Alternative zum Kühlschmierstoff
Die Minimalmengenschmierung
Bei der Zerspanung metallischer Werkstoffe kommt es auf das Zusammenspiel mehrerer Faktoren an, um eine hohe Produktivität bei möglichst geringer Verschleißzunahme zu erzielen. Neben der Auswahl geeigneter Werkzeuge und Prozessparameter, spielt die Verwendung einer passenden Kühlschmierstrategie eine große Rolle. Die am weitesten verbreitete industrielle Strategie ist die Überflutungskühlung mit Kühlschmierstoff (KSS), einer Emulsion aus Wasser, Öl und weiteren Zusätzen. Die Verwendung von KSS ist jedoch mit Nachteilen verbunden: Die Wartung und Entsorgung ist mit Aufwand und Kosten verbunden, die Werkstücke müssen nach der Bearbeitung gereinigt und getrocknet werden, zudem birgt die Verwendung gesundheitliche Risiken für das Maschinenpersonal. Eine Alternative stellt die Trockenbearbeitung dar.
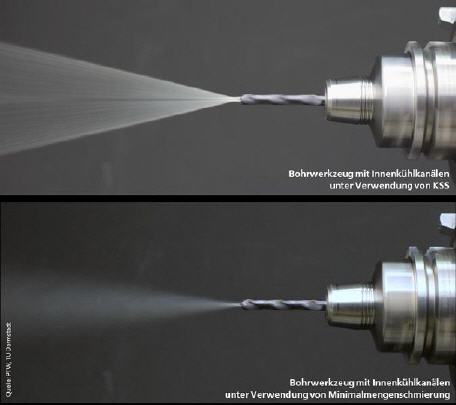
Während der vollständige Verzicht auf eine Kühlschmierung nur für bestimmte Prozesse geeignet ist, stellt die Minimalmengenschmierung (MMS) einen Kompromiss dar, der in den letzten Jahren verstärkt Einzug in das industrielle Umfeld gehalten hat. MMS verwendet eine Kombination aus Schmiermedien (z.B. Ester-Öle o. Fett-Alkohole) und Druckluft, um ein Aerosol zu erzeugen das gezielt in den Kontaktbereich zwischen Werkzeug und Werkstück geleitet wird.
Dort bewirkt es eine Reibungsreduzierung die zu einer Verringerung der Prozesswärme führt. Die Zuführung des Aerosols erfolgt meist durch die Werkzeugspindel und Werkzeuge mit Innenkühlkanälen, die Ver-wendung externer Düsen ist jedoch auch möglich. MMS-Systeme sind in der Regel eigenständig und können nach der Durchführung bestimmter Modifikationen an vielen Werkzeugmaschinen nachgerüstet werden.
MMS ist nicht gleich MMS
Die Systeme können grob in Ein- und Zwei-Kanal-Systeme unterteilt werden. Bei ersteren erfolgt die Erzeugung des Aerosols im MMS-Gerät. Dies hat den Nachteil, dass das Aerosol eine relativ große Distanz bis zum Austritt zurücklegt, was mit strömungstechnischen Problemen, wie bspw. Ablagerungen von Öl an Leitungswänden, verbunden sein kann. Der Vorteil liegt in der einfachen und günstigen Nachrüstbarkeit, die lediglich einer Modifikation der Drehdurchführung bedarf. Zwei-Kanal-Systeme erfordern einen aufwändigeren Umbau der Werkzeugspindel und das Einziehen einer Lanze. Das Medium und die Druckluft werden getrennt (in zwei Kanälen) zur Wirkstelle transportiert, wodurch u. a. eine proesssichere MMS-Versorgung sowie ein verbessertes An-sprechverhalten des Systems erzielt werden.
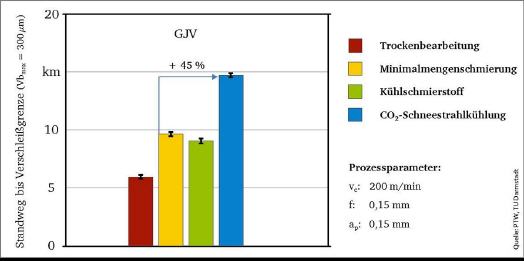
MMS kommt häufig bei Operationen zum Einsatz bei denen die Prozesskühlung eine untergeord-nete Rolle spielt, die auf eine ausreichende Schmierung jedoch nicht verzichten können (z.B. beim Bohren von Aluminium Legierungen). Während der Bearbeitung wirkt ein thermo-mechanisches Belastungskollektiv auf die Werkzeuge, welches zu schnell voranschreitendem Werkzeugverschleiß und schließlich -versagen führt. Die Prozessschmierung vermindert die durch Reibung entstehende Prozesswärme, die die Festigkeit und Härte von Werkzeugen herabsetzt. MMS Medien sind hier aufgrund ihrer im Vergleich zu KSS überlegenen Schmierwirkung im Vorteil.
Wirtschaftliche Vorteile liegen auf der Hand
Der Hauptgrund für die Popularität von MMS in der Industrie liegt in der Ressourcen- und Energie-effizienz der Technologie. Im Vergleich zur Überflutungskühlung verwenden MMS-Systeme einen sehr kleinen Öl-Massenstrom von etwa 5-50 ml/h. Ein Großteil des Öls verdampft während der Bearbeitung, der sich bildende Rauch ist über Abluft- und Filteranlagen einfach aus dem Maschi-nenraum zu entfernen. Eine Entsorgung des Mediums entfällt somit und die gefertigten Bauteile sind quasi trocken.
