Automatisierung für optimalen Materialfluss
Flexibel, schnell und zuverlässig
Handwerkzeuge, Werkstückspannung, Luftfahrtprodukte und allein rund 7.000 Normalien – bei einem derart umfangreichen Sortiment ist eine flexible und abgestimmte Lagerlogistik ein absolutes Muss, damit Kunden schnell und zuverlässig ihre Waren erhalten. Aus diesem Grund hat die Erwin Halder KG ihr bisheriges System durch eine modernere automatisierte Logistiklösung ersetzt. Das neue System wurde exakt auf die Produktionsbedürfnisse von Halder angepasst und sichert den langfristigen Erfolg durch Flexibilität und optimalen Materialfluss.
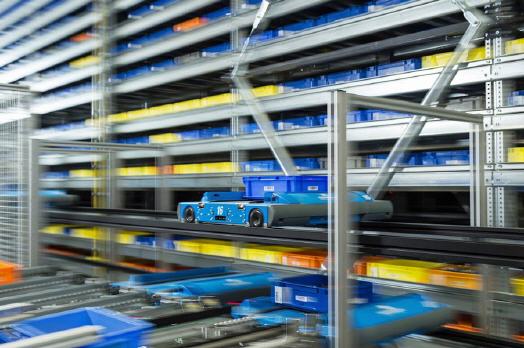
„Um unser großes Produktspektrum aus Maschinen- und Vorrichtungsteilen, Spannelementen, Bedienteilen sowie Maschinen- und Basiselementen, Schonhämmern, Forstwerkzeugen, Flight-Pins und unterschiedlichen Vorrichtungssystemen, mit fertig zusammengebauten Teilen und auch Halbfabrikaten, zu verwalten, setzten wir bisher eine teilautomatisierte Kombination aus Palettenregal und Lagerliften ein. Mit der kontinuierlichen Steigerung unseres Angebots wurde die Lagerhaltung mit diesem System durch vermehrte Nachschubfahrten zwischen den Palettenregalen und den Lagerliften jedoch zunehmend aufwändiger.
Zudem war eine Kapazitätserweiterung unbedingt notwendig, die jedoch mit dem bisherigen System ohne Neubau nur bedingt möglich gewesen wäre. Und da die Pflege der zuletzt eingesetzten Lagerverwaltungssoftware zum Jahresende 2015 eingestellt wurde, war die Anschaffung einer neuen unumgänglich. Bei diesen Fakten war die Entscheidung für ein komplett neues Intralogistiksystem nur logisch“, so Michael Dunz, Betriebsleiter der Erwin Halder KG.
Automatisierung bringt viele Vorteile
Bei der Umstellung auf ein neues System wollte die Erwin Halder KG dann auch direkt weitere Faktoren verbessern: Die bestehende Halle sollte besser ausgenutzt und unnötige, nicht wertschöpfende Tätigkeiten, wie etwa Nachschubfahrten und Zwischenlagerungen bei maßlich zu überprüfenden Artikeln, eliminiert werden. Auch hier sollte die neue Lagerverwaltung Abhilfe schaffen. Die ideale Lösung fand die Erwin Halder KG im automatisierten Shuttlesystem der Servus Intralogistics GmbH aus dem österreichischen Dornbirn. Dazu Michael Dunz: „Das neue System bietet uns vielfältige Vorteile: Dank des hohen Automatisierungsgrads kommen die Artikel nun zu unseren Mitarbeitern und nicht der ‚Mann zur Ware‘ wie bisher. Wir können mehr Artikel lagern, ohne die vorhandene Hallenkapazität erweitern zu müssen und bleiben dabei flexibel für die Zukunft.“
Das neue Anlagenkonzept bietet zusätzlich eine Stückzahlverwaltung auf Behälterebene und nicht nur auf den Gesamtbestand des jeweiligen Artikels. Ein weiteres großes Plus gibt es beim Durchführen der Inventur: Mit dem Liftsystem war diese bisher nur in einem definierten Zeitkorridor von Oktober bis Dezember möglich. Das war durch den permanenten Ausbau des Produktsortiments sehr personalintensiv und damit aufwändig. Nun erfolgt die Überprüfung des Lagerbestandes anhand einer permanent durchgeführten Inventur über das gesamte Jahr verteilt.
