Die Standzeitsteigerung im Blick
Beschichten mit Al2O3 & Co.
Immer größere Standzeiten bei Zerspanungswerkzeugen sind nicht zuletzt ein Ergebnis der modernen PVD- und CVD-Beschichtungstechnik. In dieser Technik steckt noch ein gewaltiges Potenzial, dessen Erschließung gewaltige Vorteile im Werkzeugmarkt generiert. Kein Wunder, dass Mapal eine der modernsten CVD-Beschichtungsanlagen der Welt in Betrieb genommen hat.
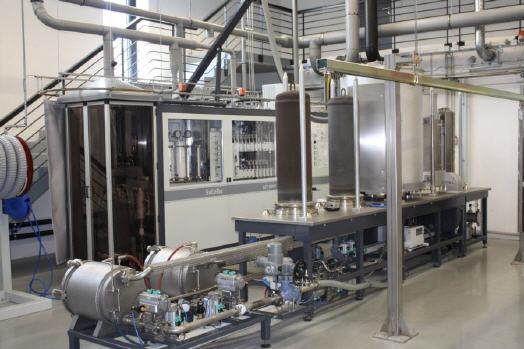
CVD-Beschichtungsanlage ›SCT 400TS‹ von SuCoTec
Waren es in der industriellen Anfangszeit Werkzeugstähle und Hochleistungsschnellschnittstähle, die man zum Zerspanen verwendete, wurden bereits ab 1923 Hartmetalle eingesetzt. Das Ziel: die Standzeit beim Zerspanen weiter steigern. Immer neue HM-Substratmischungen kamen auf den Markt, um den Anforderungen unterschiedlicher zu zerspanender Materialien gerecht zu werden.
Sehr bald wurde überlegt, dass das Beschichten der Hartmetalloberfläche eine weitere Steigerung der Standzeiten ermöglichen sollte. Alleine die Umsetzung machte Probleme. Die Lösung wurde in der Atomforschung geboren: die Hartstoffbeschichtung im Plasma. Hier haben sich zwei Verfahren etabliert, die sich gegenseitig ergänzen, da diese in unterschiedlichen Temperaturbereichen arbeiten und Schichten unterschiedlicher Dicke und Kristallstruktur erzeugen können: Das PVD- und das CVD-Verfahren.
Zwei Verfahren, ein Vorteil
Das PVD-Verfahren (Physical Vapour Deposition) unterscheidet sich vom CVD-Verfahren (Chemical Vapor Deposition) nicht nur in der zu erzielenden Schichtdicke, sondern auch in der Arbeitstemperatur und der Art, wie die Hartstoffschicht auf die Werkstückoberfläche aufgebracht wird.
Während das PVD-Verfahren zwischen 50 und 500 Grad Celsius angewandt wird und daher gerade für Kunststoffe, Leichtmetalle und auch Hartmetalle prädestiniert ist, benötigt das CVD-Verfahren wesentlich höhere Temperaturen, die bis zu 1000 Grad Celsius gehen. Da die Reaktionsheftigkeit von Teilchen untereinander zunimmt, wenn die Temperatur steigt, ist es naheliegend, dass CVD-Schichten besser an der Oberfläche des beschichteten Werkstücks haften.
Die geringe Arbeitstemperatur des PVD-Verfahrens hingegen erlaubt es, hochwertige Produkte aus Kunststoff, Leichtmetall oder gelötete und Voll-Hartmetallwerkzeuge mit einem robusten Verschleißschutz zu versehen. Was früher nur lackiert oder mit Folie bezogen wurde, wird heute in eine PVD-Beschichtungsanlage geschoben und erhält dort einen optimalen Schutz vor Kratzern und Verschleiß.
Es ist hochinteressant zu erfahren, wie das geschieht. Das Geheimnis liegt darin, dass im PVD-Verfahren Scheiben, sogenannte Targets, die aus dem Material bestehen, mit dem man das Werkstück beschichten möchte, entweder via Lichtbogen-Verfahren oder durch Sputtern an der stirnseitigen Oberfläche zum Verdampfen gebracht werden. Per Plasma wird Material von den Targets in die vakuumierte und beheizte Reaktionskammer abgegeben, wo es sich Atomlage für Atomlage auf der zu beschichtenden Oberfläche absetzt.
Je länger dieser Prozess dauert, desto mehr Lagen werden gebildet, bis eine maximale Schichtdicke erreicht ist, deren Grenze u.a. durch Eigenspannungen im Schichtmaterial bestimmt wird. Typische Schichtdicken liegen daher zwischen 1 und 8 Mikrometer. Dickere Schichten haben durch die erwähnten Spannungen keinen Halt und können Abplatzen.
