Experteninterview zum Thema Leichtbau
NextGen Spaceframe
Fahrzeugkarosserien von morgen, speziell im Hinblick auf alternative Antriebssysteme in variantenintensiven Kleinserien, müssen nicht nur leichter, sondern vor allem hochflexibel konzipiert werden. Die Folge ist eine steigende Anzahl an Fahrzeugderivaten, die nach anpassungsfähigen und wirtschaftlich zu fertigenden Karosseriekonzepten verlangen. Die additive Fertigung könnte in absehbarer Zeit ganz neue denkbare Wege offerieren.
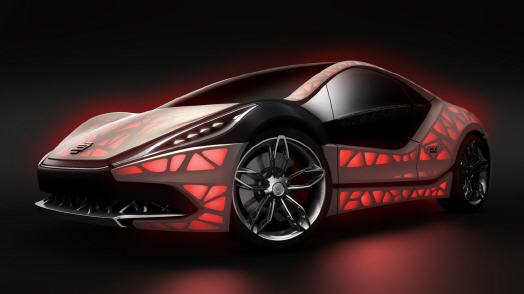
In einem Gemeinschaftsprojekt zeigten die EDAG Engineering GmbH (Wiesbaden, D), die Laser Zentrum Nord GmbH (Hamburg, D), die Concept Laser GmbH (Lichtenfels, D) und die BLM Group (Cantù, IT) mit dem bionisch optimierten, hybrid gefertigten Spaceframe eine neue Perspektive auf, wie ein wandelbares und flexibel zu fertigendes Karosseriekonzept realisiert werden kann, um die zunehmende Fahrzeugvarianz durch die Vielzahl von Antriebsvarianten und Laststufen beherrschbar zu machen.
Kombiniert werden generativ hergestellte Karosserieknoten und intelligent bearbeitete Profile. Die Knoten können dank generativer Fertigung hochflexibel und multifunktional gestaltet werden, um z.B. unterschiedliche Fahrzeugvarianten ohne zusätzliche Werkzeug-, Betriebsmittel- und Anlaufkosten „On Demand“ produzieren zu können. Als Verbindungselemente dienen Profile aus Stahl. Auch diese können durch unterschiedliche Wandstärken und Geometrien individuell und einfach den vorgegebenen Laststufen angepasst werden.
Der NextGen Spaceframe ist Teil des EDAG Concept Car „Light Cocoon“, ein kompakter Sportwagen mit einer bionisch gestalteten und generativ hergestellten Fahrzeugstruktur, überzogen mit einer Außenhaut aus wetterbeständigem Textil.
Wir sprachen mit allen beteiligten Projektpartnern über den neuen Ansatz eines fertigungsoptimierten Leichtbaurahmens.
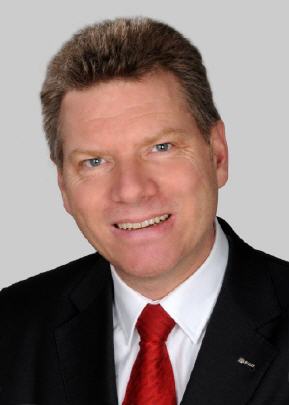
Dr.-Ing. Martin Hillebrecht
Leiter Competence Center Leichtbau, Werkstoffe und Technologien, EDAG Engineering GmbH, Wiesbaden
Redaktion: Wird es im Bereich Automotive schwieriger, die Nachhaltigkeitsziele zu erreichen? Wenn ja, worin liegt der Beitrag der hybriden NextGen Spaceframe-Bauweise von EDAG?
Martin Hillebrecht: Die Automobilhersteller entwickeln unter Hochdruck Fahrzeuge mit Produktionsstarts zwischen 2015 und 2020. Die neuen Karosserien sollen weniger wiegen, eine hohe Steifigkeit für ein hervorragendes Fahrverhalten aufweisen und anspruchsvolle Crash-Lastfälle erfüllen. Höhere Kundenanforderungen, denken wir an alternative Antriebe, Komfort, Funktionalität und Vernetzung, sowie auch neue Sicherheitsanforderungen der internationalen Gesetzgeber wirken als Verkaufskriterien trotz aller ambitionierten Gewichtsziele dem Leichtbau entgegen. Kernidee eines visionären und bionischen Spaceframes wäre es aus meiner Sicht u. a., nur dort Werkstoffe einzusetzen, wo es für Funktion, Sicherheit und Steifigkeit benötigt wird. Also ein reduzierter Ansatz nach dem Motto „weniger ist mehr“. Durch werkzeuglose generative Fertigung und das werkzeugarme Profilierverfahren könnten zukünftig vielleicht sogar alle Karosserievarianten laststufengerecht ausgelegt und „on demand“ gefertigt werden. Wie auch immer, hier liegen Potenziale.
Sergio Raso: Nachhaltigkeit ist das führende Ziel der Automobilindustrie. Verschiedene Kerntechnologien für die Zukunft der Automobilproduktion wurden bisher untersucht. Die Rahmenkonstruktion des EDAG Light Cocoon vereinigt viele dieser Technologien in einem Ansatz. So z. B. Hybridleichtbauweise zur Gewichtsreduzierung und Kraftstoffeffizienz, die Verwendung von additiven Verfahren für ein bionisch optimiertes Design und die Verwendung von Rohren und Profilen für eine hochflexible Fertigung des Fahrzeugrahmens.
Redaktion: Wie das Beispiel Elektrofahrzeuge in Europa zeigt, braucht es von ersten Innovatoren, wie den Pionieren Hayek (Ur-Smart) oder Tesla Motors (USA), bis hin zu adaptierten Innovationen lange Zeiträume. Ist die Automobilindustrie wirklich reif für völlig neue Sichtweisen auf ihre Produkte?
Martin Hillebrecht: Ein möglicher Einstieg in neue Fertigungsstrategien, wie dem Leichtbau, wird erfahrungsgemäß häufig über kleine Stückzahlen im Luxus- und Supersportsegment möglich. Diese Kundschaft identifiziert sich deutlich mehr mit Leichtbau, E-Mobilität und technischen Innovationen als im Massengeschäft. Diese „Innovatoren“ sind bereit, zugunsten der Fahrdynamik, des Komforts, der Sicherheit und aus ökologischen Motiven heraus wesentlich höhere Herstellkosten zu akzeptieren. Bei entsprechendem Potenzial der Technologie und bei fortschreitender Technologieentwicklung für die automobile Massenproduktion können dann die Prozesse aus der Nische hin zu größeren Stückzahlen transferieren. Das erfordert aber durchaus seine Zeit, nachhaltige Investitionen in die Zukunft der Unternehmen und viel technische Kompetenz. Ich will nicht gelten lassen, von „langen Zeiträumen“ zu sprechen, aber es braucht Zeit für die Adaptation neuer Technologien.
