Spritzgießen deluxe
Werkzeugtechnik mit konturnaher Kühlung
Rowenta eine neue, innovative Modellreihe von Bügeleisen eingeführt. Am Fertigungsstandort von Rowenta in Erbach im Odenwald entstehen die neuesten dieser ebenso hochwertigen wie praktischen Haushaltshelfer.
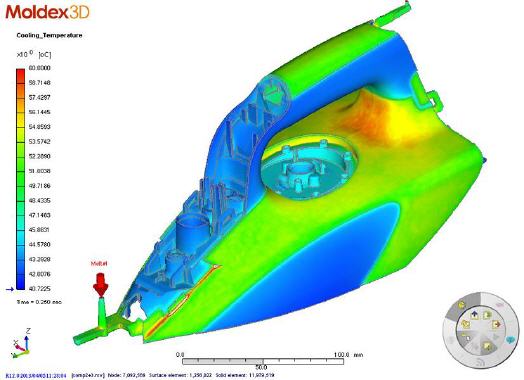
Die Besonderheiten bei Rowenta sind eng mit dem Produkt verknüpft: Das Bügeleisen muss hitzebeständig sein, es braucht einen Tank für Wasser, sowie eine Dampferzeugung und eine gute Sohle soll für ein perfektes Bügelergebnis sorgen – tagein, tagaus, Jahr für Jahr. Dies stellt besondere Anforderungen an Komponenten und Fertigung bzw. Montage.
Herzkammer bei Rowenta: Die Montage
Alle Hauptkomponenten, also Griff, Tank und Hitzeschild, werden in der eigenen Kunststofffertigung hergestellt. Die Funktionsmechanik, Thermostat und Sohle kommen von Zulieferern als fertige Module in die Endmontage. Komplett automatisierte Fertigungsstraßen können alle unterschiedlichen Modelle sequentiell abarbeiten. Von Biegeautomaten, die filigrane Drähte biegen, über Plasmabehandlung bis zur Veredelung durch Bedampfen oder Bedrucken ist alles zu sehen, was man für Qualität „Made in Germany“ braucht.
Fertigungsstrategien und Einstufen-Prozesse
Qualität „Made in Germany“ bedeutet auch eine Anpassung der Fertigung unter Kostengesichtspunkten. Im Jahre 2004, so Jochen Weber, stieg Rowenta in die 3K-Technik ein. Der Werkzeugbau Hofmann lieferte dazu Werkzeuge mit konturnaher Kühlung, eine damals völlig neue Konzeption im Werkzeugbau. Dies ermöglichte einige wesentliche Pluspunkte: Weniger Montageaufwand, bessere Funktionsintegration, bessere Teilequalität, eine kürzere Zykluszeit und generell günstigere Stückkosten durch die Konzentration auf mögliche Einstufen-Prozesse.
Dahinter steht eine konsequente Ausrichtung von Maschinen- und Werkzeugtechnik in der Produktion. Für die 2K- und 3K-Kunststofffertigung kommen Wendeplattentechnik, Drehtellerwerkzeuge und Indexplattentechnik zum Einsatz. Für jedes Bügeleisenmodell wird nach einer optimalen Strategie von Werkzeug- und Maschinentechnik gesucht. Die Wahl einer Drehteller- oder einer Wendeplattenlösung ergibt sich aus der Kapazitätsplanung oder auch aus den Losgrößen. Generell gilt auch: In den Fertigungszellen der Fertigung ist alles automatisiert, was automatisiert werden kann.
Werkzeugtechnik mit konturnaher Kühlung von Hofmann
Die reibungslose Montage der Baugruppen mit sehr komplexen Stegen auf engstem Raum oder zahlreichen Funktionsteilen wird durch eine konsequente Ausrichtung der Kunststoffformen auf konturnahe Kühlung möglich. „Dabei ergibt sich in der Konstruktion sehr oft eine Kombination von konturnaher Kühlung mit Einsätzen, die mit dem Metall-Laserschmelzverfahren LaserCUSING generativ hergestellt werden, und klassisch temperierten Flächen.
Konturnahe Kühlung setzt generell immer an den kritischen Stellen, also Stegen, schwierigen Kernzonen oder atypischen Materialanhäufungen an“, schildert Jochen Weber seine Erfahrungen mit dem Konzept von Hofmann. Als konstruktive Maßnahmen gelten formgerechte Kühlkanaldurchmesser und der Einsatz von Parallelkühlungen an physikalisch besonders anspruchsvollen Stellen, um möglichst viel Kühlleistung an die Oberfläche der Kavität zu bringen. Damit die Kühlkanäle einwandfrei funktionieren und den erforderlichen Volumendurchsatz aufweisen, achtet Fertigungsleiter Robert Löw auf Prävention durch einen Korrosionsinhibitor.
In der Praxis spricht man auch von „geimpftem“ Wasser, um Ablagerungen und Partikelverunreinigungen zu vermeiden. Dies gilt insbesondere für rotierende Formen, die an den mechanischen Übergangsstellen auch hinsichtlich der Dichtigkeit überprüft werden müssen. Das bewährte Temperierungskonzept von Hofmann gilt bei Rowenta als die effektivste Methode der Wahl.
