Almig: Auf schwankenden Bedarf flexibel reagieren
Schraubenkompressor mit Wärmerückgewinnung
Mit dem Ziel, die Produktion energieeffizienter zu gestalten und damit noch wettbewerbsfähiger zu sein, hat der international tätige Anbieter von technischer Keramik, die CeramTec GmbH mit Hauptsitz in Plochingen bei Stuttgart, seinen Betrieb nach den Umwelt- und Energiemanagementsystemen ISO 14001 und 50001 zertifizieren lassen.
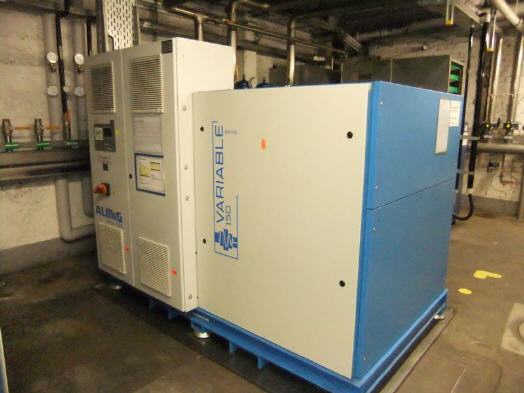
Die Welt richtete im Februar ihr Augenmerk auf die Olympischen Winterspiele im russischen Sotschi. Im Russki Gorki-Skisprung-Zentrum bestritten die Nordischen Kombinierer und die Skisprung-Weltelite ihre Wettkämpfe. Um den Sportlern auf der Normal- und der Großschanze unabhängig vom Wetter die immer gleichen Bedingungen beim Springen zu ermöglichen, sind die Schanzen mit einem Anlaufspursystem von CeramTec versehen.
Das Unternehmen zählt zu den führenden Herstellern von Hightech-Hochleistungskeramik. Mit Sitz im schwäbischen Plochingen in der Nähe von Stuttgart betreibt es weitere Produktionsstätten in Europa sowie in den USA und Asien. Die wissenschaftlich errechnete Form der Keramiknoppen im Anlaufspursystem, die in einer getesteten Anordnung in Spezial-Kautschuk einvulkanisiert sind, das integrierte Kühlsystem sowie die an der Spur installierte Eisfräse mit Bürsten ermöglichen den Springern optimale und immer konstante Gleitbedingungen – Sommer wie Winter. „Sotschi ist zwar ein prominentes Beispiel, aber mit Hochleistungskeramik lassen sich noch ganze andere Sachen machen“, ist sich Werner Portscher, Leiter Instandhaltung bei der CeramTec GmbH, sicher.
„Dieser Werkstoff spielt mit seinen besonderen mechanischen, elektrischen, thermischen oder biologisch-chemischen Eigenschaften meist eine gewichtige Rolle in vielen Anwendungen. Hochleistungskeramik kommt dort zum Tragen, wo andere Werkstoffe versagen“, fügt Stephan Kaiser, technischer Leiter und Fachkraft für Arbeitssicherheit bei CeramTec, hinzu. Ein sehr wichtiges Einsatzfeld für die Schwaben ist die Herstellung keramischer Komponenten für die Medizintechnik.
Als Marktführer für Kugelköpfe und Pfanneninserts für Hüftgelenks-Prothesensysteme, fertigt CeramTec jährlich über eine Million Komponenten, so dass circa alle 30 Sekunden eine Hüft-OP weltweit mit einer CeramTec-Komponente durchgeführt wird. Zum Portfolio gehören zudem Dicht- und Regelscheiben in Sanitärarmaturen, Schneidplatten zur Metallbearbeitung, Träger für elektronische Schaltungen, Geräte- und Maschinenelemente, Sicherungsbauteile, Schutzelemente bis hin zu Piezokeramiken als Kernbauteile von Sensoren. CeramTec liefert sowohl kundenspezifische Einzelanfertigungen als auch Komponenten in Millionenstückzahlen.
Auf energieeffiziente Produktion gesetzt
Bei der Herstellung der Produkte legt das Unternehmen besonders viel Wert auf eine effiziente Prozesstechnologie. Deswegen hat sich CeramTec freiwillig verpflichtet, den Betrieb nach dem Umweltmanagementsystem gemäß der international anerkannten Norm DIN EN ISO 14001 zertifizieren zu lassen. Darin ist das Energiemanagementsystem nach ISO 50001 integriert. Berücksichtigt werden bei dieser kombinierten Zertifizierung unter anderem die kontinuierliche Verringerung der Umweltauswirkungen, die Einhaltung umweltrelevanter Rechtsvorschriften und die Umwelterklärung.