Sergio Raso: In der Automobilindustrie hängt die Zahl der Arbeitsplätze in hohem Maße von Fertigungsmethodik und -strategie ab. Sie bestimmen maßgeblich die Kostenstrukturen, die erzielbaren Margen und den Erfolg. Diese Faktoren bestimmen unsere Sichtweise auf Mobilität und nicht zuletzt auch den Wohlstand vieler Volkswirtschaften. Um das erreichte Niveau der automobilen Mobilität zu erhalten, hat die Automobilindustrie kontinuierlich in technologische Fortschritte ihrer Automobile und die dahinter stehenden Produktionsprozesse investiert. Die Investitionen in Forschung und Entwicklung sind daher obligatorisch, und auch wir von der BLM Group sind auf diesem Pfad der Innovation und Fortentwicklung.
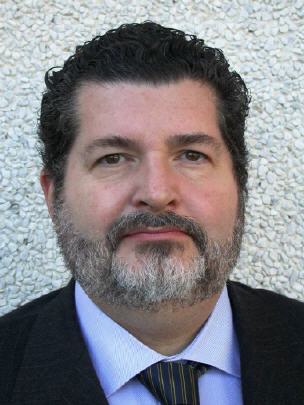
Sergio Raso
Strategischer Marketingleiter - Laser Produkte, BLM Group, Cantù (I)
Redaktion: Stichworte Ressourcenschonung und „grüne Technologie“. Wie sieht dies der Automobilbauer?
Martin Hillebrecht: Dank intelligentem Leichtbau, vor allem in Mischbauweise, sollen die Fahrzeuge je nach Marktsegment um etwa 100 kg leichter gegenüber den jeweiligen Vorgängern werden. Hierbei können in der Karosserie und den Anbauteilen noch weitere 10 bis 20 % an Gewicht eingespart werden. Vielen Herstellern ist die Trendumkehr der Gewichtsspirale bereits im Ansatz gelungen. Fakt ist aber auch: Höhere Kundenanforderungen an alternative Antriebe, Komfort, Funktionalität und Vernetzung sowie auch neue Sicherheitsanforderungen der internationalen Gesetzgeber wirken als Verkaufskriterien trotz aller ambitionierten Gewichtsziele dem Leichtbau entgegen. Es ist ein Spagat, den wir da versuchen.
Sergio Raso: Lösungen für „grüne Technologien" und intelligentes Energiemanagement sind stark abhängig von Regierungen durch deren politische Zielvorgaben, Gesetze und sicherlich auch durch die gesetzten Anreize. Diese Zielausrichtung, blicken wir einmal auf den US-Staat Kalifornien, sind ein immer augenfälliger Fakt, dem wir uns stellen müssen und nicht entziehen können. Die Automobilhersteller nehmen diese Anforderungen an und sehen politische Zielvorgaben auch als Motor der Innovation. Ergo: Es gibt also ein gemeinsames Interesse von Politik und Herstellern. Zusammen mit den bekannten Lösungen für das Energiemanagement, wie beispielsweise der Entwicklung von Elektrospeichern und -antrieben, oder auch den Fahrzeugen mit Brennstoffzellen, können auch die Fertigungsprozesse stark an die Visionen der „grünen Technologie" herangeführt werden. Das Fertigungsdesign mit vollelektrischen Biegemaschinen, Laserschneidanlagen mit hohem Wirkungsgrad oder das Laserschmelzen sind Beispiele für das Engagement der BLM Group hin zu einer „grüneren“ Zukunft. Der Pfad hin zu intelligenter Ressourcenschonung und Nachhaltigkeit ist ein unumkehrbarer Megatrend. Alle Akteure der Automobilindustrie haben das in den Köpfen.
Redaktion: Skizzieren Sie bitte kurz die Vor- und Nachteile konventioneller Karosseriebauweisen.
Claus Emmelmann: Aktuelle Karosserien sind intelligente, last- und crashoptimierte Konstruktionen, deren Material- und Konstruktionskonzepte einen hohen Reifegrad erlangt haben. Sowohl im Leichtbau als auch beim Insassenschutz. Die eingesetzten traditionellen, werkzeugbasierten Fertigungsverfahren stoßen hinsichtlich der Flexibilität und Realisierbarkeit an ihre Grenzen. Das Laser Zentrum Nord konnte mit den Projektpartnern durch die bionischen, der Natur nachempfundenen, Konstruktionsprinzipien diese Grenzen konzeptionell überwinden. Das Spaceframe-Konzept versucht, das „beyond limits“ in Bezug auf Produkt, Fertigung und Automation aufzuzeigen.
Martin Hillebrecht: In einer typischen Karosserie in Schalenbauweise sind Beplankungen, Verstärkungen, Aufnahmebleche und Profile mit Fügetechnik verbunden. Alle Bauteile wirken als Schalen. Die geforderte Steifigkeit wird hierbei durch Blechquerschnitte erzielt. Der Vorteil sind die geringen Herstellkosten in einer industriellen, weltweit einheitlichen Massenproduktion. Neben kostengünstigen Halbzeugen aus Blech kommen bewährte und robuste Technologien wie das Umformen und das Punktschweißen zum Einsatz. Nachteil ist hier, dass Werkzeug- und Anlageninvestitionen sich nur über große Stückzahlen rechnen und Variantenvielfalt erschweren. Zudem sind werkzeuggebundene Teile mit Werkzeugkosten verbunden, und man braucht Vorbereitungszeiträume für die Werkzeugtechnik. Schließlich müssen die Werkzeuge über den Lebenszyklus des Produktes abrufbar sein. Eine Spaceframe-Bauweise besteht aus geschlossenen Hohlprofilen, die über Knoten miteinander verbunden sind. Flächige Bauteile wie das Dach nehmen die Schubkräfte auf. Mit einem Spaceframe-Konzept einhergehend können zukünftig neue Werkstoffe verwendet werden. Das wäre zu untersuchen. Generell gilt aber schon heute, das Konzept ermöglicht dem Hersteller signifikante Gewichtseinsparung und hohe Verwindungssteifigkeit bei hoher Wirtschaftlichkeit für Fahrzeuge mit eher kleineren Stückzahlen.