Erfahrungen der konturnahen Kühlung von Hofmann
Konstruktions- und funktionsbedingt ist das Bügeleisen durch die ausgeprägten Verrippungen ideal für eine konturnahe Kühlung geeignet. Bei einem 3K-Teil sind die Zykluszeitverbesserungen und Verminderungen des Verzugs gegenüber den Werkzeugen von vor fast zehn Jahren deutlich erkennbar. In diesem Zeitraum lieferte Hofmann zahlreiche Werkzeuge mit dieser Technik aus, die bei Rowenta zum großen Teil bis heute im Einsatz sind. Wesentlich ist die Verzugsfreiheit.
Sie ist für das positive „Montageverhalten“, also für die hohe Maßhaltigkeit verantwortlich, die sich aus den zahlreichen Dornen oder auch Metallröhrchen ergibt, die exakt eingepasst werden müssen. Auch fertigungstechnisch ist dies relevant: So kann Fertigungsleiter Robert Löw bei Produktionsanläufen in den mit LaserCUSING-Einsätzen konturnah gekühlten Bereichen sehr schnell die geforderte Maßhaltigkeit erreichen, um dann mit den Prozessparametern an anderen Stellen zu variieren bis sich ein stabiler, reproduzierbarer Prozess einstellt. Dies ergibt eine gewisse Flexibilität des Prozessfensters.
Die Komplexität bis ins Detail beherrschen
Die Simulationssoftware Moldex3D von SimpaTec, mit der Hofmann das Kühlkonzept konzipiert, ermöglicht dem Konstrukteur einen virtuellen Blick ins Innere des Werkzeuges. Aussagen über das Strömungsverhalten, Temperaturverteilungen, Druckverluste, sowie Fließgeschwindigkeiten stehen zur Beurteilung der optimalen Kühlmethode zur Verfügung. „Dies ist speziell dann unverzichtbar, wenn die Temperierkanäle in unseren LaserCUSING-Einsätzen so komplex werden, dass man sich die Durchströmung nicht mehr ohne Weiteres im Kopf vorstellen kann," erläutert Stefan Hofmann, „hier greifen wir zur Auslegung und Kontrolle der Kühlkanalkonstruktion immer auf die Simulation zurück."
Moldex3D in der 3K-Technik
Der Fokus beim 3K-Bügeleisengehäuse von Rowenta lag in der Reduzierung der Verzugsneigung im vorderen Teilbereich, die durch eine möglichst homogene Temperaturverteilung in der Abkühlungsphase des Spritzprozesses realisiert werden sollte.
Dreidimensionale Darstellungsergebnisse und -animationen des Verzuges verdeutlichen das Verzugsverhalten des Endproduktes und können so helfen, die konturnahe Temperierung auszulegen oder zu optimieren. Neben der Fragestellung der idealen Temperierung bietet Moldex3D zusätzlich die Möglichkeit, das Zusammenspiel der verschiedenen Komponenten, Materialien und Geometrien genauestens zu analysieren.
Beide Aspekte - Transparenz und Optimierung – führen zu einem qualitativ hochwertigen Bauteil. Gesamtzykluszeiten werden verkürzt, Produktionskosten gesenkt, eventuelle Werkzeugnachbearbeitungen auf ein Minimum reduziert und damit werden deutlich kürzere Entwicklungsprozesse möglich.
Entwicklungsdurchlauf und enge Zusammenarbeit mit dem Werkzeugbauer
Für das neue Modell agierte Hofmann Innovation Group aus Lichtenfels erneut als Werkzeugpartner. Die Entwicklungszeiten bewegen sich je nach Aufwand eines neuen Modells zwischen 12 und 16 Monaten. Dabei arbeiten in der Produktentwicklung bis zum SOP (Start-of-Production), Designer, Projektleiter und Konstrukteure des Hofmann Werkzeugbaus sowie Fertigungsverantwortliche eng zusammen, um das Projekt zeitlich einhalten zu können. Das erfordert eine hohe Flexibilität der Akteure und ein eng vernetztes Arbeiten – sowohl parallel als auch gemeinsam.
Die Einbindung des Werkzeugbaus mit seinen produktbegleitenden Dienstleistungen in das Projekt senkt die Kosten und minimiert den Änderungs- und Freigabeaufwand. „Für die 3K-Teile des neuen Modells war für uns der Werkzeugbau Hofmann, dessen Werkzeugkonzepte mit konturnaher Kühlung seit vielen Jahren hohe Maßhaltigkeit versprechen, der Partner der Wahl“, so Jochen Weber.
Mehr Informationen zur Hofmann Innovation Group:
![]() |
Hofmann Innovation Group AG |
![]() |
An der Zeil 2 |
![]() |
96215 Lichtenfels |
![]() |
Telefon +49 (0) 9571 - 76 67 00 |
![]() |
Telefax +49 (0) 9571 - 76 67 09 |
![]() |
E-Mail: info@hig-ag.de |
![]() |
www.hig-ag.de |
War dieser Artikel für Sie hilfreich?
![]() |
![]() |
![]() |
![]() |
![]() |
Bitte bewerten Sie diese Seite durch Klick auf die Symbole.
Zugriffe heute: 1 - gesamt: 3256.