AHCs Alternative zur konventionellen Verchromung
Selektivgalvanische Abscheidung von Hartchrom
In nahezu allen Bereichen des Automobil- und Maschinenbaus finden technische Hartchrom-Überzüge Anwendung und verleihen den Bauelementen das Eigenschaftprofil, das den bestimmungsgemäßen Einsatz ermöglicht: Härte, Korrosionsbeständigkeit, Verschleißfestigkeit, Reibungseigenschaften sowie thermische und chemische Beständigkeit. Das gute tribologische Verhalten funktioneller Hartchromschichten wird dabei beschrieben durch die relativ hohe Ausgangshärte, ihrer fest anhaftenden, sich ständig erneuernden Oxidschicht sowie ihren antiadhäsiven Eigenschaften. Das Metall weist im Zustand wie abgeschieden (as plated) zudem hexagonalen Gitteraufbau auf. Die verschleißfördernden Gleitebenen innerhalb des Gitters fehlen also.
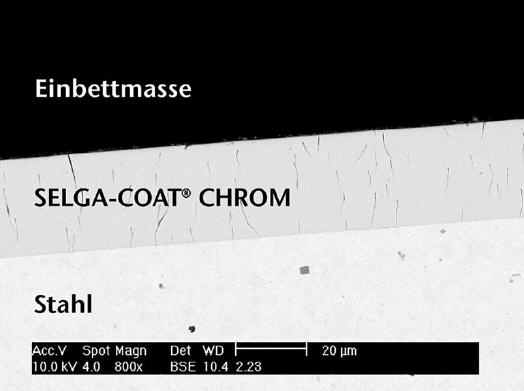
Nahezu alle technisch bedeutsamen Verfahren zur Darstellung funktioneller Hartchrom-Überzüge basieren auf der elektrolytischen Abscheidung von Chrom als Metall aus mittel- bis höher konzentrierten, wässrigen Chromsäurelösungen bei Prozesstemperaturen zwischen 50°C und 55°C. Es sind eine ganze Reihe von bewährten industriellen Elektrolytkonzepten auf dem Markt verfügbar, zugleich hat sich die Technik zur Herstellung der Überzüge in den letzten Jahrzehnten stetig verbessert.
Umweltaspekte und Effizienzsteigerungen haben dazu geführt, dass moderne Anlagentechniken in der Kombination mit modernen Elektrolytkonzepten die Hartchromverfahren zu einer nachhaltig wettbewerbsfähigen Technologie erhoben haben. Gleichwohl sind die Verfahren durch die aktuelle Verordnungslage und durch die EU-Chemikalienverordnung REACH erneut und zu Unrecht in die Diskussion geraten. Die Bestrebungen der Regulierungsbehörden geht bis hin zur jeweiligen Neuzulassung bezogen auf spezifisch genutzte Techniken zur Abscheidung von funktionellen Hartchromschichten.
Mithin sind weitere Überlegungen anzustellen, die es ermöglichen, funktionelle Hartchromschichten auch auf längere Sicht im Repertoire der bewährten Beschichtungsverfahren zu halten. Eine Lösung bietet die selektivgalvanische Abscheidung von funktionellen Hartchromüberzügen. Hierbei wird der zur Beschichtung notwendige Elektrolyt in überschaubaren Mengen jeweils nur zu einem spezifizierten Beschichtungsbereich hingeführt und nur an eben dieser Stelle eine ressourcenschonende selektive Schichtabscheidung durchgeführt.
In der Folge entfällt zumeist auch ein Nachschleifen des Beschichtungsbereiches. Diese Vorgehensweise stellt erhöhte Anforderungen an die Anlagentechnologie als auch an die eingesetzten Elektrolytkonzepte. In der Regel sind auch deutlich höhere Abscheidungsgeschwindigkeiten möglich als bei den konventionellen Hartchrom-Beschichtungsverfahren. Die Erhöhung der Stromdichte und die Steigerung der Abscheidungsgeschwindigkeit wirken sich zudem deutlich positiv auf die Stromausbeute aus.
Die eingesetzte Technologie erlaubt neben der Einsparung von Ressourcen wie Energie und Chemie zudem die Darstellung eines abwasserfreien Umlauf-Systems. Ferner besteht die Möglichkeit, Beschichtungsanlagen zur Einkopplung von Beschichtungsprozessen in-line in eine Fertigungskette bereitzustellen - ein Gebot der Zukunft.
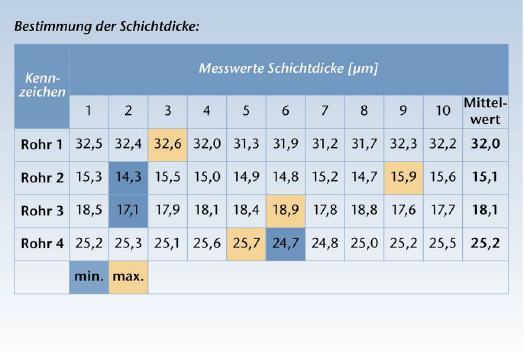
Hartchrombeschichtung an Stoßdämpferrohren
AHC Surface Technology SAS in Faulquemont verfügt schon seit mehr als zehn Jahren über weitreichende Erfahrung bei der partiellen Hartanodisation von Aluminiumlegierungen /2/. Daher lag es nahe, die gesammelten Erfahrungen und technischen Daten auf ein Verfahren zur selektiven High-Speed-Abscheidung von Hartchrom zu übertragen.