Sergio Raso: Ein großer Vorteil der herkömmlichen Konstruktionen von Fahrzeugrahmen ist das Zusammenspiel konsolidierter Technologien, die heutzutage für die Herstellung und die Montage des Rahmens zur Verfügung stehen. Heute müssen Fertigungslinien in der Regel verschiedene Prozesse und Phasen vor der Endmontage des Fahrzeugrahmens abbilden. Der Nachteil dieses Konzepts ist der Aufwand und die begrenzte Flexibilität im Montage-Workflow. Hier sind neue Ideen und, daraus abgeleitet, wirtschaftliche und flexible Konzepte für die zukünftige Fertigung gefordert. Ich möchte dies so formulieren: Es sind große Herausforderungen.
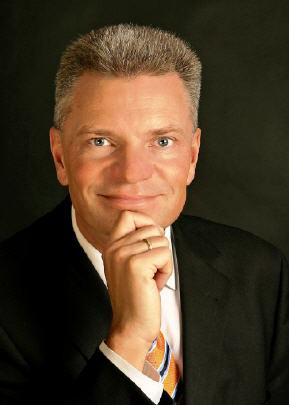
Prof. Dr.-Ing. Claus Emmelmann
CEO, Laser Zentrum Nord GmbH, Hamburg
Redaktion: Welche Merkmale und neuen Verfahren wurden beim NextGen Spaceframe-Konzept aufgezeigt?
Martin Hillebrecht: Der gemeinsam erarbeitete Stahl-Spaceframe-Knoten kombiniert generativ gefertigte Knoten auf Basis des „selektiven Laserschmelzens“ mit intelligent bearbeiteten Profilen in Hybridbauweise. Dieser Ansatz verspricht eine extreme Flexibilisierung der Produktion. Und er verspricht eine denkbare hohe Variantenintensität bei null Euro für weitere Investitionen in Vorrichtungen, Werkzeuge und Anlagentechnik pro Fahrzeugvariante. Ich denke, dass sich eine hohe Modellvielfalt ergeben kann, weil restriktive Kostenhürden entfallen. Zudem erlaubt die generative Fertigung im Hinblick auf die eingesetzten Werkstoffe eine größtmögliche Ressourceneffizienz. Außerdem ergeben sich bionische und lastpfadoptimierte Strukturen, die mit anderen Fertigungsverfahren geometrisch gar nicht herstellbar sind.
Claus Emmelmann: Das Spaceframe-Konzept vereint die Vorteile des 3D-Drucks, wie Flexibilität und Leichtbaupotenzial, mit der Wirtschaftlichkeit bewährter konventioneller Profilbauweise. In beiden Technologien spielt der Laser die zentrale Rolle. Die bionisch optimierten Knoten ermöglichen einen derzeit maximalen Leichtbau und einen hohen Grad an Funktionsintegration. Sowohl die Knoten als auch die Profile können ohne Zusatzaufwand auf neue Geometrien und Lastanforderungen angepasst werden. Sie bieten so die Möglichkeit, jedes einzelne Teil laststufengerecht auszulegen – und nicht wie bisher die Dimensionierung der Bauteile an der größten Motorisierung auszurichten. Der Grundgedanke ist also eine Rahmenbauweise, die optimal auf die Anforderung der Modellvariante abgestimmt werden kann.
Sergio Raso: Das Hauptmerkmal des NextGen Spaceframe-Konzepts ist eine konsequente Ausrichtung auf extreme Flexibilität von Prozessen zur Herstellung und Montage. Mit additiven Fertigungstechnologien sowie Profilen, die leicht gebogen und im 3D-Laserschnitt hergestellt werden, liegen mögliche Antworten für ein Plus an Flexibilität. Additiv hergestellte Freiform-Knoten ermöglichen neue Design-Lösungen und eine Vielzahl von Varietäten an Modellen. Die Einbeziehung von bionischen Konstruktionen, Hohlbauweise oder Gitterstrukturen ermöglicht ein optimiertes mechanisches Verhalten des Rahmens. Die Integration von Merkmalen der Kraftaufnahme in den Profilen und Knoten eröffnet eine kontrollierte Verformung des Rahmens und eine erhöhte Sicherheit der Passagiere. Die Einbeziehung des AM und die Gestaltung von Schnittstellen für das Laserschweißen optimiert die Fertigung. Also erstens Flexibilität, zweitens Sicherheit und drittens die Vereinfachung von Prozessen sind einige Beispiele für die Vorteile dieses Ansatzes.
Frank Herzog: Ich möchte hier nur einwerfen, dass die Hybridbauweise auch in anderen Branchen bereits zum Einsatz kommt. Relativ einfache oder überlange Geometrien, wie hier vielleicht die Profile, werden mit der klassischen Zerspanung hergestellt, und komplexere Geometrien entstehen dann additiv. Das Phänomen bildet die Wirtschaftlichkeit ab. Mischbauweise ist in vielen Bereichen interessant, wenn es gilt, eine Brücke zwischen Funktion und Wirtschaftlichkeit zu bauen.
Redaktion: Welche neuen Fertigungsstrategien und Automationspotenziale ergeben sich zukünftig daraus? Welche Potenziale sehen Sie in Konstruktion und Fertigung?
Claus Emmelmann: Die Potenziale der Konstruktion sind in der flexiblen, laststufengerechten Auslegung zu sehen. Und in der Chance, mit den gezeigten bionischen Strukturen einen maximal möglichen Leichtbau zu betreiben, so wie er bisher noch nicht umsetzbar war. Am Laser Zentrum Nord entwickeln wir Gestaltungsrichtlinien, um bionische Vorbilder, wie z. B. eine Bambus- oder Vogelknochenstruktur, in solch anspruchsvolle technische Leichtbauteile mit Gewichtseinsparungen von in der Regel 30 bis 50 % erfolgreich umzusetzen. „Bionisches Konstruieren“, wie es mit Additive Manufacturing möglich wird, zeigt zahlreiche Optionen auf. Die Fertigung profitiert mehrfach von den neuen Fertigungsverfahren: Nicht nur die investitionsintensiven Werkzeuge entfallen, sondern es können auch flexible Kleinserien oder auch Bauteiländerungen innerhalb des Modellzyklus ohne Mehraufwand sofort abgebildet werden.
