Mit Hochdruck zu Prozessvorteilen
KNOLL stellt MMS-System mit Injektortechnik vor
Das neue KNOLL Minimalmengenschmiersystem ›ControLube‹ wird über einen Mikroprozessor gesteuert und macht sich die aus der Automobilindustrie bekannte Einspritztechnik zunutze. Es vereint die Vorteile von ein- und zweikanaligen Lösungen – und hat noch einiges mehr zu bieten.
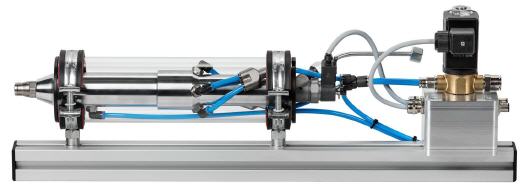
Kühlschmierstoffe (KSS) und -systeme erfüllen beim Zerspanen vielfältige Aufgaben: Sie vermindern die Reibung, entfernen Späne, führen Wärme ab und sorgen für eine gleichmäßige Temperatur von Werkstück und Werkzeug, um enge Toleranzen einhalten zu können. Doch der Einsatz von Kühlschmierstoffen ist mit teilweise beträchtlichen Kosten für Bereitstellung, Aufbereitung sowie Entsorgung verbunden und belastet die Umwelt.
Schon seit langem sind die Betreiber zerspanender Werkzeugmaschinen auf der Suche nach Alternativen. Die Minimalmengenschmierung (MMS), die einen Mittelweg zwischen Nass- und Trockenbearbeitung darstellt, gewinnt zunehmend an Bedeutung. Zumindest, wenn es um das Zerspanen mit definierter Schneide von Werkstoffen wie Aluminium-, Knet- und Gusslegierungen, Grauguss, Stählen und sogar rostfreiem Material geht.
MMS bietet vielfältige Vorteile bezüglich Prozess und Kosten
Branchen wie die Luftfahrt- und Automobilindustrie, die Werkstücke aus diesen Materialien in großen Stückzahlen produzieren, setzen immer häufiger MMS-Systeme ein. Denn allein aus der geringen Menge benötigten Schmierstoffs ergeben sich zahlreiche Vorteile. Zum Vergleich: Der Volumenstrom bei MMS liegt in der Regel bei weniger als 50 ml pro Stunde, während bei der Nass-Kühlschmierung in der gleichen Zeit bis zu 12.000 Liter eingesetzt werden.
So spart der Anwender sowohl beim Verbrauch als auch bei der Überwachung und Pflege sowie der Aufbereitung bzw. Entsorgung, denn die minimalen Mengen Schmierstoff verdampfen bei optimalem Prozess nahezu rückstandslos. Somit genügt es, die bearbeiteten Teile mit geringerem Aufwand zu reinigen.
Für viele Anwendungen sind die durch MMS entstehenden Prozessvorteile noch entscheidender. Bei der Zerspanung mit Nass-Kühlschmierung bleiben Feinstpartikel in Öl und Emulsion zurück, die bei der Wiederverwendung die Oberflächenqualität gefährden und dementsprechend aufwändig herausgefiltert werden müssen. Dieses Problem gibt es bei MMS schlichtweg nicht. Der eingesetzte Schmierstoff wird komplett verbraucht und daher stets neu in reiner Qualität zugeführt.
Zudem profitiert der Anwender von geringerem Werkzeugverschleiß, der auf die bessere Schmierung und geringere Thermoschockwirkung (bei unterbrochenem Schnitt) zurückzuführen ist. Auch lassen sich bei idealen Bedingungen höhere Werkzeugvorschübe realisieren. Nicht zuletzt gehören der geringere Platzbedarf, der niedrigere Geräuschpegel und weniger Gesundheitsgefahren für den Bediener zu den positiven Seiten der MMS.
Varianten der Minimalmengenschmierung
Nun gibt es verschiedene MMS-Systeme, die allerdings deutliche Unterschiede aufweisen. In bestimmten Anwendungsfällen wird die Möglichkeit genutzt, das Schmiermittel von außen auf das Werkzeug aufzubringen. Der gerätetechnische Aufwand ist hier gering, leider aber auch der gewünschte Schmiereffekt. Von der Späneabfuhr ganz zu schweigen.
Die meisten genutzten Systeme setzen auf interne Zufuhr des Schmiermediums, also durch Spindel und Werkzeug. Hier wird bislang in Einkanal- und Mehrkanal-Systeme unterschieden. Während bei ersteren das Öl der Druckluft schon vor der Hauptspindel zugesetzt wird, findet bei Mehrkanal-Systemen die Vermischung nach der Hauptspindel im Werkzeughalter statt.