„Gerade bei ständig steigenden Energiekosten prüfen wir ganz konkret, wo wir Einsparungen vornehmen können“, sagt Kaiser. Eine Möglichkeit, Energiekosten zu senken, ist eine effiziente Drucklufterzeugung – da waren sich die Verantwortlichen von CeramTec einig. Deshalb setzt das Unternehmen seit Jahren auf Schraubenkompressoren von ALMiG.
„Technische Keramik herzustellen, ist ein äußerst komplexer Prozess. Das läuft ganz ähnlich ab wie in einer Backstube“, schmunzelt Kaiser. „Statt Mehl und Eiern verwenden wir hochreine Materialien wie Aluminiumoxid, Zirkonoxid, Aluminiumnitrid sowie Siliziumnitrid. Diese Pulver werden aufbereitet und mit Bindemitteln vermischt. „Dabei hat jeder Hersteller seine ganz eigene Rezeptur.“ Im Produktionsprozess setzt das Unternehmen auf spezielle Fertigungsverfahren wie Brennen unter reduzierender Atmosphäre oder heiß-isostatisches Pressen – ein Verfahren, bei dem das Material zugleich unter sehr hohem Druck gepresst und gesintert wird.
Je nach gewähltem Herstellungsverfahren und Kombination der optimalen Ausgangsstoffe lassen sich so gezielt keramische Bauteile mit individuellen Eigenschaften herstellen. Genau wie Teig zu Brot gebacken wird, reift auch die Mischung im Ofen zu Hochleistungskeramik – allerdings bei 1.600 Grad und je nach Anforderung an die Zähigkeit oder Härte zwischen 24 und 72 Stunden. Das Material ist danach so hart, dass es nur mit Diamantwerkzeugen bearbeitet werden kann.
Druckluft den Anforderungen entsprechend anpassen
Die Hartbearbeitung der Bauteile erfolgt in einem hochmodernen Maschinenpark. Darunter befinden sich zum Beispiel Bearbeitungszentren, die die fertig gesinterten Keramikteile von fünf Seiten in einer Aufspannung mit Diamantwerkzeugen bearbeiten können. Auch das Schleifen von äußerst verschleißfesten Komponenten für die Antriebstechnik, etwa Zahnräder oder Schneckenwellen, ist mit dem Maschinenpark möglich. Druckluft kommt zum Beispiel für die Steuerung der Ventile oder Zylinder an den Maschinen zum Einsatz.
Einen großen Stellenwert nimmt sie zudem als sogenannte Sperrluft ein. Damit können Hohlräume mit Hilfe eines Luftüberdrucks berührungsfrei abgedichtet werden. Die Druckluft verhindert somit, dass Bohrwasser oder Späne in die Lager der Bearbeitungsspindeln eindringen oder Linearmaßstäbe und Gleitflächen der Messsysteme beschmutzen, die in der Qualitätssicherung im Einsatz sind.
„Bevor wir das Energiemanagementsystem bei uns eingeführt haben, übernahmen vier luftgekühlte Schraubenkompressoren der Baureihe BELT 55 von ALMiG die Versorgung mit Druckluft“, sagt Portscher. Diese Kompressoren mit einer Leistung von je 55 Kilowatt sorgen für lange Standzeiten und niedrige Wartungskosten. Im Dauerbetrieb sind sie zuverlässig und betriebssicher. Die kompakt gebauten Schraubenkompressoren überzeugen durch eine wirksame Kühlung und eine gute Schall- und Vibrationsdämmung. Zudem lassen sie sich fundamentlos aufstellen und sorgen durch großzügig bemessene Kühler für niedrige Anlagen- und Druckluft-Austrittstemperaturen. „Diese Baureihe wird jedoch im Last-Leerlauf geregelt. Die Kompressoren laufen damit immer bei voller Leistung. Im Rahmen des Energiemanagements sollte der Verbrauch dieser aufwendigen Energieform an den tatsächlichen Bedarf flexibel angepasst werden können.
Leerlaufzeiten vermeiden
Nach eingehender Diskussion mit den ALMiG-Beratern entschied sich das Unternehmen für eine weitere Anlage, einen Schraubenkompressor der Baureihe VARIABLE 150. Dieser öleingespritzte, drehzahlgeregelte und direktangetriebene Kompressor vermeidet damit den Leerlauf und teure Lastwechsel. „Mit dieser Lösung spart CeramTec erheblich Strom“, sagt Armin Salzmann, Gebietsverkaufsleiter bei ALMiG, der den Keramik-Hersteller betreut. „Denn bei mehreren tausend Lastwechseln pro Jahr summiert sich der Energieaufwand beachtlich.“
Die VARIABLE-Baureihe läuft energetisch sehr günstig. Im Vergleich zu den anderen Kompressoren, die im Last-Leerlauf geregelt werden, spart dieser schon allein damit rund 30 Prozent Energie“, erklärt Salzmann. Die VARIABLE 150 liefert zwischen 9,40 und 27,25 Kubikmeter pro Minute. Der Betriebsdruck ist zwischen fünf und 13 bar wählbar. Der Druckluftbedarf kann bei CeramTec bis zu 1,1 Millionen Kubikmeter im Monat betragen. „Mit unserer Lösung lässt sich das sicher bewältigen“, weiß Salzmann.