Martin Hillebrecht: Außerdem sind die Reaktionsfähigkeit auf Stückzahlschwankungen sowie „updatefähige“ Bauteile während eines Fahrzeuglebenszyklus im Sinne einer „lernfähigen Industrie 4.0“ hervorzuheben. Das sind ganz neue Ideen für die Branche. Wir sind selbst sehr gespannt, wie unsere Kunden hierauf reagieren werden.
Sergio Raso: Das neue Konzept bedeutet für die Entwickler und Konstrukteure eine hohe Designfreiheit. Das vorgeschlagene Konzept eröffnet den Designern der Automobilindustrie leichtere Lösungen, ökologischere Ansätze und verbesserte Sicherheitslösungen. In der Fertigung bedeutet die Adaptation von laserbasierten Verfahren, wie additiver Fertigung von Knoten, Laserschneiden und Laserschweißen von Rohren und Profilen, ein unvergleichliches Maß an Flexibilität. Nicht zuletzt können diese Fertigungsstrategien zu einer Erhöhung der Automatisierung beitragen. Diese Verfahren stehen für die Innovation von Fertigungsprozessen.
Frank Herzog: Ich danke Herrn Dr. Hillebrecht für den Hinweis auf die „Industrie 4.0“. Kernelemente dieses Konzeptes wie Automatisierung, Digitalisierung und Vernetzung spielen in unserer neu vorgestellten „AM Factory of Tomorrow“ eine elementare Rolle. Ziel ist es, manuelle Prozesse zu automatisieren und somit zu minimieren, um Totzeiten in der Produktion der Bauteile zu vermeiden. Maschinen, welche bisher als Stand alone-Lösungen konzipiert waren, werden zudem im Sinne einer Smart Factory in beliebiger Anzahl miteinander vernetzt. Dabei wird es auch zu einer Automatisierung und Vernetzung additiver und konventioneller Techniken kommen, insbesondere in der Nachbearbeitung der entstandenen Bauteile. Klassische Fertigungsmethoden gehen dann einher mit additiven Verfahren. Unsere „AM Factory of Tomorrow“ deckt sich mit den Anforderungen des Industrie 4.0-Leitgedankens und wird unser Verfahren zukünftig auch für die Serienfertigung von metallischen Bauteilen aus wirtschaftlicher Sicht attraktiv machen. Dieses gilt dann sicher auch für die Automobilindustrie, bei der es vornehmlich auf hohe Stückzahlen ankommt.
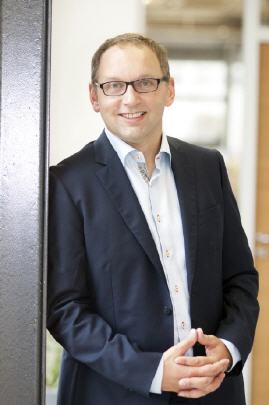
Frank Herzog
Geschäftsführender Gesellschafter, Concept Laser GmbH, Lichtenfels
Redaktion: Welche Bedeutung hat das pulverbasierte Laserschmelzen von Metallen heute und zukünftig in Automotive?
Claus Emmelmann: Aktuell ist das 3D-Drucken von Metallen im Bereich des Prototypenbaus in der Automobilindustrie nicht mehr wegzudenken. Mit dem Verfahren ist es möglich, schnell und ohne die sonst üblichen hohen Werkzeugkosten voll belastbare Erprobungsbauteile herzustellen. Der Schritt in die Serienfertigung steht allerdings noch bevor. Durch die kontinuierliche Produktivitätssteigerung der 3D-Druckanlagentechnik wird dieser Schritt jedoch auch in den nächsten 5 bis 10 Jahren erfolgen. Mit den beiden auf der IAA-Messe 2015 vorgestellten Projekten, dem bionischen Spaceframe und dem Leistungselektronikgehäuse, wurden zwei konkrete Ansätze gezeigt, wie diese Technologie schon in Kürze bei Fahrzeugen der Elektromobilität oder auch anderen Kleinserienfahrzeugen wirtschaftlich zum Einsatz kommen kann.
Sergio Raso: Additive Fertigungstechniken werden heute vor allem in der Automobilindustrie für die Herstellung von Funktionsteilen in kleiner Serie eingesetzt. Allerdings sehen wir auch, wie Luft- und Raumfahrtbranche es vormachten, dass der Übergang auf additive Fertigungsstrategien die Produkt- und Prozess-Performance signifikant erhöht. Die Einführung des Paradigmas „Manufacturing for Functionality“ anstelle des eher restriktiven „Design for Manufacturing" ebenso wie die „Just-in-time-Fertigung" und punktgenaue Konzepte haben bereits begonnen, sich in der Automobilindustrie zu verbreiten. Wir sehen hier Grundlagen für etwas ganz Neues.
Martin Hillebrecht: Heute stellen die generativen Verfahren ein großes Potenzial im Prototypen- und Werkzeugbau sowie der Ersatzteilfertigung dar. In der Automobilproduktion sind diese Verfahren bisher nicht angekommen. Das liegt sicherlich auch an den hohen Preisen für Werkstoffe und Anlagentechnologien. Auf die Zukunft sind wir gespannt. Es würde uns freuen, wenn die Branche unsere Ideen der werkzeuglosen generativen Fertigung in Kombination mit klassischen Fertigungsverfahren aufgreifen würde. Hier liegen ja einige Chancen.
Frank Herzog: Das Interesse wird zunehmen, je weiter sich der Stand der Technik beim Thema Additive Manufacturing fortentwickelt. Natürlich ist eine starke Annahme in Automotive erst dann zu erwarten, wenn man sich, wie in der Luft- und Raumfahrt, bereits in der Konstruktion auf die neuen Möglichkeiten einer additiven Fertigung einlässt. Eine reine Substitution von Teilen aus klassischen Methoden bietet wenig Vorteile. Es kommt auf eine verfahrensgerechte Konstruktion an – und diese Teile sehen dann anders aus, sind leichter und wahrscheinlich oft auch leistungsfähiger.
Redaktion: Danke für den Hinweis auf die Konstruktion. Wie verändert dies die Konstruktion oder Projektabläufe von Strukturelementen in Automotive? Was wird sich zukünftig noch verändern?
