Lärmreduzierung durch Hightech-Werkzeuge
Optimal für die Bahnindustrie
Der Verband der Bahnindustrie in Deutschland e.V. (VDB) prognostiziert ein weiteres Wachstum des Personen- und Güterverkehrs. Deshalb müsse der Standort Deutschland die Bahnindustrie stärken und für einen leistungsfähigen Schienenverkehr sorgen. Eine der wichtigsten Herausforderungen des Schienengüterverkehrs (SGV) ist die nachhaltige Lärmreduzierung. Laut VDB ist im Nationalen Verkehrslärmschutzpaket II von 2009 die Halbierung des Schienenlärms bis 2020 festgelegt. Da müssen alle Zulieferer an einem Schienenstrang ziehen, um dies zu erreichen. Qualitätswerkzeuge für die Fahrwerks-, Räder-, Achsen- und Schienenfertigung spielen hierbei eine wichtige Rolle.
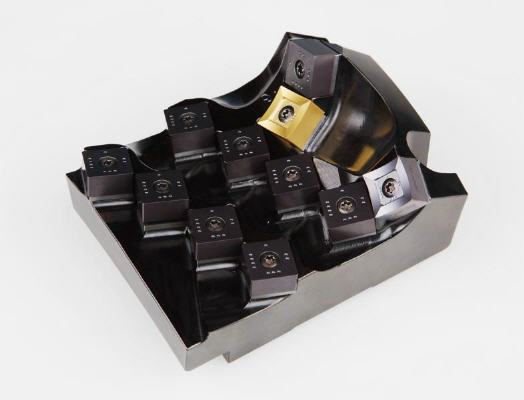
Bereits seit 1974 regelt das Bundesimmissionsschutzgesetz den Schutz vor Verkehrslärm. Immer wieder kamen Novellierungen in Form von Bundesimmissionsschutzverordnungen hinzu. Lärmsanierung bspw. durch Schallschutzmaßnahmen oder Geräuschabsorber sind eine Maßnahme zur Geräuschminderung, die Lärmvorsorge eine andere. Neben Wagen- und Bremsklotzgeräuschen sind auch Radlaufflächen und der Gleiszustand die Hauptursachen für den Lärm. Deshalb verlangt der Lärm- und Erschütterungsschutz an den Schienenwegen einen innovativen Technologie-Mix an Maßnahmen.
Präzisionswerkzeuge für viele Bearbeitungsfälle im Railway- Segment
Seit vielen Jahrenzehnten schon liefert Dormer Pramet Präzisionswerkzeuge für die Bahnindustrie und deren Zulieferer. „Wir verfügen über eine breite Produktpalette an Schneidwerkzeugen für die Produktion bspw. in der Schienenund Räderfertigung wie auch der Wartung“, so Tomáš Hantek. Als ein etablierter Partner der Bahnindustrie in vielen Standorten weltweit, unterstützt Dormer Pramet die Herstellung und Reprofilierung der Räder sowie die Bearbeitung der Achsen, Fahrwerken, Schienenprofilen und -renovierungen, Schalter, Grundplatten, eingebauten Achsen, Verbindungen und anderen Schienenfahrzeugkomponenten.
Jede Oberflächenrauhigkeit oder -unregelmäßigkeit kann zu unerwünschten Kräften, Reibung, Vibrationen und Verschleiß führen und somit negative Auswirkungen auf das Fahrzeug und die Infrastruktur haben. Im Personenverkehr hat dies Einfluss auf den Komfort der Reisenden,. Zudem sind erhebliche Lärmbelastungen damit verbunden. Bei jedem Kontakt zwischen den Fahrzeugrädern und Schienenoberflächen müssen die Werkstoffe stark genug sein, um den Normalkräften (Vertikalkräften) der regulären und schweren Lasten zu wiederstehen. Die Kräfte in der Kontaktzone müssen niedrig genug sein, um eine schnelle Bewegung schwerer Lasten bei geringem Widerstand zu ermöglichen, aber gleichzeitig groß genug, um Beschleunigung, Bremsung und Führung der Fahrzeuge sicher auszuführen.
„Eisenbahnräder und -schienen sind die wichtigsten Komponenten in jeder Eisenbahnoperation, weil sie die Schnittstelle zwischen Fahrzeug und Fahrweg darstellen. Die Schienen- und Räderoberflächen müssen deshalb immer die beste Qualität ausweisen“, betont Tomáš Hantek, internationaler Anwendungsmanager für die gesamte Bahnindustrie bei Dormer Pramet. Die zunehmende Zuverlässigkeit durch neue Werkzeuge, Werkstoffe und Bearbeitungstechniken sowie unterstützende, produktive und kostengünstige Wartung der bestehenden Infrastruktur sei entscheidend für die Bahn, um im Wettbewerb auch in puncto Lärm zu bestehen.
