Sicherheit hat beim Fräsen höchste Priorität
MartinMechanic entwickelt neue Roboterzelle
Auch wenn ein Roboter die eigentlichen Aufgaben einer CNC-Fräsmaschine übernimmt, bedeutet das noch lange nicht, dass eine solche Produktionsanlage ohne umfangreiches Sicherheitspaket auskommt. Vor allem, wenn sie zur Bearbeitung von glas- und kohlefaserverstärktem Kunststoff eingesetzt wird. Die MBZ 021005 von MartinMechanic entspricht sogar den Vorgaben für Ex-Schutz-Zonen.
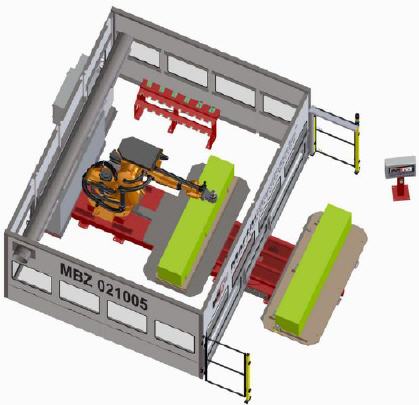
ei dieser neuen Anlagengeneration zum Bohren, Sägen, Fräsen und Entgraten von GFK und CFK wird deutlich, wie Robotik, Bewegung, CNC-Fräsen und SPS-Steuerung bei der Produktion immer mehr ineinandergreifen, ohne dabei die Anforderungen an die bestmögliche Sicherheitstechnik außer Acht zu lassen. Um das zu gewährleisten wurde sie mit der Siemens-Steuerung S7-1500 F ausgestattet. Diese steht für fehlersichere Kommunikation und setzt auf Profinet mit PROFIsafe. Das "F" steht dabei für "fail-safe", was so viel wie "ausfallsicher" bedeutet. Damit haben die Ingenieure die weltweit führende und durchgängigste Technologie für funktionale sichere Kommunikation gewählt.
Überall da, wo GFK- und CFK-Materialien bearbeitet werden, entsteht Feinstaub, der zu einer Verpuffung führen kann. Deshalb wurde die Anlage als Schutz vor elektrostatischer Aufladung komplett geerdet. Schutzeinrichtung und Maschinenschutz bestehen aus Metall, wodurch Funkenbildung und Brandgefahr deutlich reduziert werden. Sogar der Roboter ist explosionsgeschützt.
Um den Werker vor Stäuben zu schützen, geschieht die eigentliche Produktion hinter einer Glasscheibe und unter einem geschlossenen Zellendach. Damit die Feinstäube bei Entnahme der fertig bearbeiteten Kunststoffteile erst gar nicht in die Umluft gelangen können, wurde eine Absauganlage mit einer Leistung von 8000 Kubikmeter pro Stunde in die Arbeitszelle integriert. Durch einen konstanten Unterdruck werden die Luftströme so gelenkt, dass ihr Inneres während des Arbeitsvorgangs permanent von oben nach unten abgesaugt wird.
Über einen Pendeltisch werden die einzelnen Werkstücke dem Sechs-Achs-Roboter in der 20 Quadratmeter großen und 3,20 Meter hohen Arbeitszelle zur Bearbeitung zugeführt. In diesem Fall sind es Überlaufrinnen für Wasserführungssysteme mit einer Länge von 2500 Millimeter und einem Durchmesser von 500 Millimeter. Denkbar wäre auch jede andere Art von Bearbeitungsaufgaben, zum Beispiel an Armaturenbrettern, Dachfensterrahmen oder Bodenplatten.
Der Pendeltisch dreht sich um 180 Grad in den Arbeitsbereich des Roboters. Die Glasscheibe schließt automatisch. Während der Bearbeitung kann ein zweites Werkstück eingelegt und nach Fertigstellung entnommen werden, wodurch eine nahtlose Produktionsfolge gewährleistet ist. Damit die Werkstücke bei der Bearbeitung nicht flattern oder verrutschen, werden sie vorab mit einem Vakuum- Mehrfachgreifer auf dem Pendeltisch fixiert. Dadurch wird auch der Lärm des Fräsvorgangs reduziert. Bei kleineren Bauteilen wird die Vakuum-Vorrichtung abgeschaltet, so dass Werkstücke unterschiedlicher Größe bearbeitet werden können.
