Verbesserung der Dichtungseigenschaften
Hart/Hart-Paarungen im Fokus
Bei jeder berührenden mechanischen Dichtung wird vorausgesetzt, dass die beiden Gegenlaufpaare optimal ausgeführt und aufeinander abgestimmt sind. In der Praxis lässt die Zuverlässigkeit dieser Elemente jedoch zu wünschen übrig. Morgan Advanced Materials hat nun Patentiertes im Portfolio.
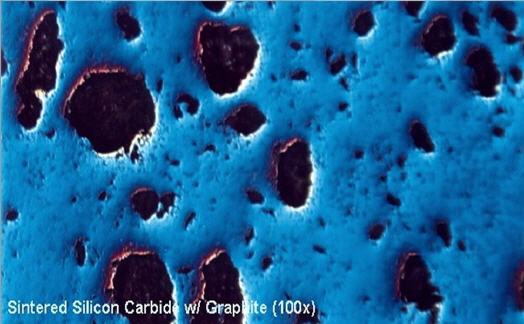
Um Leckagen zu verhindern, werden unterschiedliche Werkstoffe eingesetzt, darunter synthetisch hergestellter Kohlenstoff mit Gummi- oder Antimon-Imprägnierung, Metalle und harte Beschichtungen, Aluminiumoxid, Hartmetall und Siliciumkarbid. Die letzten drei Werkstoffe zeichnen sich durch eine harte Oberfläche aus. Gegenwärtig kommt besonders häufig Siliciumkarbid zum Einsatz. Um die Gefahr einer Leckage im Bereich der Dichtfläche auszuschließen, ist häufig eine Planheit der Gleitflächen von maximal drei Heliumlichtbändern (0,000033 Zoll) gefordert.
Die Kraft, die die Dichtung schließt, wird üblicherweise mechanisch, z. B. durch Federn, aufgebracht. Die hydraulischen Kräfte, die durch die Dichtungsausführung selbst erzeugt werden, pressen die Dichtflächen so stark gegeneinander, dass es letztendlich zum Verschleiß einer oder beider Gleitflächen kommt. Diese harten Dichtflächenwerkstoffe werden häufig bei besonders anspruchsvollen Anwendungen eingesetzt, bei denen sich die beiden Dichtflächen berühren. So kann z. B. Siliciumkarbid mit Siliciumkarbid oder aber Siliciumkarbid mit Hartmetall kombiniert werden.
Je anspruchsvoller die Einsatzbedingungen der Dichtungen sind, desto wichtiger ist es, dass die harten Dichtflächenwerkstoffe effizient aneinander reiben, um ihre positiven Eigenschaften zur Geltung zu bringen. Anders als synthetisch hergestellte Kohlenstoffwerkstoffe sind diese harten Dichtungswerkstoffe nicht selbstschmierend und bedürfen daher bei längerem Einsatz einer Flüssigkeitsschmierung. Weitere Verbesserungen sind nötig, um die beiden Dichtflächen optimal aufeinander abzustimmen.
Die Entwicklung von Siliciumkarbid-Werkstoffen
1.1 Monolitische Siliciumkarbide
Siliciumkarbid ist hart und zeichnet sich durch eine hervorragende Verschleißfestigkeit aus. Kennzeichnend sind ferner ein geringer Reibungskoeffizient, wenn Schmierung zum Einsatz kommt, eine hohe Härte und ein hohes Elastizitätsmodul. Es behält außerdem auch bei hohen Temperaturen seine Festigkeit, hat einen geringen Wärmedehnungskoeffizienten, hohe Wärmeleitfähigkeit und eine hervorragende Korrosionsbeständigkeit.
1.2 Siliciumkarbid mit Graphitfüllung
In den 70-er Jahren führte der Einsatz der chemischen Gasphasenabscheidung zu einer Verbesserung der berührenden Dichtungen mit Siliciumkarbid. Die poröse äußere Oberfläche der Dichtung entsteht durch eine Reaktion zwischen dem Siliciumkarbid und dem Graphit und enthält sowohl Siliciumkarbid als auch Graphit. Es handelt sich nicht um eine Beschichtung. Die Oberfläche schließt einen Kohlenstoffkern ein und verfügt über eine gehärtete Oberfläche mit einer einzigartigen Oberflächengüte, die eine verbesserte Oberflächenschmierung begünstigt.