Wirtschaftliche WSP-Fräser für Schienenwartung
Das häufigste mechanische Geräusch eines Zugs wird im Kontakt zwischen Rad und Schiene erzeugt. Diese „Vibrationen“ werden über den Boden übertragen und können sogar in nahegelegenen Gebäuden gespürt werden. Die Vibrationen (im Bereich von 4 bis 80 Hz) oder das Rumpeln tiefer Frequenzen (zwischen 30 und 250 Hz) werden zum Teil auch in das Fahrzeug selbst übertragen und beeinflussen Reisekomfort sowie Fahrzeuglebensdauer deutlich. Um diese konstante Kraft zwischen Fahrbahn und Fahrzeug zu bekämpfen, muss die Schiene ständig in gutem Zustand sein. Es gibt mehrere Gründe für die Schienenbearbeitung mit Schienenschleif- und -fräszügen vgl. Abb. 1), doch in erster Linie geht es um Fragen der Betriebssicherheit und der Lärmminderung.
Die mechanischen Belastungen im Kontakt zwischen Rad und Schiene können zu Riffeln, Schlupfwellen oder gar Rissen auf der Schienenoberfläche führen. Sie müssen schnell beseitigt werden, bevor sie sich ausbreiten und den Gleisbereich zerstören. Aus diesem Grund ist die regelmäßige Bewertung des Schienenprofils wichtig, um Schäden an Fahrwegen und Schienenfahrzeugen zu begrenzen. Ein weiteres Ziel der Schieneninstandsetzung besteht darin, bestehende Fahrstrecken auch für moderne Hochgeschwindigkeitszüge zu nutzen bei Wahrung der Anforderungen an Zuverlässigkeit und Sicherheit.
Saubere Fräs-Fräs-Schleif-Methode
Die Schienenbearbeitung kann nach mehreren Verfahren erfolgen. Die zeitaufwändigste Tätigkeit im Bahnbetrieb ist das Ersetzen alter Schienen durch neue mithilfe von Gleisbaumaschinen. Da der Schienenaustausch recht kostenintensiv ist, werden verschlissene Gleise auch geschliffen. Eine alternative Möglichkeit ist deshalb das dynamische Schienenfräsen. Die Reprofilierung der Bahnstrecke ohne das Entfernen der Schienen stellt deutliche Zeit- und Kosteneinsparungen dar.
Es überrascht daher nicht, dass sich das dynamische Schienenfräsen zu einer der beliebtesten Methoden entwickelt hat, obwohl der erste Fräszug erstmals 1996 eingesetzt wurde. Seit dem sind die Anforderungen Spezialausrüstungen permanent gestiegen, um optimale Resultate zu erzielen. Das dynamische Fräsen kann durch speziell konzipierte Züge durchgeführt werden, die bei einer konstanten Geschwindigkeit von 700 Meter pro Stunde arbeiten. Die aus R350HT-Stahl erzeugten Schienen haben eine gute Abriebfestigkeit mit einer Härte zwischen 900 und 1.200 MPa. Durch das Befahren der Schienen kann es zumTeil zu einer Aushärtung des Schienenkopfes bis zu 1.500 MPa kommen, was eine besondere Herausforderung für die Fäswerkzeuge und Schneidstoffe bedeutet.
Das Bearbeitungsprinzip heißt: Fräsen, Fräsen, Schleifen. Zur Reprofilierung der Schienen werden zwei Fräseinheiten verwendet. Die erste schruppt die Oberfläche vor, die zweite sorgt für ihre Fertigbearbeitung, wobei beide Einheiten auf beiden Schienen gleichzeitig arbeiten. Das Endprofil der Schiene und die hohe Oberflächenqualität werden durch eine integrierte Schleifeinheit sichergestellt. Die beim Fräsen erzeugten Späne werden über einen Späneförderer in einen nahegelegenen Behälter abgeführt, sodass kein Schmutz oder Späne auf dem Fahrweg zurückbleiben. Eine andere Einsatzmöglichkeit ist die Verwendung eines Fahrzeugs, das zwischen Straße und Schiene durch Veränderung seines Radtyps wechseln kann. Es nutzt nur eine Fräseinheit auf jeder Seite, sodass die Fahrzeuge nur für die Endbearbeitung eingesetzt werden können.
Nachtschicht im Fräszug
Es ist eine gängige Praxis, dass während der Reprofilierung der Schienen bei Verschleiß der Wendeschneidplatten der Wechsel an Bord des Zugs erfolgt. Um Stillstandzeiten zu senken, wird dabei oft der komplette Fräser gewechselt. Die Renovierung der Bahninfrastruktur wird jedoch üblicherweise in der Nacht durchgeführt, wenn weniger Verkehr herrscht. Um die Sicherheit zu verbessern, ist es empfehlenswert, den Fräserwechsel während der Schicht, insbesondere in der Nacht, zu vermeiden. Die normalerweise zurückgelegte Entfernung beim Fräsen während einer Standardschicht beträgt zwischen 3.000 und 3.500 m. „Unsere Wendeschneidplatten und Fräser zur Schienenbearbeitung haben eine Standzeit von mehr als 3.700 m, so kann das Personal die ganze Schicht über im Fräszug bleiben“, erläutert Anwendungsexperte Hantek.
