Extrem tiefe Bohrungen mit Standarddreher
Cincom Evolution L20E von Citizen
Das Herzstück eines Lichtbogenschweißbrenners ist die Stromdüse, durch die der Draht geführt wird. Bei Abicor Binzel wird dafür besonders tief gebohrt – und das in einem speziell dafür entwickelten und patentierten Tieflochbohrprozess, der zuerst nur auf Spezialmaschinen möglich war. Nun setzt das Unternehmen in seinem Maschinenpark einen Cincom Evolution L20E Langdrehautomaten von Citizen ein und hat damit eine Möglichkeit gefunden, dieses hoch anspruchsvolle Fertigungsverfahren auch auf einer Standardmaschine zu realisieren – mit höchster Präzision und ohne Belastung des Werkzeugs.
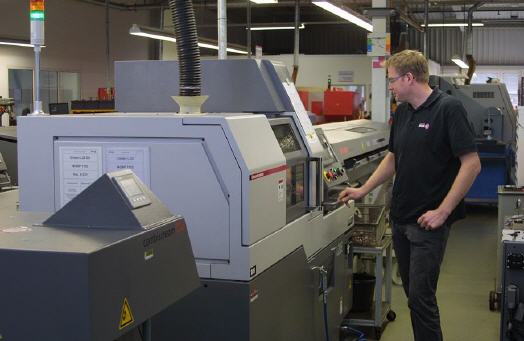
Die Alexander Binzel Schweisstechnik GmbH & Co. KG (ABICOR BINZEL) aus Buseck ist mit 32 Tochterunternehmen und mehr als 20 Vertriebspartnern weltweit vertreten und ein Marktführer auf dem Gebiet der Schweißbrennertechnologie. Weltweit werden Produkte unter der Marke ABICOR BINZEL verkauft. In einer Produktionsstätte des Unternehmens in Tschechien werden pro Jahr zwischen 13 und 15 Millionen Stromdüsen gefertigt.
„Allerdings handelt es sich dabei ausschließlich um Standardbauteile“, erklärt Wolfgang Nau, Leiter Fertigungsprozesse International bei ABICOR BINZEL. „Kundenspezifische Sonderausführungen werden hier in Buseck produziert. Dafür verwenden wir seit einiger Zeit eine Cincom Evolution L20E Langdrehmaschine von Citizen, die speziell für ABICOR BINZEL modifiziert wurde.“
ABICOR BINZEL setzt die Cincom Evolution L20E für einen patentierten Tieflochbohrprozess ein, den das Unternehmen vor zwölf Jahren entwickelt hat. Der Langdrehautomat erlaubt Bohrungen ab 0,93 mm Durchmesser. „Mit der L20E erreichen wir an Bohrungstiefen mehr als das 35-Fache des Durchmessers“, so Andreas Müller, Teamleiter Langdrehen bei ABICOR BINZEL. „Aktuell testen wir Tieflochbohrungen von bis zu 95 mm.“
Die dafür erforderlichen Werkzeuge sind innengekühlte HSS-Bohrer mit aufgelöteter Hartmetall-Spitze. Das ist notwendig, weil reine HM-Werkzeuge für den Fertigungsprozess zu spröde wären und während der Zerspanung brechen würden.
Tieflochbohrungen mit solch geringen Durchmessern und gleichzeitig enormen Tiefen waren bisher nur mit viel Zeit- und Kostenaufwand auf Spezialmaschinen möglich. „Dazu braucht es hohe Schnittgeschwindigkeiten und großen Öldruck auf den Innenkühlungskanälen der langen, dünnen Werkzeuge, um eine absolut saubere Spanabfuhr zu erreichen“, so Wolfgang Nau.