Für den automatischen Werkzeugwechsel bedient sich der Roboter aus einem Regal, in dem 20 Werkzeuge bereitgestellt werden. Dieses ist ein wesentliches Element für die Prozessflexibilität. Nach Gebrauch legt er sie dort auch ordnungsgemäß wieder ab. Dazu zählt ein Winkelkopf, mit dem auch schwer zugängliche Stellen erreicht werden und ein Messtaster. Bevor der eigentliche Arbeitsgang startet, greift der Roboter nach dem Messtaster, mit dem er das Bauteil vermisst. Dann passt er sein Programm an, um Toleranzen, die beim Einlegen des Werkstücks entstehen, zu eliminieren.
An den Überlaufrinnen nimmt er Anfräsungen in Form von Aussparungen für Gitter vor. Außerdem werden an der Gehäuseoberseite Löcher mit drei unterschiedlichen Gewindedurchmessern gebohrt. Zum Schluss wird noch die Außenkontur des Werkstücks an der Stirnseite besäumt. Für den kompletten Arbeitsgang erreicht die integrierte Roboterspindel an der sechsten Achse im Spindelschaftträger 30.000 Umdrehungen pro Minute bei einer Leistung von 12 Kilowatt.
Für die Bearbeitung der Außenkonturen werden an den Roboter hohe Anforderungen bezüglich der Bahngenauigkeit gestellt, weshalb die Wahl auf einen Kuka KR 120 R2900 HA (High Accuracy) fiel. Er hat eine Reichweite von 2900 Millimeter und ist deshalb in der Lage, das beschriebene Werkstück von fünf Seiten innerhalb einer Zykluszeit von 30 Minuten zu bearbeiten. Das bedeutet enorme Zeitersparnis.
Da die GFK-/CFK-Stäube abrasiv sind, sind die Führungen gekapselt ausgeführt. Das trägt auch zur Reduzierung der Lärmemissionen bei. Außerdem befinden sich im Zelleninneren glatte Bleche, an denen der Staub nicht haften bleibt. Die Zuführung zur Spindel ist durch ein integriertes Schlauchpaket geschützt. Die Scheiben sind zweiglasig. Die Luftschicht dazwischen dient als zusätzlicher Lärmschutzpuffer. Unterhalb des Pendeltischs befinden sich zwei Bodenscanner. Hält sich der Werker im Gefahrenbereich auf, dreht sich der Pendeltisch nicht.
Herzstück des Fräszentrums, das in fünf Monaten entwickelt und gebaut wurde, ist die SPS-Steuerung mit einer äußerst komfortablen Bedienoberfläche. Durch Eingabe der Koordinaten können sogar neue Bearbeitungsschritte ohne Programmierkenntnisse hinzugefügt werden. Dazu bedient sich der Werker des 19-Zoll-Bedienpaneels, das Fehlbedienungen schon gar nicht zulässt. Durch ihre Vielseitigkeit hat die MBZ 021005 ein enormes Potenzial für die Bearbeitung von Produkten aus den unterschiedlichsten Branchen.
Mehr Informationen zur Friedrich Martin GmbH:
![]() |
Friedrich Martin GmbH & Co KG |
![]() |
Hauptstrasse. 25 |
![]() |
72202 Nagold |
![]() |
Tel.: +49(0) 74 52-84 66-0 |
![]() |
Fax: +49(0) 74 52-84 66-5 66 |
![]() |
E-Mail: info@MartinMechanic.com |
![]() |
www.martinmechanic.com |
War dieser Artikel für Sie hilfreich?
![]() |
![]() |
![]() |
![]() |
![]() |
Bitte bewerten Sie diese Seite durch Klick auf die Symbole.
Zugriffe heute: 1 - gesamt: 1789.