Das Sortiment für die Bahnindustrie von Pramet umfasst Scheibenfräser, Kartuschen und Wendeschneidplatten für das dynamische Schienenfräsen. Die Schienenfräser haben bspw. einen Durchmesser von 600 mm, Schnittgeschwindigkeiten zwischen 220 und 280 m/min und jeder Fräszahn kann zwischen 3,5 bis 5 mm der Schienenlänge mit Schnitttiefen zwischen 0,5 bis 1,5 mm bearbeiten. Außerdem steht eine breite Auswahl an universellen und herausnehmbaren Kassetten zur Verfügung, wobei jede ein für linke und rechte Schienen identisches Gehäuse hat, das Schruppen sowie Schlichten unterstützt. Diese Kassetten werden für die Bearbeitung unterschiedlicher Schienenprofile verwendet - AHC (Anti-Head-Check, für Schienen der Züge mit Geschwindigkeiten bis zu 160 km/h) und UIC 60E2-Profil für Hochgeschwindigkeitsstrecken.
Praktisch: bei einer Profiländerung müssen nur zwei von elf Wendeschneidplatten in jeder Kassette ausgewechselt werden, das spart Rüstzeit. Davon will auch die DB Netz AG künftig profitieren und hat bei Dormer Pramet einen dynamischen Fräser mit herausnehmbaren Kassetten und Wendeschneidplatten geordert. Außer bei der Reprofilierung der Schienen kommen Fräser von Dormer Pramet auch bei der wirtschaftlichen Bearbeitung der Bahnräder zum Einsatz. „Wir sind ständig bemüht, die Kundenanforderungen an Zuverlässigkeit, Produktivität und Kosteneffizienz zu erfüllen“, sagt Tomáš Hantek. Auch Bahnräder müssen, ähnlich wie Schienen, regelmäßig bearbeitet werden, um die Sicherheit zu gewährleisten und Vibrationen und Geräuschpegel zu reduzieren.
Die Bearbeitung der Bahnräder erfordert ebenfalls eine spezifische Technologie, nach dem sogenannten Kopierprinzip mit runder Schneidkante. Eine der größten Herausforderungen dabei ist die Bestimmung der optimalen Spandicke und Wärmeverteilung. „Unsere Railway- Teams arbeiten mit vielen Herstellern auf allen Kontinenten zusammen, deren gemeinsame Jahresproduktion mehr als 8 Millionen Räder umfasst. So können wir den Kunden regional mit unserer umfassenden Kompetenz unterstützen.“
Für die zukünftige Entwicklung gerüstet
„Der kontinuierliche Dialog über viele Jahre zwischen uns, Herstellern und Zulieferern, hat Dormer Pramet zum idealen Partner der Bahnindustrie gemacht, der für die wachsenden Industrieanforderungen in Qualität und Zuverlässigkeit hervorragend gerüstet ist“, erklärt Tomáš Hantek. Obwohl der Werkzeughersteller bereits über ein recht breites Produktsortiment für die Bahnindustrie verfügt, kommen jedes Jahr neue, innovative Werkzeuge, Komponenten und Schneidstoffe hinzu. „Bevor diese jedoch auf den Markt eingeführt werden, testen wir alle unsere neuen Werkzeuge nach strengen Anforderungskriterien“, versichert der erfahrene Anwendungstechniker.
Durch die umfangreichen Produkttests werden die Zuverlässigkeit im Schnittvorgang, Langlebigkeit und Produktivität für den Kunden, optimaler Spanbruch, Maßgenauigkeit und -stabilität sowie hohe Oberflächenqualität sichergestellt. „Nur wenn diese Eigenschaften eingehend getestet wurden, werden diese Produkte in unser Sortiment aufgenommen. Damit wollen wir die kontinuierliche Entwicklung für den Eisenbahnbereich in seiner Ganzheit für kommende Jahre sicherstellen“, so sein Fazit.
Mehr Informationen zu Dormer Pramet:
![]() |
Dormer Pramet |
![]() |
Am Weichselgarten 34 |
![]() |
91058 Erlangen |
![]() |
Tel.: +49 (0)9131 9330874-0 |
![]() |
E-Mail: isabel.hagen@dormerpramet.com |
![]() |
E-Mail 2: info.de@dormerpramet.com |
![]() |
www.dormerpramet.com |
War dieser Artikel für Sie hilfreich?
![]() |
![]() |
![]() |
![]() |
![]() |
Bitte bewerten Sie diese Seite durch Klick auf die Symbole.
Zugriffe heute: 2 - gesamt: 2555.