Der Einsatz dieses Werkstoffes ist dadurch begrenzt, dass er nur nach vorhergehender Imprägnierung zuverlässig dicht ist. Die Graphitfüllung schränkt zudem gewünschte physikalische Eigenschaften, wie das Elasitizitätsmodul, ein. Durch den Einsatz dieses Werkstoffes konnte gezeigt werden, dass beide Teile eines Gegenlaufpaares aus einem harten nicht selbst-schmierenden Werkstoff bestehen können und sich ihre Leistungsfähigkeit gegenüber den Gegenlaufpaaren aus Standardwerkstoffen verbessert. Dieser Werkstoff wird heute nach wie vor eingesetzt.
1.3 Rekationsgebundenes Siliciumkarbid
Homogene Werkstoffe wie reaktionsgebundenes Siliciumkarbid bieten die Vorteile geringer Porosität, eines höheren Elastizitätmoduls (Steifheit), besserer Wärmeleitfähigkeit sowie guter tribologischer Eigenschaften, wenn sie in Kombination mit einem geeigneten Werkstoff, wie synthetisch hergestelltem Kohlenstoff, zum Einsatz kommen. Aufgrund der hohen Herstellungskosten wurde ihr Einsatz in Hochleistungsanwendungen ursprünglich auf chemisch weniger aggressive Umgebungen beschränkt. Diese Werkstoffe erforderten aufwändige Schleifprozesse und das freie Silicium in der Struktur ging in ätzenden oder sauren Umgebungen leicht eine chemische Reaktion ein.
Diese Werkstoffgruppe hat sich bei einigen Anwendungen schnell durgesetzt, da eine Erhöhung des abzudichtenden Druckes nicht, wie das bei metallischen Werkstoffen der Fall wäre, zu einer nennenswerten Oberflächenverformung führt. Üblicherweise wurde ein harter, synthetisch hergestellter, häufig mit Antimon imprägnierter Hochleistungskohlenstoff in Verbindung mit einem reaktionsgebundenen Siliciumkarbid eingesetzt.
1.4 Gesintertes Siliciumkarbid
Gesintertes Siliciumkarbid (auch bekannt als drucklos gesintertes, direktgesintertes oder bei niedrigem Druck gesintertes Siliciumkarbid) eröffnet aufgrund des Herstellungsprozesses weitere Einsatzmöglichkeiten. Der Werkstoff kann in definierte Formen gebracht und dann beinahe auf Endmaß gesintert werden. Dadurch können teure Schleifprozesse eingespart werden. Aufgrund der geringen Produktionskosten und des homogenen Erscheinungsbildes wird ein Einsatz in hochkorrosiven Umgebungen bei hohen Stückzahlen möglich.
Gesintertes Siliciumkarbid ersetzte zunehmend andere Werkstoffe wie z. B. Aluminium, bei dem ein besseres Verhältnis aus Flächenpressung und Gleitgeschwindigkeit erforderlich ist. (Das Verhältnis aus Flächenpressung und Gleitgeschwindigkeit ist eine Kenngröße, die beschreibt, wie anspruchsvoll eine Anwendung ist. Es dient zur Beurteilung von Werkstoffkombinationen und wird durch weitere Parameter wie das abzudichtende Medium beeinflusst.) Ungünstigerweise verfügt dieses monolithische Material nicht über dieselben tribologischen Eigenschaften wie reaktionsgebundenes Siliciumkarbid als Zweiphasenwerkstoff. Auch scheidet ein Einsatz bei extrem hohen Belastungen aus. Hier gilt wiederum, dass die Werkstoffeigenschaften die Einsatzmöglichkeiten begrenzen.