Beide Systeme haben ihre Stärken und ihre Berechtigung. Das klassische Einkanal-System, das mit einem einzigen Kanal durch die Spindel geht, ist relativ einfach aufgebaut und kostengünstig. Es erzeugt ein verhältnismäßig feines Luft-/Öl-Gemisch (Aerosol), das sich gleichmäßig auf alle Kühlkanäle verteilt. Damit lassen sich auch Spezialmaschinen versorgen. Systembedingt ist jedoch mit Druckverlust und aufgrund der langen Leitungsführung von der Aerosolerzeugung bis zum Werkzeug mit Reaktionsverzögerungen zu rechnen. Zudem ist die transportierbare Ölmenge eingeschränkt.
Ein Zweikanal-System ist deutlich komplexer aufgebaut. Hier führen Öl- und Luftkanal separat durch die Spindel und die Medien werden im Anschluss daran im Werkzeughalter gemischt. Durch die separate Öllanze ist die Ölmenge unabhängig von der Werkzeuggröße und Drehzahl einstellbar. Doch nur unter optimalen Bedingungen entsteht ein homogenes Gemisch.
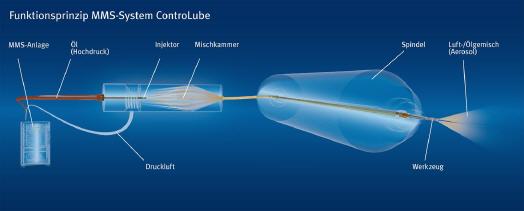
ControLube - das Beste aus beiden Welten
KNOLL Maschinenbau, Bad Saulgau, einer der führenden Anbieter von Förder- und Filteranlagen für Späne und Kühlschmierstoffe in der Metallbearbeitung, beschäftigt sich seit einiger Zeit auch mit der Minimalmengenschmierung. Geschäftsführer Matthias Knoll argumentiert: „Es gibt Produktionsbereiche, da ist die Nass-Kühlschmierung auf dem Rückzug, und die Zukunft gehört dort eindeutig der Minimalmengenschmierung. Für diese Bereiche, zu denen beispielsweise die Alu-Druckguss-Bearbeitung in der Automobilindustrie gehört, haben wir ein System entwickelt, das mit Hochdruck arbeitet und ein besonders feines Aerosol erzeugt. Damit erreichen wir verbesserte Prozessbedingungen, die sich für den Anwender in kürzeren Bearbeitungszeiten und geringeren Kosten niederschlagen.“
Beim MMS-System ControLube von KNOLL werden Öl und Druckluft separat zu einer Mischkammer geführt, die sich unmittelbar vor der Hauptspindel befindet. Diese Mischkammer ist das Herz des MMS-Systems ControLube. Denn hier wird das Öl einem Injektor zugeführt, wie er sich in der Einspritztechnik von PKWs seit vielen Jahren bewährt. Er spritzt das Öl mit Hochdruck in die Mischkammer, wo es sich mit der zugeführten Luft zu feinstem Aerosol vermischt. Das stark komprimierte Luft-/Öl-Gemisch wird anschließend einkanalig durch die Spindel zum Werkzeug geführt.
Jochen Blersch, Produktmanager MMS bei KNOLL, erklärt: „Auch wenn unser System ControLube vom prinzipiellen Aufbau her einkanalig ist, werden durch die Mischkammer mit ihrer Hochdruck-Einspritzung und einer speziellen Elektronik Eigenschaften erreicht, die bisher Zweikanal-Systemen vorbehalten waren, zum Beispiel die unabhängige Öl- und Luftmengenregelung sowie die sehr kurzen Reaktionszeiten.“ Durch die kalibrierte Hochdruck-Einspritztechnik wird das Schmiermedium schnell und präzise dosiert, und es werden feinste Ölpartikel erzeugt, die sich besonders bei hohen Drehzahlen bewähren.
Mikroprozessor übernimmt die Systemregelung
Ein wesentlicher Bestandteil des neuen KNOLL MMS-Systems ControLube ist die speziell entwickelte Elektronik auf Basis einer Mikroprozessor-Technik, die für kurze Reaktionszeiten bei Programmwechsel und Zyklusbetrieb sorgt sowie die Möglichkeit zum Live-Monitoring bietet. Sie ist über ProfiNet oder ein anderes Bussystem direkt mit der CNC-Werkzeugmaschine verbunden.
