Mit der Pero R1 in der halben Zeit entfetten
Saubere Kontakte mit PER
Die einwandfreie Funktion elektrischer Schaltkontakte wird nachhaltig von ihrer Fettfreiheit bestimmt. Darum wird im Werk Weikersdorf der Kraus & Naimer Produktion GmbH seit 23 Jahren mit dem halogenierten Kohlenwasserstoff Perchlorethylen (Per) in Anlagen von Pero gereinigt. Mit der Vollvakuum-Anlage R1 ist jetzt die dritte Anlagen-Generation des Herstellers im Einsatz – und mit ihr werden neue Rekorde aufgestellt: Die Zykluszeit wurde halbiert, der Energiebedarf um zwei Drittel reduziert – aber die Qualität blieb unverändert hoch.
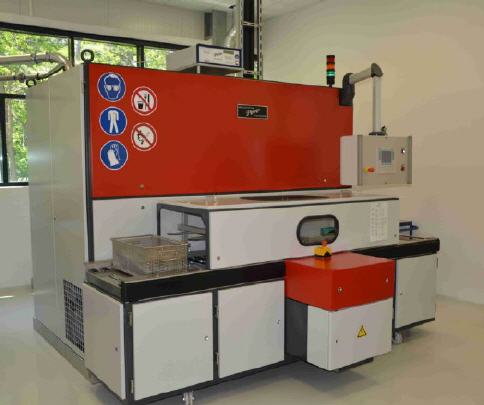
„Wir haben über die ganzen Jahre mit Perchlorethylen als Reinigungsmedium beste Erfahrungen gemacht“, begründet Josef Schuster, Abteilungsleiter Produktion-Metall bei der Kraus & Naimer Produktion GmbH im Werk Weikersdorf vor den Toren Wiens, die Entscheidung, auch die neue Reinigungsanlage von Pero mit dem Lösemittel Per zu betreiben. Auch die umfangreichen Versuche mit alternativen Lösemitteln wie modifiziertem Alkohol konnten Josef Schuster nicht überzeugen, ein anderes Medium einzusetzen. Es wurden gleiche Teile jeweils zur Hälfte mit Per und mit modifiziertem Alkohol entfettet. Die Sauberkeits-Ergebnisse waren unter objektiven Gesichtspunkten gleichwertig. Aber Josef Schuster wollte kein Risiko eingehen. „Wir liefern unsere Kontakte in alle Welt und in alle Klimazonen“, fasst er seine Erfahrungen zusammen, „und hatten noch nie Probleme wegen Korrosion – und das soll auch so bleiben.“
Mit Per setzt er auch weiterhin auf das Lösemittel, das eine große Fettlösekraft unter den gängigen Lösemittel-Typen besitzt. Das unpolare Medium Per ist nicht brennbar – ein Vorteil, der sich auch positiv auf das gereinigte Produkt auswirkt. Durch die hohe Dichte des flüssigen Reinigungsmediums wirkt im Reinigunsprozess eine besonders hohe Mechanik auf die Oberfläche der zu reinigenden Teile. Der relativ niedrige Siedepunkt von Per ermöglicht, dass niedrig siedende Öle sicher abgeschieden werden – ein Plus für die zu erreichende Reinheit.
Das Medium kann im Verlauf seines Einsatzes stabilisiert werden, was einen Medientausch seltener macht. Durch die schonende thermische Behandlung in der Voll-Vakuumanlage reduziert sich zudem die Notwendigkeit, das Lösemittel zu stabilisieren. Josef Schuster konnte mit der R1 eine Reduktion des Stabilisator-Einsatzes von etwa 55 Prozent verzeichnen. Auf die gleiche Einheit umgerechnet ist Per auch günstiger zu beschaffen als modifizierter Alkohol.
In der Produktions-Abteilung Metall von Kraus & Naimer (K&N) werden täglich zwischen 50.000 und 80.000 Teile produziert, die als Schüttgut in Drahtkörben zur Pero-Reinigungsanlage R1 transportiert und dort von Fett und Spänen befreit werden. Kraus & Naimer verfügt über eine große Fertigungstiefe und produziert auch die Basisteile der Kontakte selbst. Das sind Drehteile, die als Achsen in die Schalter montiert werden, sowie Stanzteile und Spezialschrauben. DIN-Schrauben kommen von Zulieferern. Aber Josef Schuster muss nicht nur seine Metallteile entfetten, auch einige Kunststoff-Teile aus den eigenen Spritzgieß-Maschinen, die in einer separaten Halle untergebracht sind, müssen die Reinigungsanlage R1 durchlaufen.