Ausgangspunkt war die Darstellung einer funktionellen Hartchrombeschichtung auf Stoßdämpferrohren (Oberfläche 8-10 qdm) für die Automobilindustrie mit einer geforderten Schichtdicke von 20 – 25 µm. In Anlehnung an das bewährte Verfahren zur selektiven Hartanodisation von Aluminiumlegierungen (SELGA-COAT) wird dieses Verfahren SELGA-COAT CHROM genannt. Eine Prototyp-Anlage für das selektive Hartchromverfahren wurde mit Unterstützung der Verfahrensspezialisten der AHC-Gruppe in Faulquemont (Lothringen) entwickelt und dort errichtet.
Im niederländischen AHC-Werk in Venlo (AHC Benelux BV) ist eine vollautomatische Anlage zur Serienbeschichtung in geschlossener Werkzeugtechnik (Kreislaufsystem) von unlegiertem oder gehärtetem Stahl im Aufbau. Die Anlagen enthalten keine offenen Behälter/Tanks mit Chromsäurelösung. Zudem ist kein Netzmittel (Tensid) im Elektrolyten notwendig.
Der zu beschichtende Rohrkörper wird im Beschichtungswerkzeug positioniert. Je Beschichtungsstation befinden sind nur ca. 200 Liter Elektrolyt im Umlauf.
Der Chromsäureelektrolyt auf Basis von sechswertigem Chrom enthält ein spezielles Gemisch von Sonderkatalysatoren, das bei hohen Einsatztemperaturen im Durchflutsystem mit bis zu 1.200 HV genügend harte und außerdem glänzende bis hoch glänzende, mikrorissige Überzüge ergibt. Der Glanzbereich verschiebt sich dabei grundsätzlich zu höheren Stromdichten und höheren Elektrolyttemperaturen. Der bisher in der Literatur bekannte Stromdichte-Elektrolyttemperatur-Bereich wurde durch das Verfahren SELGA-COAT CHROM deutlich erweitert.
Die gesamte Beschichtungseinheit mit allen notwendigen Aggregaten wurde in einem Modul gekapselt. Es ist sowohl ein halb- als auch vollautomatischer Betrieb der Einheit möglich. Die entstehende Kontaktwärme wird mit Wasser oder Luft über eine Zwangsführung gekühlt. Die sehr hohe Übergangswärme im Bereich der Grenzfläche Beschichtung/Grundwerkstoff wird vom Elektrolytdurchfluss während des Beschichtungsvorganges abgeführt. Die Abwärme, die durch die Elektrolytführung aus dem Prozess aufgenommen wird, wird dazu genutzt, die eingesetzten Spülwassermengen zu reduzieren, so dass die Einheit abwasserfrei und mit fast vollständiger Rückführung der eingesetzten Chemie betrieben werden kann.
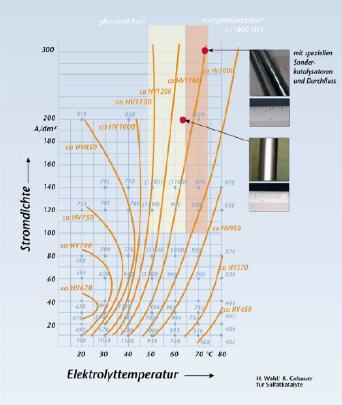
Schichtdickenverteilung, Härte, Schichtstruktur
Die Hartchrom-Schichten werden beim SELGA-COAT CHROM – Verfahren mit hoher Geschwindigkeit abgeschieden. Eine Schichtdicke von 25 µm lässt sich in 3 bis 4 Minuten erzeugen. Die Schichten sind über den gesamt Verlauf der Beschichtungslänge (im Falle der Stoßdämpferrohre 800 mm) sehr gleichmäßig. Über den gesamten Verlauf ergibt sich bei einer Sollschichtdicke von 22 µm eine Abweichung von plus/minus 2 µm. Auch bei dickeren Überzügen mit mehr als 30 µm werden keine größeren Abweichungen ermittelt.
Die Härte der Überzüge konnte für die extrem hohen Stromdichten reproduzierbar mit 1.050 – 1.200 HV gemessen werden.
Im Querschliff wurde erwartungsgemäß Mikrorissigkeit mit bis zu 400 Risse/linear cm (ausgezählt) festgestellt, die Schichten sind kompakt und bei störungsarmer Grundmaterialoberfläche von guter Beschaffenheit, dies zeigt die.
Es bleibt an dieser Stelle zu erwähnen, dass eine gute Grundwerkstoffbeschaffenheit eine der Voraussetzungen für störungsarme und korrosionsbeständige Überzüge ist. So können im neutralen Salznebeltest nach DIN EN ISO 9227 mehr als 240h Beständigkeit bis Rp9/Rp10 (DIN EN ISO 10289) erzielt werden.
Mit der selektivgalvanischen Abscheidung von Hartchrom nach dem Verfahren SELGA-COAT CHROM steht nunmehr für einige Anwendungen eine echte Alternative zur konventionellen Verchromung zur Verfügung.
Mehr Informationen zur AHC Oberflächentechnik:
![]() |
AHC Oberflächentechnik GmbH |
![]() |
Boelckestraße 25-57 |
![]() |
50171 Kerpen |
![]() |
Tel. 02237 502 - 0 |
![]() |
Fax: 02237 502 - 100 |
![]() |
E-Mail: info@ahc-surface.com |
![]() |
www.ahc-surface.com |
War dieser Artikel für Sie hilfreich?
![]() |
![]() |
![]() |
![]() |
![]() |
Bitte bewerten Sie diese Seite durch Klick auf die Symbole.
Zugriffe heute: 2 - gesamt: 3650.