Smart Data statt Big Data
SKF arbeitet an vorausschauender Instandhaltung
Das Sammeln von Prozessdaten ist eine bedeutende Grundlage für vorbeugende Maßnahmen zur Instandhaltung von Maschinen. Die korrekte Verwendung bzw. Interpretation der gesammelten Daten ist aber noch wichtiger. Am besten wäre es, wenn man all dies automatisieren könnte. SKF arbeitet daran.
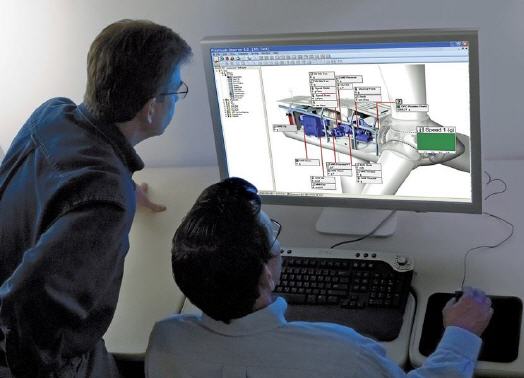
„Industrie 4.0“ ist ohne „Big Data“ nicht umsetzbar. Allerdings hilft bloßes Datensammeln nicht wirklich weiter: Mehrwert liefern diese Datenmengen erst dann, wenn sie sinnvoll genutzt werden. Deshalb geht es immer mehr darum, Big Data in „Smart Data“ zu verwandeln.
Big Data wird meist als große Menge von Daten aufgefasst, die auf „traditionelle“ Art und Weise nicht mehr gespeichert und ausgewertet werden können. Im Industriesektor entstehen solche Datenmenge vor allem bei der Messung von Betriebsparametern und -zuständen von dort eingesetzten Maschinen. Während solche Daten meist in strukturierter Form vorliegen, entstehen zusätzlich häufig auch sogenannte „unstrukturierte“ Daten; wie etwa Text-, Bild-, Video- und Audiodateien. Derartig unterschiedliche Formate „unter einen Hut“ kriegen zu müssen, verschärft die Komplexität von Big Data. Hinzu kommt, dass ständig steigende Datenvolumina, -geschwindigkeiten, -varianten und -zuverlässigkeiten neue Datenbanksysteme erfordern, um das angehäufte Material überhaupt noch bündeln zu können.
Erfahrung unerlässlich
Das reine Abspeichern dieser Daten verursacht jedoch zunächst nur Kosten und keinen Mehrwert. Daher gilt es, die Datensammlung zu verstehen und dadurch in Smart Data umzuwandeln. Dazu ist die Anreicherung der Rohdaten mit Wissen und Erfahrung unerlässlich. Dieser Prozess wird im industriellen Kontext vor allem auf Betrieb und Instandhaltung angewandt: Das Sammeln großer Mengen von Prozessdaten samt deren richtiger Interpretation versetzt die Unternehmen in die Lage, ihre betrieblichen Abläufe zu optimieren. Wer die Daten korrekt sichtet und auswertet, kann beispielsweise die Leistung seiner Maschinen verbessern oder ihre Lebensdauer verlängern, indem die Betriebsbedingungen auf Grundlage der entsprechenden Erkenntnisse angepasst werden.
Im einfachsten Fall gelangt ein erfahrener Bediener durch Auswertung mehrerer Messwerte – z. B. Temperatur, Druck und Schwingung – zu einer Diagnose. Aus der fachmännischen Analyse dieser Daten lassen sich Programme zur zustandsabhängigen Überwachung bzw. zur vorbeugenden Instandhaltung ableiten. Anders ausgedrückt: Wer die richtigen Messungen durchführt und Abweichungen von definierten Toleranzen frühzeitig erkennt, kann rechtzeitig Gegenmaßnahmen ergreifen und dadurch einen reibungsloseren Betrieb sicherstellen. In der Praxis funktioniert das beispielsweise durch die Schwingungsüberwachung von Lagern: So lässt sich anhand der gesammelten Daten die Lebensdauer der betreffenden Maschine verlängern bzw. ihre Zuverlässigkeit erhöhen.
Schneller gepaart mit clever
Je komplexer die Anlage ist, desto schwieriger wird es allerdings selbst für Experten, aus der Masse an Daten die relevanten Informationen zu extrahieren. Diese Erfahrung hat vor nicht allzu langer Zeit auch das Formel 1-Team der Scuderia Ferrari gemacht: Zwar verfügt der Rennstall über moderne Prüfstände, aber manche während der Tests auftauchenden Phänomene blieben den Ingenieuren ein Rätsel. Da eine Online-Überprüfung von Hochfrequenzdaten nicht zur Verfügung stand, artete die Fehlersuche zu einem langwierigen Prozess aus – und machte es letztlich unmöglich, Prognosen für die Lebensdauer von Komponenten auf Basis von Trendwerten zu erstellen.