Martin Hillebrecht: Die Entwicklungsprozesskette vom Lastenheft über die Topologieanalyse, Funktionsentwicklung, bionische Gestaltung und fertigungsgerechte Gestaltung ist heute noch nicht etabliert und noch sehr zeitintensiv. CAD und CAE werden zunehmend verschmelzen. Es wird eine übergreifende CAx-Kompetenz gefordert. Zudem benötigen wir bionische Kompetenzen und Tools, nicht zuletzt eine funktionierende Schnittstelle zur Laserschmelzanlage, damit dann später wirklich alles „druckbar ist, was denkbar wäre“.
Sergio Raso: Der Einsatz von 3D-gebogenen und lasergeschnittenen Rohren und Profilen für die Strukturmontage konnte sich bereits als gewichtseinsparende Anwendung unter Beibehaltung der mechanischen Eigenschaften in der Montage bewähren. In diesem Entwurf fällt der lastspezifischen Abstimmung von lasergeschmolzenen 3D-Knoten und lasergeschweißten 3D-Profilen eine wichtige Rolle zu. Knoten, mit traditionellen Gusstechnologien hergestellt, erwiesen sich in der Vergangenheit als eine bewährte Lösung. Die generative Fertigung erlaubt den 3D-Knoten nun durch Bionik, Hohlräume und Gitterstrukturen noch mehr Möglichkeiten für Design, Variationen und Sicherheitsaspekte. Ich sehe das als einen wichtigen „next step“.
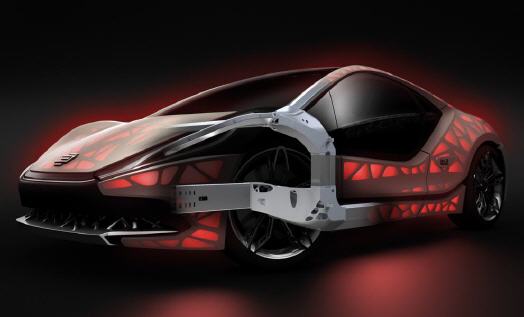
Concept Car ›EDAG Light Cocoon‹
Der "EDAG Light Cocoon" ist ein visionärer Ansatz eines kompakten Sportwagens mit einer umfassend bionisch optimierten und generativ gefertigten Fahrzeugstruktur.
Redaktion: Kann ein neues Konzept wie der EDAG Light Cocoon die Nachfrage der Autokäufer beeinflussen?
Sergio Raso: Autos stehen heutzutage wie kaum etwas anderes für die „Ausübung von Freiheit“ jedes Einzelnen. Das Lichtkonzept des Cocoon stimuliert sicherlich „gute Gefühle" im Straßenverkehr. Allerdings zielt die Nachfrage der Käufer heute primär auf praktische Bedürfnisse wie Kosten, Sicherheit und Zuverlässigkeit der Marke. Daher hat das Konzept eines leichten Hybrid-Designs realistisch zu berücksichtigen, erst einmal nur einen Blick in die Zukunft werfen zu wollen. Ein möglicher Schritt in Richtung Innovation. Es braucht natürlich weitere Anstrengungen und möglicherweise viel Zeit, um Schritt für Schritt die etablierten Kaufentscheidungen in neue Bahnen zu lenken.
Martin Hillebrecht: Werkstoffe sind zwar nicht, wie das Fahrzeugdesign in Interieur oder Exterieur, für die Kaufentscheidung des Endkunden verantwortlich, sie sind allerdings für die wirtschaftliche Herstellung und Funktionalität eines Fahrzeugs unerlässlich in der Betrachtung. Intelligente Mischbauweisen sind im Leichtbau ebenso wichtig wie die Energie- und Ressourceneffizienz von Fahrzeugen im globalen Kontext. Mir wäre ein Aspekt wichtig: Sichtbare bionische Strukturen im Fahrzeug mit ihrem positiven Image in der Gesellschaft, realisiert durch die Zukunftstechnologien der generativen Fertigung, könnten aber erstmals dazu führen, dass auch Endkunden spannende Werkstoffentscheidungen treffen. Wie viele Euro Mehrkosten pro reduziertem Kilogramm durch bionische Lösungen würden es den Kundensegmenten wert sein umzusteigen – darüber lässt sich nur spekulieren.
Frank Herzog: Stimmt. Hier können wir nur spekulieren. Es wird aber noch etwas dauern, bis die Vorzüge der additiven Fertigung auch in die Argumentationsketten der Werbung der Automobilindustrie Einzug halten. Das Thema Nachhaltigkeit ist aber schon mal gesetzt.
Redaktion: Zu den Stichworten Leichtbau und Bionik: Die Gewichtsreduzierung scheint ein klarer Vorteil zu sein. Wo stößt man an Grenzen bei sicherheitsrelevanten Bauteilen und beim Crash-Test?
Sergio Raso: Das vorgeschlagene Konzept kann klare Vorteile für sicherheitsrelevante Komponenten aufzeigen. Sollte es zu einem Unfall kommen, sorgen Funktionalisierung der 3D-Profile und 3D-Knoten für eine kontrollierte Deformation des Rahmens. Simulationen haben bereits gezeigt, dass das Zusammenspiel von Knoten, Quer- und Längsträgern das Verhalten unter Crash-Bedingungen deutlich verbessert. Das Abführen von mechanischer bzw. kinematischer Energie ist gegenüber einer konventionellen Rahmenkonstruktion ungleich besser realisierbar.
Martin Hillebrecht: Bei crash-beanspruchten Bauteilen, z. B. den Längsträgern und A-Säulen-Knoten, wird durch ein „definiertes Faltenbeulen“ des Trägers Energie abgebaut. Eine entsprechende CAE-Methodik zur Crash-Optimierung bionischer Konstruktionen ist aktuell ein neues und spannendes Thema für Forschung und Entwicklung geworden. Zudem wurde die Angebotspalette generativer Werkstoffe bisher noch gar nicht auf die Anforderungen von Automobilherstellern abgestimmt. Hier stehen wir häufig mit Rat und Tat zur Seite. Generative Strategien verändern alles: Konstruktionen, Funktionen, Materialwahl – und das mögliche Qualitäts- und Leistungsspektrum.