1.5 Siliciumkarbid mit eingelagertem Graphit
Im Laufe der Jahre wurden Siliciumkarbid-Werkstoffe immer weiter entwickelt. Heute findet man sie häufig in Form eines Zweiphasenwerkstoffes, der in Hochleistungsanwendungen zum Einsatz kommt. Am weitesten verbreitet ist eine Kombination aus Siliciumkarbid mit Graphit. Dieser Verbundwerkstoff wird als Siliciumkarbid mit eingelagertem Graphit bezeichnet, da das Graphit in die Struktur des Siliciumkarbids integriert ist. (Das Siliciumkarbid ist also nicht imprägniert.) Durch das eingelagerte Graphit entstehen kleine Kavitäten an der Oberfläche und somit eine optimierte Wirkflächentextur ohne ungewollte Leckagen. Durch diese Textur werden die Eigenschaften der Dichtflächen verbessert.
Ein Einsatz bei höherer Flächenpressung und größerer Gleitgeschwindigkeit wird möglich. Die Werkstoffe können auf spezielle Anwendungen zugeschnitten werden. Anfänglich wurde Graphit in reaktionsgebundenes Siliciumkarbid eingelagert. Dies führte schnell zu einer Steigerung der Leistungsfähigkeit bei Hart/Hart-Paarungen. Während die Festigkeit etwas sinkt und die Abrasion weniger gut als bei monolithischem Karbid beherrscht wird, verbessern sich die tribologischen Eigenschaften deutlich.
Durch den Einsatz dieses Werkstoffes für wenigstens eine der beiden Oberflächen konnte die Lebensdauer der Dichtung in einigen Fällen von wenigen Minuten auf hunderte von Stunden verlängert werden. Gesintertes Siliciumkarbid mit eingelagertem Graphit wird seit mehr als zehn Jahren in Hart/Hart-Paarungen eingesetzt. Diese einzigartige Verbundwerkstoff-Gruppe verbindet die Vorteile des gesinterten Siliciumkarbids mit dem positiven Effekt des Abriebs, durch die das Fluid in kleinen Kavitäten gespeichert wird.
1.6 Siliciumkarbid mit kristallinem Diamant
Diamant ist der härteste Werkstoff mit exzellenten tribologischen Eigenschaften, hervorragender Wärmeleitfähigkeit und chemischer Widerstandsfähigkeit. Diese Qualitäten werden auf die Oberfläche eines konventionell gefertigten Siliciumkarbid-Rings übertragen, indem eine kristalline Diamantschicht auf dessen Oberfläche erzeugt wird. Dies lässt sich dadurch erreichen, dass man den Siliciumkarbid-Ring in eine Kammer gibt, in der der Druck, das Gasgemisch und die Temperatur genauestens kontrolliert werden. Ein kohlenstoffhaltiges Gas wie Methan (CH4) wird in die Kammer eingeführt. Unter den richtigen Prozessbedingungen wachsen Diamantkristalle auf dem Siliciumkarbid.
Dieser Prozess heißt chemische Gasphasenabscheidung (CVD) und findet unter Vakuum bei Temperaturen um die 800?C statt. Der Diamant entsteht nicht aus der Gasphase, sondern wächst auf der Oberfläche des Siliciumkarbids. Je mehr die kleinen Diamantkristalle wachsen, umso mehr verbinden sie sich miteinander und bilden so eine geschlossene Diamantoberfläche. Die Eigenschaften der Diamantschicht werden durch definierte Prozessbedingungen festgelegt. Die Höhe der Temperatur bestimmt die Festigkeit der Bindung zwischen der Diamantschicht und dem Siliciumkarbid. Es ist wichtig während des Prozesses die Planheit der Dichtflächen deutlich unter zwei Heliumlichtbändern zu halten. Diese Verbesserungen bringen Vorteile bei Anwendungen in anspruchsvollen Umgebungen, haben aber ihren Preis.
Die Dichtfläche
Die Leistung und Zuverlässigkeit einer mechanischen Dichtung wird wesentlich von ihrer Oberflächenbeschaffenheit, d.h. also der Form, der Höhe und der Tiefe der Oberflächenmikrostruktur beeinflusst. So ist z. B. ein monolithisch gesintertes Siliciumkarbid so homogen und fest, dass es, bedingt durch seine Struktur, keine Oberflächenrauheit hat. Wenn dieses Material durch Läppen auf normale Dichtungsflächenstandards gebracht wird, kann es zu Festkörperkontakten der Reibpartner im Reibspalt kommen. Dies bedingt eine sehr hohe Haftreibung und Mangelschmierung, wodurch die Dichtflächen beschädigt werden können.