Die Cincom Evolution L20E wurde so verändert, dass sie den Tieflochbohrprozess schnell meistert, ohne die Bohrer zu belasten. „Dazu haben wir dem Werkzeughalter für die Rückseitenbearbeitung den Antrieb entnommen und ihn an dem Werkzeughalter für die Vorderseitenbearbeitung angebracht. Den Werkzeughalter dort haben wir dann ein Stück nach hinten versetzt, um Platz für die Tieflochbohrer zu schaffen“, sagt Björn Wied, Geschäftsführer von Wietec und Gebietsvertreter für Citizen-Produkte in Hessen, Rheinland-Pfalz und Baden-Württemberg. „Zudem wurden der Kühlmitteltank und der Spänebehälter gegen eine spezielle Combistream-Anlage ausgetauscht.“ Diese Sonderkonstruktion von Müller Hydraulik liefert enormen Öldruck von bis zu 200 bar. Den braucht es, um die Späne mit dem Öl über eine Längsnut am Werkzeug aus der Bohrung herauszuspülen.
Dafür ist auch die hohe Drehzahl der Bohrer von bis zu 16.000 U/min erforderlich. Björn Wied: „Das Lademagazin der L20E ist mit drei Meter langen Stangen ausgestattet, die automatisch in die Hauptspindel vorgeschoben werden. Würde man die Hauptspindel mit 10.000 U/min ausreizen, erzeugte das Lademagazin Vibrationen. In der Anwendung würde der Bohrer sofort brechen. Um solche schädlichen Einflüsse zu vermeiden, fährt die Hauptspindel lediglich mit 500 bis 1.000 U/min. Deshalb brauchen wir zusätzlich einen gegenläufigen Antrieb für das Werkzeug an der Vorderseite. Auf diese Weise erreichen wir nun eine Drehzahl von mehr als 16.000 U/min.“ Herkömmliche Kühlschmiermittel halten dem nicht stand: Wie in einer Zentrifuge in ihre Bestandteile zerlegt, würden sie weder kühlen noch schmieren.
„Eine solche Maschine zu konstruieren, war eine große Herausforderung, die wir zusammen mit Citizen erfolgreich gemeistert haben“, so Wolfgang Nau. „Dass die Tieflochbohrungen bei uns nun auch auf einer Standardmaschine realisierbar sind, bringt uns signifikante Vorteile in puncto Flexibilität, Zeit und Kosten.“
Von besonderer Wichtigkeit sind konstante Fertigungsergebnisse: Bei ABICOR BINZEL ist eine Stromdüse wie die andere. Darüber hinaus sind die Stromdüsen besonders verschleißfest. „Vor allem bei industriellen Anwendungen mit Schweißrobotern ist das unerlässlich“, erläutert Wolfgang Nau. „Denn die Stromdüse ist das entscheidende Element beim Schweißen. Allein schon der Austausch ist sehr aufwändig, weil dafür der gesamte automatisierte Prozess angehalten werden müsste. Wenn der Anwender dann zusätzlich die Maschine auf eine neue Stromdüse einstellen müsste, würde er noch mehr wertvolle Zeit verlieren.“
Wie wichtig Stromdüsen ohne Abweichungen sind, zeigt ein Kunde von ABICOR BINZEL, der Unterwasser-Pipelines auf Schiffen verschweißt und direkt anschließend verlegt. Dabei ist höchste Qualität gefragt, die auf dem Schiff sofort per Röntgenaufnahmen geprüft und dokumentiert wird. Dazu Björn Wied: „Die L20E von Citizen fertigt solche Stromdüsen mit einer Mittenabweichung von nur 2/100 und gewährleistet damit höchste Präzision und Konstanz auch bei solch anspruchsvollen, speziellen Applikationen.“
Mehr Informationen zu Citizen:
![]() |
CITIZEN MACHINERY EUROPE GmbH |
![]() |
Mettinger Straße 11 |
![]() |
73728 Esslingen |
![]() |
Telefon ++49 (0)711 / 3906-100 |
![]() |
Telefax ++49 (0)711 / 3906-106 |
![]() |
E-Mail: cme@citizen.de |
![]() |
www.citizen.de |
War dieser Artikel für Sie hilfreich?
![]() |
![]() |
![]() |
![]() |
![]() |
Bitte bewerten Sie diese Seite durch Klick auf die Symbole.
Zugriffe heute: 1 - gesamt: 2787.