Für erfolgreiche Hartbearbeitung
Hohe Einsparpotenziale dank Prozessoptimierung
Im Werkzeug- und Formenbau hat die Hartbearbeitung längst einen festen Platz und bietet hohes Potenzial gegenüber dem Erodieren. Für sehr gute Zerspanergebnisse müssen jedoch alle Faktoren – von Maschine und Werkzeugen über die CAD-CAM-Programmierung bis hin zu den einzelnen Parametern – perfekt aufeinander abgestimmt sein. Um seine Bearbeitungsstrategie zum Fräsen von gehärteten Stahleinsätzen zu optimieren, holte sich deswegen die Otto Klumpp GmbH die Experten der Zecha Hartmetall-Werkzeugfabrikation GmbH, der GF Machining Solutions GmbH und der Men at Work GmbH an einen Tisch – und erreicht enorme Zeit- und Kosteneinsparungen.
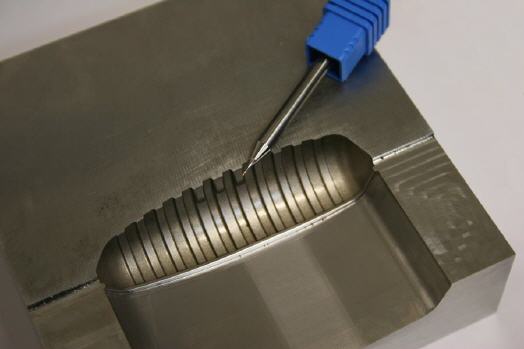
Seit 55 Jahren entwickelt, produziert und vertreibt die Otto Klumpp GmbH aus Balingen-Ostdorf hochwertige technische Spritzgussartikel – vor allem für die Automobilbranche, die Filtertechnik und die Medizintechnik. Wer in diesen Branchen erfolgreich sein will, bei dem sind höchste Präzision und ausgezeichnete Oberflächenqualitäten oberstes Gebot. Deswegen setzt das familiengeführte Unternehmen auf eine hohe Fertigungstiefe und betreibt einen internen Werkzeugbau, bei dem Werkzeuge bis zu 7 Tonnen Gesamtgewicht und Kavitätenzahlen von 1- bis 32-fach hergestellt werden können.
Im Zuge einer kompletten Umstrukturierung entschied sich Klumpp, den Werkzeugbau zu modernisieren und weiter zu automatisieren. Dazu investierten die Ostdorfer in neue Technologien zum Fräsen und Erodieren und beauftragte GF Machining Solutions mit der Installation einer Linearzelle zur vollautomatischen Elektrodenfertigung, Senkerosion und Hartbearbeitung, bestehend aus einem 5-Achs-Bearbeitungszentrum Mikron HSM 600U LP, einer Senkerodiermaschine AgieCharmilles FORM 3000 HP sowie einem Linearroboter von System 3R inklusive 3R Cellmanager. Da sich die Anlage schnell bewährte, wurde sie innerhalb kurzer Zeit um das 3-Achs-Bearbeitungszentrum Mikron HSM 400 LP erweitert und eine Zeiss Duramax Messmaschine integriert.
„Bislang setzten wir die Linearzelle hauptsächlich zum Fräsen von Graphitelektroden und zum Erodieren ein. So konnten wir hier unser Knowhow nahezu perfektionieren: Unser eingespieltes Drei-Mann-Team erreicht eine sehr hohe Prozesssicherheit. Die Anlage läuft ohne Eingriff bei Auslastung sogar bis zu fünf Tage am Stück – die meiste Zeit davon im mannlosen Betrieb“, so Andreas Fauser, Projektleitung bei der Otto Klumpp GmbH.
Um die Kompetenzen in der automatisierten Hartbearbeitung weiter ausbauen und die hartgefrästen Stahleinsätze genauso einwandfrei wie die Graphitelektroden zu fertigen, rief Klumpp einen zweitägigen Workshop ins Leben. Zusammen mit dem Werkzeugspezialisten Zecha aus Königsbach-Stein, dem Schweizer Maschinenhersteller GF Machinig Solutions sowie dem CAD/CAM und VISI-Experten Men at Work aus Bietigheim stellte das Unternehmen seine Strategien und Prozessabläufe zur vollautomatischen Hartbearbeitung auf den Prüfstand.
Dafür wurden Ausschnitte eines medizinischen Gehäuses gefertigt, bei denen die Form der Außendeckel in gehärteten Stahl (1.2343) mit 52 HRC gefräst wurde. Es sollte höchste Prozesssicherheit auf der Fertigungsanlage erreicht werden verbunden mit ausgezeichneten Oberflächengüten, sehr guter Maßhaltigkeit in einem Toleranzbereich von 0,005 mm sowie langen Standzeiten der Werkzeuge – und das alles ohne Eingriffe des Bedieners. Eine Herausforderung, der das Team souverän begegnete, und die Aufgabenstellung gekonnt umsetzte.