2.1 Läppen (matt)
Üblicherweise werden durch den Läppvorgang Mikrokratzer auf der Dichtfläche induziert. Durch diese kann das Medium in und durch den Reibspalt gelangen, ein Festkörperkontakt der beiden Reibpartner wird vermieden. Aber im Laufe der Zeit wird die Oberfläche wieder glatt poliert, es stellen sich wieder die gleichen Bedingungen ein, die zwar theoretisch optimal sind, um Leckagen zu verhindern, aber eine tribologische Herausforderung für diese nicht schmierenden monolithischen Werkstoffe mit harten Oberflächen darstellen. Das Siliciumkarbid mit Graphitfüllung wurde dahingehend weiterentwickelt, dass das Graphit nun in die Struktur des Siliciumkarbids eingelagert wird.
Dies führt zu kleinen Kavitäten auf der Dichtfläche und gewährleistet eine definierte Oberfläche für die Schmierung ohne ungewollte Leckagen. Der Vorteil dieser neuen Entwicklung ist, dass das Graphit nicht nur in der Oberfläche, sondern im gesamten Dichtkörper eingelagert ist. Dadurch weist dieser während seiner gesamten Lebensdauer verbesserte Eigenschaften auf. Es ist auch möglich, in einer gegebenen Anwendung die Menge und Partikelgröße des Graphits in der Struktur genau festzulegen.
2.2 Wirkflächentextur
Die Kontrolle der Oberflächenbeschaffenheit in Bezug auf Größe, Verteilung und Tiefe des Graphits bedingt eine bestimmte Wirkflächentextur. Dadurch können die Hart/Hart-Paarungen auch bei hoher Flächenpressung und hoher Gleitgeschwindigkeit eingesetzt werden. Wie unten gezeigt, weisen Gegenlaufpaare aus Siliciumkarbid-Verbundwerkstoffen mit eingelagertem Graphit im Vergleich zu allen anderen Hart/Hart-Paarungen die besten Flächenpressungs- und Gleitgeschwindigkeitswerte auf. Wenn die Siliciumkarbid-Verbundwerkstoffe mit eingelagertem Graphit mit einem Kohlenfaserwerkstoff kombiniert werden, sind die Flächenpressungs- und Gleitgeschwindigkeitswerte sogar noch besser.
Die Möglichkeit, die Wirkflächentextur über die chemische Zusammensetzung und die Prozessführung genau zu kontrollieren führt dauerhaft zu verbesserten Eigenschaften der Dichtflächenkombinationen. Dies gilt insbesondere für Hart/Hart-Paarungen. Außerdem kann bei anspruchsvollen Anwendungen durch die Beeinflussung der Textur sehr gut auf die Kundenwünsche eingegangen werden. Eine verbesserte Textur von wenigstens einer der Kontaktoberflächen kann die Lebensdauer des Gegenlaufpaares deutlich verlängern. Je nach der Art der Endbearbeitung, die zur Erzeugung der Wirkflächentextur angewendet und durch die Menge an Graphit im Verbundwerkstoff beeinflusst wird, lassen sich die mechanischen Leistungsdaten der Dichtung, wie unten gezeigt wird, leicht vorhersagen.
2.3 Mechanische Eigenschaften
Die Materialeinlagerungen in der Struktur des Siliciumkarbids und die Verbesserung der tribologischen Eigenschaften sind nicht nur positiv zu betrachten, da auch ungewünschte Nebeneffekte entstehen können. Insbesondere kann es zu Kantenausbrüchen an den Materialgrenzen kommen. Die entstandenen Bruchstücke können die Oberfläche beschädigen. Ein gesinterter Siliciumkarbid-Verbundwerkstoff mit einer sauber konfigurierten Graphitstruktur kann eine gute Verbindung zwischen der Kavität und der Siliciumkarbid-Matrix sicherstellen. Der Verschleiß eines Siliciumkarbid-Graphit-Verbundwerkstoffes kann auch durch die Menge des eingelagerten Graphits beeinflusst werden.