Die Kosten für die Entsorgung von Kühlschmierstoffen sowie Maschinenausfall-zeiten während des Austauschvorgangs entfallen ebenfalls. Neben den Kostenvorteilen bestehen auch Ressourceneinsparpotenziale: der Verbrauch mineralölhaltiger Kühlschmierstoffe kann um 98 %, der Wasserverbrauch um 80 Prozent und der gesamte Energieverbrauch sowie der Ausstoß von CO2 können um die Hälfte reduziert werden. Der Hauptteil der Energieeinsparpotenziale lässt sich auf die Abwesenheit der für die Überflutungskühlung notwendigen Hochdruckpumpen zurückführen.
Diese erzeugen einen Arbeitsdruck von bis zu 80 bar, während MMS-Systeme in der Regel bei ei-nem Druck von 8 bis 10 bar arbeiten und an das Druckluftnetz der Fertigungsstätten angeschlossen werden. Die reduzierten Energiekosten sind einer der Gründe warum viele Automobilhersteller in ihren Fertigungslinien für Zylinderkurbelgehäuse verstärkt auf MMS setzen. Im Rahmen des Pro-jekts „Lernfabrik – Ressourceneffizienz in der Produktion“ an der TU Darmstadt wurden ein Schu-lungskonzept und ein Praxisleitfaden entwickelt, die interessierten Anwendern die Einsparpotenzi-ale der MMS vermitteln.
Kosteneinsparung ist eine branchenübergreifende Zielvorgabe, so auch in der Produktion. Jedoch muss neben den Ausgaben auch auf die Prozesssicherheit geachtet werden. Andernfalls können die Kostenvorteile durch MMS aufgrund von Prozessunsicherheiten und dadurch erforderlichen zusätzlichen Prozessschritten negiert werden. Die Umstellung eines Fertigungsprozesses auf Mini-malmengenschmierung erfordert umfassende Anpassungsarbeit. Nur dann können eine hohe Pro-zesssicherheit gewährleistet und geforderte Qualitätsanforderungen erfüllt werden. In Untersu-chungen am Fachgebiet für Produktionsmanagement, Technologie und Werkzeugmaschinen (PTW) der TU Darmstadt zur Drehbearbeitung von Vermicularguss (GJV) konnten Standweg Steigerungen durch Anwendung von MMS nachgewiesen werden.
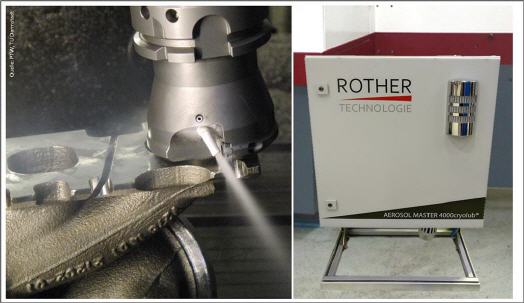
Ein Anwendungsgebiet welches momentan verstärkt Beachtung findet ist der Einsatz von MMS Systemen in der Zerspanung von Titan Legierungen. Diese Materialien kommen aufgrund ihres ausgezeichneten Festigkeits-zu-Dichte-Verhältnis in Aerospace Anwendungen zum Einsatz, zeichnen sich jedoch durch schlechte Zerspanbarkeit aus. Dies hängt unter anderem mit der geringen thermischen Leitfähigkeit der Materialien zusammen, die den Abtransport der Prozesswärme durch die Späne verhindert und zu einer starken thermischen Belastung der Werkzeugschneide führt.
Ein vielversprechender Lösungsansatz für diese Problemstellung besteht in der Verwendung von MMS in Verbindung mit einer kryogenen Kühlung durch CO2. Dieses Konzept kommt bspw. beim Aerosolmaster 4000c System der Rother Technologie GmbH zum Einsatz. Die Schmierwirkung des Aerosols wird durch die Kühlwirkung eines CO2-Schneestrahls ergänzt. Das CO2 liegt hierbei in flüssiger Form, bei etwa 60 bar und Umgebungstemperatur, vor und wird über Leitungen der Austrittsstelle zugeführt. Dort expandiert es schlagartig und bildet einen Schneestrahl mit einer Temperatur von bis -79 Grad Celsius. Untersuchungen am PTW konnten nachweisen, dass der Einsatz der kryogenen Kühlung bei der Titanzerspanung zu einer Senkung der maximalen Prozesstemperatur um bis zu 200 Grad Celsius führt.
Es ist zusammenzufassen, dass in Zeiten in denen Ressourceneffizienz eine immer größere Rolle spielt, die Minimalmengenschmierung vielversprechende Ansätze liefert, um den Spagat zwischen ökonomischen und ökologischen Vorgaben zu meistern. Der Einsatz der Technologie ist jedoch mit nicht zu unterschätzendem Aufwand bzgl. der Prozessgestaltung verbunden. Eine sorgfältige Planung und Umsetzung kann jedoch zu erheblichen wirtschaftlichen und prozesstechnischen Vorteilen führen.
Mehr Informationen zu Rother:
![]() |
Rother Technologie GmbH & Co KG |
![]() |
Rübteile 20 |
![]() |
72574 Bad Urach |
![]() |
Tel.: +49 7125 407 905 |
![]() |
Fax: +49 7125 407 990 |
![]() |
E-Mail: kontakt@rother-technologie.de |
![]() |
www.rother-technologie.de |
War dieser Artikel für Sie hilfreich?
![]() |
![]() |
![]() |
![]() |
![]() |
Bitte bewerten Sie diese Seite durch Klick auf die Symbole.
Zugriffe heute: 1 - gesamt: 7541.