Im Logistikbüro findet sich das Cockpit bzw. der Leitstand. Hier ist die Schnittstelle zum ABAS-ERP-System der Erwin Halder KG. Von dort aus werden die Verkaufsaufträge für die Funktionszellen (i-Punkte) gesteuert. Vor der Übergabe von Aufträgen an das Lagersystem wird über das ERP-System ein Bestand festgestellt. So können die Mitarbeiter gewährleisten, dass die erforderlichen Stückzahlen vorhanden sind, um die Aufträge zu bedienen. Mit der Umstellung auf das neue Shuttlesystem entschied sich Halder auch für eine neue Lagerverwaltungssoftware von Mia Systems, die über die Schnittstelle mit dem ERP-System und der Versandsoftware BEO kommuniziert. Der Echtlauf erfolgte Ende Februar 2016.
Fehler werden auf ein Minimum reduziert
Vor der Einlagerung werden die Behälter mit den gelagerten Artikeln „verheiratet“. Das bedeutet, jeder Behälter besitzt eine feste Lademittel-ID, unter der die Informationen (Artikelnummer, Stückzahl, Referenzgewicht, Tara und Charge) über den „verheirateten“ Artikel hinterlegt werden. Gerade die Speicherung des Referenzgewichts bietet hier große Vorteile: Beim Kommissionieren wird es automatisch an die Waage übertragen und muss nicht jedes Mal neu ermittelt werden. Das ermöglicht, die Aufträge sehr viel schneller und einfacher zusammenzustellen.
Michael Dunz: „Dank des neuen Systems werden Fehler, beispielsweise bei der Zusammenstellung eines Auftrages, vermieden. Denn das System liefert die Behälter auftragsrein an den Kommissionierplatz. So können Verwechslungen bei der Zuordnung der Artikel nahezu ausgeschlossen werden. Eine Farbcodierung und unterschiedliche Größen der Kunden- und Lagerbehälterverhindern zudem eine Verwechslung auf den ersten Blick.“
16 ARCs für zuverlässigen Lagerverkehr
Kernstück des Systems sind die momentan 16 intelligenten und autonomen Transportroboter ARC3 (Autonomous Roboter Carrier) und das flexible Streckensystem. Die ARCs transportieren mit einer Geschwindigkeit von 2 m/s auf 190 m Fahrschienen die Produkte zu den derzeit 42.240 Lagerstellplätzen bzw. zu den Mitarbeitern im Wareneingang und der Auslagerung, in der Kommissionierung und in der Verpackung, den sogenannten Funktionszellen. Zudem ist neben der Logistik auch die Montage in das System eingebunden, so dass die fahrbaren Shuttles auch die Montageabteilung automatisch mit den benötigten Halbfabrikaten versorgen können.
Die neue Lagerlogistik nutzt den vorhanden Raum von 52 x 9 x 8 m perfekt aus und lässt sogar noch Luft nach oben. Denn es ist möglich sowohl die Anzahl der Lagerplätze weiter auszubauen, als auch die Leistung der Anlage durch den Einsatz weiterer ARCs zu steigern.
Perfekt abgestimmt
„Das Shuttlesystem wurde perfekt auf unsere Anforderungen abgestimmt. So haben wir einen verbesserten Materialfluss und kürzere Durchlaufzeiten. Umlaufbestände, Zwischenlager und Wartezeiten werden stark reduziert. Die Mitarbeiter erhalten just in time an den Arbeitsstationen die benötigte Ware. Dabei ist das System so flexibel, dass wir es einfach an beispielsweise größere Auftragseingänge und auch sich ändernde Produktionsabläufe anpassen bzw. erweitern können“, ergänzt Michael Dunz.
Mehr Informationen zur Erwin Halder KG:
![]() |
Erwin Halder KG |
![]() |
Erwin-Halder-Str. 5-9 |
![]() |
88480 Achstetten-Bronnen |
![]() |
Tel.: +49 7392 7009-0 |
![]() |
Fax: +49 7392 7009-160 |
![]() |
E-Mail: info@halder.de |
![]() |
www.halder.de |
War dieser Artikel für Sie hilfreich?
![]() |
![]() |
![]() |
![]() |
![]() |
Bitte bewerten Sie diese Seite durch Klick auf die Symbole.
Zugriffe heute: 1 - gesamt: 2777.