Beim CVD-Verfahren hingegen wird kein Material verdampft. Hier befindet sich das Material, mit dem die Oberfläche eines Teils beschichtet werden soll, in einem Gas, das in die Arbeitskammer geleitet wird.
Wendeschneidplatten für Zerspanwerkzeuge können im CVD Verfahren beschichtet werden, dies hat den Vorteil, dass dadurch im Vergleich zum PVD-Verfahren, Hartstoffschichten mit besserer Schichthaftung und größerer Schichtdicke (typischerweise bis zu 16 µm) hergestellt werden können. Die so beschichteten Wendeschneidplatten weisen haben folglich eine enorme Verschleißbeständigkeit.
Gleiches noch lange nicht gleich
Das Beschichten hat sich gerade bei zerspanenden Werkzeugen bewährt und diesen einen gewaltigen Leistungsschub beschert. Hier sind die Beschichtungsspezialisten besonders gefordert, damit die Werkzeuge ihre optimalen Eigenschaften erhalten. Es gibt eine große Zahl an Parametern, die Standzeit und Maßhaltigkeit der Werkzeuge beeinflussen.
Eine TiN-Schicht des einen Herstellers ist noch lange nicht identisch mit einer TiN-Schicht eines Wettbewerbers. Jeder Hersteller hat seine besonderen Anlagenparameter, die ähnlich wie ein Staatsgeheimnis gehütet werden. Es spielt der Schichtaufbau ebenso eine Rolle, wie die Anzahl der Schichtlagen oder die Schicht-Reihenfolge. Eine Vielzahl an Schichtlagen wird in ausgeklügelter Weise teilweise in wenigen hundert Nanometer Dicke übereinandergelegt. Dieser Schichtaufbau verhindert zudem, dass sich Risse, die beim Zerspanen entstehen, nach innen fortpflanzen. Dies erklärt, warum Werkzeuge bestimmter Hersteller einfach besser sind.
Nur ein Beispiel: Beim Zerspanen soll die Wärme möglichst komplett im Span bleiben und mit diesem in die Spänewanne fallen. Dies bedeutet für den Schichtaufbau der Wendeschneidplatte, dass die oberste Schicht extrem verschleißfest und besonders schlecht wärmeleitend sein muss. Wäre die Schicht ein guter Wärmeleiter, würde ein großer Teil der Wärme in die Wendeschneidplatte beziehungsweise das Zerspanungswerkzeug wandern, woraufhin diese, bei entsprechender Zerspanungsarbeit, in kurzer Zeit ausglühen würde. Der weitere Aufbau der unteren Schichtlagen der Platte ist unter anderem darauf ausgerichtet, die Haftung der Schichten zu optimieren.
Eigenes Wissen ist Gold wert
Das Wissen um die optimale Schicht für das jeweilige Werkzeug ist daher ein Garant, sich vom Wettbewerb abzusetzen und den Kunden Werkzeuge mit besten Standzeiten in die Hand zu geben. Aus diesem Grund verlässt sich Mapal nicht auf das Know-how externer Beschichtungs-Dienstleister, sondern hat mit dem Kauf einer eigenen CVD-Anlage die Weichen gestellt, noch mehr Leistung aus den eigenen Werkzeugen herauszuholen.
Mit der Anlage ›SCT 400TS‹ des Herstellers SuCoTec wurde feinste Technik in Betrieb genommen, die nach Mapal-Aussage den neuesten Stand der CVD-Beschichtungstechnik repräsentiert und zu den weltweit modernsten Beschichtungsanlagen gehört. Mapal-Kunden können sich also sicher sein, stets Werkzeuge zu erhalten, deren Leistungsfähigkeit und Standzeit nicht zu toppen ist.
Download
Diesen Artikel können Sie hier im PDF-Format [200 KB] herunterladen.
Mehr Informationen zur MAPAL Dr. Kress KG:
![]() |
MAPAL Dr. Kress KG |
![]() |
Obere Bahnstr. 13 |
![]() |
73431 Aalen |
![]() |
Tel.: 0 73 61 / 5 85 - 0 |
![]() |
Fax.: 0 73 61 / 5 85 - 1 50 |
![]() |
E-Mail: info@de.mapal.com |
![]() |
www.mapal.com |
War dieser Artikel für Sie hilfreich?
![]() |
![]() |
![]() |
![]() |
![]() |
Bitte bewerten Sie diese Seite durch Klick auf die Symbole.
Zugriffe heute: 1 - gesamt: 3449.