Der Wechsel von einem monolitischen Siliciumkarbid zu einem Verbundwerkstoff kann auch zu einer Verschlechterung der physikalischen Eigenschaften des Werkstoffes führen. Durch diese Eigenschaften können die Einsatzmöglichkeiten dieser tribologisch verbesserten Werkstoffe begrenzt werden, wenn sie unter Bedingungen eingesetzt werden, bei denen das Elastizitätsmodul und die Festigkeit eine wichtige Rolle spielen. Es gibt jedoch eine Eigenschaft, die sich beim Hinzufügen einer zweiten Phase verbessert: die thermische Wechselbeständigkeit ist bei den Verbundwerkstoffen besser als bei monolithischen Werkstoffen.
2.4 Siliziumkarbid-Verbundwerkstoffe
Die Siliziumkarbid-Verbundwerkstoffe mit eingelagertem Graphit bieten höhere Zuverlässigkeit bei Hart/Hart-Paarungen. Nicht alle Verbundwerkstoffe mit eingelagertem Graphit sind gleich. Der Prozess der Einlagerung der zweiten Phase ist genauso kritisch wie ihre Anwesenheit in der Werkstoffmatrix. Die Anwesenheit der zweiten Phase hat negative Auswirkungen auf wichtige Eigenschaften des Werkstoffes und begrenzt damit seine Einsatzfähigkeit unter technisch anspruchsvollen Bedingungen. Dieser Umstand hat zur Entwicklung von „Hybrid-Sliziumkarbid“ geführt.
Hybrid-Siliziumkarbid
Einmal entwickelt wurde der Kompositwerkstoff Hybrid-Siliziumkarbid dahingehend verbessert, dass er im Werkstoffinneren die physikalischen Eigenschaften eines homogenen Siliciumkarbids aufweist, an der Dichtfläche jedoch die Vorteile des eingelagerten Graphits zum Tragen kommen. Die Aufbringung einer Zwei-Phasen-Verbundwerkstoff-Textur auf ein homogenes Substrat bringt einerseits die physikalischen Eigenschaften des Siliciumkarbid-Körpers, andererseits die Verbesserung der tribologischen Eigenschaften des Verbundwerkstoffes mit sich (Patent angemeldet).
Dank dieser Entwicklung kann die Struktur des Siliciumkarbid-Verbundwerkstoffes mit eingelagertem Graphit anwendungsspezifisch ausgelegt und die Dichtfläche damit entsprechend den Anforderungen gestaltet werden, ohne dass die physikalische Festigkeit oder sonstige Werkstoffeigenschaften beeinträchtigt würden. Die tribologisch verbesserten Oberflächen können je nach endgültigem Einsatzzweck des Bauteils auf die Dichtungsfläche und / oder den Durchmesser aufgebracht werden. Die verbesserte Oberflächendicke kann theoretisch 0,2 mm betragen, liegt in der Praxis aber üblicherweise bei etwa einem Millimeter.
Schlussfolgerung
Die Gegenlaufpaare einer mechanischen Dichtung sind sicherheitsrelevante Bauteile, und Siliciumkarbid ist nach wie vor einer der am weitesten verbreiteten und günstigsten Werkstoffe. Während die physikalischen Eigenschaften der Werkstoff-Matrix durch die Einlagerung von tribologisch vorteilhaften Zusätzen wie z.B. Graphit negativ beeinflusst werden können, werden die eigentlichen Dichteigenschaften insbesondere bei ungünstigen Schmierungsbedingungen verbessert. Eine zum Patent angemeldete Entwicklung erlaubt die strategische Ausrichtung der tribologischen Oberflächen und verfügt über die besten Eigenschaften sowohl der monolithischen Werkstoffe als auch der Verbundwerkstoffe.
Mehr Informationen zu Morgan Technical Ceramics:
![]() |
Morgan Technical Ceramics |
![]() |
Teplitzerstrasse 27 |
![]() |
84478 Waldkraiburg |
![]() |
Tel.: +49 (0) 86 38 600 40 |
![]() |
Fax: +49 (0) 86 38 810 900 |
![]() |
www.morgantechnicalceramics.com |
War dieser Artikel für Sie hilfreich?
![]() |
![]() |
![]() |
![]() |
![]() |
Bitte bewerten Sie diese Seite durch Klick auf die Symbole.
Zugriffe heute: 1 - gesamt: 3017.