Höchste Technische Sauberkeit ist gefordert, damit die Schalter einwandfrei funktionieren und bei keiner Belastung – auch nicht bei Kurzschluss – zu brennen beginnen. Gerade die Reinigung im Medium Per liefert absolut trockene Teile mit porentief entfetteten Kontaktflächen, die metallisch blank und fleckenfrei sind. Die Oberflächen sind jedoch nicht stumpf und ermöglichen eine gute Handhabbarkeit der Teile. Das sind wichtige Aspekte für die Fertigungs-Verantwortlichen bei Kraus & Naimer, weil neben der Entfettung auch der Korrosionsschutz der Metallkontakte eine große Rolle spielt.
Schon die erste Pero-Reinigungsanlage vom Typ 2500/1N, die im Jahre 1990 angeschafft wurde, brachte beste Ergebnisse: „Wir hatten nie Korrosionsprobleme, nicht mal in kritischen Klimazonen von Südamerika oder Süd-Ost-Asien“, freut sich Josef Schuster und schließt dabei selbst kleinste Fleckenbildung an Buntmetallen mit ein. Die zweite Pero-Anlage vom Typ 2500/1V wurde 2001 geliefert. Sie trocknete Teile in der Arbeitskammer bereits mit Vakuumtechnik und war schon mit einem Ultraschall-Modul ausgestattet – aber Per blieb.
Mit der R1 steht nun die ganze Anlage unter Vakuum – also auch Bäder, Arbeitskammer und Wasserabscheider. Nur beim Chargenwechsel in der Arbeitskammer wechselt Atmosphärendruck zu Vakuum und umgekehrt. Mit dieser Technologie sind die nicht gefassten Emissionen an Lösemittel nahezu auf Null gesunken. Prozessluft wird über Aktivkohle geführt und so Lösemittel-Verlust im Gesamtkreislauf vermieden. Das ist in Österreich so auch Vorschrift – genau wie ein Messgerät für die Lösemittel-Konzentration und eine Luftabsaugung bei Wartungsarbeiten. Faktoren, die bei der Investitions-Rechnung durchaus beachtet wurden.
Durch die Verlagerung der Produktions-Abteilung Metall von Wien ins Werk Weikersdorf wurde die Anschaffung einer neuen Reinigungsanlage notwendig, weil der behördliche Aufwand eines Umzugs der vorhandenen Anlage extrem hoch gewesen wäre, „und außerdem hätten wir die alte Anlage ohnehin in gut zwei Jahren ersetzen müssen“, benennt Schuster die Motive für die Neu-Investition. Hinzu kommt noch, dass die Genehmigung einer neuen mit chlorierten Kohlenwasserstoffen betriebenen Anlage durch die Behörden leichter zu bekommen ist.
So hat Josef Schuster mit der dritten Pero-Reinigungsanlage der Größe „1“ einen gewaltigen Technologie-Sprung nach vorn gemacht. Die Voll-Vakuumtechnik der Anlage R1 ermöglichte im Gegensatz zu den Vorgängermodellen eine Bauform, die einen guten Wartungszugriff bietet, obwohl die Aggregate mit 20 Prozent geringerem Platzbedarf angeordnet sind. Durch innovative Verfahrenstechnik gelang es außerdem, die R1 auf Schnelligkeit zu trimmen. Fast alle Reinigungs-Prozesse bei K&N laufen in der halben Taktzeit ab – ergo verdoppelt sich damit der Durchsatz pro Zeit-Einheit.
Mehr Durchsatz bedeutet aber auch mehr Schmutz-Eintrag pro Zeit-Einheit. Darum wurde die R1 mit einer sehr hohen Destillationsleistung ausgestattet. So bleibt das Lösemittel in den Bädern sauber und die Teile werden rein. Die integrierte Restdestillation sorgt für den automatischen Ölaustrag in ein bereitstehendes Altöl-Fass. Die Restdestillation wird am Display der Anlage gestartet, und nach nur rund 1,5 Stunden ist die Wartung beendet und der Ölsumpf ins Altöl-Fass gesaugt. Sollte sich der Öleintrag künftig erhöhen, so kann die R1 mit dem Destillations-Modul CompactD erweitert werden. Das bietet K&N eine besondere Zukunftsicherheit. Dank des ausgeklügelten Wärme-Rückgewinnungs-Systems kann dieses hohe Leistungs-Potenzial mit dem vergleichsweise geringen Anschlusswert von 20 kW abgerufen werden, was den Energieverbrauch pro Charge – bis hin zum gereinigten Einzelteil – deutlich senkt und die Reinigung besonders wirtschaftlich macht.