Claus Emmelmann: Bionisch optimierte und gedruckte 3D-Bauteile sind im Bereich der Bauteilfestigkeit ebenbürtig gegenüber konventionellen Bauteilen. Durch eine gezielte Bauteilnachbehandlung, wie z. B. durch Sandstrahlen oder Wärmebehandlungen, können die Material- und Bauteileigenschaften anwendungsspezifisch eingestellt werden. Im Grunde gelingt es erstmals, Leistungsmerkmale überzeugend zu „designen“. Im Laser Zentrum Nord beschäftigen sich die Mitarbeiter im Bereich Forschung und Entwicklung u. a. mit den Themen Bauteiloptimierung, Prozessqualifizierung, Qualitätssicherung und auch mit der Ermittlung und gezielten Einstellung von Materialkennwerten. Die bionische Optimierung bietet dabei die Chance, das Material optimal und lastgerecht einzusetzen und somit maximalen Leichtbau zu realisieren.
Redaktion: Die Automobilbranche ist volumengetrieben und denkt in hohen Stückzahlen und Plattformstrategien, um die Kosten zu beherrschen. Wie kann sich der neue Ansatz eines solchen Konzeptautos gegen diese tradierten Prämissen behaupten?
Sergio Raso: Es ist schwierig zu glauben, dass die neue Hybrid-Leichtbauweise zu einer sofort umwälzenden Innovation in der Massenproduktion von Autorahmen führen kann. Ein realistischeres Szenario ist die Annahme des neuen Konzepts für kleine Serien hochwertiger Automobile, während parallel traditionelle Design-Paradigmen für die „Low cost“-Massenproduktion erhalten bleiben. Es dürfte sich ein „Sowohl-als-auch“-Denken etablieren. Das wäre aus meiner Sicht realistisch.
Martin Hillebrecht: Unser Thema ist derzeit nicht für die kostenminimierte Produktion eines weltweiten Massenproduktes unter „Low cost“-Gesichtspunkten geeignet. Unser Anspruch ist es, mit dem Konzept einer High-Tech-Fertigung im Premiumsegment aufzuzeigen. Natürlich liegt der Charme auch in einer konsequenten Nutzung von Funktionssteigerungen und Automatisierungen für den Standort Europa. Ich bin auch überzeugt, dass ein durchgängiges Konzept erst dann entstehen kann, wenn eine Vielzahl von elektrischen und nichtelektrischen Antriebsvarianten für Fahrzeuge als generelle Anforderung mit ins Spiel kommt. Das Thema entwickelt sich ja gerade erst.
Frank Herzog: Die Erfahrung zeigt, dass Innovationen im Bereich Automotive zuerst im Premium-Segment ansetzen. Denken wir nur an Themen wie den Airbag, LED-Licht oder ABS. Nach und nach arbeitet sich eine Innovation nach unten durch die Produktpalette. Dabei gibt es „Economies of Scale“, die die Kostenseite positiv beflügeln. Wenn wir langfristig sinkende Kosten für das Kilogramm lasergeschmolzener Produkte aufgrund des technischen Fortschritts unterstellen, dann wird das Thema Additive Manufacturing immer interessanter für die Automobilisten. Den Experten von Roland Berger zufolge lag im Jahr 2012 der Durchschnittspreis inklusive aller Kosten in der AM-Verarbeitung, also für Maschinentechnik, Pulver, Energieaufwand, Nachbearbeitung usw. bei rund 3,14 EUR/ccm. Für das Jahr 2018 sagen diese Analysten ca. 1,60 EUR/ccm voraus. Für das Jahr 2023 wird 1,10 EUR/ccm prognostiziert. Ich will damit nur sagen, es gibt wohl eine deutliche Tendenz, die veranschaulicht, dass auf der Kostenseite noch einiges passieren wird.
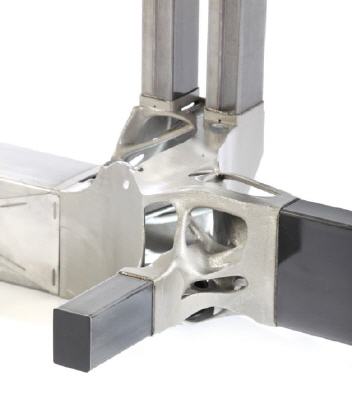
Technologiebeispiel 1 NextGen Spaceframe
Redaktion: Als logistische und kostenintensive Herausforderung gelten die Ersatzteile für Automobile. Globale Verfügbarkeit, Lagerhaltung, Lebenszyklus und Zeitdruck sind Herausforderungen für die Ersatzteilexperten. Nicht zuletzt sind Ersatzteile derzeit ein Segen für Automobilzulieferer als Erstausrüster oder Nachrüster oder auch Kopierer. Wie kann eine generative Fertigung diese Situation verändern?
Martin Hillebrecht: Die generative Fertigung ermöglicht es vor allem, Komponenten verteilt und an unterschiedlichen Standorten zu fertigen. So lassen sich lokale Vorteile nutzen: Varianten können zeitlich später und örtlich nahe an der Produktion entstehen. Dadurch entfallen Transport- und Logistikkosten, Komponentenvarianten sind nicht mehr zu bevorraten, und die markt- und kundennahe Produktion verkürzt die Lieferzeit.
Claus Emmelmann: Mit der generativen Fertigung ist es möglich, nicht länger physisch Bauteile, sondern einfach CAD-Datensätze weltweit zu versenden und dann, bei Bedarf, Ersatzteile vor Ort auszudrucken. In der dezentralen Fertigung liegt eine Option, deren Auswirkungen wir nur erahnen können. Dieses Verfahren verändert die Ersatzteilversorgung radikal – Lieferzeiten werden signifikant verkürzt und Lagerhaltungskosten entfallen vollständig. Dieses Szenario wird aktuell mit der Luftfahrtindustrie aktiv umgesetzt. Damit wird der Grundstein gelegt, dieses auch auf die Automobilindustrie zu übertragen.
Sergio Raso: Autorahmen auf Basis 3D-gebogener und geschnittener Profile sowie Knoten aus additiver Fertigung werden neue Paradigmen auch für das Management von Ersatzteilen und deren Logistik ermöglichen. Vollautomatische Herstellung von Profilen und Knoten basierend auf Just-in-time-Ansätzen würde eine drastische Kostensenkung ermöglichen, auch unter Berücksichtigung der Annahme neuer Richtlinien zur Reparatur von Fahrzeugen.
Redaktion: Welche generellen Veränderungen durch 3D-Strategien sehen Sie für zukünftige Fahrzeuge?