ControLube ist über die CNC variabel programmierbar. Für den Druck und die Ölmenge lassen sich entweder feste Werte vorgeben oder Variablen, die von den verwendeten Werkzeugen abhängen. Auch eine bedarfsgesteuerte Regelung ist möglich, die für eine konstante Luftmenge während der Bearbeitungsoperation sorgt (ideal z.B. beim Tieflochbohren). Jochen Blersch weist darauf hin, dass „die bisherigen Systeme sich nur in Stufen regeln lassen. Unser ControLube bietet die Möglichkeit, fast stufenlos im Kommabereich den Luftdruck bis zu 20 bar und unabhängig davon die Ölmenge bis zu 400 ml/h zu regeln, was auch zur Ressourcenschonung beiträgt.“
Noch eine Stärke: Eine KNOLL ControLube-Anlage kann mehrere Maschinen beziehungsweise mehrere Spindeln versorgen. Dazu wird zum Beispiel vor jede Spindel eine Mischkammer montiert, die mit dem MMS-System kommuniziert.
Auf das Umfeld kommt es an
Um die Minimalmengenschmierung prozesstechnisch und wirtschaftlich erfolgreich einzuführen, gilt es, neben der Wahl des passenden MMS-Systems verschiedene Bausteine zu beachten: den Bearbeitungsprozess, die Werkzeugmaschine, Werkzeug, Peripherie und nicht zuletzt das Personal. Es sollte schon im Vorfeld auf die Minimalmengenschmierung vorbereitet und qualifiziert werden. Denn die Mitarbeiter müssen in der Lage sein, den Prozess optimal einzustellen und zu überwachen hinsichtlich Prozessfolge, Projektierung und Strategien.
Die Werkzeugmaschine sollte eine schräg und steil angebrachte Arbeitsraumverkleidung sowie möglichst glatte, unlackierte Oberflächen besitzen, z.B. aus Edelstahl, um ein optimales Abgleiten der Späne zu gewährleisten. Zu vermeiden sind Rohrleitungen, Ecken oder waagrechte Flächen, an denen es zu Späne- und Staubansammlungen kommen kann. Eine sorgfältige Abdichtung des Arbeitsraums ist notwendig, damit keine Stäube an empfindliche Teile wie Antriebs- und Führungselemente der Maschine gelangen. Wichtig ist auch die thermische Entkopplung der Innenraumverkleidung gegenüber dem Maschinengestell, damit keine Wärmebrücken entstehen.
Bei der Minimalmengenschmierung wird die durch den Zerspanungsvorgang auftretende Wärme nicht über das KSS, sondern über die Späne abgeführt. Um ein Aufheizen von Werkstück und Werkzeug zu vermeiden, sollten die Späne möglichst schnell entfernt werden. MMS-optimierte Werkzeuge sind daher anzuraten, deren Schneidstoffe, Beschichtungen und Geometrie den Spanbruch und Spanfluss unterstützen und somit einer Überhitzung entgegenwirken.
Jochen Blersch betont die Bedeutung von kurzen Spänen für den erfolgreichen Einsatz der Minimalmengenschmierung: „Dann kann unser MMS-System ControLube seine volle Leistungsfähigkeit entfalten. Denn durch den bis auf 20 bar erhöhten Druck der Luft expandiert diese an der Austrittstelle sehr stark. Das bewirkt eine hohe Strömungsgeschwindigkeit, so dass die kurzen Späne förmlich durch die Nuten heraus katapultiert werden. Gerade bei kleinen Werkzeugen ist das von großem Vorteil.“
Die Stärken des KNOLL MMS-Systems:
- Hohe Prozesssicherheit durch Mikroprozessor-Technik mit Live-Monitoring
- Schnelle und präzise Dosierung
- Keine Nachkalibrierung notwendig
- Luftdruck und Ölmenge getrennt regelbar, auch bedarfsgesteuert
- Integrierte Luftdruckerhöhung bis 20 bar
- Direkte Maschinenanbindung über ProfiNet
- Schnelle und variable NC-Programmierung
- Kein Spezialöl notwendig, auch Emulsionsöl verwendbar
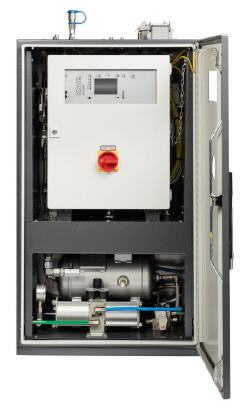
Mehr Informationen zu Knoll Maschinenbau:
![]() |
Knoll Maschinenbau |
![]() |
Schwarzachstraße 20 |
![]() |
88348 Bad Saulgau |
![]() |
Tel.: +49 (0) 75 81 / 20 08-0 |
![]() |
E-Mail: info.itworks@knoll-mb.de |
![]() |
www.knoll-mb.de |
War dieser Artikel für Sie hilfreich?
![]() |
![]() |
![]() |
![]() |
![]() |
Bitte bewerten Sie diese Seite durch Klick auf die Symbole.
Zugriffe heute: 2 - gesamt: 2534.