Die Steuerung der VARIABLE 150 „AIR Control 3“ regelt alle fünf Kompressoren im Verbund. „Die Energievorteile der Drehzahlregelung können wir somit voll nutzen, weil sie nur so viel Druck erzeugen, wie tatsächlich gebraucht wird“, erläutert Salzmann. Dieser Druck wird konstant gehalten. Steigt der Verbrauch an die Maximaldrehzahl, wird einfach ein weiterer Kompressor der Baureihe BELT zugeschaltet. Dabei wird eine Drehzahlreserve beibehalten, so dass keine Druckschwankungen durch Zu- und Wegschalten der Kompressoren entstehen. In der Hauptlastphase, also in der Hauptproduktionszeit, laufen die eingesetzten Anlagen mit gleicher Drehzahl synchron. In der Schwachlastphase, wenn weniger produziert wird, kann auch nur der VARIABLE-Kompressor eingeschaltet sein. Dieser passt sich automatisch an das Verbrauchsprofil an. Er arbeitet immer, auch bei kleinem Druckluftbedarf.
Ölfreie Druckluft nur bei Bedarf
Bei bestimmten Anwendungen muss die Druckluft ölfrei sein – zum Beispiel bei der Herstellung medizinischer Bauteile wie den Keramik-Gleitpaarungen für Hüftgelenksprothesen. „Ölfreie Druckluft kommt auch in der Qualitätssicherung bei den luftgelagerten Messsystemen zum Einsatz“, erklärt Kaiser. Um dabei jegliche Verschmutzung zu vermeiden, wird die Luft mit Zyklon, Vorfilter, Kältetrockner, Feinst- und Aktivkohlefilter aufbereitet. „Für uns ist diese punktuelle Aufbereitung günstiger als eine Aufbereitung der gesamten Druckluft. Denn das wäre mit höheren Wartungskosten verbunden“, sagt Portscher. Energie wird weiterhin durch die integrierte Wärmerückgewinnung gespart.
Bei Schraubenkompressoren mit Öleinspritzung führt das Öl etwa 72 Prozent der zugeführten elektrischen Energie ab. Diese Energie kann zurückgewonnen werden. Die öleingespritzten Schraubenkompressoren sind werkseitig mit Wärmetauscher und Wasserregelventilen zur Heizwassererwärmung auf 70 Grad Celsius ausgestattet“, sagt ALMiG-Berater Salzmann. Der Wärmetauscher lässt eine sehr hohe Wärmeausnutzung zu, er ist platzsparend untergebracht und ermöglicht diese hohen Wassertemperaturen.
Während die Kompressoren der BELT-Baureihe luftgekühlt sind, hat sich CeramTec bei dem neuen Kompressor für eine wassergekühlte Anlage entschieden. Diese kann einfach an einen Kühlwasserkreislauf angeschlossen werden. Das für die Kühlung der Anlage verwendete Wasser wird anschließend direkt in das Heizungssystem eingeleitet. Damit ergibt sich besonders in den Wintermonaten ein hohes Einsparpotenzial.
Ein wichtiger Grund für CeramTec, sich wieder für eine Anlage von ALMIG zu entscheiden, ist die robuste Bauweise dieser Kompressoren. „Damit haben wir eine sehr hohe Anlagenverfügbarkeit, weil nur selten Reparaturen anfallen – und das wirkt sich deutlich auf die Kosten aus“, ist Kaiser zufrieden. Das Wartungsintervall bei den Kompressoren liegt bei 4.000 Betriebsstunden.
Mehr Informationen zur ALMiG Kompressoren GmbH:
![]() |
ALMiG Kompressoren GmbH |
![]() |
Adolf-Ehmann-Straße 2 |
![]() |
73257 Köngen |
![]() |
Tel.: +49 (0)7024 – 9614 – 0 |
![]() |
Fax: +49 (0)7024 – 9614 – 106 |
![]() |
E-Mail: info@almig.de |
![]() |
www.almig.de |
War dieser Artikel für Sie hilfreich?
![]() |
![]() |
![]() |
![]() |
![]() |
Bitte bewerten Sie diese Seite durch Klick auf die Symbole.
Zugriffe heute: 2 - gesamt: 3670.