Martin Hillebrecht: Generative Fertigungsverfahren bzw. das Additive Manufacturing werden die klassischen Anwendungsgebiete des „Rapid Prototyping“ oder „Industrial Prototyping“ verlassen. Sie werden an die Seite der klassischen Fertigungsverfahren treten und konstruktive Gestaltungsmöglichkeiten um eine weitere Dimension erweitern. Für mich sogar radikal. Die generative Fertigung erlaubt die Darstellung von sehr komplexen, funktionsintegrierten und hocheffizienten Strukturen, die mit anderen Verfahren nicht herstellbar sind. Komplexe Komponenten für variantenintensive Produkte könnten somit zukünftig maßgeschneidert ausgelegt werden und werkzeuglos individuell optimal hinsichtlich Funktion, Sicherheit und Gewicht „on demand“ gefertigt werden. Das ist fundamental neu in der Branche.
Frank Herzog: Ich teile diese Einschätzung auf mittlere Sicht. Ich denke aber auch, dass klar sein muss, dass wir konstruktiv, wie hier beim NextGen Spaceframe, ganz neue Wege gehen müssen, um Additive Manufacturing stärker im Bereich Automotive zu implementieren. Auch die Funktionsintegration, wie eine Kühlleistung, kann ein wichtiger Mosaikstein sein. Ein additiv gefertigtes Produkt muss konsequent von den Leistungskriterien her entwickelt werden. Wenn es mehr kann als das alte und auch noch geringere Kosten und mehr Flexibilität ins Spiel kommen, wird es interessant.
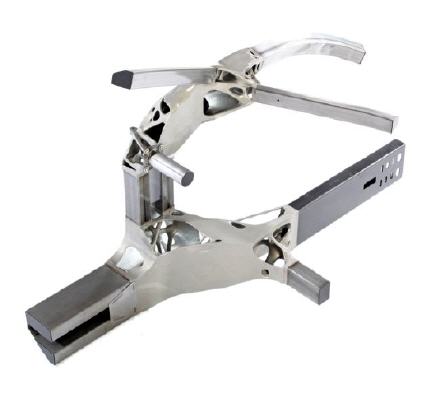
Technologiebeispiel 2 NextGen Spaceframe
Redaktion: Können diese neuen Ansätze die Entwicklungszyklen und die Modellpalette vitalisieren? Welche Potenziale ergeben sich in der Kostenstruktur und im Fahrzeugendpreis?
Sergio Raso: Die hohe Flexibilität des Spaceframe-Designs ermöglicht eine parametrische Konstruktion des Autorahmens. Prinzipiell stoßen wir ein Fenster für eine wesentlich breitere Palette von Modellen oder sogar individualisierten Autos auf. Sicher ist für mich, dass sich durch diesen strategischen Ansatz die Kostenstruktur verbessern lässt – und dadurch hoffentlich auch die Fahrzeugendkosten für den Käufer sinken.
Frank Herzog: Die Frage wäre aber auch generell, wohin steuert die Automobilindustrie? Will sie eher in Volumenstrategien gehen, oder sind zukünftig nicht auch individualisierte Autokonzepte gefragt, um Käufer zu stimulieren? Im letzten Szenario, und möglicherweise wird es beide Tendenzen parallel geben, kann das Additive Manufacturing ein paar Akzente setzen.
Redaktion: Welche Möglichkeiten sehen Sie bei Bauteilen der Zukunft zur Funktionsintegration bei Automobilen, wie etwa Kühlfunktionen, oder in der Option, leistungsfähigere Bauteile zu konstruieren?
Martin Hillebrecht: Ohne diese funktionalen Mehrwerte, die ich stillschweigend in jedem, egal welchem, Konzept voraussetze, wird es kaum gelingen, die zur Zeit hohen Herstellkosten der generativen Fertigung zu argumentieren.
Redaktion: Kritiker sagen, dass die aktuellen Bauraumgrenzen und Aufbaugeschwindigkeiten in der 3D-Fertigung die Möglichkeiten beschneiden. Wie bewerten Sie diese Diskussion?
Claus Emmelmann: Aktuell ist die Produktivität des Prozesses für gewisse Einsatzbereiche, wie der automobilen Großserie, begrenzt. Insofern stimmt die These. In Branchen wie der Medizintechnik oder der Luftfahrt wird das Verfahren bereits intensiv eingesetzt. Ich prognostiziere einen signifikanten Produktivitätssprung der Technologie für die kommenden Jahre und somit auch die Chance, beim Automobilbau im Bereich Großserien nach und nach attraktiv zu werden. Das Laser Zentrum Nord arbeitet mit seinen Partnern intensiv an neuen Maschinen- und Automatisierungskonzepten, die dies möglich machen sollen.
Martin Hillebrecht: Die Bauräume sind heute schon ziemlich ausreichend, aber typische Werkstoffe sind noch unzureichend entwickelt und deutlich zu teuer. Wir würden uns generative Fertigungsprozesse wünschen, die eine vielleicht 100-fach höhere Aufbaugeschwindigkeit bei gleicher Oberflächengüte ermöglichen. Den Anlagenbauern sei gesagt: Machen Sie weiter auf dem eingeschlagenen Weg.
Sergio Raso: Diese Einschränkung in Bezug auf Bauraum und Preise wird in naher Zukunft dank der Einführung neuer Lasersysteme für die additive Fertigung mit höherer Leistung und gesteigerten Aufbauraten reduziert werden. Allerdings lässt die eingeschlagene Hybridbauweise mit Knoten und Profilen für hohe Längsabmessungen schon heute einen wirtschaftlichen Ansatz erkennen. Das Thema ist im Fluss.
