschmelzanlage in dringenden Fällen auch sofort starten.
Thomas Lehmann: „Die additive Fertigung eröffnet eine Reihe von Perspektiven, wenn es um Ersatzteile für Abfüllanlagen in der Getränkeindustrie geht. Ein Laserscanner ist der nächste logische Schritt, um die Prozesskette vollständig zu digitalisieren. Natürlich hat das auch den Charme, dass wir uns ein Stück weit von Raum und Zeit in der Ersatzteilversorgung entkoppeln.“
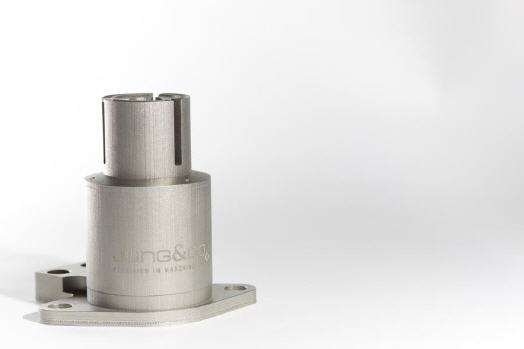
Mehr Informationen zu Concept Laser:
![]() |
CONCEPT Laser GmbH |
![]() |
An der Zeil 8 |
![]() |
96215 Lichtenfels |
![]() |
Tel.: +49 (0) 9571 / 949-238 |
![]() |
Fax: +49 (0) 9571 / 949-239 |
![]() |
E-Mail: info@concept-laser.de |
![]() |
www.concept-laser.de |
War dieser Artikel für Sie hilfreich?
![]() |
![]() |
![]() |
![]() |
![]() |
Bitte bewerten Sie diese Seite durch Klick auf die Symbole.
Zugriffe heute: 1 - gesamt: 2218.