Um Abhilfe zu schaffen, installierten Experten von SKF ein speziell „getuntes“ Überwachungssystem auf Basis der unternehmenseigenen IMx-Plattform. Das System überwacht kontinuierlich das Schwingungsverhalten von Antriebskomponenten in der Prüfkammer und verarbeitet bis zu 100.000 Messungen pro Sekunde. Diese Daten werden bis zu 20 mal pro Sekunde zusammengefasst, um sie in „überschaubare Stücke“ aufzuteilen, was die Analyse erleichtert. Seit die SKF Lösung aus „Big and Fast Data“ leichter verständliche Smart Data macht, können sich Ingenieure der Scuderia Ferrari nach eigener Auskunft „viel mehr auf Ergebnisse anstatt auf Daten” konzentrieren.
Automatisiertes Lernen
Das Beispiel zeigt, dass strukturierte Daten durchaus schon automatisch interpretiert werden können: Wenn sich ein bestimmter Parameter verändert, erkennen entsprechende Systeme selbsttätig, ob „noch normales“ bzw. „bereits fehlerhaftes“ Verhalten vorliegt. Zum Teil sind auch schon automatisierte Korrekturmaßnahmen bzw. Diagnosen möglich.
Anstatt jedoch solche Systeme manuell für jeden spezifischen Anwendungsfall neu zu programmieren, kommen vor allem selbstlernende Verfahren aus dem Bereich der Künstlichen Intelligenz zum Einsatz. Dem System werden hierfür Beispiele von normalem und fehlerhaftem Verhalten der Anlage gezeigt. Anhand intelligenter Algorithmen „erlernt“ das System automatisiert, diese beiden Fälle in Zukunft zu unterschieden. Je mehr Daten dem Algorithmus dabei zur Verfügung gestellt werden, desto höher ist dessen Genauigkeit – was wiederum die Wichtigkeit des Datensammelns erklärt.
Blick nach vorn
Erste Ansätze dazu gibt es mittlerweile. Beispielsweise können manche industriellen Bildverarbeitungssysteme nicht nur Defekte erkennen, sondern sogar deren Schwere beurteilen. Dieses Prinzip kommt bereits in unterschiedlichsten Anwendungen zum Einsatz; etwa zur Prüfung von Produkten oder zum Zwecke der Qualitätssicherung im laufenden Prozess.
Inzwischen befinden sich bei SKF ähnliche Konzepte für weitaus komplexere Aufgaben in der Entwicklung. In nicht allzu ferner Zukunft werden intelligente Systeme in der Lage sein, Massen von strukturierten und unstrukturierten Daten logisch zu korrelieren und korrekt zu interpretieren. Dadurch werden sie automatisch die Schadensursache identifizieren können. Ein solches System könnte zum Beispiel ein aktuelles Bild mit einem „historischen“ vergleichen oder Daten direkt aus einem schriftlichen Bericht extrahieren. Mit jedem Bild, jedem Text, jeder Audio- oder Videoaufnahme wird ein solches System „hinzulernen“ und sich damit weiter verbessern. Gleichzeitig können sich die Experten auf solche Probleme konzentrieren, die dem System noch nicht bekannt sind, und es später mit neuen Erkenntnissen füttern.
Prognosen per Programm
Natürlich sind noch diverse Hürden zu überwinden, bevor aus dieser Vision auch Wirklichkeit wird. Zwar ist die erforderliche Hard- und Software im Grunde schon vorhanden; allerdings können nach wie vor nicht sämtliche Systeme von verschiedenen Herstellern nahtlos miteinander kommunizieren – ein seit längerem bekannter Hemmschuh. Immerhin gibt es Anzeichen dafür, dass Datenzugang, -austausch und -interoperabilität immer offener werden. Triebfeder dafür sind insbesondere die Endverbraucher, die zunehmend danach verlangen, dass unterschiedliche Systeme eine gemeinsame Sprache sprechen. Diesem Trend wird sich die Industrie nicht lange entziehen können.
Im industriellen Umfeld bedeutet der Umstieg von Big Data auf Smart Data den Übergang von dem Wissen darüber, was passiert, zu dem Wissen darüber, was passieren wird, warum es passieren wird und welche Optionen man hat. So kann die wahrhaft vorausschauende Instandhaltung der Zukunft dazu beitragen, die Effizienz von unzähligen Industrieanlagen auf dem gesamten Globus signifikant zu steigern. SKF arbeitet daran – beispielsweise mit mobilen Sensoren zur Datenerfassung, ausgeklügelter Software zur Datenanalyse und einem weltumspannenden Netzwerk von Fernüberwachungs- und Diagnosezentren.
Mehr Informationen zur SKF GmbH:
![]() |
SKF GmbH |
![]() |
Gunnar-Wester-Straße 12 |
![]() |
97421 Schweinfurt |
![]() |
Tel.: +49 (0) 97 21 56-0 |
![]() |
Fax: +49 (0) 97 21 56-60 00 |
![]() |
www.skf.com |
War dieser Artikel für Sie hilfreich?
![]() |
![]() |
![]() |
![]() |
![]() |
Bitte bewerten Sie diese Seite durch Klick auf die Symbole.
Zugriffe heute: 1 - gesamt: 1912.