Bei den Werkzeugen legt Klumpp den Fokus auf High-End-Produkte. Bereits seit Jahren verwenden die Werkzeugbauer die hochwertigen Graphitfräser zur Elektrodenfertigung und das komplette Hartfräsprogramm von Zecha. „Um das das gestellte Ziel zu erreichen, setzten wir auf dem Workshop die neuen PEACOCK-Fräser und die vierschneidigen Werkzeuge der Serie 597T4 in Durchmessern von 0,5 bis 8 mm mit Längen bis zu 8xD ein. Die Bearbeitungsparameter konnten wir eins zu eins aus Zecha-Schnittdatenrechner für unsere Kunden übernehmen“, erklärt Klaus Bruder, Anwendungstechniker bei Zecha. Beide Fräserserien überzeugen durch ihre hohe Formgenauigkeit, eine optimierte Geometrie, neuste Beschichtungstechnologie und beste Qualität und sind damit prädestiniert für die hohen Anforderungen der Hartbearbeitung.
Durch die vier Schneiden der 597T-Torusfräser – erhältlich in Durchmesser 0,8 bis 12 mm – wird ein besonders hohes Abtragsvolumen erreicht bei einem deutlichen Standzeit-Plus in Materialien über 50 HRC. Die PEACOCK Kugelfräser – Durchmesser 0,2 bis 12 mm lieferbar – besitzen eine optimierte Stirngeometrie, die es ermöglicht, die Späne schneller aus der Gefahrenzone zu entsorgen – eine lebenserhaltende Maßnahme bei der Hartbearbeitung.
GF Machining Solutions gehört zu den weltweit führenden Maschinenherstellern für den Formen- und Werkzeugbau sowie für die Fertigung von Präzisionsteilen. Hochwertige Maschinen zum Senkerodieren, Drahtschneiden, Hochgeschwindigkeits- und Hochleistungsfräsen gehören genauso zum Portfolio wie Spann- und Palettiersysteme, 3D-Lasermaschinen für Oberflächenstrukturierung und komplette Automationslösungen.
„Unsere Serie Mikron HSM, von der wir sowohl unser 5-Achs- als auch unser 3-Achsbearbeitungszentrum in die Linearzelle integriert haben, eignet sich hervorragend für den Werkzeug- und Formenbau sowie für die Mittel- und Kleinserienproduktion hochwertiger Bauteile. Die Maschinen bringen die nötige Flexibilität mit, um sowohl Graphit als auch gehärteten Stahl mit höchster Präzision und besten Oberflächengüten zu bearbeiten“, so Johann Neustätter, Anwendungstechnik Fräsen und Automationslösungen bei der GF Machining Solutions GmbH aus Schorndorf.
Ein reibungsloser Ablauf der Prozesse – nicht zuletzt bei der Hartbearbeitung – ist stark von der CAM-Programmierung abhängig. Die richtige Software ist dabei ein entscheidender Faktor für eine erfolgreiche Zerspanung. Damit kam den VISI-Experten von Men at Work schon bei der gemeinsamen Konstruktion der Bauteile und der NC-Programmierung eine entscheidende Rolle zu. „VISI bietet mit einer einzigartigen Kombination von Anwendungsmöglichkeiten eine Komplettlösung für den Werkzeug- und Formenbau – von der Konstruktion komplexer Bauteile bis zur Programmierung umfangreicher Bearbeitungsstrategien, inklusive HSC-Optionen. Anwendungen für Draht- und Senkerodieren komplettieren die CAM-Funktionalität. Optimale Voraussetzungen für Klumpp“, so Johannes Ott, Leiter NC Technik bei Men at Work.
Andreas Fauser: „Unser Team für den Workshop war gut gewählt, um die automatisierte Hartbearbeitung auf den richtigen Weg zu bringen. Wir konnten unsere Prozesse entscheidend verbessern, unsere Horizonte über die bewährten Abläufe hinaus erweitern und damit auch die Prozesssicherheit bei der Hartbearbeitung signifikant erhöhen. Und das Ergebnis kann sich sehen lassen!“ Beim Vergleich der gefrästen und erodierten Bauteile mit Blick auf Prozess, Oberflächengüte, Maßhaltigkeit, Laufzeiten, Einsatzzeiten und Prozesssicherheit zeigten sich enorme Einsparpotenziale: Beim nachfolgenden Hochglanz-Polieren zeigte sich zudem ein weiterer Vorteil der Komplettbearbeitung mittels HSC-Fräsen. Die Qualität der gefrästen Oberfläche ist so gut, dass bei der Nachbearbeitung gegenüber einer erodierten Oberfläche enorme Einsparungen möglich sind.
Damit kann Klumpp künftig nicht nur auf eine ausgezeichnete vollautomatische Fertigung kleiner und tiefer Geometrien mittels Graphitelektroden zurückgreifen, sondern dank der neu abgestimmten Prozesse auch das volle Potenzial der Hartbearbeitung in die Waagschale werfen. Ein hervorragender Ausgangspunkt für eine wirtschaftliche Produktion der hochwertigen Spritzgussartikel.
Mehr Informationen zur ZECHA GmbH:
![]() |
ZECHA Hartmetall- Werkzeugfabrikation GmbH |
![]() |
Benzstraße 2 |
![]() |
75203 Königsbach-Stein |
![]() |
Tel.: +49 (0) 72 32 / 30 22-0 |
![]() |
Fax: +49 (0) 72 32 / 30 22-25 |
![]() |
E-Mail: info@zecha.de |
![]() |
www.zecha.de |
War dieser Artikel für Sie hilfreich?
![]() |
![]() |
![]() |
![]() |
![]() |
Bitte bewerten Sie diese Seite durch Klick auf die Symbole.
Zugriffe heute: 2 - gesamt: 2955.