Die ausgefeilte Programmstruktur mit frei wählbaren Warenbewegungen in jedem Verfahrens-Schritt ermöglicht es dem Leiter Mechanische Fertigung, eigene Reinigungs-Programme zu erstellen, die der jeweiligen Aufgabe optimal angepasst sind. Die Warenträger mit den Abmessungen 530 x 320 x 200 mm können um 360 Grad rotieren, geschwenkt und in Schräglage gehalten werden oder ohne Bewegung verharren, während die Teile im Vollbad getaucht, geflutet, mit einem Schwall Lösemittel überspült oder mit Lösemittel-Dampf entfettet werden.
Je nach Teil ruft der Werker aus den 20 möglichen das richtige Programm auf, das schon in der Testphase im Pero-Technologiezentrum entwickelt wurde, und die Maschine arbeitet es dann automatisch ab. Lediglich die Aufgabe und Abnahme der Körbe von der Rollenbahn erfolgt von Hand. Für den Abteilungsleiter Produktion-Metall ist ein einfaches Handling der Pero-R1 sehr wichtig, weil er mit vielen neuen Mitarbeitern arbeiten muss, denn die Mehrzahl seiner ehemaligen Mitarbeiter hat den Umzug von Wien nach Weikersdorf nicht mitgemacht. Das Maschinen-Diagnoseprogramm und die Bedienerführung der R1 zeigen immer, was die Anlage gerade macht und informieren sofort im Klartext, was bei auftretenden Störungen zu tun ist.
Mit der Visualisierung kann der Reinigungsprozess leicht beobachtet und kontrolliert werden. Am Bedientableau werden Wochenschaltuhr, Chargenvorwahl und Schichtautomatik in einfacher Weise programmiert oder Wartungen direkt gestartet. Damit wird die Bedien-Zeit und -Häufigkeit reduziert. Die Filtertrocknung kann so automatisch in der Nachtschicht oder in der Pause erfolgen. Sollte im Service-Fall ein manueller Eingriff notwendig werden, wird mittels Schnell-Abkühlung die Zieltemperatur in der ganzen Anlage zügig erreicht und Wartezeit reduziert. Eine integrierte Korbdrehrichungs-Kontrolle verhindert in diesem Fall, dass Teile aus dem Korb fallen. Dank großer Glasdeckel an Tanks und Dampfentwickler kann der Betreiber die Qualität des Reinigungsmediums gut kontrollieren.
Für die Wirtschaftlichkeitsbetrachtung der Pero-R1 ist die Schnelligkeit der Reinigungsprozesse von entscheidender Bedeutung. Die Prozess-Zeiten haben sich für Kraus & Naimer halbiert. Ferner sind durch die Vakuum-Technik und das geschlossene System nahezu keine Austragverluste des Reinigungsmediums zu registrieren. „Wir haben innerhalb eines halben Jahres kein Lösemittel Per nachfüllen müssen – trotz des ausdestillierten Öls“, kann Josef Schuster zufrieden feststellen und zugleich auch den Vorteil der Voll-Vakuumtechnik quantifizieren. „Das gleiche gilt für den Stabilisator-Verbrauch, der durch die Voll-Vakuumtechnik sehr niederig ist – bei Kraus & Naimer lag er sogar bei Null in sechs Monaten“, ergänzt Josef Deutsch die positiven Ergebnisse.
Mehr Informationen zu Pero:
![]() |
PERO AG |
![]() |
Hunnenstr. 18 |
![]() |
86343 Königsbrunn |
![]() |
Tel +49 - 8231 - 60 11 - 0 |
![]() |
Fax +49 - 8231 - 60 11 - 810 |
![]() |
E-Mail: pero.info@pero.ag |
![]() |
www.pero-ag.de |
War dieser Artikel für Sie hilfreich?
![]() |
![]() |
![]() |
![]() |
![]() |
Bitte bewerten Sie diese Seite durch Klick auf die Symbole.
Zugriffe heute: 1 - gesamt: 3213.