Frank Herzog: Blicken wir doch einmal zurück und nach vorne. Die Aufbaugeschwindigkeiten haben sich bereits dank der Multilasertechnik und der zunehmenden Laserleistung stark erhöht. Es gilt aber auch, genau zu beachten, dass jede neue Laserquelle die Komplexität des Prozesses und somit auch die Fehleranfälligkeit erhöht. Rein quantitative Ansätze halte ich aus heutiger Sicht nicht für primär zielführend. Wie wir mit unserer AM Factory of Tomorrow zeigen, gilt es, sich aus unserer Sicht auf sogenannte Totzeiten während des Produktionsprozesses zu konzentrieren, um diese letztendlich zu minimieren. Diese stehen meist in Zusammenhang mit manuellen Arbeiten in vor- und nachgelagerten Prozessstufen, wie z. B. dem Zuführen von neuem Pulver oder der Nachbearbeitung der Produkte. Hier sehen wir zunächst einen viel wichtigeren Ansatzpunkt, um unser Verfahren im Sinne einer wirtschaftlichen Serienfertigung weiterzuentwickeln - auch wenn die Laserleistung sicher noch Möglichkeiten zur Steigerung bietet. Zudem stehen für uns qualitative Bemühungen im Vordergrund, denn ein additiv gefertigtes Produkt sollte natürlich auch immer rein qualitativ überzeugen. Ist diese Basis sicher beherrschbar, kann man in puncto Leistung einen Schritt nach vorne gehen. Ich würde die Anmerkung von Dr. Hillebrecht unterstützen wollen, dass die Bauräume schon recht groß sind. Concept Laser bietet mit der X line 2000R den weltweit größten Bauraum (800 x 400 x 500 mm) an. Noch größere Teile sind vielleicht möglich, aber in Bezug auf sehr große Teile kommen wir an die Grenzen der Physik: Die Spannungen im Teil würden zunehmen. Prozessual kann man das heute nicht beherrschen. Als Ausweg sehe ich dann immer Fügetechniken, um z. B. sehr schmale, lange Teile modular zusammenzufügen. Trotz aller Euphorie um die additive Fertigung, sind wir gut beraten, realistisch und mit Augenmaß nach vorne zu blicken.
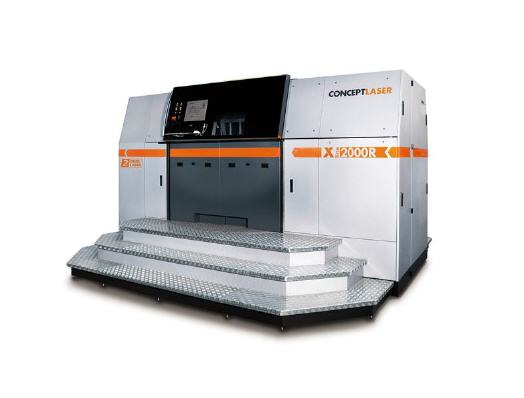
X line 2000R von Concept Laser
Redaktion: Beurteilen wir das Thema Qualität von 3D-Bauteilen. Wie bewerten Sie das Niveau klassischer Fertigungsmethoden gegenüber additiven Verfahren?
Martin Hillebrecht: Standards und Qualitätsanforderungen sind durch Branchenexperten in Erarbeitung und werden sich mit Sicherheit auch an die Normen für klassische Fertigungsmethoden anlehnen.
Frank Herzog: Fairerweise gesagt: Wir stehen noch vor einer mehr oder weniger „weißen Landkarte“, was die Additive Manufacturing-Lösungen der Zukunft betrifft. Der NextGen Spaceframe ist allerdings ein so mutiges Signal für die Automobilindustrie, sich dem Thema konstruktiv zu nähern. Vielleicht sehe ich das zu zurückhaltend, aber was wir zukünftig erleben werden, ist eine „Generation 3D“: Ingenieure und Konstrukteure, die vertraut mit dem 3D-Drucken umgehen, weil junge Menschen sich heute ein Leben ohne Smartphone und Internet kaum vorstellen können. Die „Generation 3D“ steht sicherlich in den Startlöchern, braucht aber auch konkrete Projekte, um sich zu beweisen. Ich bin aber zuversichtlich, dass diese „Generation 3D“ sich ihre Themen suchen wird.
Sergio Raso: Die 3D-Lasermaterialbearbeitung ist weltweit als zuverlässige Technologie etabliert. Sie ist aus meiner Sicht in der Lage, Qualitätsstufen des Prozesses und der Produkte besser als traditionelle Fertigungslösungen zu gewährleisten. In diesem Szenario werden additive Fertigungsverfahren uns voraussichtlich noch zu einem höheren Qualitätsniveau führen. Die Technologie kann sehr gut, auf der Basis des digitalen Prozesses, in eine digitale Produktion der Zukunft integriert werden. Zusammen mit dem Thema Automation liegen hier interessante Potenziale der „Industrie 4.0“.
Redaktion: Zum Schluss bitte noch einen Blick in die Zukunft. Welche generativen Bauteile werden in Automotive in der nächsten Dekade denkbar sein?
Martin Hillebrecht: Neben der klassischen Prototypenteilefertigung, z. B. von Gussteilen, erlaubt die generative Fertigung die Darstellung von sehr komplexen, funktionsintegrierten und hocheffizienten Strukturen, die mit anderen Verfahren nicht herstellbar sind. Es lohnt sich also, in die Nischen zu schauen und abgesehen von Rennsport und dem Ultra-Leichtbau im Kontext spezieller Anforderungen, z. B. Elektromobilität, nach Zukunftslösungen zu suchen. Diese können dann mit uns als dem unabhängigen Entwicklungsunternehmen der Automobilindustrie konkretisiert werden.
Frank Herzog: (lacht) Schauen wir mal, was die „Generation 3D“ für Flausen im Kopf hat. Als wir vor 15 Jahren Concept Laser gründeten, hatten wir auch Flausen im Kopf. Inzwischen wurden wir von der Entwicklung mehr als positiv überrascht. Und das ist auch gut so.
Sergio Raso: Ich bin kein Prophet. Laut den Wissenschaftlern der ESA wird die Menschheit nur auf Missionen, wie einer bemannten Mars-Mission, aufbrechen können, wenn Technologien für die Reparatur des menschlichen Körpers auf der Reise zur Verfügung stehen. Könnte der Fahrer eines Fahrzeug dies als politisch korrekte Antwort akzeptieren? Ich will sagen, in der Zukunft werden wir Lösungen akzeptieren, die heute nicht vermittelt werden können. Fakt ist schon einmal, dass das 3D-Drucken auf Raumstationen durch die NASA exploriert wird. Und was immer passieren wird, es liegt unter kosmischen Gesichtspunkten sehr viel Zukunft vor uns.
Mehr Informationen zu Concept Laser:
![]() |
CONCEPT Laser GmbH |
![]() |
An der Zeil 8 |
![]() |
96215 Lichtenfels |
![]() |
Tel.: +49 (0) 9571 / 949-238 |
![]() |
Fax: +49 (0) 9571 / 949-239 |
![]() |
E-Mail: info@concept-laser.de |
![]() |
www.concept-laser.de |
War dieser Artikel für Sie hilfreich?
![]() |
![]() |
![]() |
![]() |
![]() |
Bitte bewerten Sie diese Seite durch Klick auf die Symbole.
Zugriffe heute: 1 - gesamt: 2674.